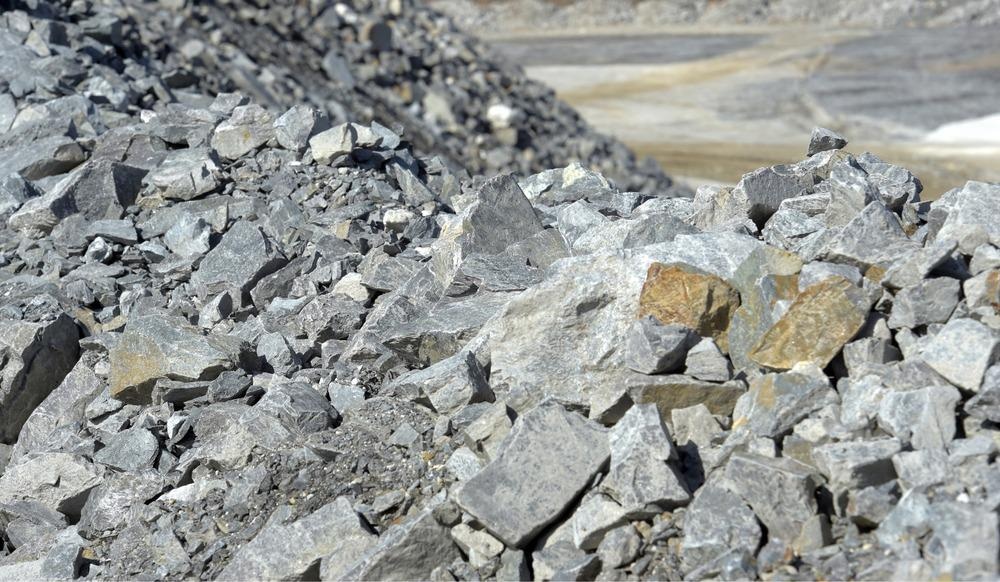
Image Credit: Steve Morfi/Shutterstock.com
Lithium-ion batteries are essential to modern life; they power everything from consumer electronics such as phones and laptops, to vehicles such as electric cars and mining trucks. They are critical in weaning the global economy off polluting fossil fuels and decarbonizing society at a time when the environment tops the list of priorities.
The number of electric vehicles (EVs) sold has steadily increased from 1.2 million units in 2017, to more than 2 million in 2018 and an estimated 4 million in 2020. Sales are expected to reach 12 million by 2025, and almost double to 23 million in 2030. Deloitte predicts 2022 will see EVs become cost-competitive with their internal combustion engine (ICE) counterparts, meaning the cost of purchasing EVs will no longer be prohibitive.
Sales of EVs are expected to bounce back after the COVID-19 pandemic. However, the industry faces supply issues as they struggle to obtain the raw materials required for EV batteries. Obstacles working against the supply chain include high costs and environmental concerns related to the mining and processing of key metals.
Raw Materials: Lithium
Lithium-ion batteries use lithium carbonate and lithium hydroxide as the cathode material. Demand for these raw materials is rising as more consumers make the switch to electric, as is the cost of obtaining them. The worldwide market for lithium, most of which is mined in China, was estimated at $7 billion in 2018 and predicted to reach $58.8 billion by 2024, according to a report from UNCTAD.
There is no shortage of lithium, but a global decrease in the demand for EVs due to a weak market and fewer sales in China - the largest consumer of EVs - has resulted in mining and plant construction slowing down. Although many manufacturers have now resumed operations following a brief pandemic-related hiatus, this lull in lithium mining has created a supply shortage, particularly in the west.
New methods of lithium mining and extraction could help speed up the process. Puerto Rico-based EnergyX is trialing nanotech membranes, which enable quick and efficient separation of lithium during the refining process. Should it be possible to scale this process up, it will be a massive boost to the global supply chain.
Raw Material: Cobalt
Cobalt is used in the cathode in lithium-ion batteries and accounts for around one-fifth of the bulk. Demand is expected to reach as much as 430,000 tons within the next decade and current trends suggest a shortage of raw cobalt in the future – the current growing demand just cannot be met with current capacity.
Nearly 50% of the world’s cobalt reserve – and therefore mining activity - is concentrated in the Democratic Republic of Congo (DRC). Around 65% of the global supply of cobalt is mined here, in one of the world’s least developed countries. There is limited transparency in the cobalt value chain, and mining is also hazardous, with dangerous working conditions, exploitation, and poor wages.
Furthermore, such highly concentrated production is susceptible to political instability and adverse environmental impact, which introduces instability in the supply chain. This, in turn, leads to tighter markets, higher prices, and more expensive batteries, which has the potential to affect the global switch to EVs.
The Solution
The UNCTAD report, Commodities at a Glance; Special Issue on Strategic Raw Materials, notes that rechargeable batteries will have a considerable role in the worldwide conversion to a low-carbon energy system and will aid efforts to mitigate climate change, but only if the raw materials used in their making are sourced and produced sustainably.
It also states that investment in green technologies could reduce dependence on critical battery raw materials, and therefore reduce vulnerability to shortfalls in the supply of lithium and cobalt. Silicon, for example, is being explored as it has the potential to absorb more charge, meaning batteries are smaller and last longer.
Ensuring a continuous supply of cobalt and lithium – or finding a viable alternative – is necessary to ensure EV sales continue as predicted. Recycling old batteries could reduce the mining and processing of raw materials and help fill the void, but it is unlikely to be in the near future, as few EV batteries have reached their end of life.
Conclusion
Demand for rechargeable batteries is expected to expand quickly as EVs become more commonplace in global transportation. The knock-on effect is that the amount of the raw materials used to manufacture them will also increase rapidly. The industry must adapt to ensure that globally, the transition to electrification and EVs continues. This will ensure that we follow the path to mitigate any future climate change.
References and Further Reading
United Nations, (2020), Commodities at a Glance; Special Issue on Strategic Raw Materials, United Nations Conference on Trade and Development, https://unctad.org/system/files/official-document/ditccom2019d5_en.pdf. Accessed 12 April 2021.
United Nations, (2020), Demand for raw materials for electric car batteries set to rise further, UNCTD https://unctad.org/news/demand-raw-materials-electric-car-batteries-set-rise-further. Accessed 12 April 2021.
Cohen, A. (2020), Manufacturers Are Struggling To Supply Electric Vehicles With Batteries, Forbes, https://www.forbes.com/sites/arielcohen/2020/03/25/manufacturers-are-struggling-to-supply-electric-vehicles-with-batteries/?sh=3b68d8a71ff3. Accessed 12 April 2021.
Disclaimer: The views expressed here are those of the author expressed in their private capacity and do not necessarily represent the views of AZoM.com Limited T/A AZoNetwork the owner and operator of this website. This disclaimer forms part of the Terms and conditions of use of this website.