Generally, the production of modern ceramic components falls into one of two distinct processing stages. The ceramic powder is first evenly dispersed in a liquid to specific proportions, and next, it is compacted into a predetermined optimal size and shape known as the ‘green body.’
A green body is a name for an object which mainly consists of weakly bound clay material, typically before it has been sintered, in the form of a bonded powder or plates.
The green body is heated to just under the melting point of the ceramic materials and sintering happens at this temperature, leading to the particles in the green body bonding together.

Image Credit: Bettersize Instruments Ltd.
Figure 1 shows the production process of ceramic components. This is highly dependent on the physical properties of the ceramic powders and how they disperse during formation.
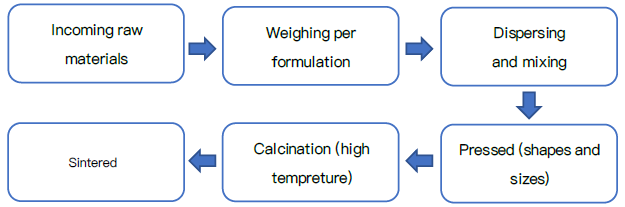
Figure 1. The manufacturing process of ceramic products. Image Credit: Bettersize Instruments Ltd.
During the dispersing process, ceramic powders can easily agglomerate. The uniformity of the powdered particles can be poor, which results in a lower performance in ceramic materials like piezoelectric products.
The measurement of the size of the ceramic powder particles during the production of ceramic components is vital to avoid this issue. Particle size analysis can be particularly helpful for the manufacturer to establish the best temperature and time needed for the green body to reach a predetermined optimal desired density in the sintering process.
Due to it having a larger surface area, a ceramic powder with a proportion of smaller particles can usually decrease the sintering time of the green body. So, in the production process of ceramic components, the particle size distribution measurement of ceramic powder is one of the most crucial parameters to control.
The Bettersizer 2600 laser diffraction particle size analyzer, with the wet dispersion module, was employed to determine the particle size distribution of some ceramic powders for this example.
In order to simultaneously detect the scattered light signals of the sample in the forward, lateral and backward directions, the Bettersizer 2600 uses the combination of Fourier and Inverse Fourier design.
An inclined sample cell is also used to diminish the influence of total internal reflections and so achieve a larger measuring range, high resolution and accuracy. The Bettersizer 2600 is a useful particle sizing tool in this and numerous other applications, particularly for investigating the size distribution of a number of ceramic materials and their interactions.
Measuring the Particle Size Distribution of Ceramic Powders
A number of different methods have been employed to measure the particle size distribution of ceramic powders. The Bettersizer 2600 laser particle size analyzer leads these technologies and due to its fast operation and ease of use, it provides unique benefits.
The dynamic measuring range that the Bettersizer 2600 covers are very wide, enabling the ceramic powders and aggregates to be detected easily in a single measurement at the same time with high repeatability.
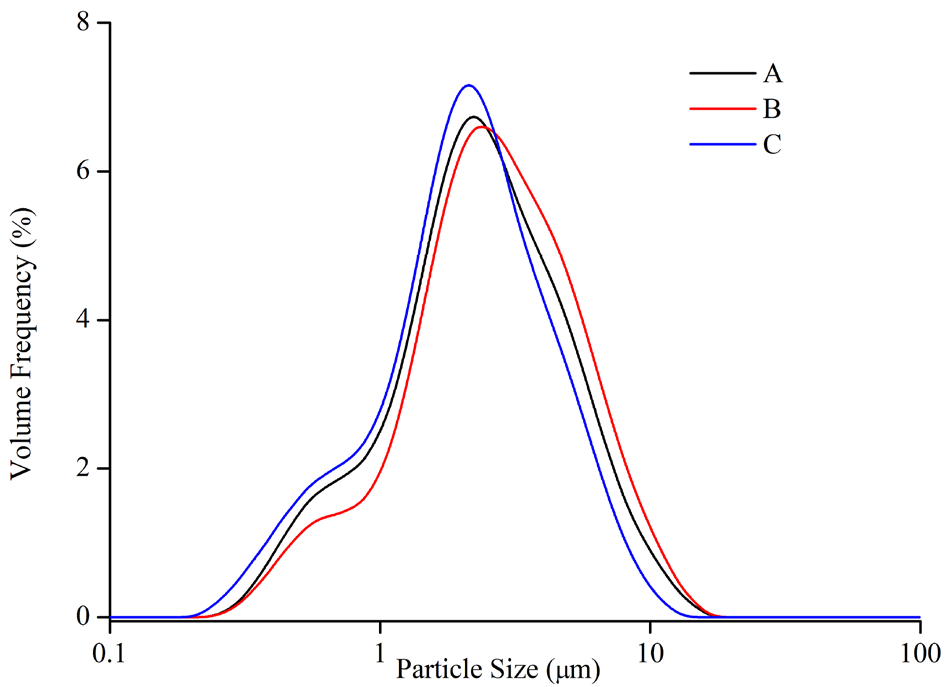
Figure 2. Particle size distribution of samples A, B and C. Image Credit: Bettersize Instruments Ltd.
Three ceramic samples supplied by a manufacturer were measured, and as can be seen in Figure 2, the test results of samples A, B and C show a wide distribution with a sub-micron inflection in each instance. Low powder homogeneity is usually indicated by a broad particle size distribution.
Small but vital differences in the distribution may be related to the differences in the processing methods. No matter what processing method is employed, the distribution and size of the ceramic material particles before the sintering of the green body must be controlled.
Typically, there is a direct relationship between the particle size of ceramic powder and the pore size seen in the green body prior to sintering. Particularly, large ceramic powders with low surface area usually combine ineffectively.
This can result in the formation of large pores, which persist throughout sintering and lead to the possibility of unqualified ceramic products 1.
Yet, uniform powders with smaller particle sizes can be utilized to control the formation of large pores or a polydisperse particle size distribution where the fine particles within the powder fill in the voids between the larger particles.
Sample A and sample B have more coarse particles than sample C, as can be seen in Figure 2. It should be noted that coarser particles greater than 10 µm appear in both samples A and B, which shows that the particle uniformity of samples A and B is poorer than sample C.
The optical microscope images in Figure 3 verify this, where the distribution of coarse particle aggregates is seen clearly for sample A and sample B but not in sample C.
Even before the formation of the green body, this can result in differences in the physical characteristics of the powdered ceramic material itself or affect the dispersibility of the ceramic mixed materials. And large pores will be produced in the parts of sample A and sample B, which are detrimental to the sintering process.
So, manufacturers must make sure that the particle size range is not too wide and that the packing factor is optimized by having the appropriate ratio of coarse to fine particles for this application. In particular, no oversized agglomerates should be present.
All these factors are used to establish if the sample A, B and C are suitable for creating ceramics or not. A static imaging analysis system was employed to confirm these results 2. The presence of aggregates in samples A and B is clearly shown in the images captured in Figure 3.
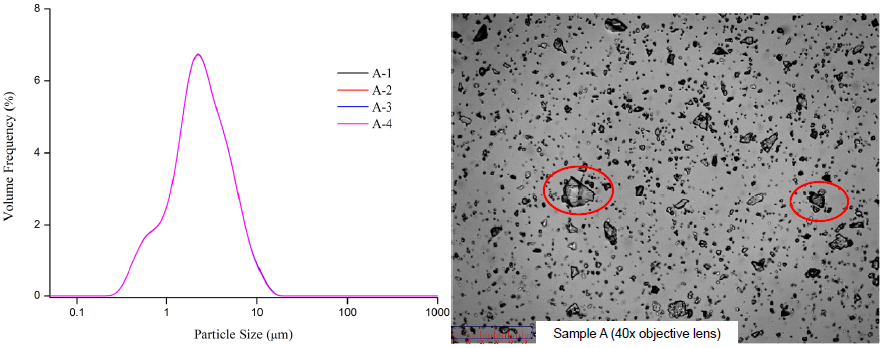
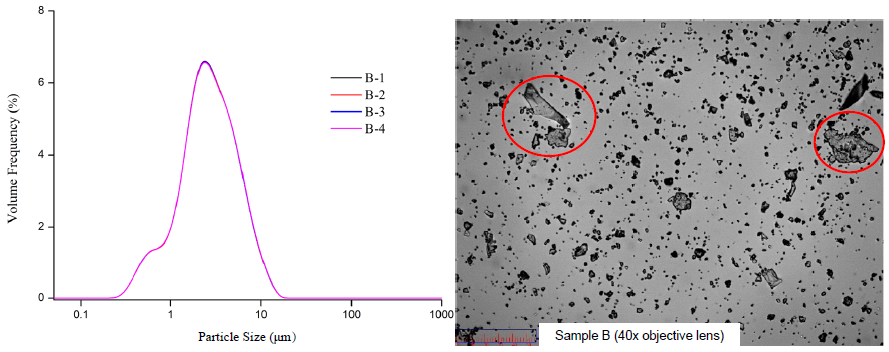
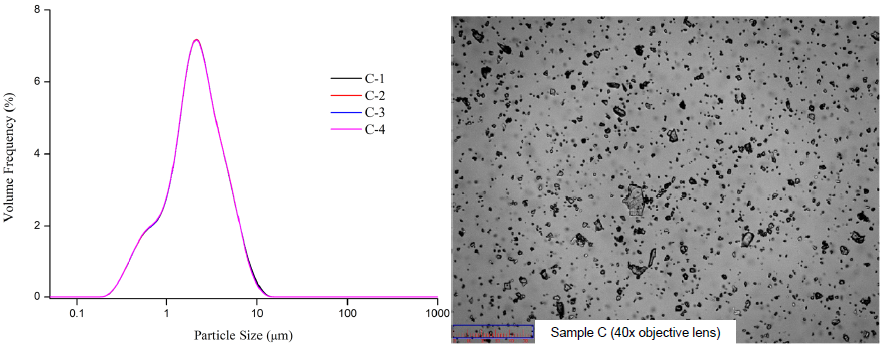
Figure 3. Particle size distribution and image analysis of sample A, B and C. Image Credit: Bettersize Instruments Ltd.
It can also be seen from Figure 3 that the numerous measurements of the three ceramic materials by the Bettersizer 2600 indicate good repeatability, which is best shown in Table 1.
Table 1. Repeatability analysis of the samples. Source: Bettersize Instruments Ltd.
Typical value |
Repeatability (%) |
Sample A |
Sample B |
Sample C |
D10 |
0.31 |
0.11 |
0.13 |
D50 |
0.86 |
0.15 |
0.09 |
D90 |
0.74 |
0.42 |
0.07 |
The repeatability values are far below the requirements of ISO 13320 2. So, by using the Bettersizer 2600, the confidence in the results of these ceramic powders is high.
Conclusion
An accurate measurement of the particle size distribution of ceramic powders is needed in the production of modern ceramic components. It has been proved that the dispersibility and particle size of a ceramic powder can be established using the Bettersizer 2600, which produces test results with high repeatability.
This high speed, accurate analysis exhibited fewer coarse agglomerates in sample C compared to samples A and B, both of which could be predicted to have a lower homogeneity. So, a sizing tool of this variety can help in the development and quality control of ceramic powders to reduce production costs.
References
- W.D. Kingery et al., Introduction to Ceramics, 2nd Edition, 1976, John Wiley & Sons.
- ISO 13320 (2009) Particle size analysis – Laser diffraction methods.
Acknowledgments
Produced from materials originally authored by Fangfang Zhang from Bettersize Instruments Ltd.

This information has been sourced, reviewed and adapted from materials provided by Bettersize Instruments Ltd.
For more information on this source, please visit Bettersize Instruments Ltd.
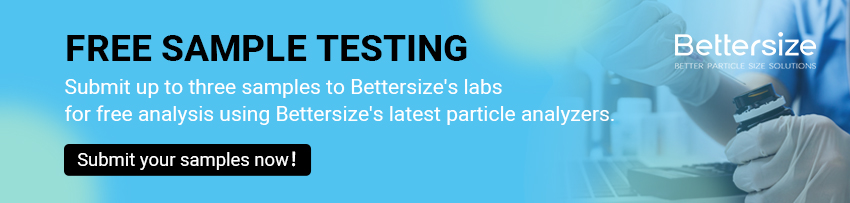