National Renewable Energy Laboratory (NREL) scientists supported by General Electric (GE) and LM Wind Power (a subsidiary of GE) recently reported on a breakthrough in lightning protection technology for wind turbines. The system, developed by a team led by Robynne Murray, provides lightning protection for wind turbine blades made from thermoplastic resin composites.
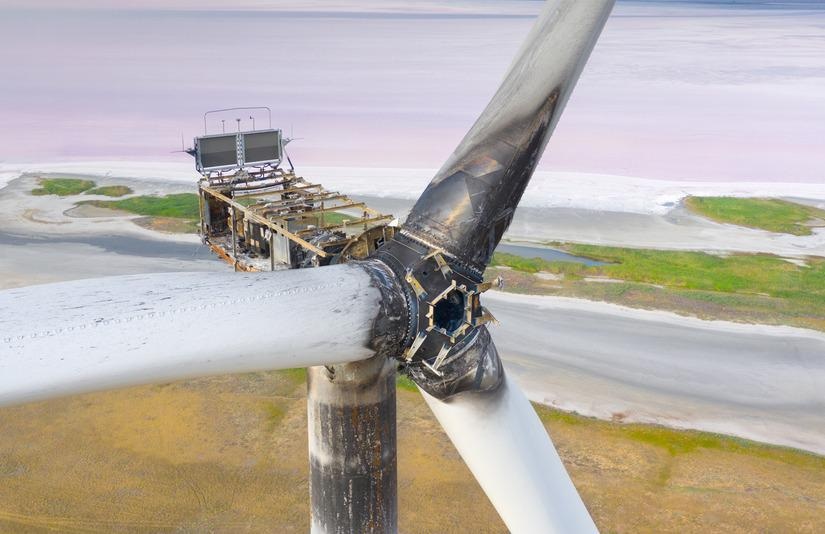
Image Credit: mykhailo pavlenko/Shutterstock.com
Conventional wind turbine blades – made from carbon fiber composites – already benefit from existing lightning protection systems. However, none had been introduced to protect the new generation of blades made out of thermoplastic composites.
NREL scientists developed a new thermal welding process to enable lightning protection for these blades. A patent application for the process has been submitted and is currently pending.
Using thermal welding, wind turbine blade manufacturers can do away with the adhesives they currently use to bond components of the blade. These adhesives are heavier than the new thermal welds and are at risk of cracking.
Murray, a specialist in materials and advanced manufacturing methods for wind turbine blades at NREL, was awarded an NREL Laboratory Directed Research and Development grant to work on thermal welding for these turbine components.
Thermal Welding for Wind Turbine Blades
Successful thermal welding required a conductive material such as carbon fiber or expanded metal foil to be placed between two halves of the blade. A wire attaching the conductive material to a power source completes the heating element.
When current passes through the heating element, the thermoplastic materials in the two blade halves melt. Once this has occurred, the current can be turned off and the bond allowed to cool under pressure.
Thermal welding has been proposed as a new method for wind turbine blade production, as it enables manufacturers to avoid the risks of cracking and more weight posed by using adhesives.
However, the conductive heating element that thermal welding requires can pose another risk: lightning strikes. This problem had been unsolved and was a barrier to increasing the commercialization of thermoplastic wind turbine blade materials.
Protecting Thermoplastic Blades Against Lightning Strikes
Together with GE and LM Wind Power, Murray and NREL proposed research into this problem to the US Department of Energy’s Technology Commercialization Fund. This research would tackle the issue head-on, seeking means to protect thermally welded thermoplastic turbine blades from lightning strikes.
The research team worked from NREL’s Composites Manufacturing Education and Technology site.
Their solution was to insert an expanded aluminum foil into the blade’s skin to divert lightning away from the metal heating element inside the blade. A simulation showed that lightning striking the turbine would not lead to blade failure with this new system in place.
The team then carried out physical damage tests, subjecting these altered blades to high electric currents. The result of these tests showed that approximately 80% of the current traveled through the aluminum foil layer safely and did not penetrate the blade’s skin. Furthermore, the carbon fiber immediately below the area of the blade that the artificial lightning struck showed no damage.
Based on these results, Murray’s aluminum foil design is likely to protect wind turbine blades from lightning strikes, which would be unlikely to cause a structural failure within the protected blade.
Giving Hope to Wind Turbine Renewable Energy
Improving thermoplastic wind turbine blade technology is good news for the renewable energy sector. Drastic improvements to current blades could help contribute to the sustainable decommissioning of wind turbines.
The shelf-life of turbine blades is around 20 years, after which they must be disposed of. A process to recycle carbon fiber is yet to be found, so the large amounts of material used for these blades are ultimately unsalvageable. Thermoplastic wind turbine blades, however, could be recycled when they reach their end-of-life
Thermoplastic wind turbine blades are still not a commercial reality, but Murray continues to work on structural validation for the innovative new manufacturing process and materials.
Finding a way to ensure thermoplastic wind turbine blades can benefit from the same level of lightning protection as traditional blades was an essential step in bringing the new technology to the market.
References and Further Reading
Omnexus.specialchem.com. (2021) New Lightning Protection System to Make Thermoplastic Wind Turbine Blades Safer. [online] Available at: https://omnexus.specialchem.com/news/industry-news/lightning-protection-system-blades-000225474 [Accessed August 2021]
Disclaimer: The views expressed here are those of the author expressed in their private capacity and do not necessarily represent the views of AZoM.com Limited T/A AZoNetwork the owner and operator of this website. This disclaimer forms part of the Terms and conditions of use of this website.