Novel research has synthesized 3D-printable composite inks by incorporating nano-clay and carbon nanotubes (CNTs) in epoxy. The addition of two-dimensional nanomaterials such as CNTs enables 3D-printed materials to adapt to an external stimulus which allows them to have different characteristics including thermal and electrical conductance.
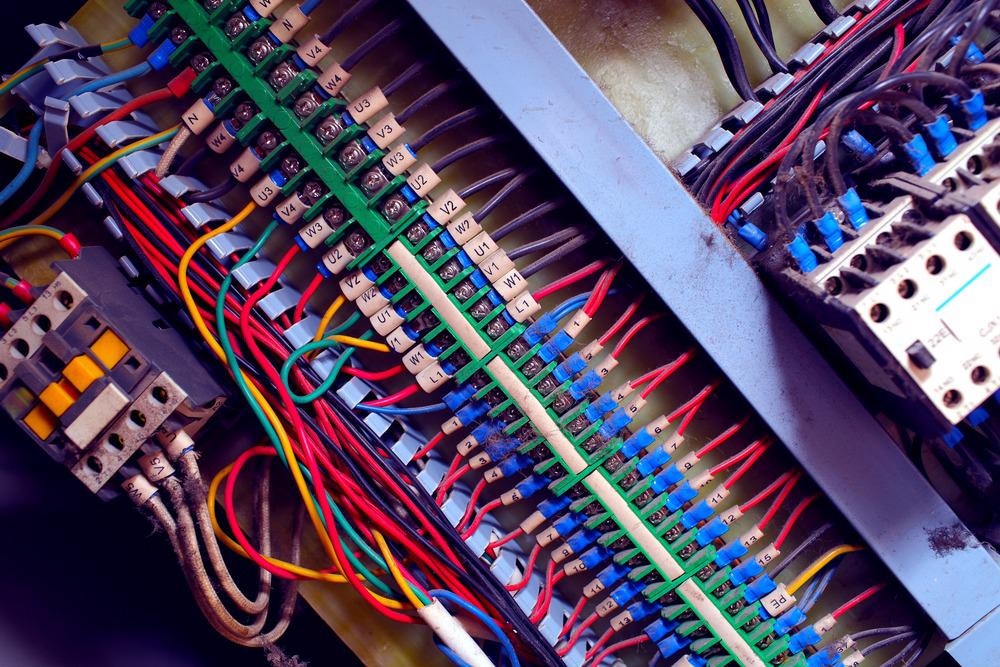
Image Credit: sfam_photo/Shutterstock.com
Additive manufacturing, or 3D printing, has increased in popular demand over recent years in comparison to casting, due to its more efficient and versatile characteristics.
This approach has enabled and increased the creation of more complex shapes with higher precision and efficacy.
Mechanical researchers from the Michigan Technological University have formulated nanocomposite polymeric ink using CNTs which could potentially have the ability to replace traditional epoxies in order for higher functionality.
This research will be explored further within this article, as well as how it can be utilized for applications such as electrical wiring.
Nanocomposite inks, which can consist of various materials such as nickel or silver nanoparticles, have attracted attention due to being a material development approach that is cost-efficient, with high conductivity, and requiring lower temperatures.
Printing processes, a large part of the global market, are competitively seeking more convenient and high functionality methods of fabricating electronic circuits, devices, or wiring.
However, the preparation of conductive ink with optimal properties has become a focal point for researchers in order to overcome challenges such as the ability to print high-quality patterns.
Novel Research into Nanocomposite Ink
Researchers from the Michigan Technological University, Houston, USA, have published their novel research within the journal Additive Manufacturing on their innovative printing process, which optimizes functionality and aims to bridge the gap between real-world applications and 3D printing.
Their nanocomposite polymeric ink utilizes carbon nanotubes, nano-clay, and epoxy as a novel approach to additive manufacturing, or 3D printing, which could possibly provide a higher performance level with better precision and a wider net for creating complex shapes.
It has the potential to be a possible competitor for traditional electrical materials and revolutionize the electronics market.
Parisa Pour Shahid Saeed Abadi, the lead mechanical researcher of this novel research, has commented on this concept, stating:
The gap between the real-world applications of 3D printing and nanomaterials versus nanomaterial 3D printing needs to be closed.
Parisa Pour Shahid Saeed Abadi, Lead Mechanical Researcher, Michigan Technological University
"The gap exists due to lack of control of nanocomposite properties in the 3D-printing process, because we don’t fully understand the process-morphology-property relationship", Dr. Abadi, the lead researcher, went on to say.
Traditional Electrical Wiring
Epoxies are known to be the traditional ‘go-to’ material that utilize versatile polymers for electrical systems, especially for electrical insulation applications.
Characteristics such as excellent adhesion, good chemical and heat resistance, as well as high durability make these systems a desirable foundation for structural composite materials.
An epoxy includes a resin and a curing agent which polymerizes and forms a cured matrix; there are many types, and when used in various combinations they can create distinct cross-linking patterns which result in different characteristics.
This can also include having mineral or metallic fillers that can impact its intrinsic attributes such as its dielectric constant, which is associated with its ability to store electrical energy in response to an electric field.
The Use of Carbon Nanotubes
The novel research undertaken by the mechanical scientists utilized CNTs as a filler material due to its undeniably versatile properties and high performance.
Their focus consisted of synthesizing 3D-printable composite inks through incorporating nano-clay and various concentrations of CNTs such as 0.25, 0.5, and 1 vol%, 0.43, 0.86, and 1.7 wt% in epoxy.
The use of CNTs is significant in electrical applications due to its ability to enhance mechanical and electrical properties.
When analyzing the rheological characterization of the inks created, they found an increased level of complex viscosity, storage, as well as loss moduli after the inclusion of CNTs, with 0.5 vol% being found to be the optimum level of mechanical enhancement.
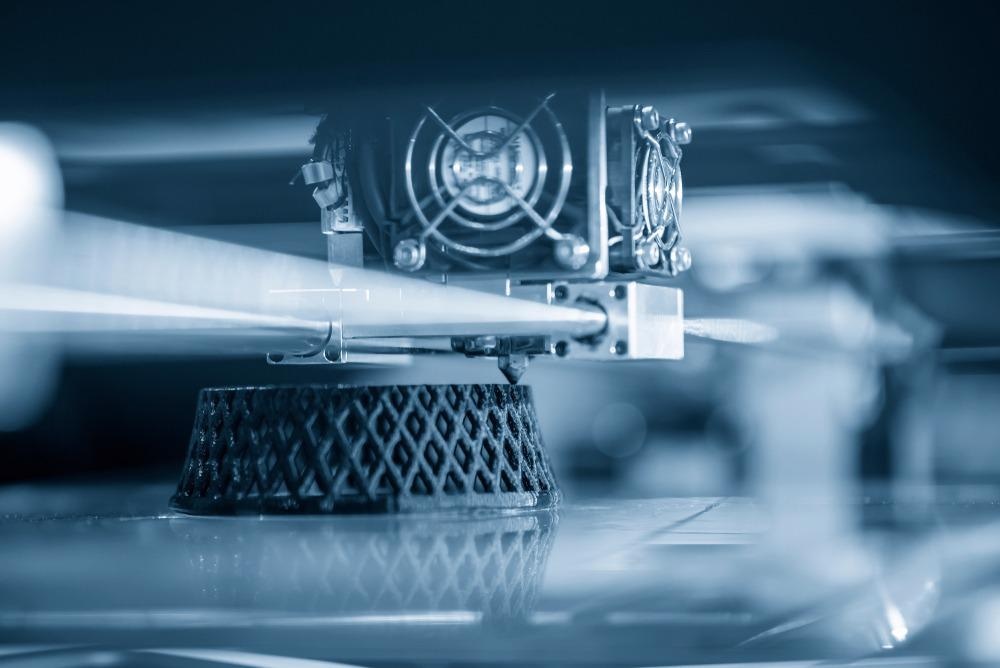
Image Credit: Pixel B/Shutterstock.com
In comparison with just 3D printed epoxy nano-clay nanocomposite structures, the synthesized version with CNTs resulted in an increase in flexural strength by 61%, flexural modulus by 59%, and tensile strength by 31%.
The use of CNTs would enhance the properties of materials such as electrical wiring materials, which would enable the newly found nanocomposite ink material to have a higher performance level.
This novel material can be considered to have a higher level of conductance than metals and traditional epoxies, with remarkable electrical and thermal conductivity due to their nanostructure and the strength of bonds between their carbon atoms.
Nanomaterial Ink Application
The use of nanomaterial ink would be a significant benefit for electrical wiring applications due to the high conductivity level, and this can even be revolutionary for other applications such as use in a circuit board, an airplane’s wing, or even 3D-printed actuators for guiding catheters within blood vessels.
The high strength to weight ratio of this nanomaterial enables it to compete against other strong materials such as steel or aluminum.
In comparison with steel and aluminium, we see 80% weight reduction with epoxy composite with the same strength
Masoud Kasraie, First Author, Michigan Technology University
Additionally, this novel polymer nanocomposite ink can also provide benefits such as corrosion resistance, whereas the nature of some traditional epoxy composites may result in the risk of failure, from breakage to underperformance to the inability to withstand heat and friction over time.
With the ability to maintain high strength and good conductivity, this novel research would be an innovative update to traditional electrical wiring.
Interview: An Unmatched Solution for Nanomaterial Characterization in SEM
The safety function of nanocomposites is also a significant advantage for use in all applications, with normal, less efficient materials enabling a small crack when something breaks, causing a structure to go from having a microscale defect to being broken. Abadi states that “nanocomposite features make bridges in those cracks and don't let the cracks grow. This is one of the mechanisms through which carbon nanotubes increase the mechanical strength of the material."
The use of 3D printing enables near-complete control over the shape and complexity of an object, and the utilization of nanomaterial ink may be revolutionary for many applications, from electrical wiring to medical applications.
Having a more cost-effective, accessible approach to the printing process of complex shapes may be a challenge; however, it could possibly be the start of a more innovative future.
References and Further Reading
Adhesives.org. (2021). [Accessed 10 October 2021].
Electronics For You. (2021). 3D Polymer Nanocomposite Ink For Future Electronics | Electronics For You. [online] Available at: <https://www.electronicsforu.com/technology-trends/research-papers/3d-polymer-nanocomposite-ink-for-future-electronics> [Accessed 10 October 2021].
Kasraie, M. and Pour Shahid Saeed Abadi, P., (2021). Additive manufacturing of conductive and high-strength epoxy-nanoclay-carbon nanotube composites. Additive Manufacturing, 46, p.102098. DOI: https://doi.org/10.1016/j.addma.2021.102098
Pajor-Świerzy, A., Szendera, F., Pawłowski, R. and Szczepanowicz, K., (2021). Nanocomposite Inks Based on Nickel–Silver Core–Shell and Silver Nanoparticles for Fabrication Conductive Coatings at Low-Temperature Sintering. Colloids and Interfaces, 5(1), p.15. DOI: https://doi.org/10.3390/colloids5010015
Disclaimer: The views expressed here are those of the author expressed in their private capacity and do not necessarily represent the views of AZoM.com Limited T/A AZoNetwork the owner and operator of this website. This disclaimer forms part of the Terms and conditions of use of this website.