Recent developments in additive manufacturing and material science have enabled a rapid expansion of PEEK application fields, including the healthcare industry and advanced composites manufacturing.
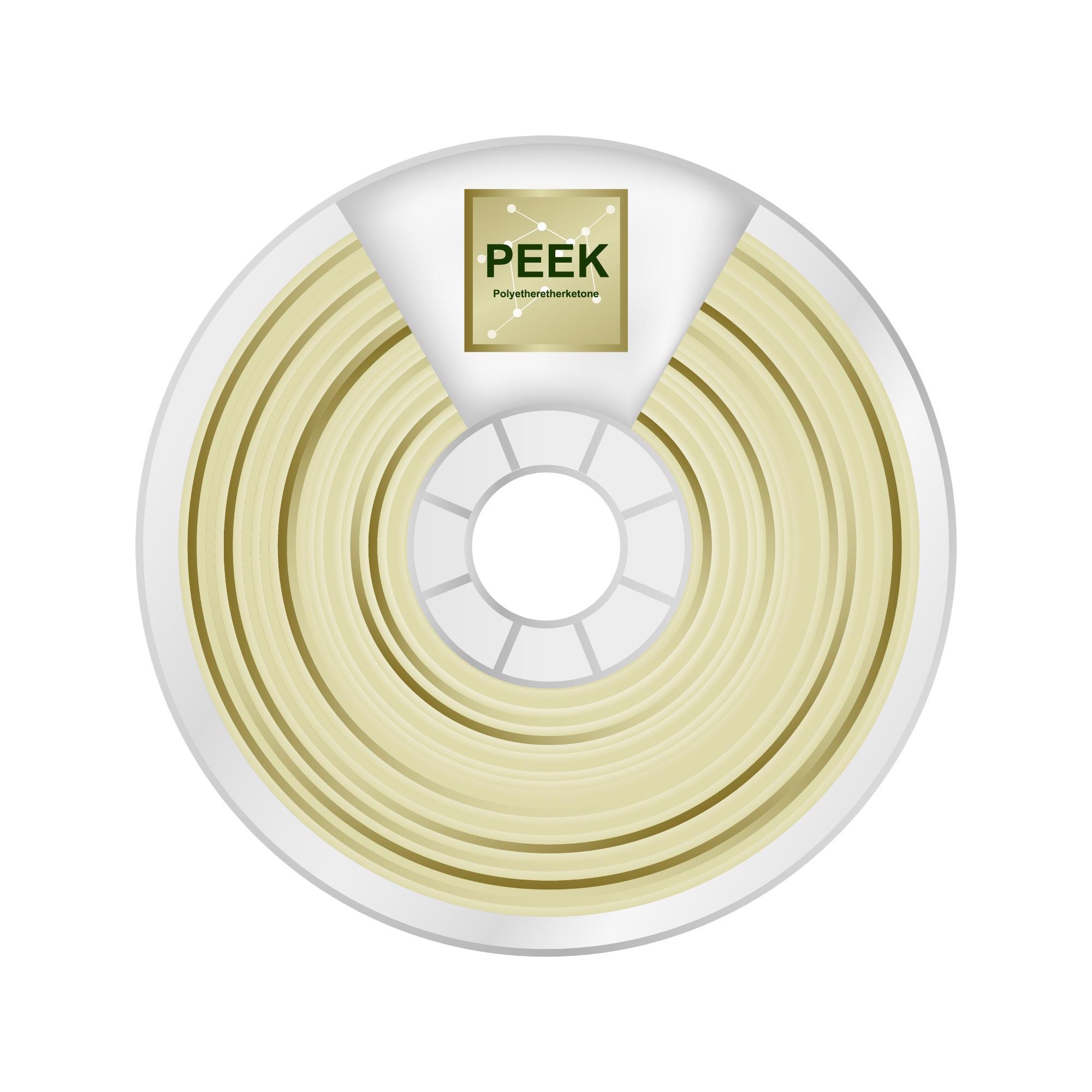
Image Credit: petrroudny43/Shutterstock.com
Since its commercialization in the 1980s, polyether ether ketone (PEEK) became one of the most valued engineering thermoplastics characterized by an unusual combination of high-temperature performance, excellent mechanical strength, and outstanding chemical resistance.
With time, the material evolved and found widespread use in aerospace, automotive, electrical, and electronic industries.
PEEK is one of the most popular modern thermoplastic materials that is used in numerous manufacturing applications. It is a semi-crystalline, high-performance, rigid polymer with a combination of unique properties, such as extremely high thermal, chemical, and wear resistance.
Owing to its high strength-to-weight ratio, PEEK is ideal for weight-critical aerospace applications. It is a material of choice for the manufacturing of electrical and electronic components due to its electrical insulation properties, and it is widely used in chemical manufacturing applications that require long-term mechanical and chemical resistance.
High-Performance Super Polymer
Structurally, PEEK consists of alternating ketone and ether bonds. Although these bonds provide some degree of flexibility, PEEK is still considered a rigid polymer. Because of the stiff aromatic polymer backbone, the material exhibits some of the highest transition temperatures among the commercial polymers, with a functional temperature range of up to 240°C.
Traditionally, PEEK is melt-processed in the temperature range of 370-420°C by conventional methods, such as injection molding, extrusion, and compression molding, facilitated by the presence of ether bonds in the polymer structure. By tuning the processing conditions, the manufacturers can relatively easily control the crystallinity of PEEK and its mechanical properties. However, PEEK processing is more expensive compared to other thermoplastics due to its high melting temperature of 343 °C.
Why PEEK is Becoming a Material of Choice for Demanding Applications
Nevertheless, the outstanding thermal, chemical, and mechanical properties of PEEK, together with the fact that it is a weldable and machinable thermoplastic, made the material a lightweight and cost-efficient replacement for stainless steel, aluminum, and even titanium tubing in aerospace and oil/gas industries. PEEK is also used as a hard-wearing insulator in heavy-duty electrical wiring, while semiconductor manufacturing shifted towards using PEEK wafer carriers that offer better rigidity, chemical resistance, and minimum weight.
The chemically-inert nature of PEEK, together with its wear and temperature resistance, make it extremely well-suited for biomedical applications. Initially, the material was used for the manufacturing of diagnostic equipment and reusable medical devices. Over the last decade, several in-vitro biocompatibility tests revealed that PEEK does not exhibit any mutagenic or cytotoxic effects. As a result, PEEK has been progressively used as a biomaterial for orthopedic implants and prostheses.
More from AZoM: Particle Analysis Applied to Additive Manufacturing Feedstocks
In the last couple of years, a considerable research effort was directed towards combining the qualities of PEEK with the capabilities of additive manufacturing. Such a combination permits the creation of customized implants and scaffolds with complex shapes and structures from a bioinert material that can withstand the harshest conditions.
Challenging Material for 3D Printing Applications
PEEK 3D printing poses some challenges that have been overcome only very recently. For example, the fused filament 3D printing technology requires extruders with an operating temperature of up to 450 °C (much higher than the extrusion temperatures of other plastics like PLA and ABS). In addition, the high viscosity of the molten PEEK requires novel extruder designs with optimized polymer flow. Appropriate cooling of the printed materials is another critical aspect that needs consideration when 3D printing PEKK to minimize the shrinkage and wrappage of the final product.
The rapid development of 3D printing technology and the growing demand for high-temperature 3D printers have prompted companies like Roboze, Intamsys, Bond, Apium, and others to produce increasingly affordable, larger, and easier-to-operate PEEK printers for industrial production and rapid prototyping.
Development of PEEK as a Biomedical Material
More importantly, recently-developed PEEK-based composite materials show enormous potential as 3D printing materials. Novel formulations where organic (carbon fiber or glass fiber) or inorganic (hydroxyapatite) fillers are added into the PEEK filament enable fine-tuning of the mechanical properties of the 3D-printed biomaterials for orthopedics, spine reconstructive surgery, and bone fusion. The 3D-printed PEEK composite biomaterials allow the development of customized patient-specific implants and prosthetics with a precise fit that cannot be accomplished by traditional materials and manufacturing practices.
In a recent study, 3D-printed PEEK implants were used as cartilage prostheses for rib cage skeletal reconstruction as a replacement of natural cartilage which was removed during tumor extraction. Such personalized 3D printed PEEK implants not only improve patient satisfaction and safety but also permit surgeons to rapidly respond to a broader range of patient cases.
Surface modifications and treatments for PEEK implants have already shown a great promise to further improve the biocompatibility of the material. By adding osteogenic agents and improving the bioactivity of PEEK, scientists are aiming to enhance bone in-growth or on-growth to the PEEK implants in the near future.
References and Further Reading
Verma, S. et al. (2021) Developments of PEEK (Polyetheretherketone) as a biomedical material: A focused review. European Polymer Journal, 147, 110295. Available at: https://www.sciencedirect.com/science/article/abs/pii/S001430572100029X?via%3Dihub
Oladapo, B. I., et al. (2021) 3D printing of PEEK and its composite to increase biointerfaces as a biomedical material- A review. Colloids and Surfaces B: Biointerfaces, 203, 111726. Available at: https://www.sciencedirect.com/science/article/abs/pii/S0927776521001703?via%3Dihub
El Magri, A., et al. (2021) An overview on the influence of process parameters through the characteristic of 3D-printed PEEK and PEI parts. High Performance Polymers, 33(8), 862-880. Available at: https://journals.sagepub.com/doi/10.1177/09540083211009961
Yu, Y.-H. and Liu, S.-J. (2021) Polyetheretherketone for orthopedic applications: a review. Current Opinion in Chemical Engineering, 32, 100687. Available at: https://www.sciencedirect.com/science/article/abs/pii/S2211339821000198?via%3Dihub
C. Schwaar (2021) PEEK 3D Printers – The Ultimate Guide [Online] All3dp.com Available at: https://all3dp.com/1/peek-3d-printer (Accessed on 9 February 2022)
D. Maloney (2022) Extreme Thermal Mods For 3D Printing Exotic Materials [Online] Hackaday.com Available at: https://hackaday.com/2022/01/19/extreme-thermal-mods-for-3d-printing-exotic-materials (Accessed on 9 February 2022)
Rinaldi, M. et al. (2021) Additive Manufacturing of Polyether Ether Ketone (PEEK) for Space Applications: A Nanosat Polymeric Structure. Polymers, 13, 11. Available at: https://www.mdpi.com/2073-4360/13/1/11
Disclaimer: The views expressed here are those of the author expressed in their private capacity and do not necessarily represent the views of AZoM.com Limited T/A AZoNetwork the owner and operator of this website. This disclaimer forms part of the Terms and conditions of use of this website.