Polymers are occasionally treated in solutions for end-use in applications (where the polymer is dissolved in a solvent). Examples of this include spinning fibers and coating substrates with spin. The polymer is susceptible to oxidation when it is in solution. Antioxidants are, therefore, a component of polymer products.
This article demonstrates the use of viscometers to analyze the impact of antioxidants on a polyethylene solution.
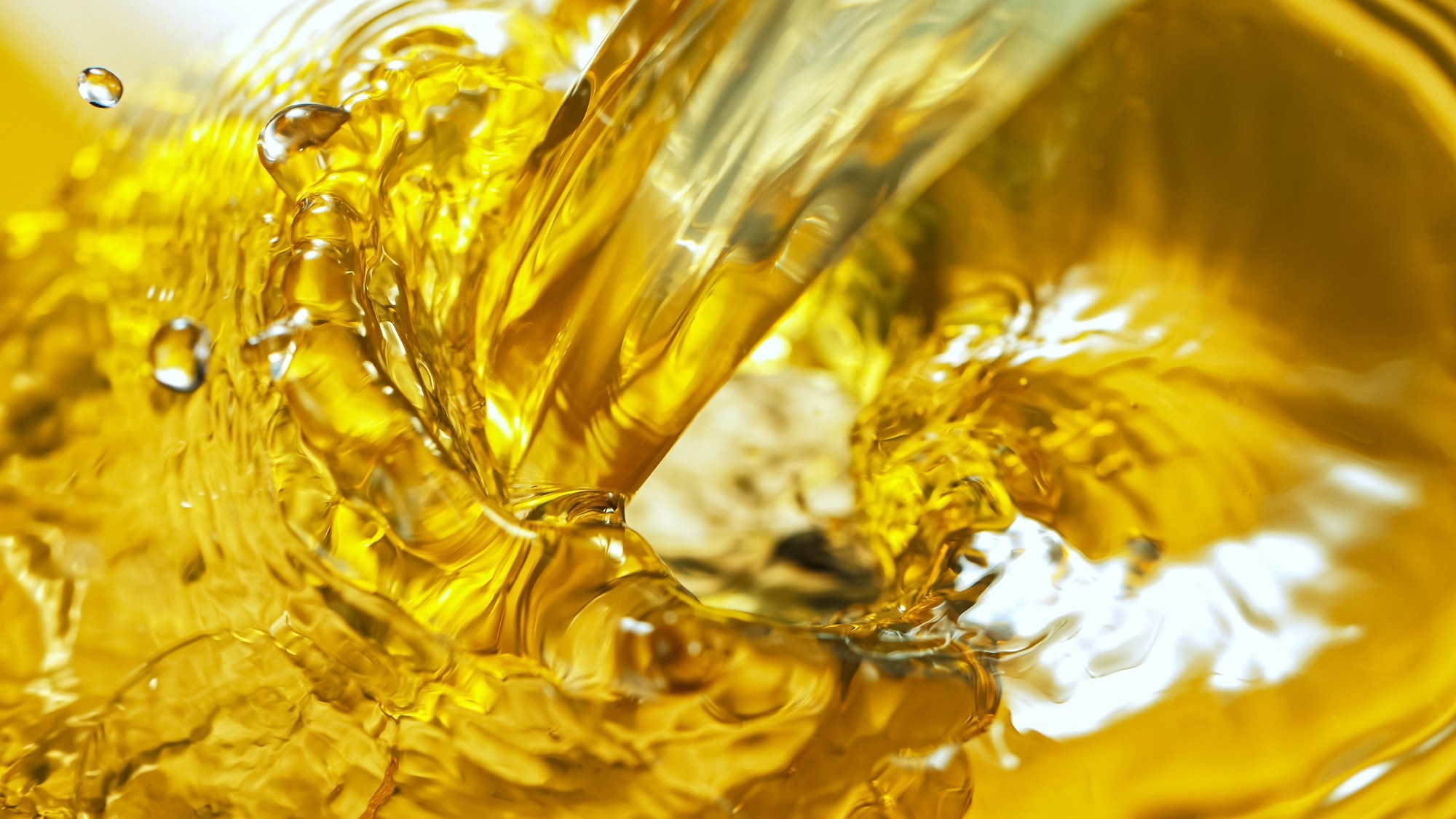
Image Credit: Lukas Gojda/Shutterstock.com
Background
In the polymer industry, dilute solution viscosity, or DSV, is used to describe the macromolecules in a polymeric material. The intrinsic viscosity, [η], in particular, gives a gauge of molecular size and a means of determining molecular weight. Practitioners in the polyolefin industry have come to understand the value of DSV in this way.
They regularly monitor DSV using either proprietary techniques or common test methods like D1601 and ISO 1628-3. The addition of antioxidant to the solvent is advised by both D1601 and ISO 1628-3 to prevent the oxidative breakdown of the polymer molecules. The remainder of this article will provide a summary of an investigation into the consequences of not adding an antioxidant during the sample preparation procedure.
Experimental
At 150 °C for 90 minutes, three polyolefin samples were dissolved in around 60 mL of decalin in sealed bottles that were set in a heating block with magnetic stirring. The solutions were created using the Solution Preparation System from Cannon Instruments, which determines and dispenses a volume of solvent based on the measured mass of the polymer sample and corresponding to a target concentration.
For these solutions, the desired concentration was 0.0200 g/dL. The Cannon Instruments Polyvisc automated viscometer, with an auto sampling function nested in an Airbath® that retains the solutions at the measurement temperature of 135 °C, was used to measure the polymer after it had been dissolved. Aliquots were transferred into vials while still hot and placed in the viscometer.
Parallel batches of the sample preparation were done with and without the addition of an antioxidant to the decalin. The processing of the viscosity measurements was done in accordance with the Polyvisc protocol, which involves successively pouring sample solutions from vials under the tip of a glass viscometer tube.
A bulb situated above a capillary section and in-between two optical sensors was filled with the aspirated solution. As the solution drains from the bulb and travels through the capillary, the sensors start and stop a timer. The average flow time was utilized to calculate the dilute solution viscosities after the drainage time was repeatedly measured.
Kinematic viscosity:
t is the average flow time
“Tube” constant, C = 0.0101236 cSt/s
“Kinetic energy” coefficient, E= 87.357270 cSt⋅s2
C & E values are determined by a calibration tool in the viscometer software.
Relative viscosity, 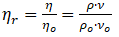
Specific viscosity, ηsp = ηr – 1
Reduced viscosity, 
Inherent viscosity, 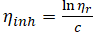
Intrinsic viscosity, 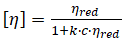
ρ is density of solution at the measurement temperature
ρo is density of solution at the measurement temperature
η is the dynamic viscosity of the solution
ηo is the dynamic viscosity of the solvent
k is the Schulz-Blaschke coefficient
There is a choice of several equations for the calculation of the intrinsic viscosity. For this experiment, the Schulz-Blaschke equation is used, which appears in ISO 1628-3 with a recommended value of k = 0.27.
NOTE: At the low concentration of 0.0200 g/dL, ≅ ρo, so that ηr becomes simply
.
Mark-Houwink-Sakurada equation: [η] = K * MWa solved for MW as 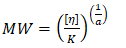
*K is the prefactor for the MHS equation, K = 0.00062 dL/g
*a is the exponent for the MHS equation, a = 0.07
*Referenced from [1]
Results and Discussion
Measured flow times, derived viscosities, and molecular weights for the two cases of solutions prepared with and without an antioxidant (AO) are compared in Table 1. Three UHMWPE samples were tested in duplicate solutions, with nominal molecular weights of 2.8 MDa (UHMWPE–2.8 M), 2.1 MDa (UHMWPE–2.1 M), and 1.5 MDa (UHMWPE–1.5 M).
Table 1. Molecular weight determination from intrinsic viscosity measurements for UHMWPE samples of three MWs. One data set used an antioxidant in the solvent, and a second set omitted an antioxidant. Source: CANNON Instrument Company
Sample |
AO |
t (s) |
ν (cSt) |
ηred (dL/g) |
[η] (dL/g) |
MW (Dalton) |
UHMWPE-2.8M |
yes |
97.757 |
0.9805 |
22.634 |
20.169 |
2,793,000 |
UHMWPE-2.8M |
yes |
97.987 |
0.9829 |
22.809 |
20.308 |
2,821,000 |
UHMWPE-2.1M |
yes |
92.163 |
0.9227 |
18.354 |
16.699 |
2,133,000 |
UHMWPE-2.1M |
yes |
92.237 |
0.9235 |
18.411 |
16.746 |
2,142,000 |
UHMWPE-1.5M |
yes |
86.917 |
0.8683 |
14.325 |
13.296 |
1,540,000 |
UHMWPE-1.5M |
yes |
86.833 |
0.8675 |
14.261 |
13.241 |
1,531,000 |
UHMWPE-2.8M |
none |
86.237 |
0.8613 |
13.982 |
13.000 |
1,492,000 |
UHMWPE-2.8M |
none |
84.190 |
0.8400 |
12.400 |
11.621 |
1,271,000 |
UHMWPE-2.1M |
none |
82.995 |
0.8275 |
11.474 |
10.805 |
1,145,000 |
UHMWPE-2.1M |
none |
81.865 |
0.8157 |
10.598 |
10.025 |
1,029,000 |
UHMWPE-1.5M |
none |
80.133 |
0.7976 |
9.253 |
8.813 |
856,000 |
UHMWPE-1.5M |
none |
79.318 |
0.7891 |
8.619 |
8.236 |
777,000 |
UHMWPE-2.8M |
none |
87.660 |
0.8761 |
13.438 |
12.529 |
1,415,000 |
UHMWPE-2.8M |
none |
86.837 |
0.8675 |
12.819 |
11.989 |
1,329,000 |
UHMWPE-2.8M |
none |
86.437 |
0.8634 |
12.518 |
11.725 |
1,287,000 |
UHMWPE-2.8M |
none |
86.013 |
0.8590 |
12.199 |
11.445 |
1,243,000 |
A comparison is made in Table 1 between the measured flow times and derived viscosities and molecular weight for the two cases of solutions that were prepared with and without an antioxidant (AO). Duplicate solutions of three UHMWPE samples were measured; the nominal molecular weights were as follows; 2.8M Da (UHMWPE-2.8M) and 2.1M Da (UHMWPE-2.1M) and 1.5M Da (UHMWPE-1.5M).
For the average of replicate measurements, the molecular weight degradation was 51%, 49%, and 47% with respect to the three samples, UHMWPE-2.8M, UHMWPE-2.1M, and UHMWPE-1.5M. Figure 1 compares the levels of degradation.
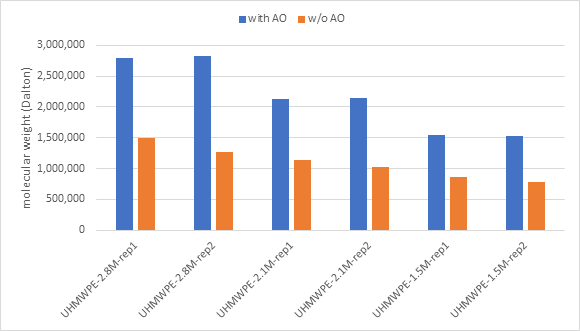
Figure 1. Molecular weight of three UHMWPE samples in duplicate solutions. Image Credit: CANNON Instrument Company
It was also discovered that in the absence of AO, degradation took place from the time the initial aliquot was measured to the subsequent replication (see the orange columns in Figure 1 that show a decline in MW for replicate measurements in the “w/o AO” series).
This discovery led to the following experiment, including four aliquots that were measured at intervals of around 30 minutes. These four samples are the last four entries in Table 1, and Figure 2 shows the results for the inherent viscosity reduction.
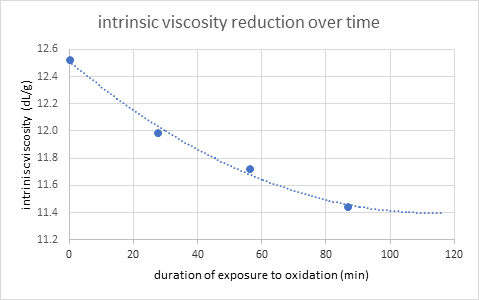
Figure 2. Intrinsic viscosity reduction measured in a sequence of four UHMWPE-2.8 M sample solutions without AO. Image Credit: CANNON Instrument Company
Conclusions
It has been demonstrated that adding an AO to the solvent is necessary to maintain the molecular weight of UHMWPE in a dilute solution at 135 °C at a concentration of 0.0200 dL/g.
When an AO was skipped during the solution preparation process, MW was reduced by around 50%.
The IUPAC name of the AO employed is pentaerythritol tetrakis(3,5-di-tert-butyl-4-hydroxyhydrocinnamate). It is referenced in ASTM D1601 as tetrakis[methylene 3-(3’,5’-di-tert-butyl-4’-hydroxphenyl) propionate]methane. Along with three other suggestions for AO, this AO was also mentioned in ISO 1628-3 as tetrakis[methylene 3-(3',5'-di-tert-butyl-4'-hydroxphenyl) n-propionate] methane.
The first sign of degradation was a decrease in intrinsic viscosity in the second replication of the DSV measurement, which was conducted after 27.6 minutes. The trend continued in the third and fourth measures, which were taken after 86.7 minutes of total oxidative exposure. In this time period, a second-order polynomial was used to simulate the trend.
References
[1] Brandrup, J, E H. Immergut, and Eric A. Grulke. Polymer Handbook, Vol 2, Fourth Edition, page VII/8. New York: Wiley, 1999. Print.
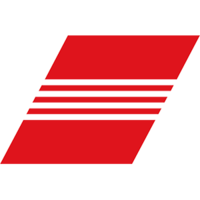
This information has been sourced, reviewed and adapted from materials provided by CANNON Instrument Company.
For more information on this source, please visit CANNON Instrument Company .