Heat treatment is a critical process used in various industries to enhance the mechanical properties of metals and alloys. Heat treatment furnaces play a pivotal role in this process, providing controlled heating environments that modify the material's structure. In this article, we will delve into different types of heat treatment furnaces and explore their advantages and disadvantages, helping you make informed decisions for your specific heat treatment needs.
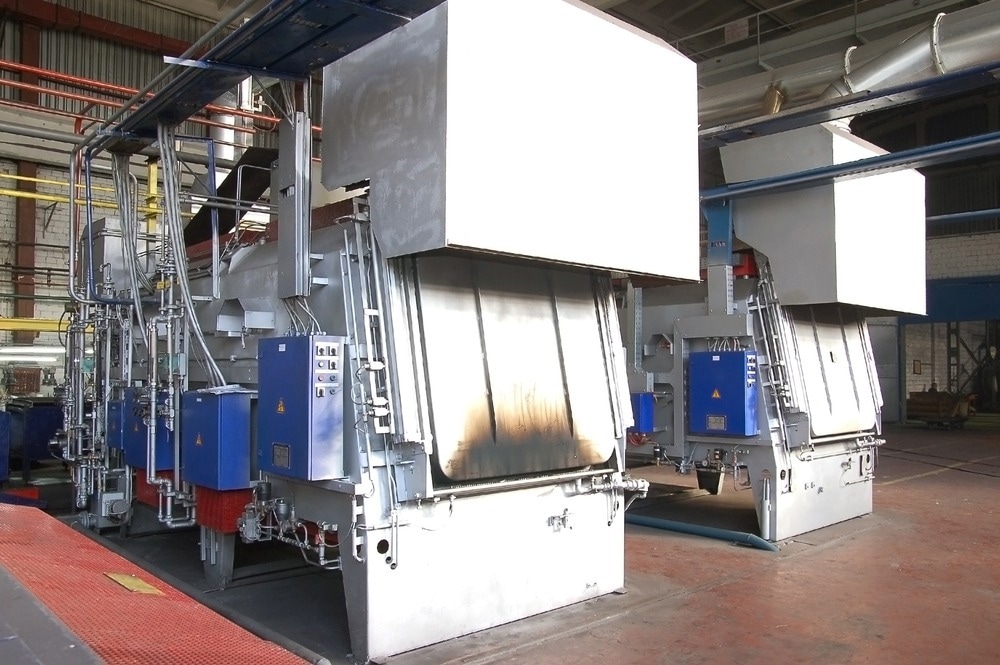
Image Credit: Mikheyev Viktor/Shutterstock.com
What is Heat Treatment?
Heat treatment is a controlled heating and cooling process applied to metals and alloys to alter their physical and mechanical properties. This process can significantly impact the hardness, strength, toughness, and other essential characteristics of materials.
Importance of Heat Treatment Furnaces
Heat treatment furnaces provide a controlled environment to perform specific heat treatment processes precisely and consistently. They enable uniform heating, precise temperature control, and controlled cooling rates, ensuring that desired material properties are achieved.
According to research published in the International Journal of Thermal Sciences, some common heat treatment methods are Annealing, Quenching, Tempering, Normalizing, Case Hardening, and Martensitic Transformation.
Types of Heat Treatment Furnaces
Salt Bath Furnaces
Salt bath furnaces, also known as salt pot furnaces, use molten salt as the heating medium. Salt bath furnaces are a specialized type of heat treatment equipment used to enhance the properties of metals and alloys. The process involves immersing the workpiece into a bath of molten salt at high temperatures, creating a controlled environment for various heat treatment processes.
They are particularly suitable for processes like carburizing, carbonitriding, and nitrocarburizing. A typical salt bath furnace consists of several essential components. The heating element provides the necessary heat to melt the salt and maintain the desired temperature, the insulated Chamber encloses the salt bath to ensure heat retention and safety, and the temperature Control System: Allows precise temperature adjustments for different heat treatment processes.
- Advantages of Salt Bath Furnaces
The direct contact between the molten salt and the workpiece enables rapid and uniform heating, leading to consistent and predictable heat treatment results. Salt bath furnaces have reduced oxidation, as the salt creates a protective atmosphere. They are also suitable for small and intricate parts due to easy immersion. Salt bath furnaces ensure even temperature distribution throughout the bath, ensuring uniform heat treatment across all parts of the workpiece.
- Disadvantages of Salt Bath Furnaces
Salt bath furnaces have a limited temperature range based on the type of salt used. After heat treatment, the workpiece may retain salt residue, necessitating thorough cleaning to avoid any adverse effects on subsequent processes or end products. They also require high maintenance to prevent salt leakage and corrosion.
Box Furnaces
Box furnaces, also called batch furnaces, are versatile and widely used for various heat treatment processes. They consist of an insulated chamber to accommodate the workload and provide controlled heating. The box furnace's main purpose is to provide a controlled heating environment for various heat treatment processes.
A research paper published in Energies described the working of batch furnaces. In the batch furnace, the workpieces are loaded into the insulated chamber and subjected to controlled heating at specific temperatures. The furnace's heating elements generate the required heat, and the insulation helps maintain uniform temperature distribution throughout the chamber. Once the heat treatment process is complete, the workpieces are removed from the furnace.
- Advantages of Box Furnaces
Box furnaces offer versatility in accommodating various shapes and sizes of workpieces, making them suitable for custom heat treatment jobs. They offer a wide temperature range suitable for various heat treatment processes. Box furnaces are easy to operate and do not require high maintenance.
- Disadvantages of Box Furnaces
Box furnaces require longer heating and cooling times due to the batch processing nature. They have less uniformity due to potential temperature variation within the chamber. They also have limited automation capabilities compared to continuous furnaces. The initial investment for purchasing a box furnace can be higher, especially for advanced models with additional features.
Continuous Furnaces
Continuous furnaces, as the name suggests, are industrial heat treatment furnaces designed to handle a continuous flow of workpieces. Unlike batch furnaces, which process a limited number of workpieces at once, continuous furnaces offer a continuous and uninterrupted heat treatment process. They are ideal for high-volume production and continuous heat treatment processes.
Continuous furnaces offer a continuous flow of workpieces through the heating chamber on a conveyor or roller system. The furnace's heating elements generate the required heat, and the conveyor system ensures a steady flow of workpieces through the heating chamber. As the workpieces move through the furnace, they undergo the specified heat treatment process.
According to the research published in Energy, continuous furnaces have high production rates and efficiency due to continuous processing. Continuous furnaces ensure uniform heating of workpieces throughout the entire process. The consistent heat distribution leads to uniform material properties and improved product quality. They also have reduced labor requirements.
However, continuous furnaces have limited flexibility in handling small batches or complex geometries. They require higher energy consumption during continuous operation. Continuous furnaces are complex systems, and their maintenance requires specialized knowledge and resources.
Vacuum Furnaces
Vacuum furnaces are specialized heat treatment furnaces that operate in a vacuum or low-pressure environment. Unlike conventional heat treatment methods that use atmospheric air, vacuum furnaces ensure a clean and contamination-free environment during the heat treatment process.
In a vacuum furnace, the air is removed from the heating chamber, creating a vacuum or low-pressure environment. The workpieces are then heated without exposure to gases or impurities. The absence of air prevents oxidation and other chemical reactions during the heat treatment process.
Vacuum furnaces have minimized surface oxidation and decarburization due to the absence of air. They offer precise control of the atmosphere and heating conditions. In a vacuum environment, heat transfer occurs primarily through radiation, which provides more uniform and efficient heating compared to conduction or convection. Vacuum furnaces can achieve high temperatures and pressures, making them suitable for advanced heat treatment processes.
However, vacuum furnaces require a significant initial investment due to their advanced technology and sophisticated construction. They have slower heating rates compared to other furnace types. Vacuum furnaces are more suitable for batch processing, which may limit their production volume compared to continuous furnaces.
Induction Heating Furnaces
Induction heating furnaces are specialized heat treatment equipment that uses electromagnetic induction to heat conductive materials. Unlike traditional heating methods that rely on direct contact, induction heating creates an electromagnetic field that induces heat directly into the workpiece.
In an induction heating furnace, an alternating current is passed through a copper coil, creating a powerful electromagnetic field. When a conductive material is placed within this field, eddy currents are induced within the material, generating heat. The heat is produced internally, ensuring efficient and uniform heating of the workpiece.
Induction heating furnaces offer high heating efficiency with minimal heat loss, ensuring precise and controlled heat treatment processes. Induction heating provides rapid heating rates, allowing for quick processing times and improved productivity. The efficient heating process of induction furnaces results in reduced energy consumption, making them more environmentally friendly.
Induction heating furnaces require a significant initial investment, including the cost of specialized equipment and power supplies. Operating induction heating furnaces requires skilled personnel with expertise in induction heating principles and safety procedures. Induction heating is most effective for surface heating, which may limit its application in certain heat treatment processes.
The process of heat treatment is among the highly effective processes utilized in the materials science industry for obtaining the desired physiochemical properties of the materials. These furnaces carefully monitor the treatment process and enable precise and controlled modification of material properties. The selection of a furnace depends on the material, temperature requirements, and production volume. Keeping in view all the parameters, selecting the most viable heat treatment furnace results in obtaining the most viable results.
More from AZoM: The Best High-Temperature Alloys for Aerospace Applications
References and Further Reading
Joachimiak et. al. (2019). Analysis of the heat transfer for processes of the cylinder heating in the heat-treating furnace on the basis of solving the inverse problem. International Journal of Thermal Sciences, 145, 105985. https://doi.org/10.1016/j.ijthermalsci.2019.105985
Filipponi et. al. (2016). Thermal analysis of an industrial furnace. Energies, 9(10), 833. https://doi.org/10.3390/en9100833
Jabari, F. et. al. (2018). Design and robust optimization of a novel industrial continuous heat treatment furnace. Energy, 142, 896-910. https://doi.org/10.1016/j.energy.2017.10.096
Disclaimer: The views expressed here are those of the author expressed in their private capacity and do not necessarily represent the views of AZoM.com Limited T/A AZoNetwork the owner and operator of this website. This disclaimer forms part of the Terms and conditions of use of this website.