Dianhydride curing agents, such as benzophenone tetracarboxylic dianhydride (BTDA®), enhance high-temperature performance in epoxy formulations.
This article will examine sample formulations for liquid epoxy systems suitable for elevated-temperature applications, such as adhesives, casting compounds, and composites. The discussion will encompass the curing behavior of these formulations using various accelerators and the resulting glass-transition temperatures.
Introduction
Thermoset epoxies hold significant relevance in applications subjected to demanding operating conditions.
Many epoxy products may lose effectiveness when exposed to extreme service conditions, including high temperatures, chemical exposure, and mechanical stresses. Some may perform well initially but experience a decline in integrity over time.
Conventional solutions often involve transitioning from epoxy to alternative chemistries like cyanate ester, bismaleimide, and polyimides, which, although technically suitable, can introduce complexity to the application processes and, in some cases, prove economically unfeasible.
Aromatic dianhydrides, like BTDA® (3,3’,4,4’-benzophenone tetracarboxylic dianhydride), have long been recognized for their ability to promote robust crosslinking in epoxy formulations.1,2
Refer to Table 1 for detailed information on this molecule and Figure 1 for its chemical structure. The resulting dense crosslinking, combined with the unique structure of this dianhydride, yields thermosets characterized by high glass-transition temperatures and exceptional heat resistance.
These formulations also offer superior dielectric properties, mechanical strength, and chemical resistance, making them suitable for various applications, including electrically insulating encapsulants, chemically resistant coatings, adhesives, and composites like prepregs.
It is worth noting that, in many cases, dianhydrides serve applications in demanding conditions while employing simple bisphenol-A-based epoxy resins (Figure 1).
Where necessary, blending dianhydrides with specialty resins such as cycloaliphatic epoxides, epoxy novolacs, and other multifunctional resins can further elevate performance levels.
Table 1. Chemical & Physical Characteristics of JAYHAWK BTDA®.
Source: Jayhawk Fine Chemicals Corporation
Chemical Name: |
3,3’,4,4’-benzophenone tetracarboxylic dianhydride |
Molecular Wt. (MW) |
322 g/mole |
Anhydride Equiv. Wt. (AEW) |
161 g/eq. |
Physical Form |
Off-white fine powder |
Specific Gravity |
1.6 |
Melting point |
220-230 °C (dissolves in & reacts with epoxy resin at lower temperatures) |
For a given epoxy system, its heat resistance, chemical resistance, glass transition temperature, and electrical insulation performance closely correlates with its cross-linking degree.
Among these properties, the glass transition temperature (Tg) is relatively easier to measure for comparisons with alternative formulations. Typically, standard epoxy resins based on bisphenol A offer maximum glass transition temperatures, as indicated in Table 2, depending on the chosen curing agent.
As shown in the table and this article demonstrates, dianhydrides result in remarkably high Tg values when used in conjunction with simple epoxy resins.
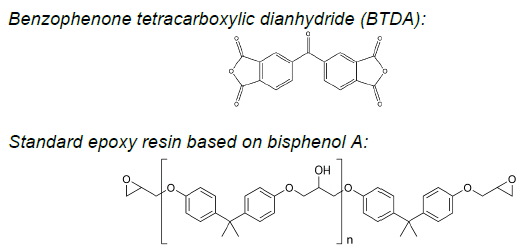
Figure 1. Chemical structures of 3,3’,4.4’-benzophenone tetracarboxylic dianhydride (BTDA) and simple epoxy resins based on bisphenol A. Image Credit: JAYHAWK Thermoset Additives
Table 2. Typical maximum glass-transition temperatures (Tg’s) achievable using standard epoxy resin based on bisphenol A, based on the choice of curing agent. Source: Jayhawk Fine Chemicals Corporation
Curing Agent |
Typical Maximum Achievable Tg (°C) |
Dicyandiamides |
125 |
Cycloaliphatic amines, e.g.,
Isophorone diamine (IPD) |
150 |
(Mono) Anhydrides, e.g.,
Methyl tetracarboxylic anhydride (MTHPA)
Nadic methyl anhydride (NMA) |
150
175 |
Aromatic Amines, e.g.,
4,4’-Methylenedianiline (MDA) |
180 |
Dianhydrides, e.g.,
3,3’,4,4’- BenzophenoneTetracarboxylic
Di-Anhydride (BTDA)
|
~240 |
Special Stoichiometric Treatment of Dianhydride-Epoxy Formulations
Several essential considerations must be taken into account when designing dianhydride-epoxy formulations. Dianhydrides induce high levels of crosslinking in epoxy formulations through esterification reactions. A detailed examination of the intricate reaction mechanism falls beyond the scope of this article.3-6
Figure 2 outlines a simplified two-step esterification reaction model embraced by the epoxy industry.
A single epoxide group reacts with one anhydride group in the overall esterification reaction. Initially, this implies an obligatory stoichiometric ratio of anhydride to epoxide groups (referred to as the A/E ratio) of 1.0. However, the optimal A/E ratios are considerably less than 1.0 for most dianhydride-epoxy formulations.
There exist two primary reasons for this phenomenon. Firstly, an A/E ratio < 1.0 accounts for the side reaction known as epoxy etherification (or homopolymerization), which can deplete epoxides without consuming anhydride groups, as depicted in Figure 3.7
Without excess epoxides, this side reaction results in a cured epoxy containing residual, unreacted anhydride groups (some possibly converted to acid). In specific applications, these residual functional groups can be detrimental to the long-term performance of the cured epoxy.
Practical formulations typically involving liquid epoxy resins and mono-anhydrides (e.g., methyltetrahydrophthalic anhydride (MTHPA), nadic methyl anhydride (NMA), etc.) employ A/E ratios as low as 0.90.
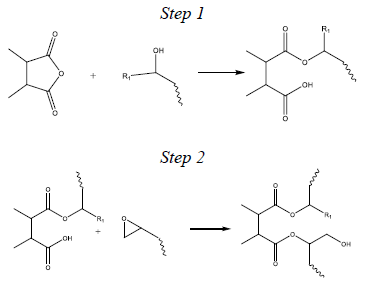
Figure 2. A simplified two-step cure mechanism for the esterification reaction between epoxides and anhydride groups which leads to crosslinking. Image Credit: Jayhawk Fine Chemicals Corporation
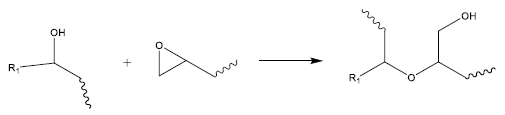
Figure 3. Epoxy etherification (homopolymerization) is a side reaction that can consume epoxide functional groups without using up anhydrides. Image Credit: Jayhawk Fine Chemicals Corporation
However, when transitioning from a monoanhydride to a dianhydride curing agent, an even lower A/E ratio is required for optimal properties. For instance, in the case of BTDA, A/E ratios around 0.5 prove to be significantly more effective.
This is due to the remarkably high levels of crosslinking induced by BTDA. Near-stoichiometry, formulations may undergo vitrification well before complete curing, entrapping unreacted functional groups and potentially compromising long-term performance.8
While post-curing at elevated temperatures can lead to full cure, it may result in excessively high crosslink density and suboptimal performance. Therefore, using BTDA at low dosage rates helps manage the degree of crosslinking and optimize properties.
Most surplus epoxide groups are expected to be consumed via the etherification side-reaction (epoxy homopolymerization).
In this manner, the epoxy formulator can intentionally introduce a predetermined degree of this side reaction for an effective formulation.
The ideal A/E ratio for a specific application is determined experimentally, and Table 3 provides initial recommendations. Consequently, the dosage of BTDA in an epoxy formulation is calculated using the following equation:
BTDA (in phr*) = [100 x 161x (A/E)] / [EEW of resin]
*phr = parts per hundred parts of epoxy resin by weight
Table 3. Suggested ranges for anhydride/epoxide equivalent ratio (A/E ratio) for BTDA-cured epoxy formulations, based on resin epoxy equivalent weight (EEW). Source: Jayhawk Fine Chemicals Corporation
Epoxy Resin EEW, g/eq. |
Example resin types |
Suggested A/E ratios |
190 or less |
Liquid epoxy resins (BPA, BPF, cycloaliphatics, multifunctional, epoxy novolac resins) |
0.5 or lower |
500 – 900 |
BPA Solid epoxy resins, Type 1-4 |
0.6 – 0.8 |
> 900 |
BPA Solid epoxy resin, Type 5 & higher |
0.8 – 1.0 |
Model Formulations Using BTDA and Simple Liquid Resins
A study investigated the attainable glass transition temperatures (Tg) achievable with basic epoxy resins derived from bisphenol A when cured with BTDA (dianhydride).
As previously mentioned, the Tg of a thermoset system serves as a valuable indicator of its crosslink density, which, in turn, impacts various performance characteristics, such as thermal resistance, chemical resistance, and dielectric performance.
The curing behavior of these formulations was analyzed using differential scanning calorimetry. The chosen epoxy resin possessed a nominal viscosity of 8,000 cps and an EEW of 181, in contrast to the more common standard resin with 12,000 cps and 189 EEW.
BTDA was employed in its micronized form, with a median particle size specification of approximately 2 to 5 microns. An A/E ratio of 0.5 was applied, indicating that only half the stoichiometric weight of BTDA was used for a given weight of epoxy resin.
A small quantity of fumed silica was incorporated to enhance sag resistance and replicate commercial formulations, and the formulation details are provided in Table 4. An array of curing accelerators was chosen, as outlined in Table 5.
Sample Preparation and Characterization
Each formulation was mixed using a FlackTek SpeedMixer® DAC 150, with a total mass of 20 grams, for one minute at 1000 rpm, followed by two minutes at 2000 rpm. Subsequently, each formulation was cured for 24 hours at 200 °C for subsequent analysis of Tg using differential scanning calorimetry (DSC) and dynamic mechanical analysis (DMA).
The cured specimens were given ample time to equilibrate to ambient temperature before undergoing testing. The instruments employed were a DSC Q100 and a DMA TA 800, both from TA Instruments.
For Tg determination through DSC, pre-weighed specimens were initially oven-cured in aluminum DSC pans. These specimens were then subjected to thermal scanning in the DSC, ranging from 30 °C to 300 °C, at a ramp rate of 40 °C/min.
Table 4. Model formulation for evaluating cure behavior and achievable glass transition temperatures using BTDA and a simple liquid epoxy resin. Source: Jayhawk Fine Chemicals Corporation
Component |
Parts by wt. |
Bis-A epoxy resin (EEW 181) |
100.0 |
BTDA micronized powder (@ 0.5 A/E)* |
45.0 |
Fumed silica |
0.5 |
Selected catalyst (see Table 5) |
1.0 |
TOTAL |
146.5 |
* A/E = ratio of anhydride equivalents to epoxide equivalents in the formulation
Table 5. The selection of cure catalysts (accelerators) was evaluated in this study. Source: Jayhawk Fine Chemicals Corporation
Catalyst Type |
Name / Designation |
Physical Form |
Quaternary
ammonium salt |
BV-CAT 7 *
(Organic ammonium chlorides) |
Liquid |
Imidazole |
EMI-24
(2-ethyl 4-methyl imidazole) |
Liquid |
Imidazole |
AMI-2
(2-methyl imidazole) |
Solid powder |
Imidazole |
2P4MZ
(2-phenyl 4-methyl imidazole) |
Solid powder |
Zinc Chelate |
Zinc acetyl acetonate |
Solid powder |
* Blended catalyst formulation, obtained from Broadview Technologies.
Specimens for DMA testing were oven-cured in aluminum molds. The following test parameters were applied for DMA testing:
- Thermally equilibrate at 30 °C
- Thermally ramp at 3 °C/min. from 30 °C to 330 °C
- Strain amplitude: 1.5 μm
- Frequency: 1 Hz
Using hermetically sealed aluminum pans, uncured samples were also examined for curing behavior in the DSC. A 10 °C/min thermal ramp was applied, ranging from 30 °C to 300 °C, under a nitrogen purge rate of 50 ml/min.
Results and Discussion
The Tg values for the cured specimens in this study proved challenging to detect accurately via DSC, as illustrated in Figure 4.
Since DSC detects Tg by monitoring changes in the polymer’s specific heat (Cp) during the glass transition, such results suggest that these cured specimens experience a relatively minor alteration in specific heat at their Tg.
This phenomenon is common in epoxies cured with BTDA and can be expected due to these polymers' substantial crosslinking.
In a typical thermoset, the polymer segments between crosslinks become considerably mobile above their glass-transition temperature, resulting in changes in various properties, such as specific heat, modulus, dielectric strength, and even chemical resistance.
In highly cross-linked polymers, the segments between crosslinks are too short to significantly increase their mobility when the temperature exceeds Tg. Consequently, Tg-induced alterations in numerous properties are considerably smaller in densely cross-linked thermosets than lightly cross-linked counterparts.
This phenomenon has been discussed in the thermoset polymer literature, for instance, using DSC and modulus analysis.9,10
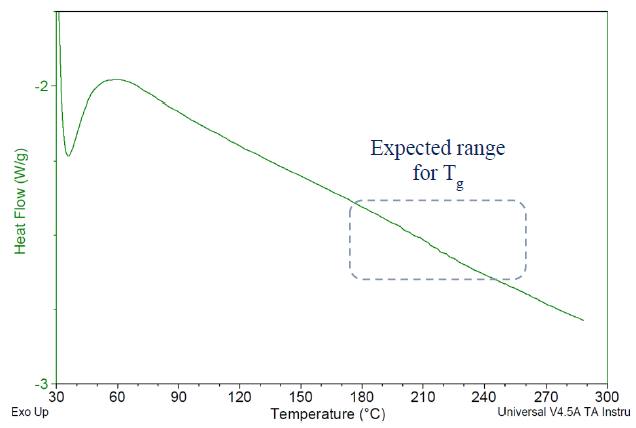
Figure 4. DSC thermogram for Bisphenol A based liquid epoxy resin, cured with BTDA at 0.5 A/E ratio, using BV-CAT-7 catalyst. Cured 24 h/200 C. Glass transition appears too faint to be properly detected via DSC. Image Credit: Jayhawk Fine Chemicals Corporation
The Tg-induced drop in modulus occurs on a logarithmic scale, making it far easier to detect via thermo-mechanical tests such as DMA, as shown in Figure 5 (for the same formulation as in Figure 4). Using the loss tangent peak, a Tg of 233 °C is noted.
As an additional example, DMA data for the formulation using an EMI-24 catalyst are plotted in Figure 6, which shows a Tg of 239 °C. The catalysts from Table 5 show Tg’s ranging from 230 °C to 239 °C, see Table 6.
These high Tg’s are especially remarkable for two reasons: (1) they were obtained using a simple difunctional liquid epoxy resin based on bisphenol A, and (2) the amount of curing agent (BTDA) used was only half the stoichiometric amount.
The data also shows that the Tg-induced drop in modulus is merely one order of magnitude, far smaller than for thermoset epoxies in general, resulting in a relatively high modulus even in the rubbery phase.
Literature data indicate dielectric strengths of similar epoxy thermosets to be quite high even at temperatures above their Tg’s.11 The minimal specific heat changes (ΔCp) around Tg for these thermosets have already been noted.
These observations together project the degree of crosslinking in these formulations to be exceptionally high, considering they are based on a simple bisphenol A epoxy resin.
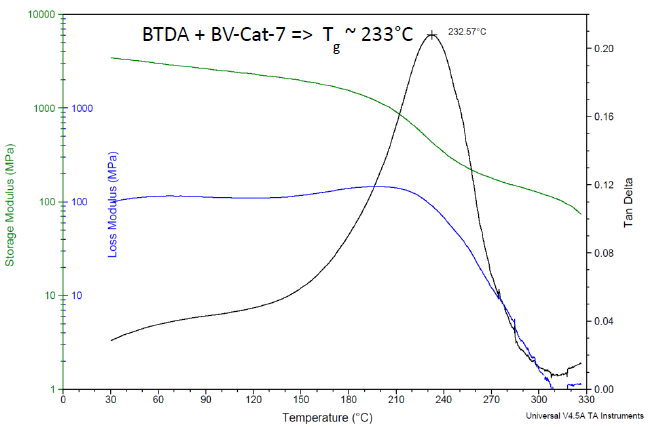
Figure 5. DMA results for Bisphenol A-based liquid epoxy resin, cured with BTDA at 0.5 A/E ratio, using BV-CAT-7 catalyst. Cured 24 h/200 °C. Image Credit: Jayhawk Fine Chemicals Corporation
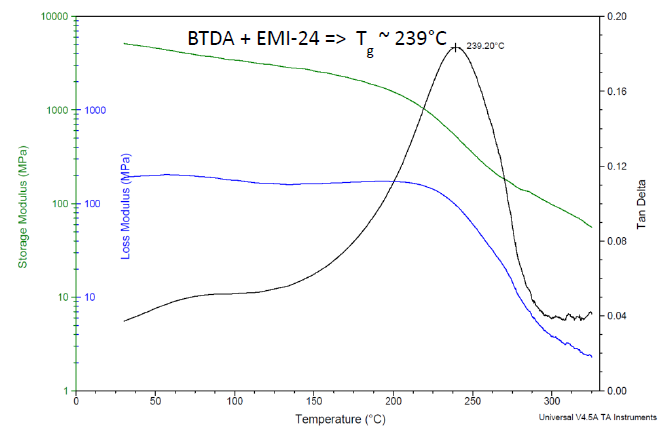
Figure 6. DMA results for Bisphenol A-based liquid epoxy resin, cured with BTDA at 0.5 A/E ratio, using 2-ethyl-4-methylimidazole catalyst. Cured 24 h/200 °C. Image Credit: Jayhawk Fine Chemicals Corporation
Table 6. Summary of Tg’s measured via DMA for BTDA-cured liquid epoxy resin and various catalysts. Each specimen was cured for 24 hours at 200 °C. Source: Jayhawk Fine Chemicals Corporation
Catalyst Type |
Catalyst Name |
DMA Tg (tanδ peak) |
Quaternary
ammonium salt |
BV-CAT 7 (Organic ammonium chlorides) |
233 °C |
Imidazole |
EMI-24 (2-ethyl 4-methyl imidazole) |
239 °C |
Imidazole |
AMI-2 (2-methyl imidazole) |
237 °C |
Imidazole |
2P4MZ (2-phenyl 4-methyl imidazole) |
236 °C |
Zinc Chelate |
Zinc acetyl acetonate |
230 °C |
Cure exotherm data on the formulations, determined via DSC, are plotted in Figure 7. The cure behavior is primarily similar for each catalyst used. Minimal reaction occurs until the temperature reaches 80 °C to 100 °C, depending on the catalyst.
BV-CAT7 shows the earliest onset of cure and may be appropriate where a somewhat lower cure temperature is desired. The catalyst 2-phenyl-4-methylimidazole shows the highest overall cure temperatures and may be appropriate where the curing process would benefit from some latency.
The catalyst 2-ethyl-4-methylimidazole shows the most rapid exotherm of the catalysts shown. While such cure behavior can be detrimental for thick composite parts due to the risk of localized hot spots, it may be perfect for rapid cure cycles in thinly applied thermosets e.g. in films or adhesives.
Using BTDA as a curative for epoxy resin enables exceptionally high Tgs while giving the formulator the freedom to choose an accelerator depending on the specifics of the application process.
Two Peculiarities in Thermosets with High Glass-Transition Temperatures
The data on BTDA-cured epoxies point to two peculiarities that would also seem to apply to broader high Tg thermosets. The notably smaller-than-expected change in thermoset properties at Tg has already been discussed.
A second unique characteristic of these formulations is the quick progression to a functional degree of cure but with the capability to substantially increase crosslinking over time.8 DSC cure thermograms in Figure 7 indicate that these cure exotherms are completed when the ramp temperature reaches around 160 °C-180 °C.
Considering that the reaction starts approximately when the ramp temperature reaches 60 °C to 80 °C, this indicates a total elapsed time of merely 10 minutes (at the thermal ramp rate of 10 °C/min).
This could lead us to believe that the cure is essentially complete, the cross-linked network has developed almost fully, and any further reaction would have only a marginal influence on the cured properties.
Tgs measured after fast cure cycles (as mimicked by these DSC curing ramps) routinely show lower values than the Tgs summarized in Table 6.
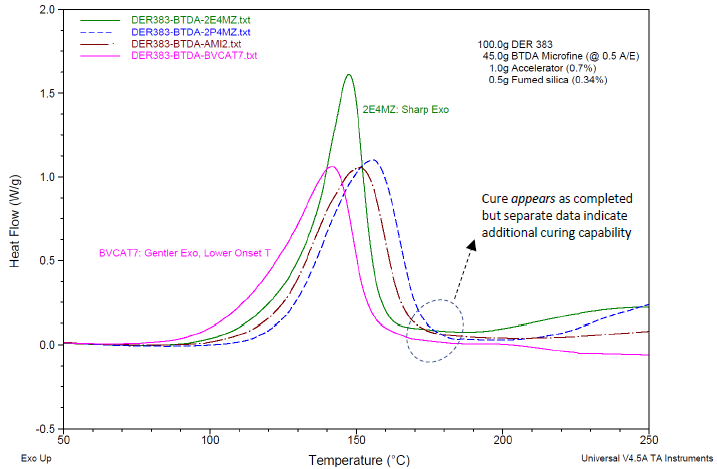
Figure 7. DSC cure exotherm data on formulations generated via a thermal curing ramp of 10 °C/minute. Formulations as in Table 4, with BTDA usage at A/E ratio of 0.5. At the end of the exotherm peaks, the cure appears complete; separate data point to additional curing capability, see Reference [8] and Figure 8. Image Credit: Jayhawk Fine Chemicals Corporation
Many glassy polymers encounter a common issue called premature vitrification during cure. When the ongoing curing elevates the instantaneous glass transition temperature (Tg) of the reacting resin to the curing temperature, the substance shifts from a liquid or gel state to a glassy phase.
This transition effectively hinders the curing reaction because, in the glassy state, the mobility of any remaining reactive components is significantly diminished.12 To achieve complete curing, it becomes necessary to implement a post-curing stage at a sufficiently high temperature to prevent further premature vitrification.
In the case of BTDA-cured epoxies, a similar halt in the curing reaction occurs, even when the instantaneous Tg of the reacting resin is below the curing temperature.
Figure 8 illustrates this phenomenon through DSC-Tg data for a basic BTDA-epoxy formulation. It is worth noting that this particular formulation, distinct from those presented in Table 4 (varying in terms of catalyst type, A/E ratio, etc.), indeed yielded discernible DSC-Tg values.
As indicated, the curing temperature was set at 200 °C, with different curing durations. This system's DSC cure exotherm profile (not displayed) resembled those in Figure 7.
Extending the curing times at 200 °C demonstrated a noteworthy advancement of Tg values. It is hypothesized that BTDA-cured epoxies achieve a sufficiently high degree of crosslinking during the curing process, which significantly restricts the mobility of polymer segments.
This dramatic reduction in mobility slows down the reaction of any remaining functional groups, even if the cure temperature exceeds the instantaneous Tg.
Subsequent curing can still proceed, albeit at much lengthier durations. Even in the rubbery phase, the resin system exhibits behavior akin to vitrification.
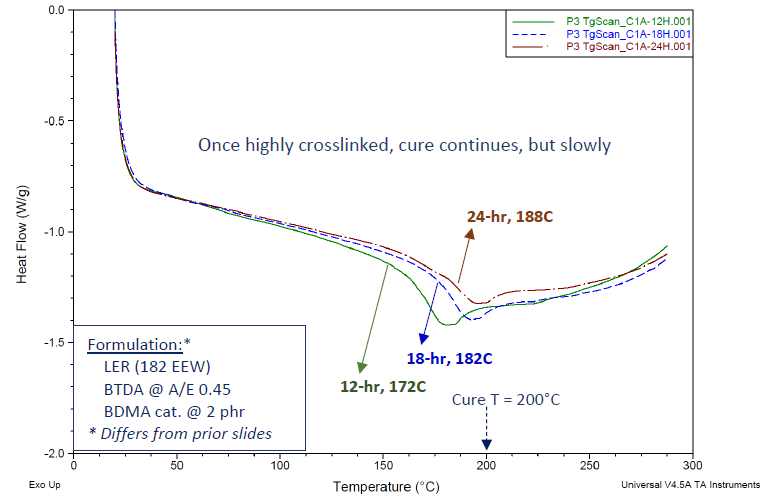
Figure 8. DSC thermograms showing Tg’s for BTDA-cured Bisphenol A epoxy resin, using BDMA catalyst. Cured 24 h/200 °C. Even with cure temperature above the instantaneous Tg, the measured Tg increases with increasing cure times. Image Credit: Jayhawk Fine Chemicals Corporation
Building upon these arguments, the authors propose that this phenomenon is not exclusive to BTDA or other dianhydride curatives but is likely applicable to highly cross-linked thermosetting materials in general.
In this context, the authors introduce the term pseudo-vitrification to describe this reaction stage in highly cross-linked systems, recognizing that it occurs even when the reacting resin has not yet reached a glassy state.
This concept holds practical significance. Firstly, these systems can attain notably high Tg values within relatively brief curing times, enabling swift progress toward a functional level of curing.
Specific applications may find satisfaction at this stage with proper formulation design to limit residual anhydride groups. Longer curing times can further enhance crosslink density, Tg, and related properties, such as dielectric strength, when necessary.
Given that these systems are generally preferred for high-temperature applications, some components may even enter partial service, allowing the heat from the service environment to complete the curing process to the desired level.
Using BTDA in Combination with Liquid Anhydrides
The preceding formulations employed BTDA powder as the sole curing agent for liquid epoxy resin, resulting in a paste-like consistency. These paste formulations find suitability in composite materials, molding applications, prepregs, etc., allowing them to be compounded and used within the same facility, preferably within a few hours.
For specific applications, there may be a requirement for more user-friendly formulations with lower viscosities than those attainable with the aforementioned formulations.
In other instances, there may be a need for stable two-component formulations, enabling the production, packaging, and subsequent utilization of products by applicators months later.
To address such needs, it is possible to combine BTDA powder with liquid mono-anhydrides like Nadic methyl anhydride (NMA) or methyl tetrahydrophthalic anhydride (MTHPA).
In this formulation approach, the liquid anhydride serves as a reactive diluent, facilitating more process-friendly formulations and leading to the development of final mixed resin systems.
Given that the modifier is a mono-anhydride, it also gives the formulator effective control over the ultimate crosslink density, allowing for the optimization of thermoset performance.
This approach appeals to a broader range of advanced applications, particularly considering the remarkably high glass transition temperatures (Tg) achievable with BTDA. However, some high-temperature applications may indeed benefit from slightly lower Tg values.
Such applications include two-component formulations for composites (such as prepregs, infusion, and filament winding), syntactic foams, adhesives, encapsulants, and molding compounds. Figure 9 illustrates a model syntactic foam formulation from a prior investigation.13
This formulation employed a straightforward epoxy resin with an equivalent weight (EEW) of 182. The curing agent was prepared in an approximate 1:1 weight ratio of BTDA and NMA (specifically, 45% BTDA and 55% NMA).
Glass micro-balloons were incorporated at a rate of 20% by weight to mimic a low-density syntactic foam. Following a four-hour cure at 220 °C, a commendable Tg of 199 °C was observed.
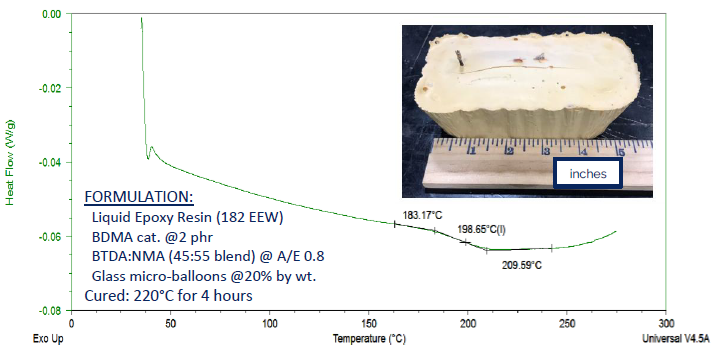
Figure 9. DSC thermogram showing a Tg of 199 °C for a model syntactic foam formulation, produced by using a blend of BTDA and NMA as curing agent 13. Image Credit: Jayhawk Fine Chemicals Corporation
To further delve into this concept, a study was undertaken to develop two-component epoxy formulations. This study employed the widely used standard bisphenol A resin with an EEW of 189. Curing agents were prepared using BTDA powder and MTHPA (a liquid monoanhydride) in various ratios, as outlined in Table 7.
The quantities of BV CAT-7 catalyst and fumed silica thickening agent were held constant for these curing agents. By dispersing BTDA powder and fumed silica in the liquid MTHPA and adding the liquid catalyst, user-friendly paste-like curing agents were produced.
These pastes also demonstrated stability for long-term storage and could be readily blended with the epoxy resin at the time of use. The mixing ratios with the epoxy resin were calculated based on the A/E ratios in Table 7.
The combined A/E ratios for these blended curing agents were determined by treating the BTDA portion at an A/E ratio of 0.5, and the MTHPA portion at an A/E ratio of 0.9.
Glass transition temperatures were determined from the tanδ peaks observed in DMA testing. As shown in Table 7, all formulations containing BTDA exhibited significant improvements in Tg compared to the 150 °C Tg obtained with the 0%-BTDA formulation.
Starting with 44% BTDA in the curative, Tg values of 180 °C or higher were consistently achieved, even when using the most standard liquid epoxy resin.
Table 7. Model formulations (in parts by weight) for two-component epoxy applications, with curing agents designed with BTDA and liquid MTHPA. DMA Tg’s reported after 24-hour cure at 200 °C. Source: Jayhawk Fine Chemicals Corporation
LER
(189 EEW) |
BTDA |
MTHPA |
BV-CAT-7
catalyst |
Fumed
Silica |
Tg, peak
tanδ (°C) |
%BTDA in
Curative |
Overall
A/E |
100 |
0 |
79 |
1 |
0.5 |
150 |
0% |
0.90 |
100 |
21 |
42 |
1 |
0.5 |
172 |
33% |
0.72 |
100 |
26 |
33 |
1 |
0.5 |
180 |
44% |
0.68 |
100 |
30 |
25 |
1 |
0.5 |
188 |
55% |
0.63 |
100 |
42 |
0 |
1 |
0.5 |
218 |
100% |
0.50 |
Notably, the Tg for the BTDA-only formulation in this dataset measured at 218 °C, which is slightly lower than the BTDA-only Tg of 233 °C previously observed in Table 6 for the same catalyst, BV CAT-7. Much of this variance can be attributed to the differences in the equivalent weight of the resins utilized in these two formulations.
The somewhat higher equivalent weight (EEW) of 189 in this study, as opposed to the previous use of 181, should marginally increase the average distance between crosslinks, reducing the Tg. Conversely, reverting to a resin EEW of 181 would raise the Tg for each formulation in this context.
Viscosity Measurements
A formulation (44% BTDA in curing agent) was selected for rheological assessment to quantify the ease of use of these hybrid curing agents. As indicated in Table 8, the viscosities for the curing agent (comprising anhydrides, catalyst, and fumed silica) and its mixture with the resin fall within user-friendly ranges.
Table 8. Viscosities for a selected formulation from Table 7 (44% BTDA in curative). Source: Jayhawk Fine Chemicals Corporation
Component |
Viscosity, 25 °C (mPa.s) |
Resin |
12,000* |
Curing Agent (44%BTDA in curative) |
1,993^ |
Mixed |
5,824^ |
* Nominal value as published by the supplier of the epoxy resin (EEW 189).
^ Measured on a TA Instruments AR 2000ex using a 2°/40 mm cone at a shear stress of 911 Pa
Conclusions and Summary
In summary, dianhydrides are high-performance curing agents for epoxy resins and serve as valuable components in the toolkit of epoxy formulators. As demonstrated by BTDA, they offer superior properties by facilitating extensive crosslinking in formulations employing even the simplest of epoxy resins, owing to their aromatic structure.
In particular, when focusing on glass transition temperatures (Tg), this study has observed Tg values as high as 239 °C when employing a standard epoxy resin based on bisphenol A. Even higher Tg values can be achieved by utilizing specialty resins such as novolacs and multifunctionals, among others.
The substantial degree of crosslinking achieved is evident from the relatively minor alterations in properties around the Tg (e.g., specific heat, modulus, etc.). Enhancements in other properties associated with crosslink densities, such as dielectric strength and chemical resistance, are both recognized and anticipated.
For broader applications, BTDA exhibits compatibility with liquid anhydrides, resulting in notably high Tg values, as exemplified with MTHPA or NMA, while simultaneously improving process-friendliness through reduced formulation viscosities.
This approach also enables the optimization of physical and other performance properties by effectively controlling the final crosslink density.
Acknowledgments
The authors extend their sincere gratitude to their suppliers for providing various samples. The epoxy resin was generously provided by Dr. Lingyun He of Olin Corporation.
The imidazole catalysts were supplied by Dr. Pritesh Patel, and the fumed silica was furnished by Mr. Joe Abrantes, both affiliated with Evonik Corporation. Liquid anhydride MTHPA and catalyst BV-CAT-7 were made available by Mr. Jason Tuerack and Mr. Phil Rhodes of Broadview Technologies.
References and Further Reading
- Barie and Franke, Ind. Eng. Chem., Vol. 8, No. 3, 72-76 (1969).
- EP0587757B1; Thermosetting powder coating compositions (1998).
- Barabanova et. al., Polymer 178, 121590 (2019).
- Kolar and Svitilova, Acta Geodyn. Geomater., Vol. 4, No. 3, 147, 85-92 (2007).
- Corcuera et. al., J. Appl. Polym. Sci. 64, 157–166 (1997).
- Bouillon, Pascault et. al., J. of Appl. Polym. Sci., Vol. 38, 2103-2113 (1989).
- Mishra & Campanella, Anhydride-cured epoxy composites: overview & recent advances, presented at the annual meeting of Thermoset Resin Formulators Association (TRFA) in Charleston, SC (2019).
- Mishra, Biller, Dimmit & Bilic, BTDA-cured epoxy powder coatings for high glass-transition temperatures, presented at the 2021 Virtual Annual Meeting of Thermoset Resin Formulators Association (2021).
- Greenberg & Kusy, Journal of Applied Polymer Science, Vol. 25,1785-1788 (1980).
- Ferry, Viscoelastic Properties of Polymers, 3rd Ed. (1980).
- Doone, Tait & Glaze, Functional Coatings: BTDA The high-performance curing agent, Surface Coatings International (7) 348-349 (1999).
- Gotro, J., Thermoset Characterization Part 7: Introduction to Vitrification, Polymer Innovation Blog, May 27, 2014.
- Pillay, S., et. al., Novel mono/dianhydride blends as curative systems for epoxy-based syntactic foams, presented at the annual meeting of Thermoset Resin Formulators Association (TRFA) in Raleigh, NC (2017).
BTDA® is a trademark of Jayhawk Fine Chemicals Corporation

This information has been sourced, reviewed and adapted from materials provided by Jayhawk Fine Chemicals Corporation.
For more information on this source, please visit Jayhawk Fine Chemicals Corporation.