This article discusses dry granulation (compaction) and wet granulation. Dry granulation involves the agglomeration of particles by applying a compressive force, while wet granulation relies on the binding effects of water or a binder solution.
Dry Granulation
In dry granulation, powders bind because of the application of mechanical stress. As particles are forced to be within closer proximity, entrained air is forced out, bulk density increases, and a stable compact is produced, which is then milled to create granules.
The response of powders to compressive force differs considerably, and not all powders are well-suited to dry granulation. Binders and fillers may be needed for certain materials to alter compressibility and enhance compaction behavior.
Post-processing, compacts may undergo elastic recovery, and the extent to which they experience this is dependent on the powder’s physical properties and the processing conditions.
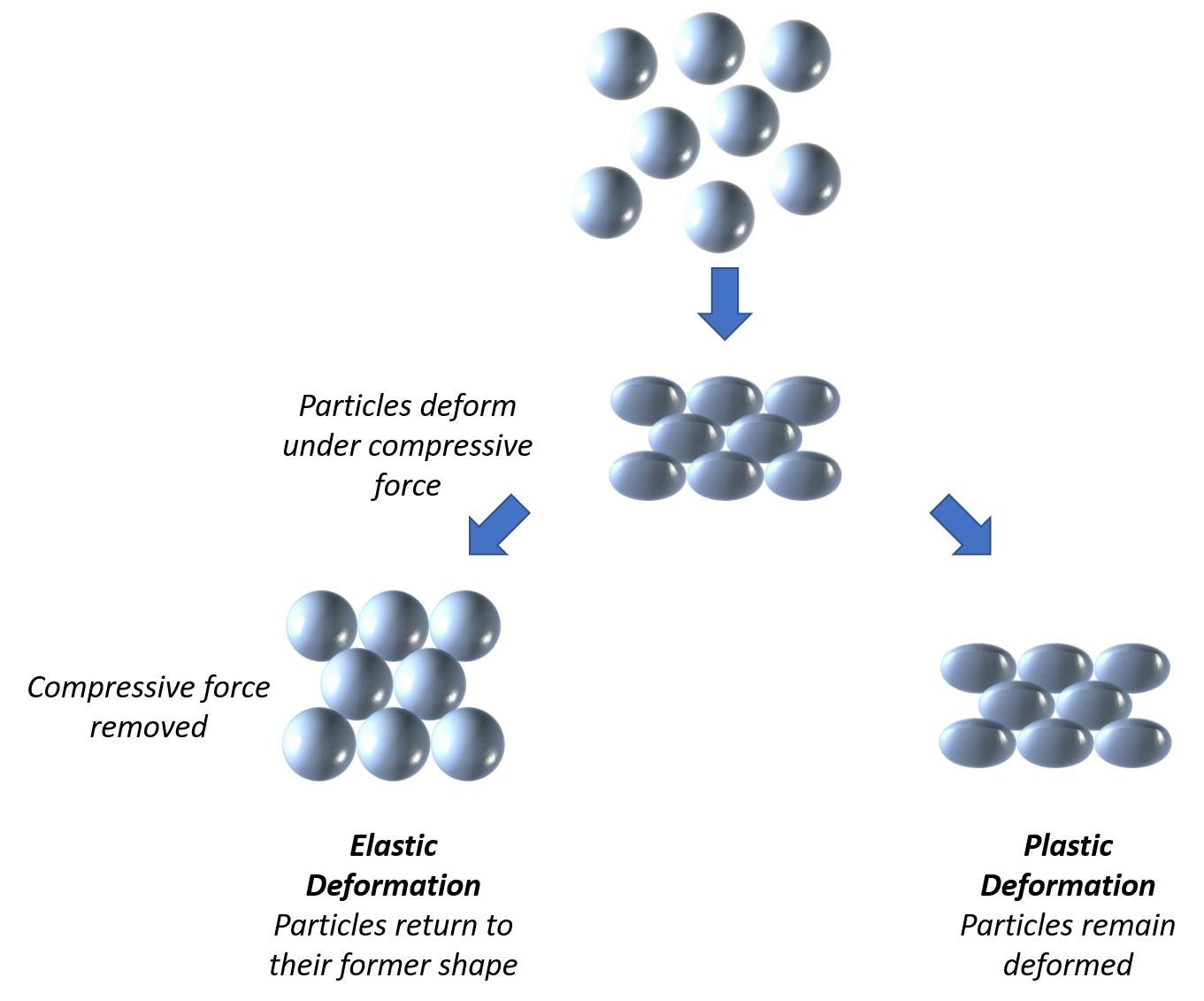
Dry compaction forces air out of a powder pushing particles together; elastic recovery post-processing depends on the properties of the powder and processing conditions. Image Credit: Micromeritics Instrument Corporation
Wet Granulation
In wet granulation, adding a binder solution or water triggers the particle-wetting process that underlies agglomeration. As liquid spreads across the surface of the particles, bridges start to be produced between one particle and another – this is the pendular stage of the wet massing process.
These links become more pronounced at higher liquid levels– referred to as the funicular stage – and the liquid phase can become continuous with the further addition of liquid. In this case, liquid also penetrates the particle pores via capillary action.
This latter capillary stage is related to excessive wetting or overgranulation, and if the addition of liquid continues to this point, any formed granules can return to a wet mass. The point at which the capillary stage begins is the typical ideal endpoint for wet granulation.1
Once a wet granulation process is stopped, the granules are dried. This can lead to disintegration but ideally causes solidification of the liquid bonds and the creation of stable granules. Similarly to dry granulation, milling may be necessary to satisfy a particle size specification.
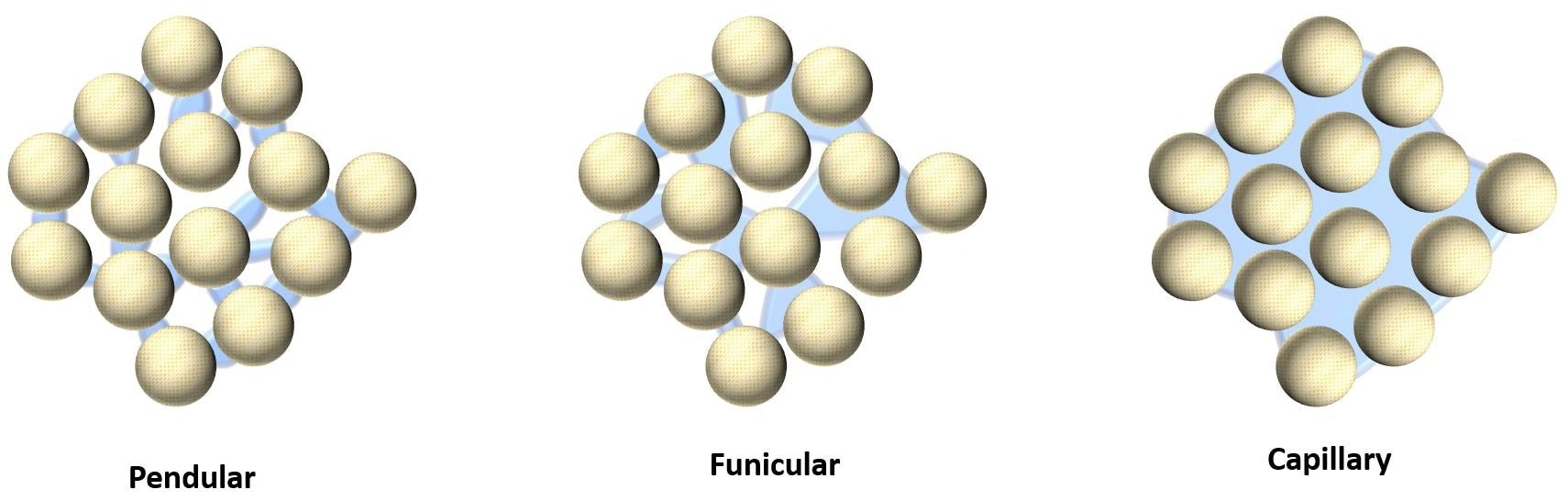
The formation of liquid bonds between particles underpins the process of agglomeration in wet granulation. Image Credit: Micromeritics Instrument Corporation
The Challenges of Granulation
These basic principles of wet and dry granulation are relatively easy to understand. However, there are challenges encountered with granulation processes regarding practical implementation.
- Endpoint detection: There is ongoing debate surrounding which parameter is most suitable to define the endpoint of a granulation process robustly, but the negative effect of poor endpoint detection is evident.
The product is not optimal, and throughput may be needlessly compromised because of a natural tendency to over-granulate in the face of poor control. Manufacturing costs are subsequently higher than necessary.
The goal is to granulate just enough to guarantee optimal granule quality. This relies on the identification and measurement of parameters that quantify granule quality in a manner relevant to the ensuing stages of the process and adequately sensitive to slight fluctuations close to the endpoint.
Such an approach enables more reliable and precise endpoint detection.
- Assessing the quality of an intermediate: The challenge of endpoint detection is intensified by the fact that the granules being created are frequently not the final product but an intermediate, such as in the production of pharmaceutical tablets.
Granulation of a tableting formulation generates a feed that will process at high speed through the press to yield tablets with the necessary critical quality attributes. The granules’ properties are not of interest, but they essentially influence the quality of the finished tablets and processing efficiency.
It is not necessary to process each batch of granules and evaluate the resultant tablets to quantify the quality of the granules if granule properties can be identified that are robustly associated with attributes such as content uniformity, stability, and hardness to allow the prediction of tablet quality.
Quantifying these properties enables an output specification for the granulation step to be defined based on the downstream success requirements and treat the granulation stage as an independent unit operation.
This is hugely advantageous for developing, designing, scaling up, monitoring, and controlling granulation.
- Scale-up: Batch granulation processes are common and are typically associated with scale-up challenges.
As equipment grows in size, geometry and process dynamics change. This makes scale-up non-linear and complicates the transfer of processing conditions that were previously established, e.g. the amount of binder that is added or the time required to reach an optimal endpoint.
For instance, a ten-fold scale-up in granulator volume does not equate to a ten-fold increase in granulation time. The granulation time may decrease if the larger scale equipment enables more efficient mixing.
As previously mentioned, having a robust granule specification to target that is independent of scale makes the transition from lab to pilot plant to commercial manufacturing considerably easier, especially when granulation is an intermediate step.
This issue can be particularly challenging in the pharmaceutical industry due to historical and highly regulated work practices. Many pharmaceutical processes operate in batch mode with several scale-up stages before commercialization.
A design space must be specified during the process development as part of the regulatory submission.
The design space is essentially the operating envelope within which the commercial plant will be maintained to allow the consistent manufacture of a product that satisfies quality targets.
Granulation processes are scale-dependent, making it complicated to predict optimal conditions for the manufacturing plant, which may lead to a delay in design space definition.
Manufacturing representative products for clinical trials without a defined design space is challenging. As a result, scale-up problems can be a significant challenge.
- Monitoring and control within a continuous processing environment: In many industries, the multiple advantages of continuous processing are appreciated and the adoption of continuous granulation processes is growing.
This is a particularly significant trend in the pharmaceutical industry, and this change introduces an extra demand concerning monitoring equipment. Present requirements are for relevant and timely process monitoring methods, especially when considering commercial-scale operations.
References and Further Reading
- B. De Schepper et al. ‘Relations between in-line dynamic torque measurement and off-line rheometry of high shear wet granulate’ Poster presented at PBO World Meeting 2014

This information has been sourced, reviewed and adapted from materials provided by Freeman Technology.
For more information on this source, please visit Freeman Technology.