With each passing day, the performance of aerospace systems is increasing significantly. This requires the use of advanced structural and functional materials that possess the required characteristics and can take the applied loads. New materials that are used to increase the performance of aerospace systems are usually developed using cutting-edge modern techniques that lead to changes in the structural topology of the materials.
The novel metallic materials used in aerospace components have a different microstructure than traditional metals that have been utilized for a long time. There is very little data available on the microstructure properties of modern aerospace metals, and much research is needed in this sector.
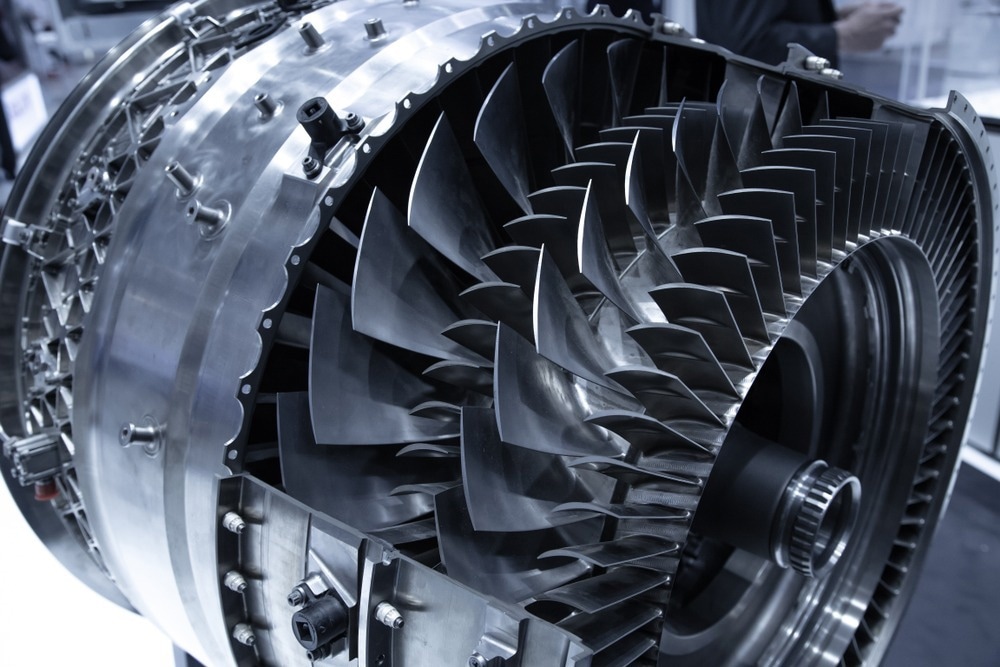
Image Credit: patruflo/Shutterstock.com
Why is the Study of Microstructural Attributes Important?
The microstructural properties of metals affect their behavior and response upon the application of thermal and aerodynamic loads during their use for aerospace components. Other significant tensile and physical properties, such as durability, brittleness, and electrical conductivity, are also affected by the microstructure.
However, verified data about the microstructural properties of metals, especially the effect of processing on microstructural attributes of metals, is limited. In the aviation sector, where components are often specified based on worst-case performance assumptions, having more knowledge about the microstructure of metals is essential. This becomes even more critical as engineers aim to promote sustainable aerospace operational methods through weight reductions, new manufacturing processes, and the adoption of new materials.
The introduction of metal additive manufacturing (AM) in the aerospace sector further emphasizes the need for a deeper understanding of metal microstructures. AM processes, with their rapid heating and cooling timescales, present unique challenges, and there is limited information about the effects of AM on metals compared to traditional manufacturing methods. This knowledge gap makes it challenging to accurately estimate the safety and durability of components produced through 3D printing in the aerospace industry.
What Techniques are Employed for the Study of Microstructural Attributes?
Experts are utilizing different established techniques for understanding the microstructural attributes of different metals employed in various industries. The most famous technique for microstructural characterization of metals is Scanning electron microscopy (SEM). The SEM imaging technique for microstructure characterization mainly involves two steps: data collection and image analysis.
Additionally, the study of the topological structure of metals, the different phase compositions of metals such as titanium, etc., and the crystallographic structure is usually done by transmission electron microscopy (TEM) and X-ray diffraction (XRD). These techniques offer insights into the detailed features of the material at the microscale.
In addition to microstructural characterization, mechanical and tensile characterization methods play a crucial role. Hardness testing, wear, and friction testing, as well as scratch and indentation testing, are utilized extensively to evaluate the mechanical behavior and performance of engineered surfaces.
Study of Microstructural Properties of 21-6-9 Stainless Steel for Aerospace Applications
Additive manufacturing (AM) has become a transformative process in manufacturing, especially in the aerospace sector. It provides a direct route from design to finished products, bypassing the lengthy traditional manufacturing procedures.
A metal that is extensively used for aerospace components is a 21-6-9 stainless steel alloy. The alloy contains 21% chromium, 6% nickel, and 9% manganese in its composition.
An article has been published in the Journal of Materials Research and Technology that involves the investigation of microstructural properties of nitrogen-strengthened stainless steel alloy 21-6-9.
Eight samples were prepared for tensile testing at both room temperature and cryogenic temperature (77 K), following ISO 6892-1 standards. The yield strengths (YS) at room temperature, ranging from 580 to 650 MPa, were significantly higher than those reported for traditionally manufactured 21-6-9 (around 300 MPa).
At cryogenic temperature, both yield strength and ultimate tensile strength increased significantly (80%) compared to room temperature, but elongation decreased severely (90%).
Heat treatments at 750°C for 1 hour and 24 hours did not significantly affect the mechanical properties, and no noticeable increase in grain size was observed. The microstructure of the laser powder bed fusion (L-PBF)-manufactured 21-6-9 exhibited sub-cellular structures typical of austenitic stainless steels after L-PBF production.
The microstructural examination of the alloy in the study has highlighted its importance as a structural component for aerospace applications. The alloy demonstrated remarkable elongation at room temperature, nearly reaching 40%. Additionally, it exhibited a notable amount of strain hardening at room temperature compared to cryogenic temperature.
Microstructural Study of Titanium Grade 5 Metallic Parts
Components made from titanium have high specific strength and corrosion resistance, making them widely used in industries such as aircraft, power and chemical machine building, sporting equipment, and medical device manufacturing.
Currently, the majority of titanium components are produced through machining. However, other famous manufacturing methods, such as Additive Manufacturing (AM) are being used to fabricate aerospace parts.
The International Journal of Advanced Manufacturing Technology has a recent article in which the microstructural properties of parts made from Ti6Al4V were studied. Three different techniques, forging, machining, and additive manufacturing (AM—were employed to manufacture aerospace parts, and their microstructural characteristics were investigated.
Additionally, two distinct additive manufacturing processes, namely, selective laser melting (L-PBF) and electron beam melting (E-PBF), were considered by the researchers.
Geometrical features, such as thin walls, influence part distortion in additively produced parts. The T component manufactured by L-PBF exhibited higher distortion in the stringer, with a maximum value of about 1.3 mm.
Different microstructures were observed based on the manufacturing route. While machining minimally affected the core's microstructure, forging allowed the determination of the final microstructure based on the chosen process temperature.
Anisotropy was noted in all case studies, influenced by factors such as preferential grain growth direction in AM technologies, strain distribution in forging, and feedstock material anisotropy in machined parts.
The different microstructures directly affect the micro-mechanical properties of the parts. Larger micro-hardness values were found for the machined part. The research is useful as it links the microstructural properties of parts with the manufacturing routes.
Microstructure design is key in targeting the properties of the desired material. Microstructural properties analysis is used extensively in failure investigations and supplements material performance tests. It is, therefore, essential to understand the relationship between properties and microstructure and how they are driven via a specific process.
More from AZoM: Mechanical Properties of Steel in High-Stress Environments
References and Further Reading
Sampson, B., (2020). Metals Testing for Aerospace Under the Microscope. [Online]
Available at: https://www.aerospacetestinginternational.com/features/metals-testing-for-aerospace-under-the-microscope.html
Riley (2016). Microstructural Analysis. [Online]
Available at: https://www.nasa.gov/centers-and-facilities/white-sands/microstructural-analysis/
Mishra, P. et. al. (2023). Microstructural characterization and mechanical properties of additively manufactured 21-6-9 stainless steel for aerospace applications. Journal of Materials Research and Technology. 25. 1483 - 1494. Available at: https://doi.org/10.1016/j.jmrt.2023.06.047
Campanella, D. et al. (2022). Mechanical and microstructural characterization of titanium gr.5 parts produced by different manufacturing routes. Int J Adv Manuf Technol 122, 741–759. Available at: https://doi.org/10.1007/s00170-022-09876-
Disclaimer: The views expressed here are those of the author expressed in their private capacity and do not necessarily represent the views of AZoM.com Limited T/A AZoNetwork the owner and operator of this website. This disclaimer forms part of the Terms and conditions of use of this website.