Nearly 13 years after the incident at the Fukushima power plant, the reactor and nearby area are still generating a large amount of heat, requiring 400 cubic meters of water daily. This water must be decontaminated to remove radioactivity and radioactive compounds, which increases recurring costs and leakage hazards. In fact, leakage of caesium-137 has been reported on a few occasions.
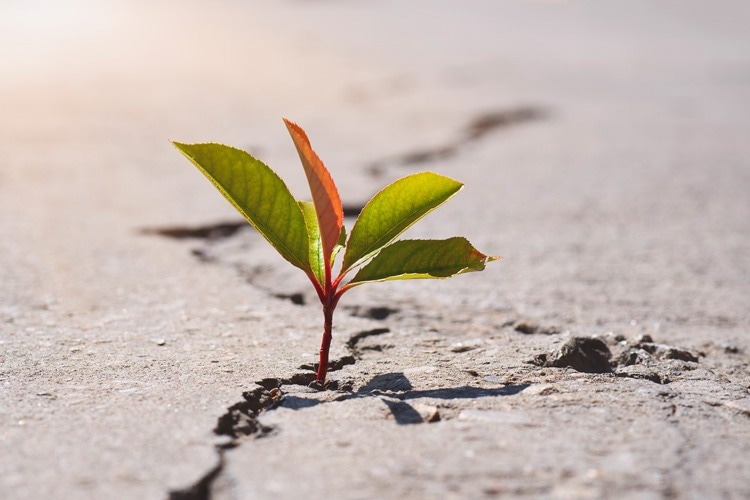
Image Credit: Thermo Fisher Scientific
To fully decommission the plant and protect the surrounding environment, workers need to contain and stock the highly radioactive compounds contained in the core. However, the core is now surrounded by a glass-ceramic mixture of uranium oxide pellets, zirconium cladding, and other materials like steel and concrete that melted together during the incident. This mixture is known as the molten core-concrete interaction or MCCI.
Due to the deadly level of radiation in the area, humans cannot directly work to break through the MCCI. The viable alternative is to use robots to dig through the material. But to ensure that they succeed in their mission, the robots need to be strong enough to pierce the MCCI.
To find out just how much force would be needed, a group of researchers led by Charilaos Paraskevoulakos analyzed material from the MCCI.
Breaking a Radioactive Sample
Analyzing radioactive material comes with a number of challenges, chief among which is the safety of the people investigating the material. Sourcing real MCCI from the site was not an option, so the researchers collaborated with Ding et al. to obtain a custom-made replica of the materials from Fukushima.
As the real material composition varies per area and assessing the real composition was too complex, the composition of the material was approximated. Dangerous materials were also replaced by less hazardous ones.
As the simulated material was still radioactive, the sample dimensions also had to be contained. Instead of the traditional compression test, the researchers had to rely on Hertzian indentation to apply mechanical stress on the sample.
The intention was to measure how brittle the material was by monitoring the formation of pores and cracks, the global volume variation, and the local deformation in the analyzed volume. The sample was, therefore, cyclically compressed and imaged with synchrotron radiation (XCT). The results of the scan were then imaged with software designed for visualization and measurement.
This allowed the researchers to extract the fraction of the sample represented by the matrix and by the inclusions, as well as monitor the porosity and observe the formation of new pores or cracks.
The Material Response to Stress
The sample was compressed with increasing forces of 20, 70, 130, and 160 Newtons. The last compression resulted in sample failure, as shown in the graph below.
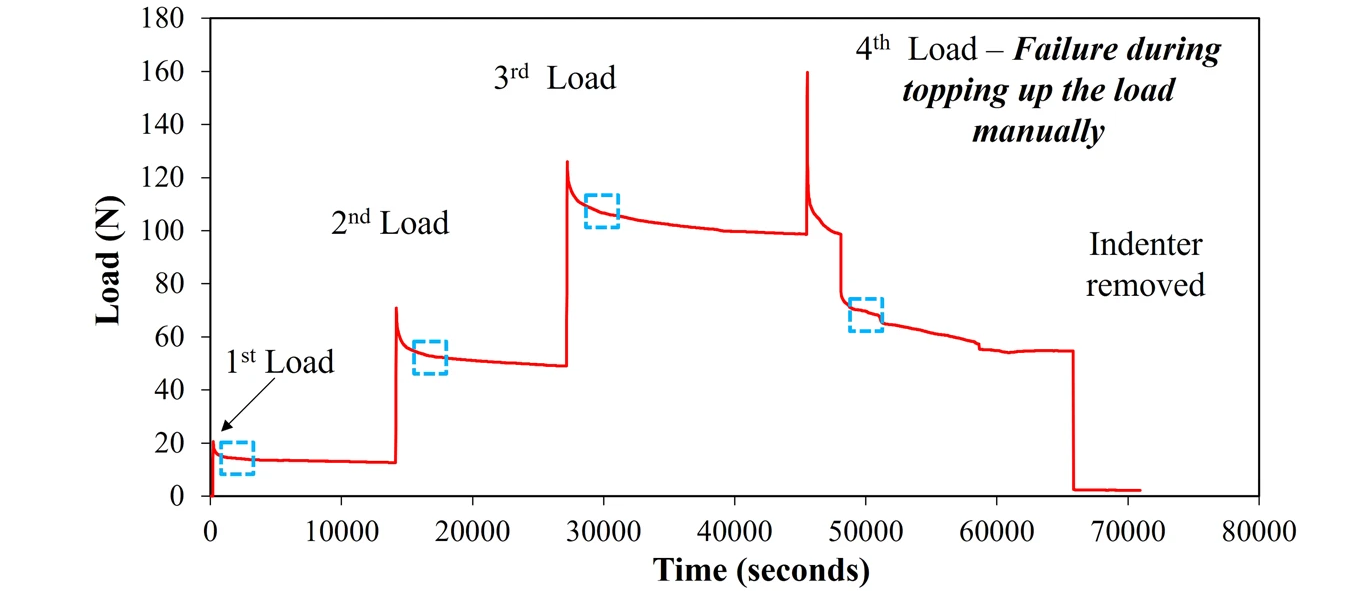
Graph of the stress tests showing how the material responded to each load and ultimately failed. Image Credit: https://doi.org/10.1038/s41529-022-00264-y
The compressions were alternated with imaging sessions, and the results were segmented to highlight the areas containing different materials as well as the pores.
No micro cracks were observed in the material, possibly because the resolution was not sufficiently high. Also, no measurable variation was observed in the porous phase, which remained practically constant at 2 % of the total volume. The researchers, therefore, decided to take their analysis one step further by focusing on the local deformations inside the sample.

a Identification of pores, uranium and iron phases, b segmentation of the several phases in a 2D slice, and c 3D volumes of the segmented uranium, iron and pore phases. Image Credit: https://doi.org/10.1038/s41529-022-00264-y
A Way to Study Material Deformation
Digital volume correlation (DVC) — a popular technique available in some image processing software — focuses on comparing a sample before and after physical stress. This makes it possible to identify the pixels (or groups of pixels) that have changed their mutual position in relation to the rest of the sample.
Due to the sudden sample failure and the severity of the cracking, it was not possible to run the DVC analysis with the sample after the fourth compression. However, the researchers published the results of the scans during the relaxation phase after the compressions of 20 and 70 Newtons and between the compressions of 20 and 130 Newtons.
The investigation showed that the deformation was not homogeneous within the sample and detected discontinuities within the deformation pattern. This hints toward the theory that micro cracks have indeed formed within the material, but the XCT resolution was not sufficient to resolve them.

Axial displacements in the simulated MCCI material measured by DVC as weight was added during the stress test. Image Credit: https://doi.org/10.1038/s41529-022-00264-y
A Cleaner Planet
The researchers conclude the paper with an additional observation on the sample composition: While this is rather representative of the materials from the incident site, a large diversity of mixing ratios is to be expected, dictated by the higher concentration of certain compounds locally and by the lack of mixing.
This, however, does not disqualify the importance of the results they obtained — they are valuable insights into what the robots will encounter on site and how they need to be equipped to complete their mission of extracting the radioactive material.
Thermo Scientific Avizo Software helped scientists and engineers visualize and measure features of interest within their samples. The researchers could extract quantitative information on the presence of pores and the ratio of materials mixed in the MCCI by segmenting the volume based on grayscale levels.
The digital volume correlation (DVC) module of Avizo Software ultimately provided them with key information to decode the material behavior and armed them with the necessary information to continue their investigation and clean our planet.
Learn more: Introduction to Avizo Software for composite materials characterization webinar
References and Further Reading
Paraskevoulakos, C., Forna-Kreutzer, J.P., Hallam, K.R. et al. Investigating the mechanical behaviour of Fukushima MCCI using synchrotron Xray tomography and digital volume correlation. npj Mater Degrad 6, 55 (2022). https://doi.org/10.1038/s41529-022-00264-y
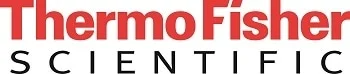
This information has been sourced, reviewed and adapted from materials provided by Thermo Fisher Scientific - Software.
For more information on this source, please visit Thermo Fisher Scientific - Software.