By Taha KhanReviewed by Lexie CornerMay 30 2024
The aerospace industry requires materials that can withstand extreme conditions. Ceramics are essential in this context due to their unique properties, including exceptional thermal resistance, lightweight nature, and durability.
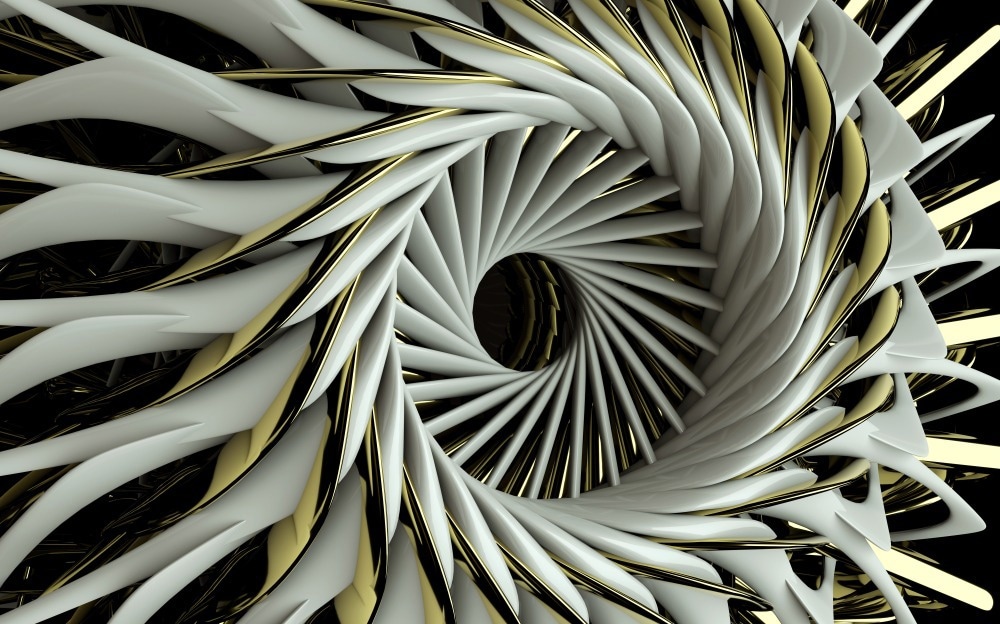
Image Credit: Philipp Tur/Shutterstock.com
Properties of Ceramics Crucial for Aerospace
Ceramic materials can maintain structural integrity at extremely high temperatures. This makes them ideal for aerospace applications, such as jet engine parts that endure intense heat during operation.1,2
Ceramics are also highly durable, with excellent abrasion and corrosion resistance, ensuring long-lasting performance for components exposed to friction and corrosive environments. They are also lighter than metals, reducing aircraft and spacecraft weight. This translates into increased fuel efficiency, longer flights, and larger payloads.1,2
Applications of Ceramics in Aerospace
Ceramic materials are used in various areas of the aerospace industry. Modern aircraft engines heavily rely on ceramics; turbine blades and vanes, which experience extreme heat and pressure, are commonly made from advanced ceramics. These materials are more thermally resistant than traditional metal alloys, allowing engines to run hotter and more efficiently, improving fuel consumption and reducing emissions.2,3
Ceramics are also used in heat-resistant tiles, which shield spacecraft from extreme heat during re-entry into Earth's atmosphere. These tiles, often made from silica or carbon-fiber-reinforced ceramics, can absorb and dissipate intense heat generated by air friction.1,4
Piezoelectric ceramics convert mechanical pressure into electrical signals and are used in aircraft pressure sensors. Advanced ceramics are also employed in constructing high-temperature sensors for rocket engine exhaust monitoring.5
OCMCs used in Rocket Engines
Arecent’s study explored the application of oxide–oxide ceramic matrix composites (OCMCs) in rocket engines, specifically focusing on rocket thrust chambers. Various tests, including strength, leakage, and hot gas tests, evaluated the material's potential and limitations.
The study highlighted the successful development of an impermeable coating using a recrystallized glass of a Y-Al-Si-O compound, which did not compromise the OCMC's damage-tolerant behavior. Despite difficulties in manufacturing complex structures, simple OCMC geometries showed promising results in hot firings, suggesting potential use as lightweight components in rocket engines.6
Challenges and Recent Advances in Implementing Ceramics
Utilizing ceramics in aerospace applications presents challenges. The manufacturing process for complex ceramic components requires specialized processing techniques that can be intricate and expensive.
These methods often involve high temperatures and pressures, leading to difficulties in achieving precise shapes and consistent material properties. They also require expensive raw materials, increasing production costs compared to traditional metallic components.
Moreover, although ceramics used in aerospace applications are very strong, they are brittle and require careful handling and design considerations.7,8
Scientists and researchers are addressing these challenges by experimenting with new ceramic-based materials and utilizing new technologies. Additive manufacturing techniques like 3D printing allow for greater precision in creating complex components.
Researchers are also exploring ceramic matrix composites (CMCs) that combine the high-temperature resistance of ceramics with the toughness and ductility of other materials like fibers or polymers, improving fracture resistance and addressing the inherent brittleness of ceramics.7,9,10
Advanced Material Offering Thermal Protection for High-speed Aerospace Applications
In a 2020 study, researchers developed a novel ceramic material designed for aerospace applications. This material addresses the challenge of achieving high electrical conductivity for electromagnetic interference (EMI) shielding while maintaining low thermal conductivity for thermal protection.
The innovative composite system features a multilayer structure composed of polymer-derived silicon carbon nitride (SiCN) ceramic reinforced with yttria-stabilized zirconia (YSZ) fibers.11
The YSZ-reinforced SiCN layers provide thermal insulation, while the incorporation of carbon nanotubes within the ceramic enhances EMI shielding capabilities. Testing demonstrated that this composite system offers approximately 22.5 % lower thermal conductance than traditional carbon fiber-reinforced polymer composites and can withstand high temperatures.
It also shows significant potential in both reflection and absorption-dominant EMI shielding, making it a promising material for high-speed aerospace applications.11
Future Outlook and Technological Developments
As research in advanced materials progresses, we expect to see novel ceramic materials with higher thermal resistance, lower weight, and improved fracture toughness, enabling even more efficient and powerful engines and robust spacecraft.
Nanotechnology can also play an important role by developing ceramics with tailored properties at the nano-level, offering even higher strength-to-weight ratios and improved resistance to extreme environments.8
Hybrid materials that combine the unique properties of ceramics with complementary functionalities of other materials can further advance the aerospace industry.
More from AZoM: Zinc-Based Batteries: Recent Advances, Challenges, and Future Directions
References and Further Reading
- Bhasha, B., Gautam, S., Malik, P., Jain, P. (2019). Ceramic composites for aerospace applications. Diffusion Foundations. doi.org/10.4028/www.scientific.net/DF.23.31
- Dhanasekar, S., et al. (2022). A comprehensive study of ceramic matrix composites for space applications. Advances in Materials Science and Engineering. doi.org/10.1155/2022/6160591
- Fox, A., et al .(2024). Design and Cooling Performance of Additively Manufactured Ceramic Turbine Vanes. Journal of Turbomachinery. doi.org/10.1115/1.4064226
- Pradeep, A., Abhilash, S., Sunish, K. (2018). Performance Analysis of Ceramic Composite Thermal Protection System Tiles. Exergy for A Better Environment and Improved Sustainability 2: Applications. doi.org/10.1007/978-3-319-62575-1_40
- Capsal, J. F., David, C., Dantras, E., Lacabanne, C. (2012). Piezoelectric sensing coating for real time impact detection and location on aircraft structures. Smart materials and structures. doi.org/10.1088/0964-1726/21/5/055021
- Bach, C., Wehner, F., Sieder-Katzmann, J. (2022). Investigations on an all-oxide ceramic composites based on Al2O3 fibres and alumina–zirconia matrix for application in liquid rocket engines. Aerospace. doi.org/10.3390/aerospace9110684
- Karadimas, G., Salonitis, K. (2023). Ceramic matrix composites for aero engine applications—a review. Applied Sciences. doi.org/10.3390/app13053017
- Rathod, VT., Kumar, JS., Jain, A. (2017). Polymer and ceramic nanocomposites for aerospace applications. Applied Nanoscience. doi.org/10.1007/s13204-017-0592-9
- Katz-Demyanetz, A., Popov Jr, VV., Kovalevsky, A., Safranchik, D., Koptioug, A. (2019). Powder-bed additive manufacturing for aerospace application: Techniques, metallic and metal/ceramic composite materials and trends. Manufacturing review. doi.org/10.1051/mfreview/2019003
- The American Ceramic Society. Ceramics and glass in the aerospace industry. [Online] The American Ceramic Society. Available at: https://ceramics.org/about/what-are-engineered-ceramics-and-glass/ceramics-and-glass-in-the-aerospace-industry/
- Jia, Y., Ajayi, TD., Wahls, BH., Ramakrishnan, KR., Ekkad, S., Xu, C. (2020). Multifunctional ceramic composite system for simultaneous thermal protection and electromagnetic interference shielding for carbon fiber-reinforced polymer composites. ACS Applied Materials & Interfaces. doi.org/10.1021/acsami.0c17361
Disclaimer: The views expressed here are those of the author expressed in their private capacity and do not necessarily represent the views of AZoM.com Limited T/A AZoNetwork the owner and operator of this website. This disclaimer forms part of the Terms and conditions of use of this website.