The production of top-quality lightweight alloy wheels as used in the Formula 1 stalls or of alloy rims for conventional passenger cars calls for the strictest requirements with respect to exactness and compliance with the relevant standards. The ZHU250 hardness tester from Zwick meets these demands - exactly.
The ZHU250 universal hardness tester is geared for standards-compliant hardness testing according to Vickers, Brinell, and Rockwell, plus ball-pressure hardness testing to max. 250 kg and is characterized by its intuitive operating concept. The test programs are quick and easy to configure, being largely self-explanatory for both the test bench engineer and the user at the machine. All the settings and parameters are provided in the several languages with a representation that is simple to understand.
Due to the manifold test jobs to be performed, the customer placed highest requirements on the versatility of the testing machine. The Zwick hardness tester was well able to meet these demands primarily due to its large working space (300 x 250 mm). Particularly worth mentioning is that the indentations are measured optically parallaxis- and error-free using a measurement line concept integrated into the focusing screen. This approach ensures high reproducibility of the test results.
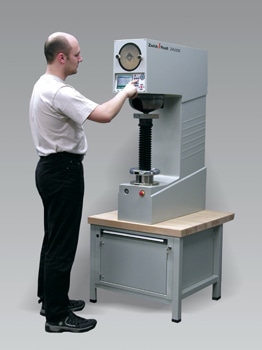
|
Figure 1. The ZHU250 hardness tester from Zwick.
|
With the Zwick ZHU250, for the first time ever a hardness testing machine utilizing the current contents of the DIN EN ISO 18265 standard to enable the revaluation of hardness values has come out on the market. Now, in addition to the conventional tables thus far employed for steels and low-alloy steels and steel castings, the user is provided with standards-compliant revaluation options for materials made from aluminum and copper.
|
|
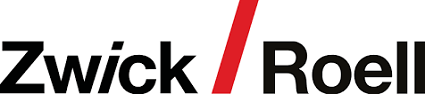
This information has been sourced, reviewed and adapted from materials provided by ZwickRoell GmbH Co. KG
For more information on this source, please visit ZwickRoell GmbH Co. KG.