Contamination levels of liquid fuel entering the combustor of a gas turbine must be low to avoid high temperature corrosion and fuel system fouling. Accordingly, each of the major industrial gas turbine manufacturers has strict contamination limits which must be met in order to comply with the warranty of the turbine. The responsibility to assure compliance lies with the owner of the power plant and can only be guaranteed with on-site fuel analysis for contaminants and ash-forming metals.
This paper discusses the various fuel analysis techniques available to the gas turbine user. It will review each technique’s ability to meet the need for fast and precise on-site analytical data. It will be demonstrated that the rotating disc electrode (RDE) atomic emission technique is the preferred analytical method for on-site fuel analysis. Actual field experience will be used to illustrate and discuss compromises that may be necessary to meet the objectives of the gas turbine user, fuel treatment supplier and turbine manufacturer.
Introduction
Gas turbine fuel analysis has become an important component of a power plant. Operating experience has shown that some of the ash-forming substances that may be present in a fuel can lead to corrosion and deposit problems. Ash-forming materials may be in a fuel as oil-soluble organometallic compounds, as water soluble salts or as solid foreign contamination. Their presence and concentration varies with the geographical source of a crude oil and they are concentrated in the residual fractions during the refining process. Although the remaining distillates are typically contaminant free, ash-forming materials may be introduced later in the form of salt-bearing water or by mixture with other petroleum products during transportation or storage. Most crudes require desalting, especially if water transportation was used.
Pre-conditioning of the fuel before it reaches the gas turbine has become a prerequisite for installations that use heavy petroleum fuel, and often also for sites that use light distillate fuels. Fuel analysis is an integral part of a fuel quality management program. It is used first to determine the extent of the required treatment, and later, the effectiveness of the treatment. It starts with the delivery of the fuel, continues throughout fuel handling and ends only as the fuel is injected into the turbine. Figure 1 is a typical example of a residual fuel storage, treatment and handling system.
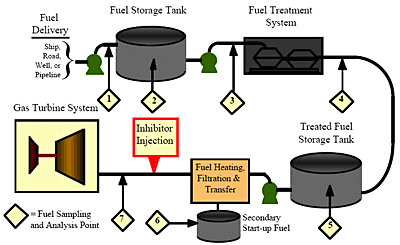
Figure 1. Typical residual fuel storage, treatment and handling system
Fuel contamination specifications vary among the different gas turbine manufacturers. However, without exception, each requires that contaminants must be as low as possible and typically below one part per million by weight. In most power generation installations, it is the owner who has the responsibility of verifying fuel cleanliness in compliance with the warranty specifications of the turbine manufacturer. This leads to an on-site analytical instrument performance requirement of well below one part per million (ppm) for six or more elements. It presents a particular challenge to the turbine user as most installations are at remote sites which often lack resources and facilities for precise onsite fuel analysis.
Analytical Techniques For Fuel Analysis
Several techniques can be applied for fuel analysis. They vary in complexity, analytical times and precision. They include flame and graphite furnace atomic absorption spectrometers (FL/AAS & GF/AAS), rotating disc electrode atomic emission spectrometers (RDE/AES) and inductively coupled plasma atomic emission spectrometers (ICP/AES). Each has its own advantages and disadvantages but at a minimum, they must be capable of detecting and quantifying contaminants and ash forming metals in the fuel including sodium, potassium, vanadium, lead, calcium, magnesium and sometimes also iron, silicon, nickel, aluminum, chromium, zinc and copper.
Atomic Absorption Spectroscopy (AAS)
In the flame atomic absorption spectroscopy (FL/AAS) technique a small amount of fuel sample is fed into a controlled flame normally fuelled by an acetylene-oxygen or nitrous oxide mixture. Heavy fuels must be diluted prior to analysis, but light distillates can often be analyzed without dilution. The flame vaporizes the sample and causes the atoms to be in an elevated energy state. A special hollow cathode lamp emits a high intensity light beam corresponding to the exact wavelength that will be absorbed by the element of interest when that element is heated in the flame. Since the lamp emits light at the specific wavelength of the element to be analyzed, a separate lamp is required for each element. A monochromator is tuned to the desired wavelength and the absorbed light can be related to the concentration of the element present in the oil [Sieber and Salmon, 1994]. A microprocessor or computer then separates the signals and converts them into concentrations.
The FL/AAS technique has been in use for over 35 years in thousands of instruments for elemental analysis, but is applied most often for aqueous solutions, rather than fuel samples. It is a single element at a time technique that is good for quantitative, not qualitative, analysis. Its main disadvantages are that it is relatively slow, involves sample preparation for most fuels, and requires a different light source for each element analyzed. Detection limits for sodium and potassium are below 0.1 ppm in undiluted fuel samples, but they degrade with heavy fuel samples in direct proportion to the dilution factor. Improvements in the past 10 years have been in alternate means to atomize the sample [Routh 1993].
Another AAS technique which can be applied to fuel analysis is graphite furnace atomic absorption spectroscopy (GF/AAS). Its main advantage is high sensitivity and small sample volume requirement [Nadkarni, 1991]. The equipment used is similar to the flame atomic absorption method except that the flame has been replaced with a small high temperature furnace typically configured as either a small cylindrical carbon tube or cup to hold the sample.
In operation, a few microliters of sample are first evaporated at low temperature, the current through the furnace is increased to a few hundred amperes, the temperature soars to approximately 2,500°C, and the sample is atomized, monochromatic light is directed through the vapor and the analysis proceeds in the same manner as in standard FL/AAS.
The GF/AAS technique offers by far the best detection limits for the corrosive contaminants in fuels. It is, however, a laboratory instrument that requires an ultra-clean environment, a relatively high level of expertise for operation and has the greatest risk of contaminant interference. Analysis times can also take several hours or more per sample.
Atomic Emission Spectroscopy (AES)
Atomic emission spectrometers employed in fuel analysis are either of the rotating disc electrode (RDE) type or of the inductively coupled plasma (ICP) type. In the RDE/AES technique, a rotating graphite disc electrode brings a continuous sample into a gap between the disc and a stationary graphite rod electrode. A high voltage arc is then struck between the disc and rod electrodes causing the individual atoms in the sample to give off light or radiant energy.
The ICP/AES excitation technique employs an electrode-free plasma created by a flow of inert gas (argon). The gas passes continuously through the plasma torch which is located inside a R.F. coil connected to a radio frequency alternating current generator. The fuel sample is aspirated through the center of the torch and into the plasma where the atoms present are totally disassociated and excited to give off radiant energy.
In RDE and ICP systems, a lens or fiber optic is then used to gather and focus the emitted radiant energy from the excitation source on an optical system which disperses the light into the various spectral lines associated with the elements present.
Photomultiplier tubes are used to detect and convert radiant energy into electrical currents which give a measure of the concentration of each metal present in the sample. This result is displayed on a video screen, sent to a printer or stored on a hard disk.
For fuel analysis, the RDE technique continues to be preferred for its simplicity of operation and reliability. It is fast and the analysis of all elements of interest in a fuel sample takes less than one minute. It is flexible and has the ability to analyze samples ranging from light distillate fuels to crude oils and heavy residuals without dilution. RDE spectrometers are very robust, have few moving parts and requires little maintenance.
While the ICP technique was developed for water analysis, modifications have been made for other applications including fuel analysis. The main advantage is its performance; accuracy, precision and detection limits are excellent. It offers fast analysis speed, multielement capability, and good detection limits.
Unfortunately, detection limits degrade with dilution requirements for heavy fuel samples [Franz, 1995]. The combined detection limit for sodium and potassium on diluted fuels does not meet most gas turbine operating specifications. Some improvements have been made in the last few years, but they consist of the addition of more gases and expensive glassware. Either way, the time consuming dilution step can lead to accuracy errors. Operation of the ICP spectrometer also requires a relatively well-trained person with experience in basic laboratory procedures. It is the kind of instrument one would place in a well staffed laboratory, but not necessarily on-site at a remote power plant.
Requirements For On-Site Fuel Analysis
On-site fuel analysis of liquid fuels suitable for use in heavy duty gas turbines has been performed successfully for over twenty five years. Its main purposes are to verify that a fuel meets the turbine manufacturer’s specifications and to monitor the effectiveness of the fuel treatment system. Analytical results are required on-site and without delay in order to determine if a fuel is acceptable or whether the fuel requires treatment prior to its introduction into the turbine. The requirement for instrumentation is to provide reliable on site analytical data to meet typical fuel requirements of sodium plus potassium at 0.5 to 1.0 parts per million.
In the case of aeroderivative gas turbines the fuel specifications are much more stringent. The typical fuel specifications call for sodium plus potassium plus lithium concentrations to be below 0.1 parts per million. It must be noted that reliable on-site, and in most cases, central laboratory analytical methods are not available at these low concentrations. It is an impossible specification without a creditable method for onsite verification.
Selecting a Qualified Contract Laboratory for Fuel Analysis
A fact which is often not taken into consideration is that few laboratories are familiar with requirements for proper fuel analysis. Most laboratories specialize in environmental, used oil or water analysis and seldom receive fuel samples. Although they have the resources for the analysis of elements in fluids, they may not be familiar with light and heavy fuels. To qualify a laboratory it is important to verify that it has the equipment, personnel and experience to analyze fuel samples. Even so, it is not uncommon to have several so called “qualified” laboratories analyze the same fuel sample with varying results. Table 1 is an actual example of an untreated and treated (washed) North African residual oil sample that was divided into four parts and sent to four laboratories for analysis. Each of the laboratories had qualified personnel and the necessary analytical instruments; yet the results varied dramatically.
This example is not uncommon and can be repeated anywhere in the world when fuel samples are sent to several arbitrary laboratories for analysis. Sometimes these problem cannot be avoided, but they can be controlled by limiting analytical services to one or two laboratories that understand and have proven experience with fuel analyses. The user must verify laboratory credentials and experience before accepting analytical data as being absolute and correct. Faulty data can result in major repair costs and unexpected turbine down-time. The fuel treatment suppliers and turbine manufactures should be consulted if local laboratory capabilities are questionable. Some fuel treatment system and gas turbine suppliers provide analytical services to their customers on a limited basis.
Selecting an On-site Analytical Technique
Obtaining accurate and timely fuel analysis is often a problem for gas turbine installations. There may not be access to laboratories equipped with the proper instrumentation and qualified and trained personnel for fuel analysis. Furthermore, the majority of gas turbine sites are in remote locations. Decisions on fuel treatment cannot be delayed until fuel samples are sent to an off-site laboratory. Analytical results are time sensitive and the capability to perform the analysis must be close to the source of the fuel sample. On-site fuel analysis at the gas turbine site has thus become the norm, and the challenge was to find an analytical technique that provides good analytical precision in non-ideal conditions. The key operational considerations that the instrumentation has to meet are [Lukas, 1993]:
- Environmental constraints (no air conditioning, high humidity, etc.)
- Ease of operation by minimally trained personnel
- Simple and reliable sample introduction
- Analytical performance to determine fuel treatment requirements
- Availability of consumables
- Safety
Table 1. Round Robin Analytical Test* on a Residual Oil Sample
|
|
|
|
|
|
|
|
|
|
1
|
5.1
|
<1
|
42.5
|
<1
|
<1
|
42.5
|
2
|
10
|
<1
|
34
|
4
|
<1
|
32
|
3
|
6
|
<1
|
32
|
1
|
<1
|
35.5
|
4
|
32
|
4
|
19
|
25
|
3
|
16
|
* Data reported in parts-per-million (ppm)
From the foregoing discussion of fuel analysis analytical techniques, one might assume that the ideal technique is graphite furnace atomic absorption (GF/AAS) followed closely by inductively coupled plasma atomic emission (ICP). These techniques offer the lowest detection limits and meet most of the analytical requirements of the gas turbine manufacturers. Unfortunately, this is true in theory, but frequently not in practice.
A classic example is the GF/AAS instrument recommended by a turbine manufacturer for use at a remote location in the jungles of South America. Although the instrument was perfect for the chemist in his laboratory, it failed to provide reliable data at the customer’s site. Data was erratic from day to day and the user soon lost confidence in the analysis. Six months later it was determined that dust raised by trucks on an access road periodically contributed to the analysis. The dust contained salt from the nearby ocean and contaminated the lengthy sample analysis procedure of the GF/AAS technique.
The main features of analytical methods available for gas turbine fuel analysis are summarized Table 2. Since the mid 1970’s, and still today, the only type of instrument that continues to meet the on-site fuel analysis requirements are those that use the rotating disc electrode (RDE) atomic emission technique.
Table 2. Comparison Summary of Analytical techniques for On-site Fuel Analysis
|
|
|
|
|
Detection Limit
|
Good
|
Excellent
|
Good
|
Very Good
|
Precision
|
1%
|
3-15%
|
3%
|
1%
|
Stability in Non Laboratory Environment
|
Fair
|
Poor
|
Very Good
|
Fair
|
Sample Preparation
|
Dilution required for heavy fuels
|
Ashing
|
Not required
|
Dilution required for heavy fuels
|
Ease of Operation
|
Simple
|
Complex
|
Very simple
|
Complex
|
Sample Throughput
|
5 to 10 minutes for 12 elements
|
30+ minutes for 6 elements
|
1 minute for 12 elements
|
1 to 4 minutes for 12 elements
|
Consumables (Daily & Capital)
|
Gases & hollow cathode lamps
|
Gases, graphite furnaces and hollow cathode lamps
|
Graphite electrodes
|
Gases and glassware
|
Instrument Cost
|
$20000 to $65000
|
$25000 to $90000
|
$65000 to $75000
|
$80000 to $120000
|
Cost per Analysis
|
$3 to $15
|
$15 to $30
|
$1 to $2
|
$2 to $4
|
Fuel analyzers using the (RDE) atomic emission technique are ideally suited to operate in non-laboratory environments, are easy to operate without sample preparation and provide a complete analysis of all the elements of interest in less than one minute. The technique does not have detection limits as good as graphite furnace or inductively coupled plasma instruments, but the limits of detection are low enough to provide acceptable on-site fuel analysis. There have been major improvements in the last few years on spectrometers of this type and typical detection limits for the key contaminants of sodium and potassium are below 0.1 ppm.
Experience has shown that by following a few basic procedures, good performance can be maintained. Some of these are detailed in the next few sections.
Statistical Improvement of Accuracy
Fuel treatment has proven to be very effective at removing contamination from gas turbine fuel. For highly contaminated fuel, several treatment steps may be required. Eventually, sodium and potassium concentrations must be below the specifications of the turbine manufacturer so the fuel can be introduced into the turbine.
The spectrometric results are the basis for determining the amount of treatment, and subsequently, the effectiveness of that treatment. It is thus important that on-site fuel analysis produces reliable and accurate data.
Untreated fuel is often not homogeneous and contains contamination in the form of particulates, and sometimes water. These contaminates along with paraffin in the fuel can have an effect on the repeatability of the analyses such that analytical results will vary from one test to the next. In order to improve the precision of the fuel analyzer, a sample should be analyzed three times and then averaged. The average of three analyses improves precision and provides a rational basis for deleting one of the analysis if for some reason it is radically different from the other two. Figure 2 shows a printout of an actual example of three consecutive analyses on the same fuel sample.

Figure 2. Printout of three analyses on the same fuel sample
Clearly the third analysis does not fit the norm because the readings for sodium and lead do not follow the trend of the first two analyses. The third analysis should be rejected and an average can be calculated for the first two analyses. However, to increase confidence in the data, the third analysis can also be repeated and averaged with the first two.
Modern instruments have software that make it easy to average multiple analyses, and also to reject any that do not fit the trend. Built-in data bases to keep permanent records of analyses before and after treatment of the fuel have also become standard. This makes it easier for the laboratory to keep track of large amounts of analyses over time. The data is also frequently used for statistics and as a permanent record of fuel quality to validate warranty compliance.
Sample Contamination
The analyses of an analytical instrument are only as good as the samples that are provided. It is imperative that the fuel sample be taken from the same sampling point and in an approved and repeatable manner such as ASTM D 4057 Manual Sampling of Petroleum and Petroleum Products. The sampling container must be clean and free of any contamination. In the laboratory, sample handling and analytical techniques are also important. Incorrect or careless procedures can influence analytical data which may lead to inaccurate data.
Contamination through careless operation can also be a source of error. The sample or the graphite electrodes of the RDE spectrometer should never be touched by hand. The electrodes must always be installed with a laboratory disposable towel to avoid contamination from the fingers. Perspiration from the body will easily add several parts per million of sodium to the analysis.
Figure 3 shows actual analytical printouts to confirm this situation. The same distillate fuel sample is analyzed three times. The first is a normal and proper analysis, the second is with the disc electrode installed by hand and the third with the tip of the rod electrode rubbed against the palm of the hand.
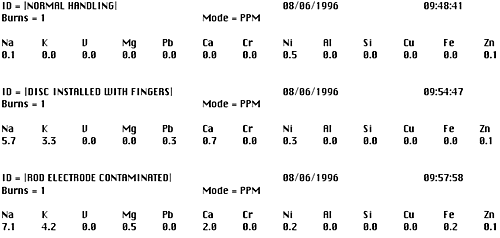
Figure 3. Analytical results showing the effect of contaminated electrodes
The influence on sodium due to improper handling of the electrodes is clear and evident in the second two analyses. In both instances, although there is no sodium in the fuel, contamination from improper operation (perspiration) has increased the sodium analysis results by several parts per million. Such errors, when not detected can lead to erroneous conclusions and costly consequences about the status of the fuel or the fuel treatment system. Although the fuel analyzer is simple to operate, proper housekeeping procedures must always be followed.
Sample Preparation & Treatment
Fuel analyzers compare the unknown fuel sample to a calibration curve generated with a commercially available oil standard. The industry has settled on one type of calibration standard which works well for most applications, but in some instances, can also be the source of accuracy problems. Experience has shown that when a fuel is treated to remove contaminants, particulates are removed and the concentration levels of sodium and potassium are reduced. Precision of the analysis is improved and eventually concentrations become so small that they approach zero; the same as the instrument calibration curve. This results in good correlation among analytical techniques on all types of fuels when concentrations of contaminants are low and approach zero.
It is good practice to always analyze a fuel sample immediately after it has been drawn. This will assure a homogeneous solution, limits the probability of outside contamination and thus improves the analytical data. In most instances, however, there is a delay between the time the sample is taken and when it finally reaches the laboratory. Except for light fuels which can be analyzed as received, bunker and crude oils should he heated and thoroughly shaken prior to analysis. The simplest and most effective method is to place the sample bottle into a heated ultrasonic water bath for about 5 to 10 minutes. The temperature of the water is not critical, but should be above the sample’s pour point. Heating the sample will make heavy fuels less viscous and the ultrasonic action will create a homogeneous mixture.
The analysis of some crude and residual fuel types with high concentrations of contaminants may be a little more complex and could result in inaccuracies for vanadium. Although they are rare, they can be problem fuels for any analytical technique. Sample preparation and treatment procedures, beyond those mentioned above, may have to be applied to improve accuracy with the RDE technique.
There have also been documented cases on these problem fuels where accurate vanadium and sometimes sodium analysis can only be obtained with some sample preparation. A simple test will determine if sample preparation has to be applied to a fuel. The test is to dilute the suspect fuel sample with an equal amount of clean kerosene, or preferably the base oil (0 ppm) standard. The undiluted and diluted fuel sample are analyzed and the vanadium data is compared. Normal fuel will exhibit the expected 2:1 vanadium ratio between the undiluted and diluted sample. This means sample preparation is not required and the sample can be analyzed using normal procedures. If, however, the ratio is not 2:1 and more like 2:1.5, then a technical representative from the instrument manufacturer should be consulted for further assistance. Instrument operating parameters or additional sample preparation may be necessary to achieve more accurate results. Typically these are minor procedures and limited to instrument reference or software modifications. An example showing the effects of such a procedure versus a certified residual fuel standard is shown in Table 3.
Table 3. Special fuels method to improve accuracy
|
|
|
|
NIST Certified Analysis*
|
37
|
17.5
|
28.2
|
Normal Analysis
|
16.5
|
12.1
|
19.9
|
Analysis after Modifications
|
35.4
|
16.4
|
27.6
|
*Data reported in parts-per-million (ppm)
*The certified analysis is for an NIST 1634C No.6 Residual Fuel Oil
(Sample supplied by the National Institute of Standards and Technology)
The normal analysis of the certified residual fuel standard is inaccurate as compared to the expected analytical results. However, with the implementation of a minor fuel dilution procedure and spectrometer reference modification the analysis compares favorably to the NIST Certified Residual Fuel Standard. It clearly shows how analytical accuracy can be restored for otherwise difficult samples.
Confirming Analyses
It is important to have confidence in the analytical capabilities of the on-site analyzer and the training of on-site personnel for gas turbine fuel analysis. One way of obtaining this confidence is to periodically send fuel samples to an independent laboratory for analysis. Of course, as mentioned previously, the independent laboratory must be one experienced with fuel samples.
Many fuel treatment system manufacturers and gas turbine suppliers have their own laboratories that can provide the comparison, or will be pleased to make recommendations. The example in Table 4 shows such a comparison. Several fuel samples and calibration standards were analyzed by the spectrometer at the gas turbine site and were also sent to the gas turbine manufacturer for comparison. The turbine site is at a remote location and used the RDE technique, while the gas turbine manufacturer used the ICP technique at their central laboratory.
Table 4. Comparison of on-site analysis with central laboratory analysis
|
|
|
|
|
|
|
|
|
|
|
|
|
|
Heavy Fuel
|
On-Site (RDE)
|
8.8
|
0.3
|
3.0
|
0.6
|
0.6
|
7.0
|
0.0
|
2.4
|
0.7
|
3.6
|
0.0
|
8.3
|
Heavy Fuel
|
Laboratory (ICP)
|
6.4
|
<5
|
4.5
|
0.6
|
<3
|
6.4
|
0.0
|
2.7
|
1.1
|
3.3
|
0.1
|
9.5
|
Diesel Fuel
|
On-Site (RDE)
|
0.2
|
0.2
|
0.4
|
0.6
|
0.0
|
0.1
|
0.2
|
0.3
|
1.2
|
0.7
|
0.1
|
0.3
|
Diesel Fuel
|
Laboratory (ICP)
|
<.5
|
<5
|
<.1
|
0.5
|
<3
|
<.2
|
<.1
|
<.1
|
<.1
|
0.7
|
<.1
|
<0.5
|
2.5ppm in diesel
|
On-Site (RDE)
|
2.2
|
2.2
|
2.0
|
3.0
|
2.3
|
2.4
|
1.5
|
2.5
|
3.0
|
2.9
|
3.1
|
2.1
|
2.5ppm in diesel
|
Laboratory (ICP)
|
2.4
|
<5
|
2.3
|
2.9
|
<3
|
2.4
|
2.5
|
2.3
|
1.8
|
3.2
|
2.4
|
2.4
|
10 ppm Cal. Std.
|
On-Site (RDE)
|
10.4
|
11.1
|
9.7
|
10.0
|
9.3
|
10.5
|
10.4
|
10.2
|
9.5
|
10.2
|
9.1
|
10.2
|
10 ppm Cal. Std.
|
Laboratory (ICP)
|
10.1
|
11.4
|
10.2
|
10.0
|
9.4
|
10.4
|
9.4
|
10.0
|
10.3
|
9.5
|
8.8
|
10.1
|
The first two fuel samples, a heavy fuel and a diesel fuel, show that there is good correlation between the analyses obtained on-site at the power plant and the analyses by the laboratory of the gas turbine manufacturer. The next two samples had known concentrations for the various elements and were divided and analyzed in the same manner. One utilized the method of additions in which 2.5 ppm by weight of a calibration standard was added to a clean diesel fuel and the other was a 10 ppm calibration standard.
The comparison confirms that the data obtained at the gas turbine site correlates well with similar analysis at a well staffed central laboratory with fuel analysis experience. It is good practice to perform such a test once a year or whenever the performance of the local laboratory is questionable. The comparison serves to provide confidence in the capabilities of the on-site analyses.
Conclusion
Although some of the gas turbine manufacturer’s fuel contamination specifications are extremely stringent and challenge the capabilities of modern on-site analytical instrumentation, the RDE spectrometer provides the best practical solution. This is particularly true since the burden of fuel cleanliness proof is usually placed on the gas turbine user who has limited on-site expertise to operate modern and complex analytical instrumentation. Although the fuel may have been clean at the refinery, and there is a certified analysis to prove it, there is no guarantee that it still meets specifications after transport. This has created a need for on-site fuel analysis for all types of liquid fuels to protect the gas turbine from corrosion and deposits.
The need for on-site analysis continues to be fulfilled best by fuel analyzers based on the rotating disc electrode atomic emission spectrometer (RDE). It is the only analytical instrument that has been able to do the job consistently for over 25 years. It is simple to use, requires no hazardous gases, operates in non-laboratory environments and provides good accuracy. There are other analytical techniques with better accuracy, but they do not meet the other performance and operational requirements for on-site fuel analysis.

This information has been sourced, reviewed and adapted from materials provided by AMETEK Spectro Scientific.
For more information on this source, please visit AMETEK Spectro Scientific.