Thermal spraying is a generic term to describe a collection of coating processes involving material transport at high speeds and elevated temperature. Particles or droplets (of coating materials) are accelerated at high speeds, heated and are made to impact an object (i.e. the substrate). Successive particles thus reach a surface where the high energy causes the particles to deform and form a mechanical bond with the underlying surface. These particles vary depending upon the process, but can cover a range of 1 to 200 microns.
Coating Formation
A coating forms by layering individual flattened particles on top of one another. The flattened particles, also known as lamellae, or “splats” form around prior surface features, cool and solidify. The rapid solidification rate of 1 million °C/sec provides a fine microstructure and metastable phases that provide properties not attainable with other material production processes. Flattening of the particles or droplets depends upon the deformation of the particle. For molten particles, the flattening ratio (disk diameter vs initial particle size) can be up to a factor of 5. Lower temperature processes impart a lower degree of flattening.
Coating Adhesion
Bonding of the particles or droplets depends upon both the material being deposited and the process used for deposition. A class of materials known as self bonding materials exhibit an exothermic response on heating and thus supply the heat necessary to create an interfacial bond. More commonly, materials do not have the ability to produce a chemical bond with the substrate and hence the surface needs to be roughened by a process such as grit blasting to provide a basis for mechanical bonding. Surfaces that can be coated include plastics, glass, ceramics, metals, paper and composites. Coating strength is dictated by the strength between the coating structural elements, known as cohesive strength, and the strength of the coating to the underlying base material, termed adhesion strength. The cohesive strength depends upon the material properties, but also porosity within the coating. This porosity includes spaces between the flattened particles and in the case of ceramics, microcracks. The porosity contributes to a decrease in the strength and has been the focal point of the more advanced coating processes that have the ability of decreasing the porosity if required.
Coating adhesion is measured according to ASTM C633. Standard Test Method for Standard Test Method for Adhesion or Cohesive Strength of Flame-Sprayed
Coatings.
Coating Processes
The material delivery in thermal spray is provided by a torch/ gun or more simply a nozzle that establishes a thermokinetic condition for heating and transporting the feedstock. The first process was discovered by Schoop in the late 19th century. The passage of zinc particles through a flame resulted in adhesion of particles onto a surface. This process initiated a series of process improvements leading a wide range of coating methods. The list of thermal spraying processes incorporates flame spraying, two wire arc spraying, plasma spraying, detonation gun, high velocity flame spraying (HVOF) and cold spraying.
The spraying techniques can be divided in terms of form of feedstock (particles, wire, ceramic rod and lately atomised droplets), material generation and transport medium velocity or transport medium temperature. Figure 1 shows the processes as a function of temperature and material delivery speed.
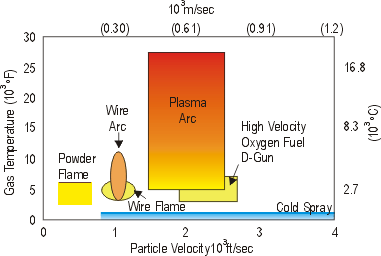
|
Figure 1. Comparison of the processing temperatures and material transport velocities for the various thermal spray processes.
|
Applications
Thermally sprayed coatings are used in a wide array of applications. Table 1 briefly outlines the industries in which the various processes are employed.
Table 1. Outline of the use of various thermal spray technologies in various industry sectors.
|
Reclamation
|
•
|
•
|
|
|
Corrosion protection
|
•
|
•
|
|
|
Automotive
|
|
•
|
•
|
|
Aircraft
|
|
|
•
|
•
|
Biomedical
|
|
•
|
•
|
•
|
Printing
|
•
|
|
•
|
•
|
Textile
|
|
|
•
|
|
Mining
|
|
|
•
|
•
|
|