The development of effective storage technologies for electrical energy plays a key role in the development of "electrically mobile" technologies. Such technologies will enable the reduction of emissions and lead to more efficient use of renewable energy as they are implemented in smart grids. Li-ion batteries are a good choice for these applications as they can provide high energy and power densities.
Lithium-Ion Batteries
The performance of a Li-ion battery is determined by the energy density, battery power and capacitance, charge and discharge rates, as well as its lifetime. The functionality, schematically shown in Fig. 1, is based on the alteration of active ions because of diffusion.

Figure 1. Schematic setup of a Li-ion battery. The performance is based on diffusion of Li- ions through the separator between the two active materials of cathode and anode.
The Importance of Microstructural Characterization
Therefore, the microstructure of the materials has a strong influence on the battery performance, alongside geometrical aspects such as the design of the cell or the thickness of the electrodes or physical properties such as diffusion coefficient, thermal capacity and expansion and volume change or resistance.
The key parameters of the microstructure of the battery material are the shape and size of the grains, surface area and volume fraction of phases.
To ensure an in-depth understanding of the battery performance, it is important to conduct a microstructure characterization of Li-ion batteries. Using microstructure characterization, it becomes possible to evaluate the relation between battery performance and cell design.
By obtaining quantitative microstructural data, it becomes possible to develop physical models. The visualization of microscopic phenomena because of aging history is also important for reliability analysis, which aids in the prevention of critical accidents caused by short circuit failures.
Correlative Light and Electron Microscopy (CLEM)
Correlative light and electron microscopy (CLEM) is necessary for this application as it enables the combination of defect identification and the optical properties of light microscopy (LM) with detailed structural analysis in the scanning electron microscope (SEM).
While LM provides a quick overview of morphology and the optical appearance of damaging effects and phases, SEM images offer information about particle size, shape and chemical composition within the same region. This allows multimodal data extraction from the microstructure. For these reasons, it is easy to understand why CLEM is viewed as an essential tool for the characterization of battery materials.
Sample Preparation and Imaging
The steps followed for sample preparation and imaging are listed below:
- A standard cylindrical Li-Ion consumer cell of type 18650 was aged for 50 days with a constant voltage of 4.2 V at 65 °C. Then it was discharged and opened in a glove box in an argon atmosphere.
- After removing the electrolyte, the sample was embedded in epoxy resin and prepared in accordance with high-end materialographic sample preparation protocols.
- The sample obtained is a polished cross-section of the battery. The sample was placed into the “Specimen Holder CorrMic Mat Universal A” which is a universal materials sample holder exclusively designed for CLEM by Carl Zeiss.
- This holder can be used in LM as well as SEM to keep the sample fixed in the holder during the complete imaging process.
- The holder has three fiducial markers which define a coordinate system that can be calibrated very quickly and semi-automatically in the Shuttle & Find module of the AxioVision Software. LM imaging of the sample was performed in an Axio Imager.Z2 (Carl Zeiss Microscopy GmbH), a compound light microscope used for materials analysis.
- 20 x and 50 x objectives (EC Epiplan-Neofluar 20 x / 0.5 HD DIC and 50 x / 0.8 HD DIC), as well as an AxioCam HR camera, were utilized for imaging. With this configuration, brightfield images in the reflected light mode were obtained with and without polarization contrast.
- Regions of interest (ROI) for further investigation were defined in the LM images with the Shuttle & Find software module. Then the sample was transferred to a SUPRA 40 VP FE-SEM (Carl Zeiss Microscopy GmbH) controlled by the same software.
- After the semi-automatic calibration of the sample-holder and fine calibration, the ROIs in the LM images were relocated within a few seconds at a precision of less than 5 µm.
- SEM imaging was done at an acceleration voltage of 15 kV with the 4 quadrant angular selective backscattered electron (AsB®) detector. Subsequently, an energy dispersive X-ray spectroscopy (EDS) mapping of the same area was performed with the SEM and a Bruker Quantax 200 XFlash-Detector with 133 eV spectroscopic resolution.
Results Obtained
A brightfield LM image of the layer structure inside an aged Li-ion battery is shown in Figure. 2.

Figure 2. Brightfield LM overview within the layer structure of an aged Li-ion battery.
The anode and cathode are layered alternately, each having a separator in-between.
The cathode comprises of an aluminium collector coated by active lithium metal oxide material. The anode has a copper collector with graphite as active material.
Aging effects can be seen within the separator, showing a layer growing from the cathode into the separator. An ROI (red rectangle) is chosen that has a complete unit cell of the battery with aging effects in the separator. The selected ROI is shown in more detail in Figure. 3.
Figure 3a is a brightfield LM image at a higher magnification and Figure 3b shows the polarization contrast in LM. Figure 3c is a backscattered electron (BSE) image of the same area in the SEM, and Figure 3d shows an EDS mapping with the distribution of the six chemical elements of highest concentration.

Figure 3. CLEM of the ROI indicated in Fig. 2 with different contrasts of brightfield (a) and polarized light (b) in LM as well as BSE signal (c) and EDS mapping (d) in SEM.
These contrasts complement each other well, and it is only this combination that enables a detailed microstructural analysis of such a battery cell.
Brightfield LM gives a perfect overview of the geometry and morphology within the electrodes as well as of the aging effects inside the separator. In polarized LM, different phase orientations of the graphite in the anode can be observed, whereas the BSE image ensures the fine grain structures within the cathode material is visible. This contrast technique also enables segmentation of the cathode using image analysis so that grain size and distribution can be quantified.
The additional EDS mapping completes the correlative imaging and offers explicit qualitative information on the chemical elements. Aluminium and copper collectors, graphite (carbon) anode and organic separator foil can be identified easily.
Due to physical limitations, lithium cannot be detected in EDS directly. However, according to the functional principle it can be worked out qualitatively that the sharply edged grains within the cathode active material are made of LiMn2O4, and the spherically shaped grains are made of LiNixCoyO2.
Conclusion and Outlook
The Shuttle & Find interface for CLEM allows productivity in structural analysis of Li-ion batteries because of a quick, consistent and precise workflow. As the process of searching the same ROI in both microscopy modes is now automated, the workflow is significantly faster. Therefore, failures can be determined quickly and the development cycle time can be minimized. This results in a significant increase of sample throughput.
The solution also offers new possibilities especially for quantitative image data analysis from the same ROI in different microscopes, which can now be carried out methodically. As Shuttle & Find is compatible with CrossBeam® workstations, the sample can also be transferred there for more detailed investigations. Then specific structures, such as migrations, can be selected and 3D inspection can be performed by focused ion beam (FIB) milling. It is also possible to fabricate a thin lamella from the selected structure for high resolution transmission electron microscopy (TEM) imaging. This enables electron energy loss spectroscopy (EELS) analysis by which the local distribution of Lithium can be determined directly.
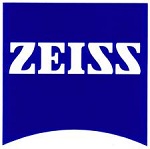
This information has been sourced, reviewed and adapted from materials provided by Carl Zeiss Microscopy GmbH.
For more information on this source, please visit Carl Zeiss Microscopy GmbH.