Toray Advanced Composites USA (TCAC) has vast experience in preparing composite prepreg products for applications in the aerospace industry utilizing vacuum bag pressure only (VBO) or out of autoclave (OOA) processing. As the prepreg supplier, TCAC perhaps provides the most volume of composite materials for applications in general aviation aircraft, unmanned aerial vehicles and satellites.
Toray Advanced Composites supplies cyanate ester-based resin systems and epoxy- based resin systems for VBO and OOA cure processing in addition to new BMI systems for use in higher temperature applications. Toray provides systems curing at below 250 °F and other systems curing at higher temperatures for wet and hot service capabilities. Lower cure temperatures come good in certain cases as it enables the utilization of lower cost tooling, while reducing thermal stresses, which are essential for a dimensionally stable structure.
Besides different resins, Toray has employed OOA resin systems on various standard, intermediate and high modulus fabrics and fibers, which include pitch-based materials. Moreover, the company has flight experience with quartz and glass based materials for aircraft radomes and structures made of out of autoclave resin systems. This article discusses processing conditions and resin databases generated which rival conventional autoclave cure processes.
Toray Out of Autoclave Applied Resin Systems
TC420 – Designed for high temperature applications with an operating temperature of as high as 600 °F.
TC350-1 – High toughness third generation system with 45+ days outtime and can be cured at 275 °F with a required postcure of 350 °F.
TC275-1 - Designed for very low void content thick parts under vacuum cure pressure only. Wide cure temperature window; Very low moisture absorption and excellent hot/wet strength retention.
TC250 – Second generation improved toughness and higher temperature performance system.
BT250E-6 – Designed for high fatigue and fracture critical structure like helicopter rotor blades.
BT250E-1 - Industry standard out of autoclave prepreg resin used on hundreds of large scale unmanned vehicle systems and more than 5,000 Cirrus aircraft.
.jpg)
Toray History and Background
Toray Advanced Composites has a long history of producing hot melt impregnated composite prepregs for use in applications under either autoclave cure processing or vacuum bag. The part quality matches that of the same autoclave-cured resins when applied to the correct part configuration with suitable production workmanship and process engineering.
.jpg)
The highly popular Cirrus SR-22 series of aircraft features both fuselage and wing structure manufactured in out of autoclave vacuum cure pressure conditions.
.jpg)
AeroVironment's Global Observer is manufactured completely in low-pressure vacuum cure conditions from wing to fuselage. It is perhaps one of the larger examples of vacuum only processing of large structure.
According to several technical papers, layup methods and techniques are like lay ups and part processing for autoclaves. However, for OOA processing, more process control and better production controls are essential during lay up, debulking, cure and inspection to obtain good part quality with minimal void contents. Eventually, it is essential for a customer to identify the overall cost gain of the entire process engineering and technical production resources to create quality parts matching the autoclave grade.
.jpg)
General Atomics Aeronautical Systems utilizes prepregs from Toray used in low pressure curing processes for Reaper.
.jpg)
Lockheed Martin Denver Orion Heat Shield utilizes Toray prepregs in a low pressure out of autoclave cure process.
Processing
Accurate process controls and non-destructive inspection (NDI) methodologies are key in large and thick structures to produce a structural part with a quality and longevity of a part cured in an autoclave under high pressure. Debulk schedules, breather types, air path methods, lay up materials, resin rheology, ramp rates, temperature and time are need to be considered during the fabrication of thick structural load carrying parts.
Prepreg Technology
Preventing and eliminating voids, mainly in the form of air inside the plies and between plies from parts before resin gelation, are critical for effective OOA parts production. Toray has more than two decades of experience in producing proprietary prepreg resins and technologies to fabricate high- performance OOA materials. Figure 6 depicts an optimal viscosity profile demonstrating a gradual drop in viscosity of the resin which then gets stabilized when curing temperature prior to start rising during final cure.
.jpg)
An example of an optimal viscosity profile which shows a gradual decrease in viscosity of the resin which then stabilizes during the temperature at cure before beginning to increase during final cure.
Debulk Schedules
Debulk schedules are essential for low void content structure. For out of autoclave processing, the resin system must be tailored for debulks. Resin rheology must take into account debulks for plies consolidation without detaining air through resin flow. Eventually, decision regarding optimum debulk schedules is on the hands of prepreg supplier and the user.
Lay up Considerations
Composite layups between autoclave and out of autoclave parts share several common features but with out of autoclave low cure pressures, it is essential that all tools have to be used to enhance the ability for plies consolidation and entrapped air removal. Cautious consideration to these methods becomes more crucial when there is an increase in part size and thickness.
Alternative Pressure Intensifiers
The utilization of secondary positive sources of pressure sometimes benefits thick complex parts that carry structural loads. These secondary methods use pressure intensifiers such as fluid pressure, closed mold processing, hydrostatic pressure, shrink, solid closed mold tooling, caul plates and bladders, and double bag techniques to utilize vacuum for positive pressure.
Secondary Materials
Syntactics, surfacing films, peel plies, and bonding films help the production of low void content parts designed to work under low pressure as well as vacuum conditions.
Other Considerations
It is important to dry honeycomb and foam structures prior to curing and when stored in desiccated environment to lower volatiles. It is also essential to document and follow repair techniques for voids present in thick parts. Figure 7 shows a typical lay up example utilized in the lay up of out of autoclave cured laminates.
.jpg)
A common lay up example used in the lay up of out of autoclave cured laminates.
Prepreg Selection
Nowadays, out of autoclave processing and prepreg system fashioned for low pressure processing provide the user the ability to rival with autoclaved cured systems. Autoclave curing offers high quality and more uniform part quality due to the collapsing of any air and volatiles inside and between the plies by the increased cure pressure (>30 psi when compared to the roughly 14.7 psi (1 atm)). Autoclave cured parts normally demonstrate better matrix fiber interfacial properties, have fewer voids and are more dense. Hence, they are stiffer, stronger and can be inspected by non-destructive techniques such as NDI and C-scan. Figure 8 shows standard NDI results illustrating good backwall and low porosity, corroborated with cross section microscopy.
Toray has realized the most success with customers during the selection of prepregs or prior to qualification by improving the impregnation level, resin, and lay up methods. This ensures the optimal process and material for yielding parts matching autoclave cured parts.
.jpg)
Typical NDI results showing low porosity and good backwall, confirmed with cross section microscopy.
Composite Laminate Fabrication
Some of the ongoing efforts in out of autoclave processing focus on AFP and ATL techniques to ensure high quality layer to layer part fabrication for reducing gross air entrapment between plies. Hence, OOA cured parts perhaps fall short in terms of void content, NDI, structural and quality criteria when compared to autoclave cured parts because of complexity in lay up and the need for the involvement of more technical skill. Figure 9 shows demonstration parts produced in autoclave and OOA to verify processing equivalency.
.jpg)
Demonstration parts fabricated both in autoclave and out of autoclave to confirm processing equivalency.
Part Quality Inspection
Voids and delaminations are given the primary focus during the comparison of part quality between autoclave and OOA cured parts. These can be analyzed by destructive methods of the part or a witness panel by matrix acid digestion and microscopic cross sectioning. NDI techniques may include thermography, acoustic emission, ultrasonic C-scan, and others. Figure 10 shows Toray TC350-1 90+ ply carbon fiber spar (0.8 inches/2 cm) section demonstrating how to measure void content across the part in line with NDI inspection results.
.jpg)
Here we have TorayTC350-1 90+ ply carbon fiber spar (0.8 inches/2 cm) section illustrating a good example of how to conducting measurement of void content throughout the part to correlate with NDI inspection results.
Toray has identified that toughened resins laminated with void contents range of 0.7%-2% can cause 50% returned signal amplitude loss. Lockheed Martin has produced space re-entry heat shields utilizing Toray's prepreg resin systems cured OOA, and assesses their part quality using thermography.
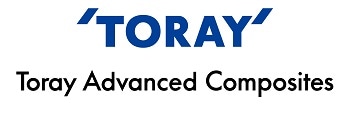
This information has been sourced, reviewed and adapted from materials provided by Toray Advanced Composites.
For more information on this source, please visit Toray Advanced Composites.