Toray Advanced Composites is a key provider of advanced resin systems and composites for the radome industry and antenna industry. The company’s cost-competitive and superior-quality materials are designed for a myriad of high-performance aerospace, electronics, communications, and commercial applications. This achievement is a result of its quality products, advanced technology, and customer-driven approach that promotes teamwork, cooperation, and responsiveness.
.jpg)
.jpg)
Radome & Antenna Composites
Today’s advanced radar and satellite communication system manufacturers need Toray to provide the latest low dielectric prepregs. The company’s adhesives and syntactic foams, liquid resin systems, and cyanate ester and epoxy-based prepregs have low moisture absorption, low loss tangent, and low dielectric constant properties. The combination of these capabilities and the company’s segregated production facilities completely eliminates conductive graphite from dielectric materials, thus ensuring electrically pure products with better quality.
.jpg)
.jpg)
Meeting the Challenges
Toray’s materials are specified for production of different shipboard, ground, airborne and space-based products like sonar domes, radomes, reflectors, antennas, radar-absorbing, and microwave transparent structures. Widely accepted and adopted reinforcements including high density polyethelene, aramid, quartz and fiberglass are completely compatible with the company’s advanced resin systems and can be delivered as prepregs to meet the most challenging mechanical and electrical applications.
|
Cyanate Ester Quartz Fabric |
Low Dielectric Epoxy/ Quartz Fabric |
Low Dielectric Epoxy/ Glass Fabric |
Electrical Performance |
BEST
Dielectric Constant 3.2 to 3.35
Loss Tangent 0.001 to 0.009 |
BETTER
Dielectric Constant 3.4 to 3.8
Loss Tangent 0.009 to 0.011 |
GOOD
Dielectric Constant 4.5 and above
Loss Tangent 0.011 and above |
Laminate Impact Strength |
Very Good |
Very Good |
Moderate |
Temperature Performance |
High
Tg 275°- 450°+F (135°-204°C) |
Moderate - High
Tg 250°- 400°F (121°-204°C) |
Moderate - High
Tg 250°- 400°F (121°-204°C) |
Laminate Moisture Absorption |
Lowest
0.1 - 0.6% |
Very Low
0.6 - 0.8% |
Moderate
1.2 - 1.6% |
PREPREG RESIN SYSTEM* |
Quartz Laminate |
Neat Resin |
Loss Tangent (Df) |
Dielectric Constant (Dk) |
Loss Tangent (Df) |
Dielectric Constant (Dk) |
Product Resin |
Name Type |
Measured at 10 GHz |
Cure Temp. °F/°C |
Tg °F/°C |
Tg after post cure °F/°C |
Out of Autoclave Processible |
Df |
Dk |
Df* |
Dk |
BTCy-2 |
Cyanate Ester |
< 0.001 |
3.28 |
0.001 |
2.70 |
350 °F/177 °C |
375 °F/191 °C |
N/A |
YES |
BTCy-1A |
Cyanate Ester |
0.001 |
3.33 |
0.003 |
2.75 |
350 °F/177 °C |
365 °F/185 °C |
405 °F/207 °C |
NO |
EX-1515 |
Cyanate Ester |
0.004 |
3.20 |
0.004 |
2.80 |
250 °F/121 °C |
249 °F/121 °C |
345 °F/174 °C |
YES |
RS-3 |
Cyanate Ester |
0.009 |
3.19 |
0.009 |
2.81 |
350 °F/177 °C |
375 °F/191 °C |
490 °F/254 °C |
YES |
TC420 |
Cyanate Ester |
0.009 |
3.39 |
0.01B (11) |
3.11(1) |
350 °F/177 °C |
350 °F/177 °C |
610 °F/321 °C |
YES |
EX-1522 |
Epoxy |
0.011 |
3.3B |
0.008 |
2.80 |
350 °F/177 °C |
356 °F/180 °C |
N/A |
YES |
BT250E-1 |
Epoxy |
0.011 |
3.40 |
0.019 |
3.00 |
250 °F/121 °C |
257 °F/125 °C |
N/A |
YES |
TC250 |
Epoxy |
0.012 |
3.49 |
0.021 |
3.00 |
275 °F/135 °C |
285 °F/140 °C |
356 °F/180 °C |
YES |
RS-8HT |
BMI |
0.014 |
3.49 |
0.007 |
3.01 |
350 °F/177 °C 482 °F/250 °C |
397 °F/203 °C |
545 °F/285 °C |
NO |
*In order of laminate loss tangent. Test method ASTM D2520.
(1) At 1MHz (2) Thermoformable (3) At 6.5 GHz (4) At 35 GHz
*See www.toraytac.com for individual data sheets for properties and process information.
PREPREG REINFORCEMENTS |
Sp. Gravity (g/cc) |
Moisture Pickup (% by Wt.) |
Service Temp. |
Applications |
Reinforcement |
Dk (10 GHz) |
Df (10 GHz) |
Aircraft |
Ground Systems |
Spacecraft |
Missiles |
“E” Fiberglass |
6.10 |
0.004 |
2.55 |
nil |
700°F |
• |
• |
|
|
“S” Fiberglass |
5.21 |
0.006 |
2.49 |
nil |
750°F |
• |
• |
|
|
Quartz |
3.78 |
0.0002 |
2.20 |
nil |
>1000°F |
• |
• |
• |
• |
HDPE |
2.00 |
0.0004 |
0.97 |
nil |
220°F |
• |
• |
|
|
LMR Kevlar® 49(1) |
3.85 |
0.008 |
1.47 |
1.9% |
350°F |
• |
• |
• |
|
(1) LMR Kevlar® 49 is a special Toray proprietary product which treats the Kevlar fiber such that moisture absorption is greatly reduced. LMR is our Low Moisture Regain designation for this material.
ADHESIVES & SYNTACTICS |
Neat Resin |
Quartz Laminate |
Product Name |
Resin Type |
Dielectric Constant |
Loss Tangent |
Dielectric Constant |
Loss Tangent |
Film Adhesives |
Dk |
Df |
Dk |
Df |
Cure Temp. °F/°C |
Cure Time Min |
Tg °F/°C |
EX-1516 |
Cyanate Ester |
2.8 |
0.008 |
N/A |
N/A |
250 °F/121 °C |
300 min |
258 °F/126 °C |
EX-1543 |
Cyanate Ester |
2.72 |
0.009 |
N/A |
N/A |
350 °F/177 °C |
120 min |
405 °F/207 °C |
RS-4A |
Cyanate Ester |
N/A |
N/A |
N/A |
N/A |
350 °F/177 °C |
120 min |
397 °F/203 °C |
TC4015 |
Cyanate Ester |
N/A |
N/A |
N/A |
N/A |
350 °F/177 °C |
120 min |
610 °F/321 °C |
Syntactic Film or Paste |
EX-1541 (11 pcf) |
Cyanate Ester Paste |
1.32 |
0.009 |
N/A |
N/A |
350 °F/177 °C |
120 min |
350 °F/177 °C |
EX-1541 (13 pcf) |
Cyanate Ester Paste |
1.32 |
0.009 |
N/A |
N/A |
350 °F/177 °C |
120 min |
350 °F/177 °C |
SF-5 (38 pcf) |
Cyanate Ester Film |
1.7 |
0.004 |
N/A |
N/A |
350 °F/177 °C |
120 min |
490 °F/254 °C |
TCF4001 (22-26 pcf) |
Cyanate Ester Paste |
1.55 |
0.012 |
N/A |
N/A |
350 °F/177 °C |
120 min |
350 °F/177 °C |
TCF4035 (40 pcf) |
Epoxy Film |
1.94 |
0.018 |
N/A |
N/A |
265 °F/130 °C |
180 min |
284 °F/140 °C |
TCF4045 (35.5 pcf) |
Epoxy Film |
1.57-1.84 |
0.008 |
N/A |
N/A |
355 °F/179 °C |
180 min |
356 °F/180 °C |
TCF4050 (69 pcf)3 |
Cyanate Ester Core Splice |
N/A |
N/A |
N/A |
N/A |
350 °F/177 °C |
120 min |
350 °F/177 °C |
(3) Unexpanded density
Carbon-Free Production for Low-Dielectric Materials
Toray Advanced Composites is proud of its advanced carbon-free production facilities. The company’s production floor has been specially equipped for the fabrication of radome-qualified composites.
.jpg)
.jpg)
The company’s facilities have the following features:
- Precision prepregging and precision filming capability
- Full computer-controlled process parameters
- Exclusive environmentally controlled carbon-free area with positive ventilation for quartz, glass, and electronic products
World Leading Radome Composite Materials
A radome is a cover designed to safeguard an antenna system from the environment, while also, in certain cases, providing lightning strike protection, aerodynamics, and stealthy features. Choosing the ideal composite materials is important for maintaining the radome-antenna system.
Applications include a ship, rail, military, and civil aircraft, and ground-based systems, including conformal or “patch” antennas.
In-flight, a military aircraft will interface with more than fifteen antennas with numerous functions such as weather detection, ground communication, sat com, jammer pods, target acquisition, fire control, ground imagery, and altitude monitoring, etc.
Trend Towards Higher Frequencies
Progressively, antenna systems are multifunctional, operating “broadband” over numerous different frequencies, with a trend towards the higher frequency bands. Not only are the lower frequency bands just filling up, but operating at a higher frequency (for example Ka instead of Ku band for Wi-Fi) permits high-speed transmission of “big data”. Streaming video onboard planes will be more achievable with Ka band communications.
The increasing advancement of antenna systems drives complexity in the radome design, requiring “B-Sandwich” and “C-Sandwich” constructions for Wi-Fi radomes, demanding higher performance advanced composite materials, such as epoxy/quartz, or cyanate ester/quartz, in place of E-glass/ epoxy.
Toray’s cyanate ester and epoxy-based prepregs, adhesives and syntactic foams, RTM resin systems, feature low density, low dielectric loss tangent, low moisture absorption, low dielectric constant, and low coefficient of thermal expansion.
.jpg)
Image Credit: Toray Advanced Composites
.jpg)
Understanding Dielectric Constant and Loss
Signal fade or “loss” occurs either by the reflection of the signal from the surface of the composite or via absorption by heating of the matrix.
The dielectric constant (Dk) offers an idea of the reflective properties, as well as the refractive properties of a material. Simplistically, the signal can be thought of as “slowing down” as it moves through the composite (compared with air). If the signal hits a surface at an angle, it will be deflected; this is labeled “boresight error” or “beam deflection”.
Dielectric constant and loss together specify the transmission efficiency of a radome antenna system and are ideally measured at the intended operating frequencies. The lower the dielectric constant and loss, the lower-powered the antenna systems have to be, and the smaller the effect of the radome on the antenna performance. Toray Advanced Composites has a wide-ranging database of materials tested over numerous different frequencies, to help improve the radome design. This data is fed to computer-aided electromagnetic modeling packages and is the main factor in the performance of the radome antenna system.
|
BEST PERFORMANCE |
|
BEST COST |
Cyanate Ester / Quartz Fabric |
Low Dielectric Epoxy / Quartz Fabric |
Low Dielectric Epoxy / Glass Fabric |
Electrical Performance |
BEST
Dielectric Constant 3.2 to 3.35
Loss Tangent 0.001 to 0.009 |
BETTER
Dielectric Constant 3.4 to 3.8
Loss Tangent 0.009 to 0.011 |
GOOD
Dielectric Constant 4.5 and above
Loss Tangent 0.011 and above |
Laminate Impact Strength |
VERY GOOD |
VERY GOOD |
MODERATE |
Laminate Moisture Absorption |
LOWEST 0.1 - 0.6% |
VERY LOW 0.6 - 0.8% |
MODERATE 1.2 - 1.6% |
.jpg)
Toray Composite Laminate Performance over C/X, Ku/K, Ka, and Q/U Bands
Laminate performance over different band frequencies |
Frequency |
C/X Band: 4-8 GHz |
X Band: 8-12 GHz |
Ku/K Band: 12-26.5 GHz |
Ka Band: 26.5-40 GHz |
Q & U Band: 40-60 GHz |
Product Name1 |
Resin Type |
Reinforcement |
Open Resonator3 |
Open Resonator3 |
Focus Beam method |
Open Resonator3 |
Focus Beam method |
Open Resonator3 |
Focus Beam method |
Focus Beam method |
Dk |
DF |
Dk |
DF |
Dk |
DF |
Dk |
DF |
Dk |
DF |
Dk |
DF |
Dk |
DF |
Dk |
DF |
BTCy-2 |
Cyanate Ester |
4581 quartz |
N/A |
N/A |
N/A |
N/A |
3.17 |
0.010 |
N/A |
N/A |
3.13 |
<0.012 |
N/A |
N/A |
3.14 |
<0.012 |
3.12 |
<0.012 |
BTCy-1A |
Cyanate Ester |
4581 quartz |
3.26 |
0.004 |
3.27 |
0.004 |
3.23 |
0.013 |
3.23 |
0.004 |
3.18 |
<0.012 |
3.24 |
0.004 |
3.19 |
<0.012 |
3.18 |
<0.012 |
EX-1515 |
Cyanate Ester |
4581 quartz |
3.24 |
0.005 |
3.24 |
0.005 |
N/A |
N/A |
3.21 |
0.005 |
N/A |
N/A |
3.19 |
0.005 |
N/A |
N/A |
N/A |
N/A |
EX-1522 |
Epoxy |
4581 quartz |
3.35 |
0.005 |
3.34 |
0.005 |
3.35 |
0.011 |
3.32 |
0.005 |
3.31 |
0.011 |
3.32 |
0.005 |
3.31 |
<0.012 |
3.31 |
<0.012 |
TC250 |
Epoxy |
4581 quartz |
3.45 |
0.013 |
3.45 |
0.013 |
3.47 |
0.015 |
3.43 |
0.012 |
3.43 |
0.015 |
3.40 |
0.012 |
3.42 |
0.011 |
3.40 |
0.012 |
BT250E-1 |
Epoxy |
7781 E-glass |
4.61 |
0.014 |
4.57 |
0.015 |
4.52 |
0.019 |
4.47 |
0.016 |
4.48 |
0.018 |
4.50 |
0.020 |
4.45 |
0.017 |
4.42 |
0.016 |
EX-1522 |
Epoxy |
7781 E-glass |
4.68 |
0.009 |
4.69 |
0.010 |
4.72 |
0.012 |
4.65 |
0.011 |
4.67 |
0.013 |
4.63 |
0.013 |
4.66 |
0.010 |
4.64 |
0.011 |
TC250 |
Epoxy |
7781 E-glass |
4.83 |
0.016 |
4.82 |
0.016 |
4.73 |
0.026 |
4.78 |
0.016 |
4.63 |
0.023 |
4.73 |
0.017 |
4.64 |
0.016 |
4.59 |
0.019 |
1. In order of laminate Dielectric Constant for X Band using Focus Beam Method.
2. Focused Beam loss tangent results are not precise < 0.010 DF. These materials represent Toray’s best candidates for high energy radome applications.
3. Open Resonator results using ASTM D2520 Method C.
Dk - Dielectric Constant
DF - Loss Tangent
Adhesives and Syntactics
|
Resin Type |
Dry Tg Onset (DMTA) |
Cure Time and Temperature |
Material at 10 GHz |
OOA / VBO |
Toughened |
Dielectric Constant (Dk) |
Loss Tangent (DF) |
SYNTACTIC FILMS |
SF-5 |
Cyanate Ester |
193 °C (380 °F) or 254°C (490°F) with post cure |
2 hours at 120°C (350°F) Optional post cure of 2 hours at 232°C (450°F) |
1.704 |
0.004 |
|
|
TCF4045 |
Epoxy |
180 °C (356 °F) |
3 hours at 179 °C (355 °F) |
1.57 |
0.008 |
ο |
|
TCF4035 |
Epoxy |
140 °C (284 °F) |
3 hours at 130 °C (265 °F) |
1.94 |
0.018 |
ο |
|
TCF4050 |
Cyanate Ester |
176 °C (349 °F) or 232 °C (450 °F) with post cure |
2 hours at 177 °C (350 °F) Optional post cure of 60-90 minutes at 232 °C (450 °F) |
N/A |
N/A |
ο |
|
FILM ADHESIVES |
EX-1516 |
Cyanate Ester |
126 °C (258 °F) |
5 hours at 121 °C (250 °F) |
2.6 - 2.7 |
0.005 - 0.006 |
ο |
ο |
EX-1543 |
Cyanate Ester |
207 °C (405 °F) |
2 hours at 177 °C (350 °F) Optional post cure of 2 hours at 204 °C (400 °F) |
2.72 |
0.009 |
ο |
ο |
TC263 |
Epoxy |
110-115 °C (230-239 °F) |
2 hours at 121 °C (250 °F) |
2.97 |
0.017 |
ο |
ο |
TC310 |
Epoxy |
157 °C (315 °F) |
2 hours at 177 °C (350 °F) |
3.06 |
0.013 |
ο |
ο |
RS-4A |
Cyanate Ester |
203 °C (397 °F) |
2 hours at 177 °C (350 °F) |
N/A |
N/A |
ο |
ο |
TC4015 |
Cyanate Ester |
176 °C (349 °F) or 321 °C (610 °F) with post cure |
2 hours at 177 °C (350 °F) Optional post cure for >60 minutes at 232 °C (450 °F) |
N/A |
N/A |
ο |
ο |
SYNTACTIC PASTES |
EX-1541 |
Cyanate Ester |
227 °C (441 °F) or 240 °C (464 °F) with post cure |
2 hours at 177 °C (350 °F) Optional post cure of 2 hours at 232 °C (450 °F) |
1.32 |
0.009 |
|
|
TCF4001 |
Cyanate Ester |
176 °C (349 °F) |
2 hours at 177 °C (350 °F) Optional post cure of 60-90 minutes at 232 °C (450 °F) |
1.55 |
0.012 |
ο |
|
4. SF-5 tested at 18 GHz
Common Prepreg Reinforcements
|
Dk (10 GHz) |
DF (10 GHz) |
Sp. gravity (g/cc) |
Moisture pickup (% by Wt.) |
Service temp. |
E-glass |
6.10 |
0.004 |
2.55 |
nil |
371 ºC
(700ºF) |
S-glass |
5.21 |
0.006 |
2.49 |
nil |
398 ºC
(750 ºF) |
Quartz |
3.78 |
0.0002 |
2.20 |
nil |
>537 ºC
(>1000 ºF) |
HDPE |
2.00 |
0.0004 |
0.97 |
nil |
104 ºC
(220 ºF) |
LMR Kevlar® 495 |
3.85 |
0.008 |
1.47 |
1.9% |
176 ºC
(350 ºF) |
5. LMR Kevlar® 49 is a Toray's proprietary Low Moisture Regain treatment of the aramid fabric from E.I. de Pont de Nemours and Company.
Resin System Performance
|
Resin type |
Dk (10 GHz) |
DF (10 GHz) |
BTCy-2 |
Cyanate Ester |
2.70 |
0.001 |
BTCy-1A |
Cyanate Ester |
2.70 |
0.003 |
EX-1515 |
Cyanate Ester |
2.79 |
0.004 |
EX-1522 |
Epoxy |
2.71 |
0.007 |
RS-8HT |
BMI |
3.01 |
0.0074 |
RS-3C |
Cyanate Ester |
2.816 |
0.0096 |
TC420 |
Cyanate Ester |
3.11 |
0.016 |
BT250E-1 |
Epoxy |
3.00 |
0.017 |
TC250 |
Epoxy |
3.00 - 3.06 |
0.020 - 0.021 |
Block wave results using test ASTM D 2520 Method A
6. Sample tested at 10.7 GHz using Open Resonator test ASTM D 2520 Method C
Manufacturing Facilities
Toray's operates positively pressurized enclosed rooms housing the carbon-free machines and equipment devoted solely to the manufacture of radome prepregs and complementary products.
The carbon-free facilities do not run carbon fiber prepregs and are isolated from conductive materials, thus assuring outstanding quality and electrically pure products. Even a tiny carbon fiber contaminate in a radome will heat up in reaction to an electromagnetic signal, and can deform the matrix around it.
Toray Advanced Composite materials from the carbon-free lines are used in antennas, sonar domes, reflectors, components with embedded de-icing elements, conformal radomes, microwave transparent, and radar absorbing structures. Popular reinforcements such as S2 glass, quartz, E-glass, and aramid are totally compatible with Toray's advanced resin systems and can be provided as prepregs to satisfy the most challenging mechanical, electrical and high-temperature applications.
.jpg)
Technologically Advanced Triband Satcom Radome
The General Dynamics LiveTV radome is a technologically progressive composite Satcom radome. Engineered to convey data across three bandwidths (K, Ka, and Ku), the radome realizes improved levels of speed and connectivity for two-way communications and inflight Wi-Fi.
Toray Advanced Composites worked along with General Dynamics, the radome designer, and manufacturer, in delivering a material solution that would permit the enclosed antennas to communicate and receive radio frequency signals across a wider range of bandwidths. Other design considerations included longevity, reliability in signal transmission across all parts, and cost-effectiveness.
The Toray TC250 is an epoxy-based thermoset prepreg that offers an exceptional balance of toughness, mechanical property translation, low dielectrics, and hot/wet performance. Incorporated with a quartz fabric, this advanced composite material solution offered superior mechanical performance while preserving cost-effectiveness.
.jpg)
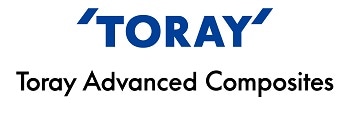
This information has been sourced, reviewed and adapted from materials provided by Toray Advanced Composites.
For more information on this source, please visit Toray Advanced Composites.