With more than two decades of experience, Toray Advanced Composites, USA, a key manufacturer of “out-of-autoclave” advanced composites, is a recognized name among major companies in the aerospace industry, including Lockheed Martin, Gulfstream, General Atomics and Cirrus Aircraft.
.jpg)
Image 1. Cirrus’s SR-22 (pictured above), an industry favorite, uses Toray’s out-of-autoclave composites for both the fuselage and wing structure.
Toray produces different vacuum cure only (VCO) capable prepreg systems, which include BMIs, cyanate ester, and epoxy, for high-temperature applications. The company supplies a suite of products to meet a user’s demand for mechanical and handling performance.
Out-of-Autoclave Composites
out-of-autoclave composites are ideal substitutes for traditional composites, offering several advantages to composite part fabricators as follows:
- Low void content
- Quality and durability as good as that of a part cured in an autoclave under high pressure
- Allowing the use of lower-cost tooling as many systems consider free standing post-cures
.jpg)
Image 2. Toray’s vacuum processible epoxy prepregs systems are used extensively by General Atomics Aeronautical Systems on all of its unmanned aerial vehicle systems.
Toray has been recognized as a leader by its customers in the advancement and production of out-of-autoclave prepreg systems in applications ranging from general aviation to unmanned aircraft systems, launch vehicles and satellites. The company’s products have been assessed on several intermediate, standard, and high modulus fibers in addition to quartz and glass-based materials. With different varieties of peel plies, surfacing films, complimentary adhesives and resins, the company has a wide range of systems that can meet a customer’s requirement.
.jpg)
Image 3. Lockheed Martin Denver selected Toray prepregs, adhesives, and syntactic to deliver a high temperature resistant 21-foot diameter heat shield on the Orion crew vehicle, replacing a titanium heat shield for both weight and cost savings.
Product Name |
Resin Type |
Tg |
Cure Temp/ Time |
Description |
Key Resin Characteristics |
Prepregs |
|
BT250E-1 |
Epoxy |
257°F/125°C |
60 minutes at 250°F/121°C |
Good moderate service prepreg
Self-adhesive to core
Good toughness with high modulus
MIL-R-9300 qualified |
30-day shelf life at 77°F/25°C 2.0% moisture absorption after 24-hour water boil |
BT250E-6 |
Epoxy |
268°F/131°C |
120 minutes at 260°F/127°C |
High modulus resin with good fatigue resistance
Optimized for rotor blade usage
NCAMP data sets |
30-day shelf life at 77°F/25°C |
TC250 |
Epoxy |
284°F/140°C or 347°F/190°C with post cure |
60 minutes at 190°F/88°C, followed by 120 minutes at 265°F/130°C.
Optional post cure of 60 minutes at 350°F/177°C for higher Tg |
250°F/121°C service prepreg
Designed for vacuum bag cure or autoclave
Good surfacing qualities
Good toughness
Self adhesive to core capability
Post curable |
Gel time: 6-10 minutes at 265°F/135°C
30-day shelf life at 77°F/25°C Hot/Wet Tg 257°F/125°C |
TC275 New |
Epoxy |
350°F/177°C |
120 minutes at 350°F/177°C |
Designed for very low voids <0.5% in thick parts without of autoclave vacuum cures
Maybe cured at 275°F/135°C |
Very low moisture uptake
High hot/wet Tg retention |
TC350-1 New |
Epoxy |
376°F/191°C |
120 minutes at 350°F/177°C |
Toray latest 350°F/177°C service prepreg
Toughened high temperature prepreg
Low moisture absorption
Good hot wet/performance
Ideal for autoclave or press cure |
Gel time: 10-12 minutes at 350°F/177°C
Hot/Wet Tg 320°F/160°C |
TC420 |
Cyanate Ester |
350°F/177°C or 610°F/321°C with post cure |
3 hours at 350°F/177°C
Optional post cure at 500°F/260°C |
Very high temperature service
Good resistance to microcracking
Out of autoclave processible |
Ultra high temperature performance |
BMI New |
BMI |
458°F/236°C after 450°F/232°C with post cure |
Call for details |
High temperature
Low void content |
NEW |
Other |
|
TC235-1SF |
Epoxy |
246°F/119°C cured at 250°F/121°C |
60 minutes at either 250°F/121°C or 350°F/177°C |
Excellent surfacing characteristics under vacuum cure
Excellent coverage even with tight radius curved parts
Passes Scribe Test (Initial and after 24 hours before tape removal) |
Gel time: 6-15 minutes at 250°F/121°C One year shelf life a <0°F/-18°C |
Adhesives/ Syntactcs |
Epoxy |
Various |
See website for details |
Compatible
Low viscosity |
Various |
Meeting the Challenge
The lower the laminate void content, the higher the ability of a prepreg system to yield high mechanical strength consistently. Toray prepreg systems are rigorously tested both mechanically and under non-destructive inspection (NDI) conditions to ensure their robust performance in vacuum only processing.
As part of Toray’s development of TC275 and TC350-1, the company fabricated large thick parts and analyzed void contents throughout the part. Picture 4 demonstrated low voids in all sections of the spar.
.jpg)
Figure 1. As part of Toray’s development of TC275 and TC350-1, we fabricated large thick parts and evaluated void contents throughout the part. This analysis demonstrated low avoids in all section of the spar.
Featured Products
TC275
TC275 is a toughened epoxy prepreg specially engineered for out-of-autoclave low cure pressure part production. It is a suitable material for fabricating thick (100+ plies) parts thanks to the ability to provide very low levels of porosity. As TC275 is capable of developing full properties without a post cure, the material can meet the challenges posed by aerospace environments and loads.
.jpg)
Figure 2. TC275demonstrates superior retention of mechanical strength under elevated and hot/wet conditioning, making it a suitable material for applications wherein these conditions are especially common (ETD: 82 °C; ETW: 82 °C.)
Advantages of TC275 are as follows
- Capable of providing below 0.5% porosity in thick parts
- Optimal cure: 135 °C for 5-6 hours
- No post cure required for full properties
- Superior hot/wet strength retention
- 7 day tack life/14 day tool life
- Easily inspectable through NDI methods
TC350-1
TC350-1 is a toughened matrice specially designed for out-of-autoclave processing for use in structural applications. With a combination of hot/wet performance, mechanical property translation and toughness, TC350-1 demonstrates the strength of an autoclave processed material with the benefits of out-of-autoclave fabrication.
.jpg)
Figure 3. TC350-1 not only retains autoclave properties but time and again exceeds them, thus delivering a strong material that eliminates the cost and complexity of autoclave processing.
Benefits of TC350-1 are as follows
- Low porosity
- 21 day tack life/45 day tool life
- Pre-screened to NCAMP database protocol
- Superior compression after impact strength
- 3 hr. 135-149 °C cure, followed by required 2 hr. 177 °C free-standing post cure
TC275 and TC350-1 Handling and Mechanical Property Summary
Property |
TC275 |
TC350-1 |
Cure Temperature |
275°F (135°C) |
275°-300°F (135°-149°C)
350°F (177°C) post cure |
Cure Time |
5-6 hours |
3 hours
2 hour required free-standing post cure |
Freezer Life |
6 months |
1 year |
Outtime - Tack |
7 days |
21 days |
Outtime - Tool |
14 days |
60 days |
.jpg)
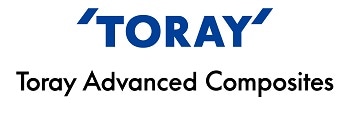
This information has been sourced, reviewed and adapted from materials provided by Toray Advanced Composites.
For more information on this source, please visit Toray Advanced Composites.