Although torch brazing is the most widely used brazing method, finding a skilled operator for the process is a difficult task for many manufacturers. Moreover, it elevates regulatory and safety concerns in production facilities due to the open flame. Furnace brazing is also a common form of brazing.
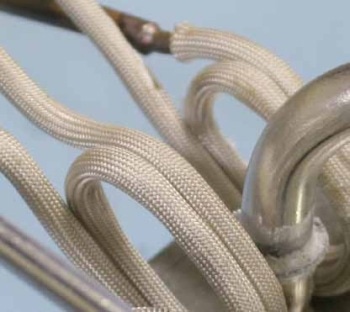
Replacing torch brazing with induction for an aluminum manifold application.
Nowadays, manufacturing companies are finding ways for production efficiency improvement, production cost reduction, and replacement of energy and space inefficient furnaces without comprising product quality. Induction brazing is the answer to the aforementioned issues as it eliminates the need for a skilled operator, reduces the equipment footprint, minimizes energy costs, and implements a lean production process for higher quality parts.
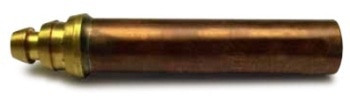
Induction brazing a brass mixing nozzle onto a twin feed copper tube for an oxyacetylene torch nozzle assembly. 6 kW at 380 kHz for 36 seconds to 732°C (1350°F).
Induction Brazing – Process
Induction brazing is utilized for a myriad of applications in the joining of a variety of metals including copper-to-aluminum, aluminum-to-aluminum, copper-to-copper, brass-to-copper, brass-to-copper, steel-to-copper, steel-to-brass and steel-to-steel.
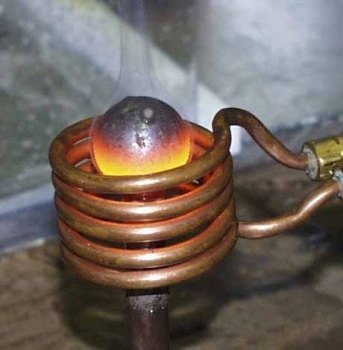
Steel-to-steel brazing of part of a regulator used in the oil industry. 200kHz at 8kW for 9 seconds to 732°C (1350°F).
Steps followed in a quality induction brazed joint include:
- The joint is designed correctly to allow for a clearance of 40–125 µm between the two surfaces at the flow temperature of the braze material to enable capillary action and joint wetting.
- The surfaces of the joint materials must be cleaned.
- Flux is then applied to both pieces.
- A pre-form or braze ring is used to clasp the two pieces together in the coil
- The two pieces are then heated to the braze material flow temperature. The braze material is stick-fed to the joint in the absence of pre-forms.
- The brazed joint is then cleaned for the removal of all of the flux residue.
Tensile Strength with Joint Clearance
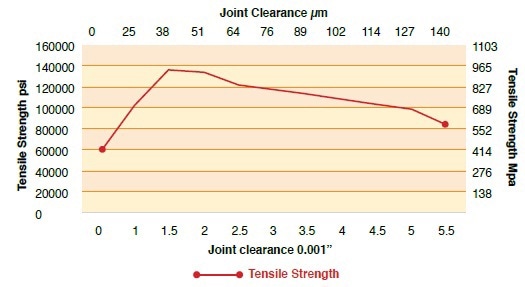
The optimum braze joint strength occurs with a part joint clearance between 25μm (0.001") and 125μm (0.005"). Data from Lucas Milhaupt.
The braze filler material is used to deliver a metallurgical bond to the material surface on either sides of the joint. Typical braze filler materials utilized for forming the required alloys for the joint materials include aluminum, nickel, zinc, silver and copper. Some filler material alloys demonstrate eutectic properties, which support the brazing process by allowing the alloy to melt and flow at a temperature lower than the base materials’ melt temperature as shown in figure 5.
Eutectic Properties
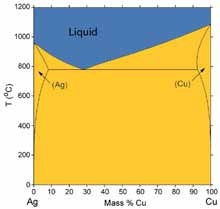
Fluxes are used for protecting the two metal surfaces being joined as well as the braze material from oxidation in the heating process. Some flux materials can also serve as cleaning agents. A potassium salt of fluorine and boron having a temperature range of 565–982 °C is a typical flux material utilized for lower temperature brazing. Flux materials with less fluorine are used for higher braze temperatures of 870–1100 °C.
Brazing Materials Temperature Spectrum
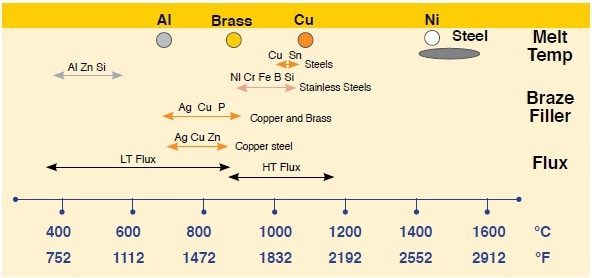
Filler and flux operating temperature ranges for typical materials used in brazing steel, copper, brass and aluminum.
Advantages
Benefits of induction brazing technique include:
- Better quality with minimal part distortion
- Better efficiency
- Throughput: Heat is generated solely in the portion of the part required for brazing
- Easy integration into a lean production process
- Smaller footprint: Frees up valuable factory floor space
- Safety: No hot furnace or open flame
- Repeatability: It is possible to achieve a precise, constant quality braze once the coil and heating processes are defined.
Applications
Aluminum Brazing Applications
Heating aluminum using induction requires a high amount of energy as aluminum’s thermal conductivity is 60% when compared to that of copper. Time for the heat to flow and coil design are crucial for brazing aluminum parts using induction. Flame and furnace heating have been successfully replaced by induction in high volume brazing of aluminum assemblies thanks to the recent developments in lower temperature aluminum braze materials. Ambrell provides solutions for precision aluminum brazing applications.
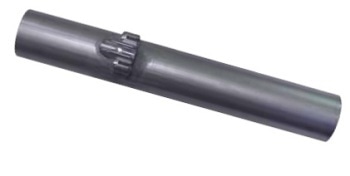
Brazing an aluminum cable fitting onto an aluminum tube for bicycle manufacturing. 20kW at 10kHz for 45 seconds to 482°C (900°F) using stick fed braze. Two parts were brazed simultaneously in a two position coil.
Steel Brazing Applications
Induction brazing is the suitable process for joining steel components where welding cannot be used. A well-designed induction brazed steel joint offers several advantages including lower part stress and part geometry integrity.
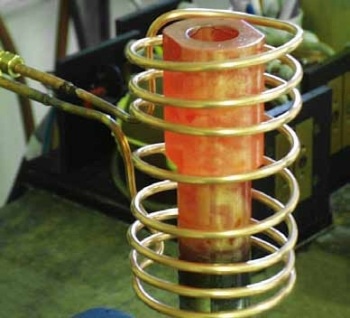
Carbon and stainless steel are induction compatible, heat easily, and have high resistivity. Nonetheless, due to their poor thermal conductivity, the induction brazing of steel components must be performed in a slow pace. For steel, time is required for the heat to travel through the joint surface for wetting out of the braze material and proper flow. Nickel-based alloys are often utilized as stainless steels, while copper-based alloys are utilized as a low-cost braze material on carbon steels. Ambrell’s induction brazing experts have the experience to provide the required solutions for joining dissimilar parts. Thermal conductivity, electrical resistivity and typical melting temperature of different materials are listed in the following table.
Material |
Thermal Conductivity k Cal/cm s ºC |
Electrical Resistivity ρ ohm m x10–8 |
Typical Melting Temp
ºC ºF |
Aluminum |
0.60 |
2.65 |
660 1220 |
Brass |
0.26 |
7.1 |
930 1710 |
Copper |
0.95 |
1.7 |
1084 1983 |
Carbon Steel |
0.11 |
74 |
1480 2700 |
Stainless Steel |
0.05 |
74 |
1510 2750 |
Steel, Copper and Brass Brazing
Induction brazing is an ideal process for joining parts made of dissimilar metals. Applications with mixed metal joining include brass-to-copper, steel-to-brass and steel-to-copper.
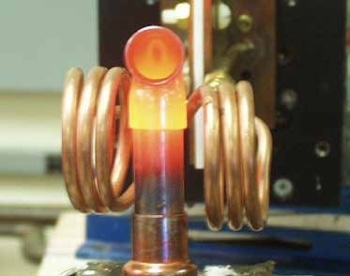
Replacing torch brazing on a copper elbow to copper pipe using a split helix coil. 7kW at 190kHz for 90 seconds to 760°C (1400°F).
For braze joining different metals, both metal surfaces must achieve the braze flow temperature at the same time as the joint. The induction heating solution must consider the materials’ different thermal conductivities and the time taken by the materials to reach the desired temperature.
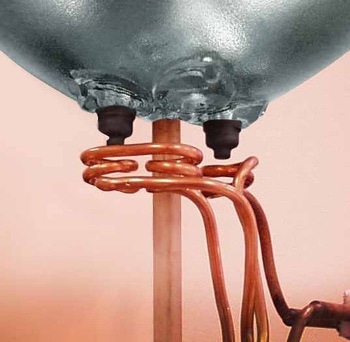
Replacing torch brazing with a multi-position helical coil to induction braze two or three nickel plated steel ferrules to nickel plated pins from an Automobile light bulb. 8kW at 360kHz for 6 seconds to 620°C (1150°F).
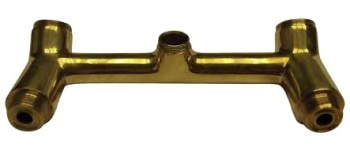
Replacing torch brazing for two brass joints on a faucet manifold. Each joint was induction brazed using a saddle coil. 22kW at 90kHz for 30 seconds to 620°C (1150°F).
Brazing a Steel Tube Assembly
A steel tube assembly is induction brazed for 30 seconds with 3.5 kW at 220 kHz to 732°C. Ambrell’s EASYHEAT 3.5kW power supply is used for brazing various tube assemblies.
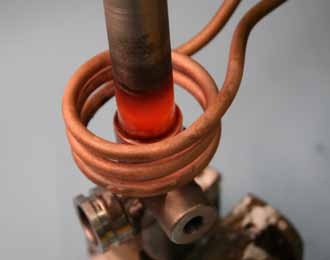
Manifold Assembly Brazing
A two-step induction brazing process is used as a replacement for torch brazing in assembling a manifold for an air conditioner. First step is the use of an elongated coil for brazing the four aluminum tubes into the aluminum manifold for 60 seconds to 566 °C at 3.5 kW and 180 kHz. Then a 3 kW of power is supplied for copper-to-aluminum brazing at 200 kHz for 95 seconds.
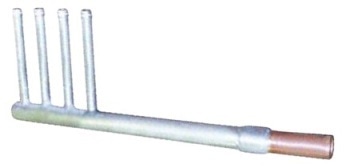
Brazing Stainless Steel-to-Copper Elbows
Copper elbows can be induction brazed on a flexible stainless steel tubing of 102 mm diameter by heating the surface to 675 °C with 10 kW power supply at 128 kHz for 3 minutes. The stainless steel tubing is utilized for enabling plumbing in large buildings to withstand movement in the structure.
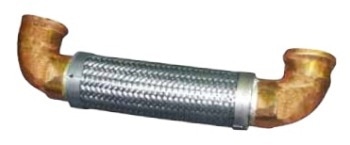
Brazing Stainless Steel-to-Stainless Steel
Using a saddle shaped coil, a single induction brazing process can be employed for brazing the two stainless steel ends of the medical tool shown in the picture below to the stainless steel flange using in 20 seconds with 3 kW at 180 kHz.
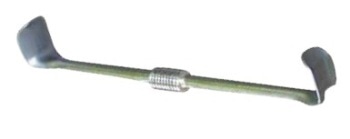
Summary
EASYHEAT 1.2 and 2.4kW are used for brazing small parts, while EASYHEAT 4.2, 6, 9, and 10kW are utilized in a variety of brazing applications that involve small or thin walled parts or brazing of multiple parts at the same time.
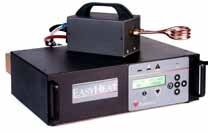
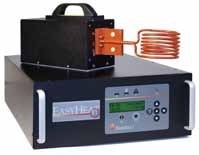
EKOHEAT 10 and 15kW are utilized in different brazing applications that involve more mass parts, while EKOHEAT 30 and 45 and 50kW are utilized in brazing applications that require faster heat up times and involve brazing of larger parts.
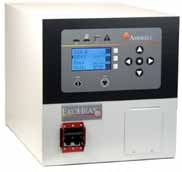
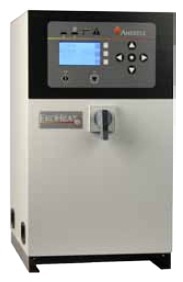
Ambrell offers versatile systems with multiple capacitor and tap transformer configurations. These systems can braze small or large parts or multiple metal materials with optimal productivity and cost efficiency.
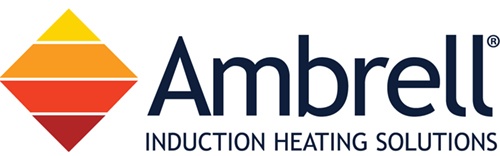
This information has been sourced, reviewed and adapted from materials provided by Ambrell Induction Heating Solutions.
For more information on this source, please visit Ambrell Induction Heating Solutions.