There are several types of hydraulic cements produced with different physical properties by altering the composition of clinker minerals. Hence, it is crucial to control the chemical composition of cement products and interim products. The fusion technique is capable of eliminating sample heterogeneity, such as mineralogical effects and grain size, thus enabling to get high accuracy for cement samples and to build calibration utilizing many different materials. Hence, X-ray fluorescence (XRF) spectrometry by the fusion method is the ideal solution to obtain accurate control in cement production processes.
The standard ASTM C114-11 discusses chemical analysis of hydraulic cements, especially procedures of wet chemical analysis. The standard mentions XRF spectrometry as example of ‘Rapid Test Methods.’ According to ASTM C114-11, NIST certified reference materials (CRMs) or other reference cements traceable to the NIST CRMs are acceptable reference cements.
This article demonstrates the ability of the Supermini200 benchtop sequential wavelength dispersive XRF (WDXRF) spectrometer to quantitatively analyze Portland and aluminate cements using the fusion technique, in accordance with the standard ASTM C114-11. In this analysis, calibration and a qualification test were performed with nine NIST CRMs (SRM1881a, 1882a, 1883a, 1884a, 1885a, 1886a, 1887a, 1888a and 1889a).
Supermini200 Benchtop Sequential WDXRF Spectrometer
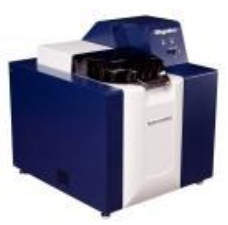
Figure 1. The Supermini200 WDXRF System
The Supermini200 is designed to reduce the requirements for installation, such as installation area, power supply, and cooling water. The system exhibits good sensitivity for light elements, including P, Mg, and Na. Moreover, it does not demonstrate any spectral overlap between typical analytes for cement thanks to the high spectral resolution of the WD optics. In addition, with three analyzing crystals and an air-cooled 200 W X-ray tube, the system can analyze elements from fluorine to uranium. The operation software in the Supermini200 is user-friendly and flexible.
Sample preparation
The wet grinding technique was used to grind the samples in a tungsten carbide container with n-hexane. The ground fine powder samples were then ignited for one hour at 950 °C. Four gram of flux, (lithium tetraborate, pre-dried at 675 °C) and 1 g of the ignited sample were weighed out and mixed for fusion at 1200 °C.
Measurement and Calibration
The Supermini200 with a 200 W Pd target X-ray tube was used to perform measurements in vacuum for the components. The results from the calibration curves are illustrated in Figure 2 and Table 1.
Table 1. Calibration Results
Analyte |
Maximum difference between duplicates |
Maximum difference of the average of duplicates from the certificate values |
SiO2 |
0.16 |
±0.2 |
Al2O3 |
0.20 |
±0.2 |
Fe2O3 |
0.10 |
±0.10 |
CaO |
0.20 |
±0.3 |
MgO |
0.16 |
±0.2 |
Na2O |
0.03 |
±0.05 |
K2O |
0.03 |
±0.05 |
TiO2 |
0.02 |
±0.03 |
P2O5 |
0.03 |
±0.03 |
ZnO |
0.03 |
±0.03 |
Mn2O3 |
0.03 |
±0.03 |
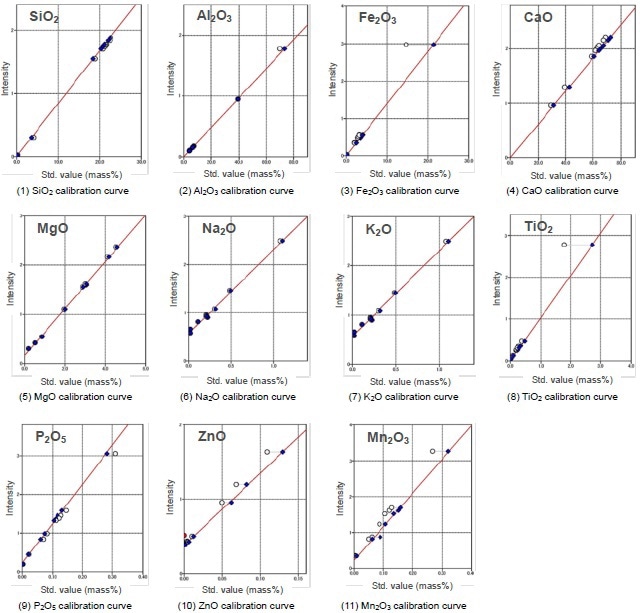
Figure 2. Calibration curves of Portland and Alumina Cements
A matrix correction technique is used to the calibrations. The data points before and after correction are demonstrated in the calibration charts. The following formula is used to calculate the accuracy of calibration:
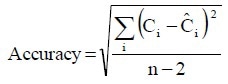
Where,
Ci: calculated value of standard sample
Ci: reference value of standard sample
n: number of standard samples.
Qualification Test for ASTM C114-11
Using the aforementioned calibration curves, the nine NIST SRMs of Portland and alumina cement were quantitatively analyzed. The results from the analyses are shown in Table 2, which compares the values of ASTM C114-11 specifications. The results confirmed that the analysis technique described in this article fulfills the prerequisites outlined in the standard ASTM C114-11.
Table 2. Qualification Test Results
X-ray tube |
Pd target, 200 W end-window type |
Tube condition |
50 kV and 4.0 mA |
Analysis area |
30 mm in diameter |
Path atmosphere |
Vacuum |
Element |
Si |
Al |
Fe |
Ca |
Mg |
Na |
Line |
Kα |
Kα |
Kα |
Kα |
Kα |
Kα |
Primary filter |
Out |
Out |
Out |
Out |
Out |
Out |
Crystal |
PET |
PET |
LiF |
PET |
RX25 |
RX25 |
Detector |
PC |
PC |
SC |
PC |
PC |
PC |
Counting time (s) |
40 |
40 |
20 |
60 |
60 |
60 |
Element |
K |
Ti |
P |
Zn |
Mn |
|
Line |
Kα |
Kα |
Kα |
Kα |
Kα |
|
Primary filter |
Al |
Out |
Out |
Out |
Out |
|
Crystal |
PET |
LiF |
PET |
LiF |
LiF |
|
Detector |
PC |
SC |
PC |
SC |
SC |
|
Counting time (s) |
40 |
20 |
40 |
20 |
20 |
|
Note) LiF: LiF(200), PC: F-PC
Repeatability Test
The duplicated fused beads of NIST SRM1889a were repeatedly measured for 10 times in order to illustrate the precision of the instrument. The repeatability test results are shown in Table 3, demonstrating very good stability. When compared to the values of the limits specified in ASTM C114-11, as shown in Table 2, the standard deviations of the repeatability test are adequately low. The results illustrate the ability of the Supermini200 to fulfill or surpass the precision requirements for hydraulic cement analysis as outlined in ASTM C114-11.
Table 3. Repeatability Test Results
Analyte |
Calibration range |
Accuracy |
SiO2 |
0.24 - 22.38 |
0.058 |
Al2O3 |
3.875 - 70.04 |
0.051 |
Fe2O3 |
0.078 - 14.67 |
0.034 |
CaO |
29.52 - 67.87 |
0.086 |
MgO |
0.19 - 4.475 |
0.050 |
Na2O |
0.021 - 1.068 |
0.024 |
K2O |
0.014 - 1.228 |
0.033 |
TiO2 |
0.020 - 1.786 |
0.005 |
P2O5 |
0.003 - 0.306 |
0.004 |
ZnO |
0.001 - 0.107 |
0.001 |
Mn2O3 |
0.003 - 0.259 |
0.006 |
Conclusion
The test results by the fusion method demonstrate that the Supermini200 is capable of meeting or surpassing the prerequisites for hydraulic cement analysis as mentioned in the standard ASTM C114-11. Using the fusion method and the Supermini200, a single calibration can be established for broad concentration ranges, including both alumina and Portland cements. The precision or stability assessed by the repeatability test is much superior when compared to the defined values specified in ASTM C114-11.

This information has been sourced, reviewed and adapted from materials provided by Rigaku.
For more information on this source, please visit Rigaku.