Rubber to metal bonding is a generic phrase covering a number of interdependent processes. The rubber bonded units that result from the process are used for the isolation of noise and vibration in automotive and engineering applications. Larger units are used to decouple translational movement for bridges and buildings. Twenty years ago the subject was regarded as a ‘black art’. Now the technology allows the production of a uniform, high quality product that is free from failure. Much of the science behind the technology remains cloaked in uncertainty, but it is sure to become an important part of future developments. Today, environmental concerns have an impact on all aspects of commerce. Rubber to metal bonding is no exception, so the process is changing to reflect these concerns. Elements of a Rubber/Metal Bond Three essential elements form the core of the bonding process, the rubber, the bonding agents and the substrate, figure 1. The selection of the polymer base and the associated compound depends mainly on the product specification. Provided that the rubber can flow into the mould without developing a significant level of cross-linking (less than 2%), a bond can be formed using any rubber compound. There are no restrictions on the use of particular compounding ingredients, although it is best to avoid substances that will bleed rapidly to the surface of the uncured stock. The rubber Compounder therefore needs to concentrate attention to matching the physical requirements of the cured rubber and the processing needs of the moulding process. 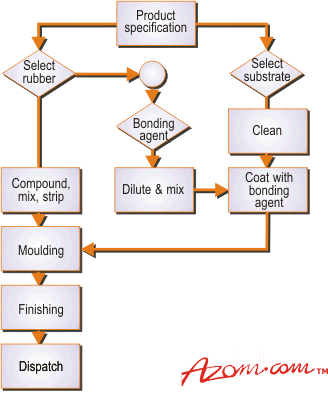 | Figure 1. The rubber bonding process. | The Bonding Layer For the past 40 years the bonding agents have consisted of proprietary polymer/solvent solutions, with a primer coat based on phenolic-style resins and a topcoat formed from solutions of polymers and other ingredients. The formulation of these materials is not disclosed, but much patent literature is available. Bond formation appears to he associated with the development of a very high modulus layer in the rubber immediately adjacent to the surface of the substrate. The thickness of the layer is of the order of 15µm and varies according to the nature of the rubber formulation and the level of an ingredient named as di-nitroso-benzene (DNB) in patents. Selection of Bonding Agents The selection of bonding agents depends on the type of rubber to be bonded, the modulus of the rubber and the component design, figure 2. The selection process is critical to the robustness of the bonding process. In the past decade water-based versions of bonding agents have been introduced, which after much development are now effective replacements for the solvent-based bonding agents. Bonds tend to be up to 10% lower but components show good resistance to the usual environmental conditions found in automotive applications. The application methods for water-based bonding agents are similar to those for the solvent systems, but inserts do need to be preheated to 60-80 °C before spraying with the primer, and reheated before applying the topcoat. Drying times are surprisingly quick and are no barrier to high volume production. 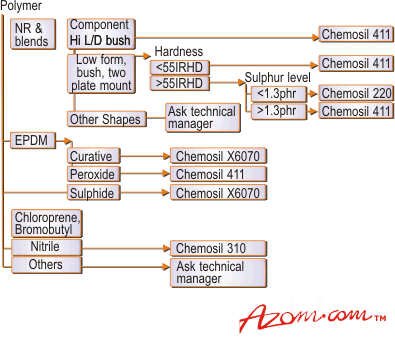 | Figure 2. Decision tree for selection of bonding agents | Choice of Substrate The choice of substrate rests solely with the component designer, who must consider the necessary strength and durability requirements for service use. The traditional substrate is steel, in all its forms and grades, but increasing use is made of aluminium alloys and polyamides to save weight. Almost any material can be bonded to rubber, provided that it can withstand the heat and pressures of the rubber moulding process. For practical purposes this eliminates polyolefin plastics. Polyacetal inserts can be bonded but require careful etching and rubber moulding temperatures below 150°C. PTFE provides a useful low friction material for use in anti-roll bar bushes. It can be bonded successfully to the rubber by chemically etching the surface of the plastic prior to application of the bonding agents. However, its use in such applications has been largely superseded by woven PTFE/Terylene fibre material, which offers a mechanical bond, and, more recently, by slip agents that bond freely to the surface. The Bonding Process Substrate Cleaning The first key step in the preparative process for the inserts is cleaning. To prepare steels, all traces of oil, grease or solid lubricant must be completely removed from the metal surface. A number of process routes are available, figure 3. Of these, degreasing and shot blast are widely employed, although wet blasting followed by a phosphate conversion treatment is gaining greater acceptance as a cost-effective process, and it gives the added benefit of improved corrosion resistance. All emissions from this process can be contained and process media recycled, making it more environmentally friendly. 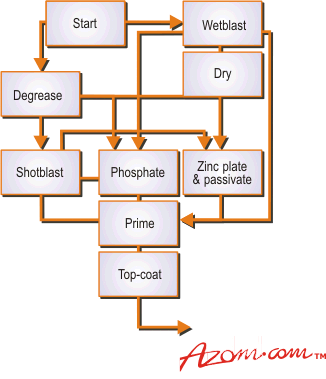 | Figure 3. Preparative process for steel substrates. | Whatever process route is taken, the emphasis has to be on control to ensure consistency of results. Degreaser plants need to be regularly monitored to minimise any build up of contaminants or change in pH. The grade of grit used in shot-blast operations is important and will affect the environmental resistance of the finished product. The profiling of particle sizes is a useful tool to monitor machine effectiveness and ensures that dust levels remain low. Routine sampling will show if fresh grit is being fed to the machine and detect a failure of the dust extraction mechanism. Differences in surface profile due to changes in the size range of the grit will not cause bond failure, but the presence of dust and debris in the grit will. Dust adheres to the newly cleaned metal surfaces and is very difficult to remove, even with a second degreasing operation. Chemical conversion processes have become an important method for preparing steels for bonding. A number of phosphate processes are available, with two characteristics in common. They produce coating weights that are consistent and in the range of 1.5-3.5 g.m-3, and the crystal size does not exceed 5 µm in diameter. If these parameters are maintained, excellent bonds are obtained that will withstand the sizing operations that are applied to rubber bonded bushes. Sizing or swaging of bushes is necessary to put the rubber into compression for optimum resistance to fatigue. Application of Bonding Agents The methods for applying bonding agents are subject to continual review. The process requires the application of a grey primer coat and a black topcoat. In high volume production methods, problems with blocked guns or other mechanistic faults may allow components to be produced without primer below the topcoat. Such parts will initially show a good bond but will be likely to fail in service. Various foolproof means to prevent this happening have been suggested, but are yet to be proven in use. The best method to date is to ensure that the primer is sprayed over a slightly wider area than the topcoat so that a witness to the primer exists. However, this does not work for inserts that need to be bonded over 100% of their surface! As for solvent systems, a barrel spraying machine may be used for parts that need to be coated on all surfaces, figure 4. Use of video or computer systems to monitor and control spray systems is another possibility but to date such systems have proved unreliable due to their inability to distinguish accurately between shades of grey. 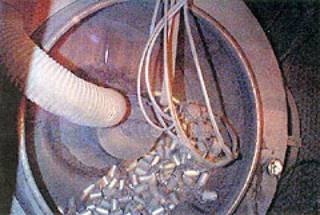 | Figure 4. Barrel spraying of inserts with bonding agent primer.. | The Environmental Protection Act has prompted manufacturers to find means of reducing or eliminating the volume of solvent used in cleaning and coating processes. The introduction of low pressure, high volume (LPHV) spray guns reduced the volume of bonding agent used by 20%. Provided the materials of gun construction are compatible, i.e. stainless steel or plastic, these same guns can be used with water-based bonding agents, albeit with significantly smaller nozzles. The spray pattern thus achieved with water-based materials allows a greater volume of the spray to be directed at the insert, resulting in reduced losses through overspray. Rubber Moulding The rubber moulding operation brings together all the elements of the process. It is the most critical point in the process. If one element in the production cycle for the inserts and bonding agent is wrong, then the product is destined to fail. For automotive production the preferred method of moulding is by injection. This allows the greatest control over the process, allowing the condition of the rubber as it enters the cavity to be tailored to the most robust for product quality. Mould Design Moulds do need to be designed to ensure exact balance between cavities and the elimination of trapped gases. The presence of gases causes a high incidence of bond failures through the ‘diesel effect’, whereby elements of the bonding agent film burn under the combined effects of heat and high-pressure gas. Lack of balance between cavities will result in some components that are imperfectly formed and give rise to bonds that may fail. Problems such as these are readily avoided by study of the rubber flow through the mould using computer flow simulation packages. These model the effect of mould design on pressure gradients and the cross-linking behaviour of the rubber. Factorially designed experiments, using the computer model, allow the optimisation of runner sizes and moulding conditions before the mould is manufactured, so that components are produced to specification when the mould is first used. Plated Inserts The use of plated inserts is popular with some designers. Good bonds can be obtained with plated inserts, but some problems can arise in service if the bond edge is subjected to frequent exposure to electrolytes. Salt solution from roads will produce ‘battery’ cells between the plated metal and the carbon black in the rubber. Up to 0.8 V has been measured under salt spray test conditions. The production of nascent hydrogen at the electrode surface causes a localised debonding process, known as cathodic dis-bondment, that will cause eventual failure. Applications Motor Vehicles Motor vehicles use a large number of rubber components, many of which are bonded. To the casual observer they remain hidden by the glossy shell. The engine and gearbox units are mounted on a rubber bonded unit that may incorporate hydraulic damping systems to damp out engine noise and virbration more perfectly over a wide spectrum of frequencies. The strut units mount the wheels to the vehicle chassis via a shear style rubber bonded bush. Sub-frames need to be coupled by stiff mounts that allow some flexibility. The steering wheel is joined to the steering rack by bonded components and the various link arms in the suspension and steering all incorporate bonded bushes. They act together to provide the comfort and road handling characteristics that are demanded in the modern motor vehicle. Bonded units are also used to correct harmonic vibrations that are sometimes found in the chassis of the lighter, less rigid bodies. Using a rubber bonded mass, called a harmonic damper, that is connected to a vibration node allows the damping of these vibrations. Summary Improvements in comfort and safety arise from a continual process of interaction between innovative designers and technologists. The process embraces the best practices from all the branches of the materials science and technology, bound together by quality. |