Some industrial and research applications require dilution of explosive gases at high concentrations. In most cases, this is in order to calibrate gas detectors. To match these unique requirements, Environics developed a modified version of its Series 4040 gas dilution system which included a twin chassis design.
The electronics enclosure comprises of the power supply and PC boards for controlling the Mass Flow Controllers (MFC) and direct acting solenoid valves in the second enclosure. The electronics enclosure connects to a computer through a 9-pin serial port connector and cable. The 4040 software, on the computer, communicates with the microcomputer board within the electronics enclosure.
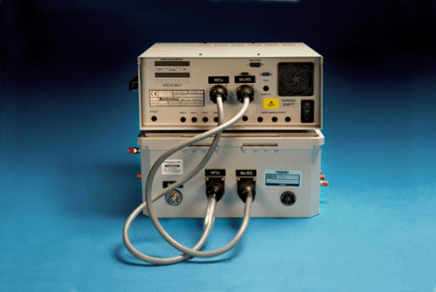
Image Credit: Environics
The second enclosure is sealed and houses the valves, MFCs and components to support the enclosure purge. A continuous purge flows through the enclosure while it is operating. This serves dual purposes. The first is to carry out heat build up by the internal components. The second is to dilute any potential leaks that may occur. The gas plumbing within this enclosure was vacuum leak tested to 1X10-8 ATM CC/SEC He.
Besides continuous purge flow, the enclosure is pressurized to approximately 5” H20 while operating the enclosure purge. This provides an indicator that the purge is stimulated as well as preventing any air leaks into the enclosure from outside. A safety vent was incorporated to vent the enclosure to atmosphere if the pressure within the enclosure touches 20” H20. This could occur if for some reason the purge vent becomes obstructed or the pressure on the purge rotameter is very high.
The two enclosures are connected electrically through two control cables labeled VALVES and MFCs. An earth ground wire is connected from the electronics chassis to the aluminum mounting plate within the purged enclosure. This safely releases any static electricity that can build up in a system with flow.