The Tschudin™ T35 from Hardinge is a modular cylindrical grinding machine specifically designed for production, fulfilling the most diverse application requirements when producing medium and large series.
The Tschudin™ T35 production machine features hydrostatic guides and a wider application range, varying from small integrated handling to complicated systems with independent cells. The machine provides prism and rod grinding, synchronous processing, and integrated additional operations. Distance between the centers of workpieces is 400 mm, the centers are a height of 175 mm and the workpieces weigh 150 kg.
Technical Data
Source: Hardinge Inc.
|
Tschudin T35 |
Dimensions |
|
Distance between centers |
400 mm |
Grinding length |
400 mm |
Center height |
125/175 mm |
Max. workpiece diameter |
249 mm |
Workpiece weight |
|
Between centers |
150 kg |
Base/Table slide |
|
Travel Z-Axis |
600 mm |
Rapid Traverse |
15 m/min |
Resolution |
0.1 µm |
Wheelhead OD |
|
Wheel (appl. spez.) |
400 - 500 mm x 80 mm x 203.2 mm |
Diameter |
up to 600 mm |
Width |
up to 120 mm |
opt |
500 mm x 120 mm x 203.2 mm |
Peripheral roller bearing |
0-120 m/s |
Peripheral hydrodynamic |
45/60 m/s |
Spindle speed |
V const (opt) min-1 |
Motor output |
10 kW (opt. up to 20) |
Workhead |
|
Spindle speed |
5 - 1,500 min-1 (opt. 3,000) |
Motor output |
2.1 kW |
Spindle nose taper |
MT5 / Ø 70 mm // MT6 / Ø 90 mm |
Spindle nose bore |
34 mm |
Spindle torque |
20 Nm |
Tailstock |
|
Sleeve retraction |
80 mm |
Internal taper |
MT3 |
Control |
Bosch / Siemens |
All data is subject to change without notice
Features
- Axes configuration available
- Angular or straight
- Burr-free grinding is possible
- Prismatic grinding system
- Range can be configured from +6° to −30°
- Sharper and burr-free edges can be achieved
- Various patented processes can be performed
- Match grinding
- Highly efficient production grinding process
- Automatic cylindrical correction can be done within the range of 0.1 μm
- Brief part changing time and quick retooling
- Hydrostatics comes with holding device X and Z guideways
- Completely integrated handling with modular peripherals and higher autonomy
- Highly precise automatic process with various extension possibilities
- Users can finish-grind high-precision parts directly from hardened bar stock
- No stick slip
- Good damping
- Wheel head
- High dynamics
- Dressing device
- Hydrodynamic spindle bearings
- Roller bearing variant for applications ranging up to 120 m/second. Grinding wheels range from 400 to 600 mm
- TailstockIn manual or automatic versions available
- Comes with workhead MT5 and MT6 versions in modular construction
- Version available for automatic taper correction
- CNC controlled profiling roll unit equipped behind the wheelhead
- Concurrently running workheads left and right for unique grinding applications
- Formed dressing roll unit fitted on the table or behind workhead or tailstock
Controls
- Siemens 840D SL: 19″ TFT LCD display with novel capacitive sensor technology—programmable resolution
- 0.0001″/0.001 mm: Inch/metric data selection by G-Code–MDI (Manual Data Input) Operation – ShopMill – 3D Simulation – SINUMERIK
Operation
- Simple tool management
- Animated element operation
- Advanced surface
- MDynamics
- CYCLE800
- Measurement cycles
- FTP
- Transmit and peripheral surface transformation
- Ethernet interface (Data transfer capability)
- Part program storage/data input/output on:
- USB 2.0
- Network drive
- 10 MB CNC memory
- 6 GB internal Compact Flash
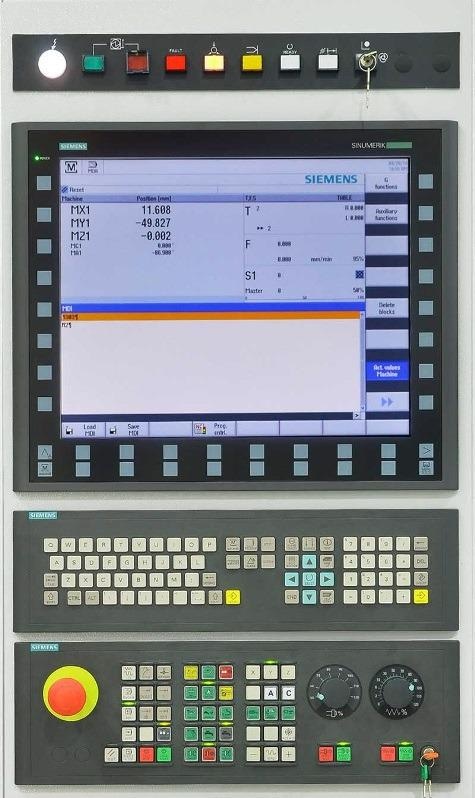
Image Credit: Hardinge Inc.