The Pilot Plants simulate industrial processes at a laboratory scale for product development, quality improvement, and process innovation.
- Conduct laboratory-scale simulations of industrial processes to facilitate product development, enhance quality, and drive process innovation.
- Proficiency in instrumentation and control guarantees reliable and reproducible outcomes within intricate systems.
Description
Enhancing competitiveness in the industry is prominently achieved through the creation of new products boasting high-quality features and significant added value. To pursue novel product developments, enhance existing product quality, and devise new processes, it is crucial to employ continuous and automated pilot plants capable of simulating industrial processes at the laboratory level with practical scalability.
Given the intricate nature of these systems, characterized by a high degree of complexity and numerous operating variables with interconnected relationships, a thorough examination of instrumentation and control becomes imperative. This ensures the attainment of representative and reproducible results from these systems.
Gasification/Pyrolysis
In response to the revived enthusiasm for innovative methods to transform current fuel reserves using advanced technologies like gasification and pyrolysis, PID Eng&Tech has partnered with influential researchers in the biofuels domain.
The collaborative effort aims to create the most versatile pilot plant currently available in the market. This plant, characterized by its versatility and full automation, enables the identification of optimal experimental conditions and the detection of potential operational issues in industrial gasification or pyrolysis reactors.
Users have the flexibility to process up to 2 kg/h of solid materials for gasification and pyrolysis processes or opt for a smaller scale, handling up to 200 g/h.
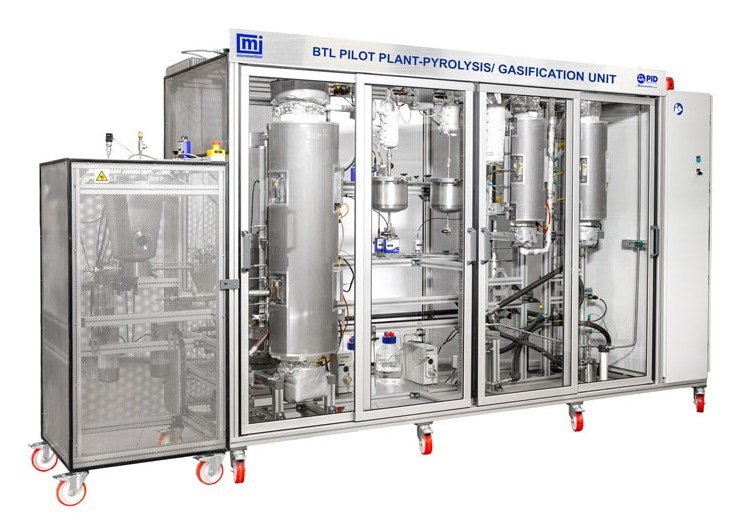
Image Credit: Micromeritics Instrument Corporation
Feeding System
A consistent and steady system for feeding solid materials, such as biomass and plastics, in a continuous and reproducible manner without fluctuations.
Gasifying Agent Inlets
Gas streams (such as air, O2, steam, and N2) undergo preheating up to 400 °C, with a comprehensive facility for steam generation integrated into the system.
Cyclones and Filter
A tandem connection of two heated cyclones and a high-temperature filter is employed to eliminate solid particles from the gas stream, thereby minimizing the ash content in the end product.
Fluidized Bed Reactor
The reactor is separated into the reactor zone and freeboard zone, maintaining a uniform operating temperature of 650–850 °C for pyrolysis and gasification, respectively. A radiant furnace, featuring three heating zones and capable of reaching up to 1000 °C, is employed to enhance the temperature profile. Provision for fluidization velocity determination.
Condensation Train
A system comprising an SS316 shell-tube exchanger, multiple vessels, and coalescence filters facilitates the effective cooling of hot gases, resulting in the efficient extraction of tar and bio-oil. Upon request, a temperature-controlled setup can be implemented to achieve fractionated bio-oil.
Electrostatic Precipitator
Suggested for use in pyrolysis, the electrostatic precipitator is specifically designed for the separation of fogging oil. This apparatus allows for the collection of liquid particles that cannot be obtained through condensation.
Additional Liquid Feeding System
A precision pump with high accuracy, capable of delivering up to 25 ml/min for liquid feeding. The system includes heat-traced lines or cooling provisions tailored to the properties of the liquid.
Tar Collection With Baths as Normative
A modular sampling system utilizing cool traps, where tar (high molecular weight organic compounds) is collected through the use of solvents.
Additional Hopper
Refilling solid materials without impacting the operating pressure of the plant to extend the duration of the experiment.
Automatic Gas Sampling System
The micro gas chromatograph (μGC) is incorporated into the system, enabling real-time analysis of gas samples and mass balance calculations.
Scrubber
To retain contaminants prior to releasing the product gas stream.
Gas Meter Totalizer
For quantifying the produced gas volume, incorporating corrections for temperature and pressure.
Burner
For combustion of any remaining contaminants within the product gas stream.
Gas Recycle/Compression System
The outlet gas stream can be reintroduced into the pilot plant at atmospheric pressure using a thermal mass flow controller, or it can be compressed for feeding into other equipment.
Slow Pyrolysis
The screw reactor unit facilitates the production of add-value solid material from waste through a slow pyrolysis process. It can treat various feedstocks across a broad range of temperature conditions.
Comprising an SS310 screw-driven horizontal tubular reactor within a multi-zone furnace, the system allows for operation with temperature ramps along the entire reactor length. The residence time in the reactor is adjustable, ranging from a few minutes to hours. The independent dosing screw system enables the modification of the feed rate independently of the residence time.
At the reactor outlet, the solid product is collected in a vessel, while the resulting gas exits through the top, where a filtering element is fixed to prevent the withdrawal of fine particles.
Vapors are then condensed to obtain liquid, and the gas product is measured using a wet gas meter. A vacuum pump is employed to prevent blockages in the reactor and maintain constant pressure in the system.
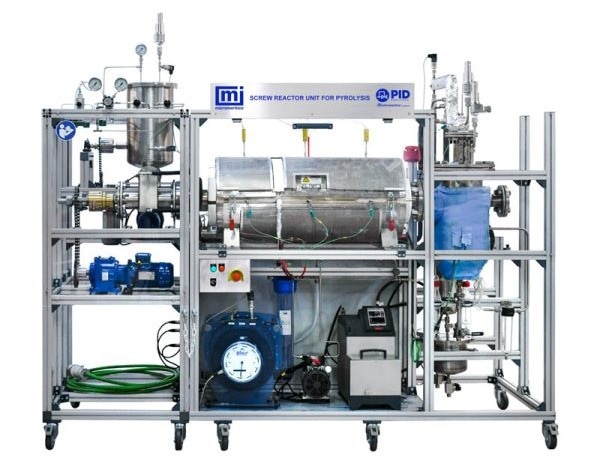
Image Credit: Micromeritics Instrument Corporation
MAT
A completely automated, controlled, and computerized laboratory reactor designed for the analysis of Fluid Catalytic Cracking (FCC). This reactor utilizes petroleum oils or renewable sources like bio-oil as feedstock.
- Facilitates the examination of catalyst activity and selectivity according to the ASTM D3907 method.
- Conducts continuous and automated control for up to four independent, programmed, and consecutive FCC tests.
- Versatile operation modes
- Fixed and normalized conditions adhering to the ASTM D3907
- Operator-determined conditions for each run and independent steps within the experiment
- Catalyst-to-oil ratio managed as a flow rate
- Injection flow rate and injection time variables
- Temperatures
- Achieves nearly zero dead volume through meticulous engineering of reactor size, precise pipe lengths, and distances.
- The standard unit can be customized to fulfill specific needs by incorporating additional equipment such as mass flow controllers, simultaneous dosing pumps, and special construction materials.
Utilizing precise syringe pump technology for gas oil feeding and maintaining excellent control over reaction temperature, this unit performs consecutive in-situ reaction and regeneration stages, including coke quantification, even for very short reaction times.
The four liquid products produced are gathered in a cooled receiver throughout the experiments, while gases can be analyzed online using a gas chromatograph.
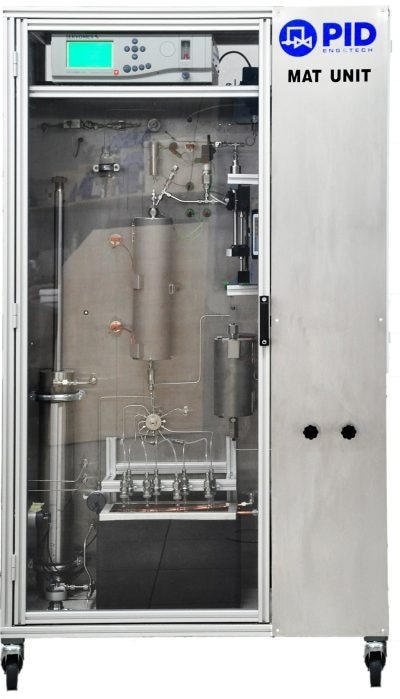
Image Credit: Micromeritics Instrument Corporation
Stirred Tank Pilot Plant
This computerized and automated pilot plant utilizes a stirred tank reactor, offering the flexibility to operate in continuous, batch, or semi-batch modes. The plant is certified for high pressure in compliance with current regulations, allowing customers to design their pilot plant with a range of options.
- Fully customizable configuration for both gases and liquids.
- Features a stirred tank reactor constructed from materials like SS316, Hastelloy C, glass, or PTFE lined, with a magnetic coupling agitator suitable for high-pressure applications. The reactor volume ranges from a few milliliters to several liters.
- Equipped with a temperature control system for the reactor, utilizing an electrical furnace or a heat-jacketed reactor with a cooling coil option.
- Offers various catalytic baskets for different applications.
- The reactor's pressure control system relies on PID Eng&Tech's patented microregulation servocontrolled valve. For fractionation purposes, two distinct pressure controllers can be chosen for the reactor and separators.
- Features a high-pressure liquid-gas separator based on PID Eng&Tech's patented design, minimizing dead volume in accordance with specific process conditions.
- Offers parallel reactors to enhance throughput capacity.
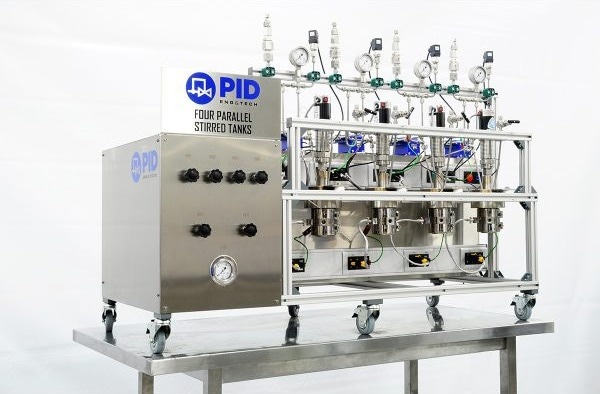
Image Credit: Micromeritics Instrument Corporation
Photocatalytic Reactor Unit
A computerized and fully automated system built around a photocatalytic reactor, equipped with one or two sight ports, capable of operating at elevated pressure and temperature.
- Includes a steam generator facility.
- Fully customizable options for both gases and liquids.
- Photocatalytic reactor designed with various materials and configurations to accommodate different amounts/sizes of catalyst.
- The high-pressure liquid-gas separator utilizes PID Eng&Tech’s patented design, minimizing dead volume to align with specific process conditions.
- Offers different light systems based on wavelength and power supply requirements.
- The pressure control system for the reactor relies on PID Eng&Tech's patented microregulation servocontrolled valve.
- Features an available vacuum system.
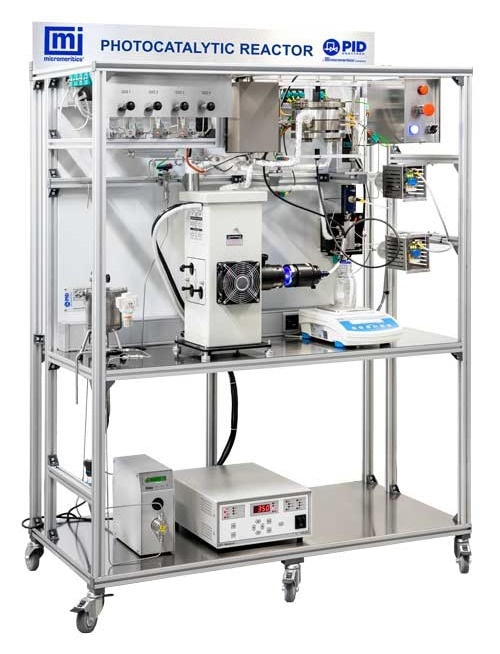
Image Credit: Micromeritics Instrument Corporation
Custom Made
Specializing in the creation of tailored pilot plants, the engineering team is dedicated to achieving customer satisfaction. This is achieved via collaboration with clients to transform process ideas into research and development equipment.
By employing pre-designed modular components, the company substantially diminishes two vital project elements: construction time and cost. Cutting-edge advancements are also integrated into process control technology to guarantee maximum efficiency.
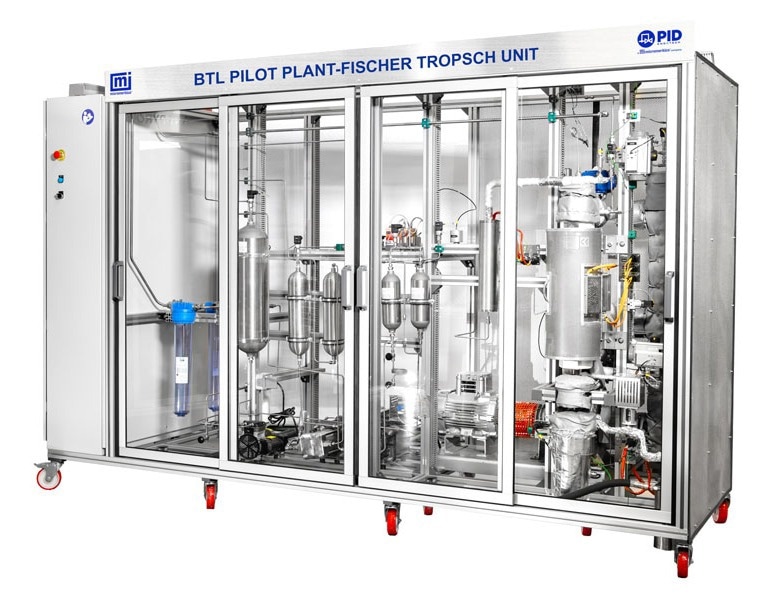
Image Credit: Micromeritics Instrument Corporation
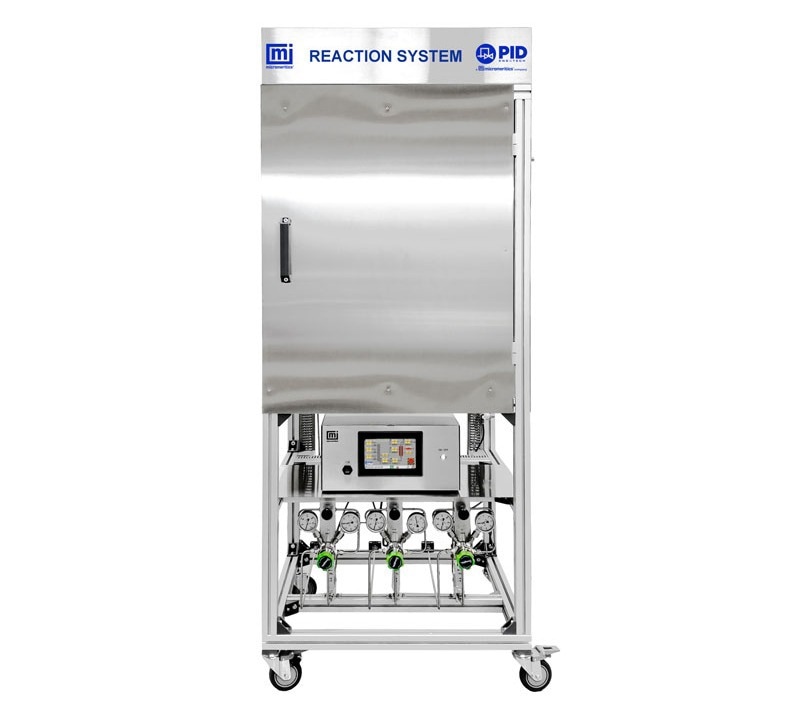
Image Credit: Micromeritics Instrument Corporation
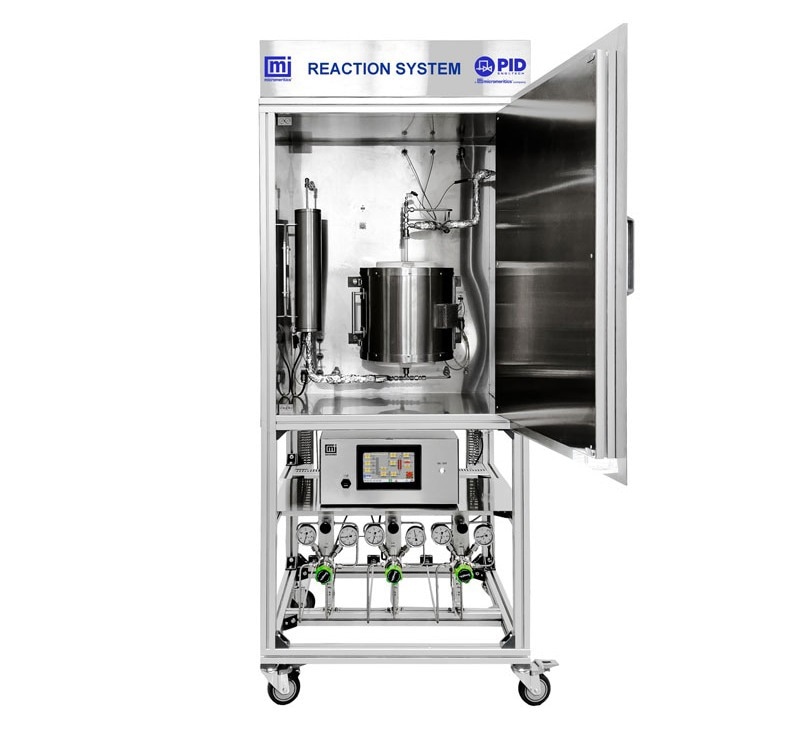
Image Credit: Micromeritics Instrument Corporation
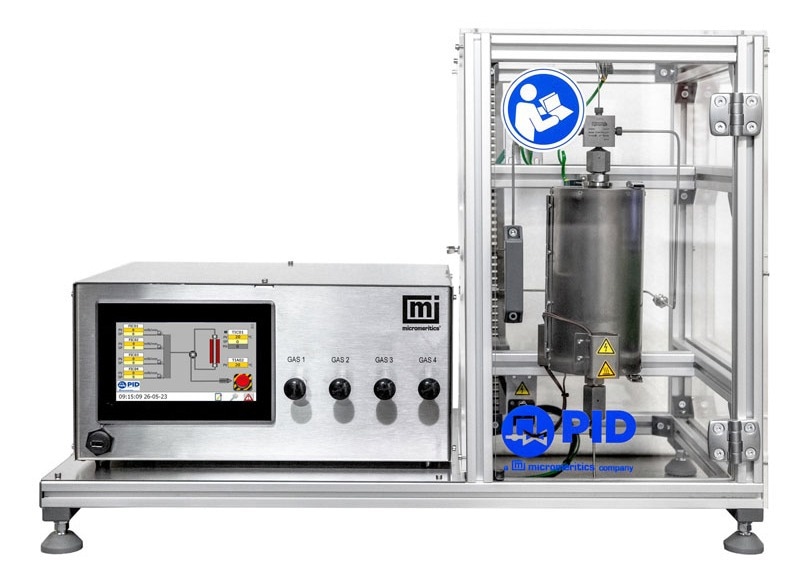
Image Credit: Micromeritics Instrument Corporation