The DSC 500 Pegasus® High-Temperature Differential Scanning Calorimeter sets the benchmark for DSC analysis precision, even at high temperatures. It is designed to solve challenging thermal analysis problems by investigating high-performance materials.
- Modular Design for Extensive Versatility: Its modular design makes it adaptable to many applications and makes it easy to exchange furnaces and sensors. This device can handle a wide range of temperatures, from –150 °C to 2000 °C, to satisfy different thermal analysis needs.
- Superior Sensor Technology for Precise Measurements: For difficult applications, such as specific heat measurements at high temperatures, the high-performance heat flux DSC sensors and accurate sensor placement guarantee outstanding accuracy.
- Vacuum-Tight Design for Elimination of Atmospheric Influences: Due to the vacuum-tight design and precise gas flow control, inert, oxidizing, reducing, and corrosive gases can all be precisely managed in high-purity atmospheres. This design promotes dependable outcomes by removing the potential for unintended reactions.
- Versatile Hardware and Intelligent Software for Efficient Research: The DSC's dual-hoist system can handle up to 20 samples, operating two furnaces or integrating the Automatic Sample Changer (ASC). The superior software suite, which includes Identify for sophisticated material identification and AutoEvaluation for automated data analysis, complements this hardware. By streamlining sample processing, this configuration improves research procedures and saves significant time.
- Beyond Standard DSC Analysis: The DSC system goes beyond conventional thermal analysis by facilitating connectivity with advanced gas analysis systems like FT-IR or mass spectrometers. By offering comprehensive insights into the evolution of gases and the behavior of materials during thermal processes, this integration greatly expands the amount of information that can be obtained from a single analysis.
Method
Differential Scanning Calorimetry (DSC) is a strong analytical technique used in materials science, chemistry, and other domains to determine temperature changes in materials. A typical variant, the Heat Flow DSC system, works by directly detecting the heat flow associated with material changes as a function of temperature and time.
Measuring Principle of Differential Scanning Calorimetry
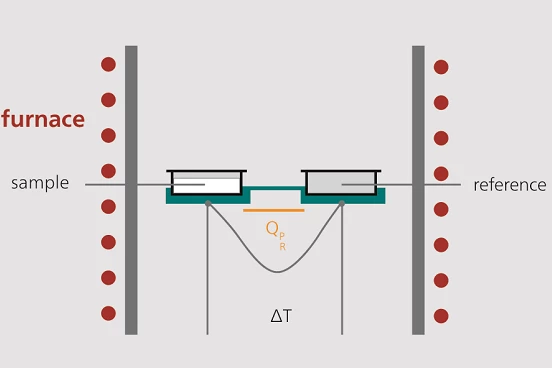
Image Credit: NETZSCH-Gerätebau GmbH
Monitoring the difference in the amount of heat needed to raise the temperature of a sample and a reference material at the same rate is the foundation of Differential Scanning Calorimetry’s (DSC) measuring principle.
Any variation in heat flow between the sample and reference is measured since they are subjected to the same temperature circumstances. This discrepancy suggests that the sample changes chemically or physically, either by melting, crystallizing, or going through chemical reactions that absorb or release heat.
A DSC measuring cell consists of a furnace and an integrated heat-flux sensor with specific locations for the sample and reference pans.
The DSC equipment provides a thorough profile of the sample’s thermal characteristics and transitions, recording variations in heat flow as the temperature varies.
Relevant instrument and application standards, such as ISO 11357, ASTM E793, ASTM D3895, ASTM D3417, ASTM D3418, DIN 51004, and DIN 51007, serve as the foundation for the DSC systems.
Specifications
Technical Data
- Maximum temperature range
- Interchangeable sensors
- DTA, DSC, DSC cp with different thermocouple options
- Gas atmospheres
- Inert, oxidizing, static, and dynamic
- Optional Oxygen Trap System (OTS®) for oxygen impurities below 1 ppm O2
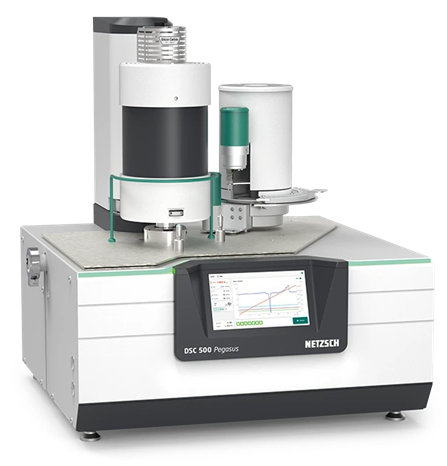
Image Credit: NETZSCH-Gerätebau GmbH
- Temperature accuracy
- Temperature precision
- Enthalpy precision
- ± 1 … 3% (depending on temperature range)
- Specific Heat Capacity precision
- –150 °C to 1000 °C: ± 1.0%
- RT to 1400 °C: ± 2.5%
- RT to 1500 °C: ± 3.5%
Sensors
The DSC 500 Pegasus® has an adjustable sensor system that enables customized solutions using different furnace-sensor combinations, assuring maximum performance for any operation.
The instrument provides unparalleled flexibility, with a diversified selection of sensors to meet various application requirements. It enables customized solutions via various furnace-sensor combinations, ensuring peak performance for every application. The user-friendly design assures easy and efficient operation, making it simple to use in any environment.
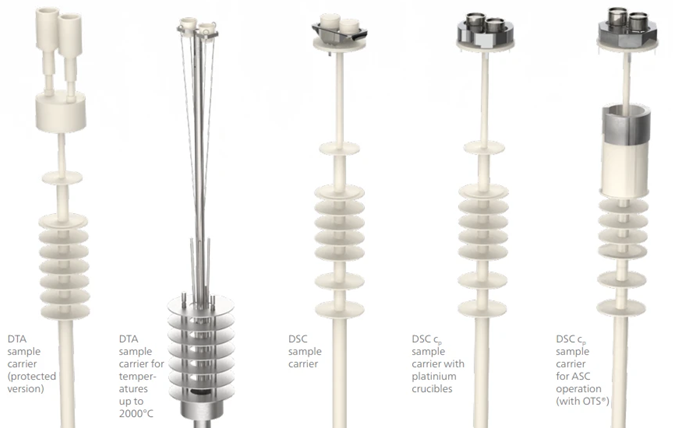
Image Credit: NETZSCH-Gerätebau GmbH
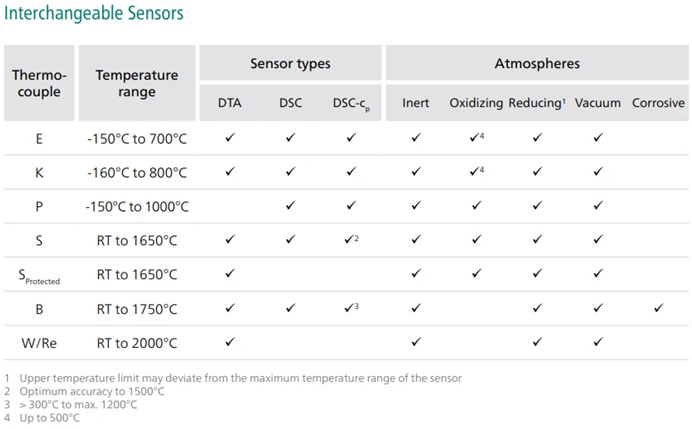
Image Credit: NETZSCH-Gerätebau GmbH
Accessories
Oxygen Trap System
The OTS® (Oxygen Trap System) is a versatile and efficient system developed for various applications, particularly in areas where controlling oxygen levels is critical. This device is designed to collect and remove oxygen from a particular region, making it perfect for processes that need very low oxygen concentrations (< 1 ppm) to prevent oxidation or other chemical reactions.
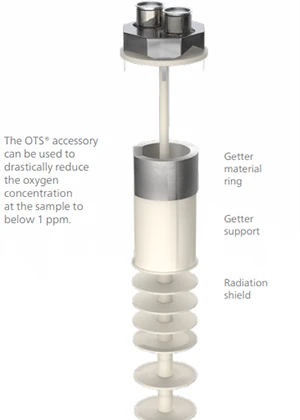
Image Credit: NETZSCH-Gerätebau GmbH
Evolved Gas Analysis
The DSC 500 Pegasus® provides seamless interaction with Evolved Gas Analysis (EGA) techniques, enhancing material characterization. Coupling choices include FT-IR, QMS, and GC-MS. These capabilities enable extensive investigations of degradation processes, volatile emissions, and reaction mechanisms, providing additional insights into material behavior during thermal treatment.
Discover the full potential of NETZSCH’s coupling solutions for thorough thermal and evolved gas investigation.
Glove Box and Hot Cell Instruments
The DSC 500 Pegasus® is available in versions specifically optimized for use in glove boxes or hot cells. These setups include external electronics and specific gas-tight feed-throughs, allowing for exact temperature analysis under restricted operating conditions.
Corrosive-Resistant Version
The DSC 500 Pegasus® is a corrosion-resistant variant with external mass flow controls and specific sealing. This architecture allows for precise temperature analysis in harsh environments, delivering reliable results even under tough settings.
Crucibles
The DSC 500 Pegasus® includes a variety of crucibles, allowing for exact readings over a temperature range of -150 °C to 2000 °C. Metals (Al, Ag, Au), ceramics (Al₂O₃, MgO, ZrO₂, Y₂O₃, BN, etc.), and graphite are among the crucible alternatives available to meet varied sample needs. Different crucible sizes allow more flexibility when working with inhomogeneous or low-density samples.
For certain applications, more specialty crucibles are available:
Aluminum crucibles can be gas-tight sealed with a compact sealing press, making them excellent for isolating samples from the surrounding atmosphere or containing gas emissions.
Reusable stainless steel and titanium autoclave crucibles for measurements of up to 100 under elevated pressures.
To ensure reliable performance under difficult circumstances, a PtRh/ceramic crucible system with a detachable liner is available for research requiring metal melts or reactive test materials.
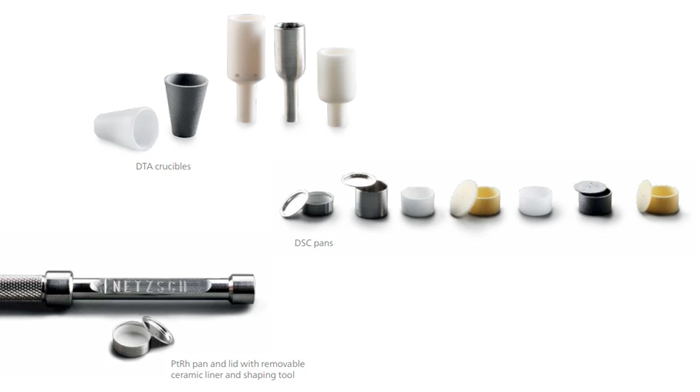
Image Credit: NETZSCH-Gerätebau GmbH
Types of Furnaces
Source: NETZSCH-Gerätebau GmbH
Type |
Temperature range |
Cooling system |
Silver furnace |
-120 °C to 675 °C |
Liquid nitrogen |
Steel furnace |
-150 °C to 1000 °C |
Liquid nitrogen |
Platinum furnace |
RT to 1500 °C |
Forced air |
Silicon carbide furnace |
RT to 1600 °C |
Forced air |
Rhodium furnace |
RT to 1650 °C |
Forced air |
Graphite furnace |
RT to 2000 °C |
Tap or chilled water |
Software
Proteus®: Simplifying Complex Thermal Analysis
Without compromising analytical power, Proteus® software simplifies thermal analysis and offers a smooth, user-friendly experience. Proteus®, made to operate on the Windows® platform, offers all the features required to carry out accurate measurements and confidently assess data.
Its user-friendly menus and automatic processes simplify even the most difficult investigations, making it an indispensable tool for professionals seeking dependable and efficient thermal insight. Proteus®, once licensed with the instrument, can be installed on multiple systems, increasing the workflow's flexibility and accessibility.
Proteus® software offers users a variety of Differential Scanning Calorimetry (DSC) features for precise and thorough thermal analysis:
- Temperature Analysis: Determine the exact onset, peak, inflection, and end temperatures
- Transformation Enthalpies: Analyze peak regions using unique baselines, including partial peak area evaluations
- Complex Peak Analysis: Obtain detailed information such as characteristic temperatures, regions, peak heights, and half-widths
- Glass Transition Analysis: Evaluate glass transition temperatures in detail, identifying onset, midpoint, and inflection points
- BeFlat® Baseline Correction: Automate baseline adjustments to increase accuracy
- Tau-R® Mode: Improves analytical accuracy by accounting for instrument time constants and thermal resistance, allowing for better resolution of exothermic and endothermic effects and correct interpretation of DSC data
- AutoEvaluation: Streamline data analysis by using automated procedures to detect critical thermal events such as peaks, onsets, and transitions, resulting in fast, accurate, and reproducible results with minimal user involvement
LabV®-Primed Instrument
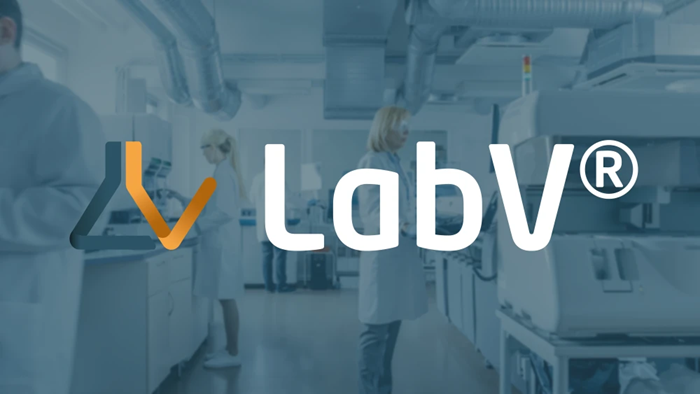
Image Credit: NETZSCH-Gerätebau GmbH
LabV® extracts information from the analytical device: All measurement data is instantly imported into the LabV® software, a secure database solution. This allows users to search and view the data in LabV®, which is available from any location. Users can also create reports.
Further Advanced Software Options
The Proteus® modules and expert software solutions enable more advanced processing of thermoanalytical data for more sophisticated analyses.
Temperature-Modulated DSC
The TM-DSC module software extension for temperature-modulated DSC tests:
Temperature-modulated DSC (TM-DSC) is a DSC technique in which a sample is subjected to a combination of linear and periodic temperature programs. Temperature-modulated DSC separates overlapped DSC effects by calculating reversing and non-reversing signals.
In a single TM-DSC test, glass transitions can be distinguished from exothermal cures, decomposition, evaporation, relaxation, and cold-crystallization processes. The DSC 500 Pegasus® is the only DSC that can perform TM-DSC tests up to 1650 °C. Almost all accessible furnaces, in conjunction with various DSC sensors, are appropriate for such tests. The test is completely dependent on a software solution. The NETZSCH TM-DSC technology increases the separation of time-dependent events from the overall heat flow.
PeakSeparation
PeakSeparation enables the proper separation and evaluation of overlapping transitions.
PeakSeparation enables the presentation of experimental data as an additive overlap of peaks. This application provides several curve types: Pearson, Gauß, Cauchy, pseudoVoigt, Fraser-Suzuki, modified Laplace, and Pearson. It fits experimental data as an additive superposition of peaks.
Purity Determination
Purity Determination is a program for assessing a material's purity by analyzing its DSC melting peak.
2DTemperatureCalibration
This innovative temperature calibration meets international standards and is both temperature and heating rate-dependent. This software feature is particularly useful for temperature accuracy when multiple heating rates are utilized in the same measurement.
Kinetics Neo
Predicting Material Behavior and Reaction Processes
Chemical reactions can change materials with precisely defined qualities into other compounds with different attributes. As in the case of explosions, the reactions might occur in a split second, or they can take hundreds of thousands of years, as in the case of mineral formation.
Temperature and time affect material sintering, crystallization, curing, and breakdown. Therefore, it is crucial to understand how quickly these events occur to improve a process or model material behavior.
Kinetics, also known as reaction kinetics or chemical kinetics, investigates the rate of chemical processes and allows for determining reaction rates. It also takes into account the factors that control these reactions.
The NETZSCH Kinetics Neo software evaluates chemical processes. It enables the analysis of temperature-dependent processes. The end consequence of such a study is a kinetics model or approach that accurately describes experimental data under various temperature settings.
The model can anticipate the behavior of a chemical system under temperature settings that the user defines. Alternatively, similar models can be applied to process optimization.
The software can evaluate many forms of thermal curves, which describe changes in a specific material characteristic, as observed during a process. Studies employing Differential Scanning Calorimetry (DSC), Thermogravimetry (TGA), Dilatometry (DIL), Dielectric Analysis (DEA), Accelerating Rate Calorimetry (ARC), Rheology, and Viscosity (Torque) are all possible data sources.