On the surface, constructing a removable insulation blanket may appear straightforward: gather insulation material, add mesh on one side and a cover on the other, stitch them together, include rivets for fastening, and voila.
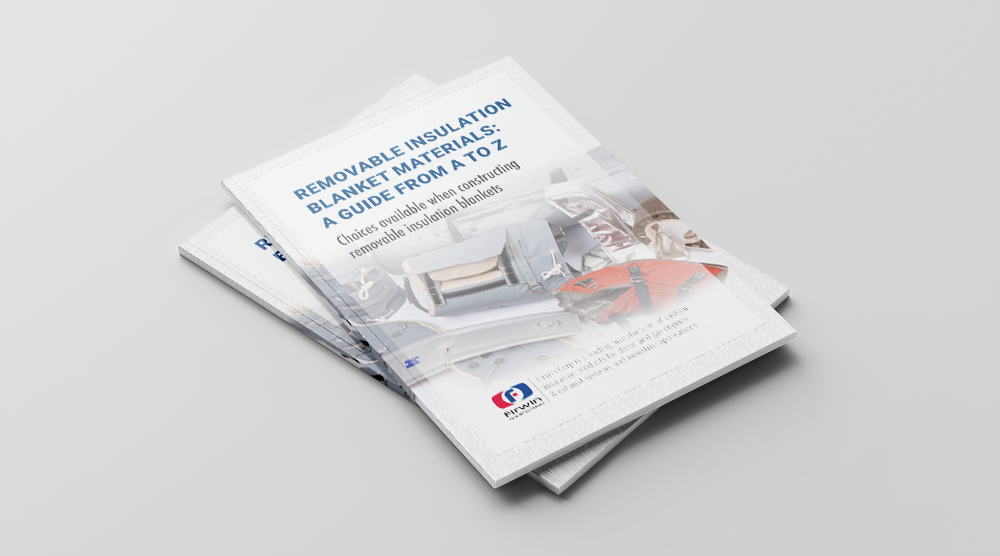
The reality is that manufacturing removable insulation blankets is much more complex than it may seem. Beyond just making sure the insulation blanket fits well around the part and accommodates any fixtures like brackets or screws, there is also the crucial decision of selecting the right materials for making the blanket.
This eBook serves as an A-Z guide of removal insulation blanket materials.
Removable Insulation Blanket Construction
It is common knowledge across industry that a removable insulation blanket is made up of three main parts.
- First, there is the “cold face,” which is the outer protective layer that shields and protects the insulation from the environment in which it is placed.
- Then, there is the main insulation mat. This is usually around 1” thick fiberglass, which is where the actual heat containment comes from. Note that the thickness of the insulation mat can vary from ½” to up to 4”, depending on the application and the amount of heat reduction required.
- Lastly, there is the “hot face”, which is the inner layer that holds the insulation mat in place and serves as a protective barrier, shielding the insulation mat from any fluid seepage.
Besides these three main components, a removable insulation blanket also requires a good fastening system to secure the insulation blankets in place. These may include straps, lacing, wire, snaps, springs, and velcro. Components can vary and this is dependent on both the application use and end-user requirements.
When determining the composition of an insulation blanket, the Firwin design team considers several factors, such as:
- Aesthetic requirements (i.e., the look of the blanket, color matching, etc.).
- Ambient temperature safety requirements (i.e., underground mining, marine, UL, etc.)
- Desired outer surface “touch temperature” Space limitations.
- Desired heat retention within the system (i.e., desired exhaust temperature)
- Exposure to elements (i.e., water, chemicals, debris, etc.)
- Frequency of insulation removal
- Location (i.e., indoors vs. outdoors).
- Maximum temperature range of an application.
- Regulatory requirements (i.e. Marine)
Download the eBook