Materials and component testing is a fundamental aspect of ensuring the safety and reliability of products used in everyday life. This eBook discusses the critical practices for protecting the professionals involved in these tests, whether they are lab managers in R&D labs or technicians in automated manufacturing facilities.

Download the eBook
The complex machinery and stringent procedures in materials testing necessitate a comprehensive approach to safety, underscoring the crucial role of equipment vendors in providing robust features, training, and ongoing support.
This eBook outlines five essential practices for safe operation across diverse testing solutions. These best practices form a foundation for minimizing safety risks throughout the testing process. They emphasize the importance of a holistic approach to safety, encompassing everything from initial specification and installation to training and maintenance.
- Practice One: Establish Intended Testing Procedures
Due to the variety of testing procedures and specimens, safety precautions must align with application-specific parameters. It is crucial to define safety features based on the test performed, the materials used, and the operating environment. Collaboration with your equipment vendor from the sales consultation stage is essential for understanding and customizing safety requirements.
- Practice Two: Adhere to Intended Testing Procedures and Specimen Materials
Continuing from the first practice, it is crucial to adhere to the specified materials and procedures throughout the equipment's lifecycle. Any deviations should be addressed with your vendor to ensure that safety features remain effective under the new conditions.
- Practice Three: Specialized Transportation is Vital
Given the heavy and often top-heavy nature of specialized testing equipment, transportation requires meticulous planning and execution. Improper handling can result in equipment damage or personal injury, making it imperative to involve your vendor in transportation logistics from the outset.
- Practice Four: Ensure Comprehensive Training for All Personnel
Only personnel specifically trained on the equipment should operate it, with all others maintaining safe distances. Continuous training resources must be available, and redundant safety warnings should be implemented to remind personnel of key risks.
- Practice Five: Vendor-Supported Continuous Quality Control: Over time, new safety risks may emerge that were not initially apparent. A committed equipment vendor will proactively address these risks through continuous quality control, drawing on the experiences of their global customer base to mitigate issues before they lead to incidents.
ZwickRoell's comprehensive approach to materials testing safety integrates all the recommended practices. From systematic risk analysis and customized safety features to specialized transportation and ongoing quality control, ZwickRoell ensures that safety is paramount in every aspect of materials testing.

Download the eBook
Download the full eBook to learn more about current guidelines and best practices that can be used to significantly enhance the safety of your materials testing operations, ensuring reliable and precise test results while safeguarding the well-being of your personnel.
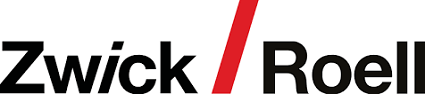
This information has been sourced, reviewed, and adapted from materials provided by ZwickRoell GmbH Co. KG.
For more information on this source, please visit ZwickRoell GmbH Co. KG.