Writing in the journal Additive Manufacturing, a team of researchers from the Manipal Academy of Higher Education in India have reported the development of a 3D printed self-moisturizing contact lens. Currently in pre-proof, the research has implications for the development of next-generation contact lens-based medical devices.
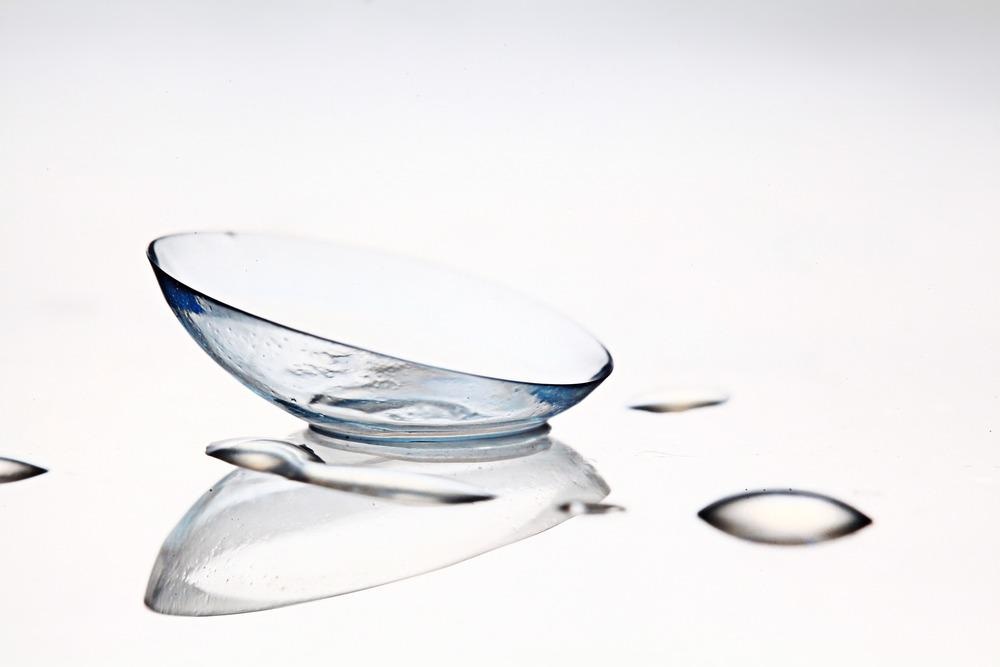
Study: Self-Moisturizing Contact Lens Employing Capillary Flow. Image Credit: Kichigin/Shutterstock.com
Contact Lenses for Biomedical Applications
Contact lenses are commonly used to correct vision, providing the advantages of being easier to wear than glasses. Moreover, they have cosmetic uses as some individuals find them more aesthetically pleasing. Beyond this conventional use, contact lenses have been explored for applications in biomedicine to develop non-invasive smart sensing devices and point-of-care diagnostics.
Several studies have been conducted in this field, with some notable innovative technologies developed. Google lens, for example, is a smart contact lens that can be used to monitor glucose levels in tears and provide diagnostic information for diabetic patients. Interocular pressure and eye motion can be monitored using smart devices. Nanostructured materials have been incorporated into smart contact lens-based sensing platforms, acting as transducers.
However, the use of these devices can prove challenging, hindering the commercial development of contact-lens-based platforms. Wearing contact lenses for extended periods of time can cause discomfort, and they have the tendency to dry out, causing further problems for the wearer. Contact lenses can interfere with the natural blinking process, leading to inadequate moisture retention and damage to the fragile tissue in human eyes.
Approaches to Overcoming these Challenges
Traditional methods include eye drops and punctum plugs that can improve tear stimulation and thereby rehydration of the eyes. Two novel approaches have been developed in recent years.
In the first approach, a single layer of graphene is used to decrease moisture evaporation, although this approach is hindered by complex manufacturing methods. In the second approach, electroosmotic flow is used to maintain the lens’s moisture, although this approach requires the development of reliable biocompatible batteries.
Manufacturing Methods
Lathe machining, molding, and spin-casting methods are traditionally used to manufacture contact lenses. Molding and spin-casting processes have the benefit of being cost-effective, but they are hindered by complex post-processing treatments to improve material adherence to the surface of molds. Lathe manufacturing is a complex and costly process that possesses design limitations.
Additive manufacturing has emerged as a promising alternative to conventional contact lens manufacturing techniques. These techniques offer benefits such as reduced time, greater design freedom, and cost-effectiveness. The use of 3D printing for contact lenses and optical devices is still in its infancy, with a lack of studies performed on these processes. Challenges occur with the loss of structural features in post-processing and weak interfacial attachments. Reducing step size produces smoother structures and thus improves adhesion.
Despite the increased research focus on using 3D printing methods for contact lens manufacturing, there has been a lack of discussion on fabricating the molds compared to the lenses themselves. Integrating 3D printing techniques with conventional fabrication methods provides the best of both approaches.
The Study
The authors have used a novel approach to 3D printing self-moisturizing contact lenses. The master structure is manufactured with 3D printing, with the model developed using AutoCAD and stereolithography, a common 3D printing technology. The concave mold has a diameter of 15 mm and a base curve of 8.5 mm. Step size in the manufacturing process is small at 10 µm, which overcomes the traditional issues with 3D printed contact lenses.
The optic zone of the manufactured contact lens is then smoothened after printing and replicated onto PDMS, a soft elastomer material. The technique employed in this step is a soft-lithographic method. A key feature of the printed contact lenses is the presence of curved microchannels within the structure, which gives them self-moisturizing abilities. Moreover, the lenses possess favorable optical transmission.
The authors discovered that the structure’s layer resolution determines the microchannels’ dimensions, with longer channels printed in the middle of the lens with reduced length at the edges of the printed constructs. However, when exposed to oxygen plasma, the structures became hydrophilic, facilitating capillary-driven fluid flow and moisturizing the printed constructs.
Due to the lack of microchannel size and distribution control, microchannels with well-defined microstructures with a reduced staircase effect were printed onto the master structure and then replicated on the contact lenses. Optical transmission loss was circumvented using acetone to polish the master structure’s optical zone and printing curved capillaries.
The authors have stated that their novel approach not only improves the self-moisturizing capabilities of printed contact lenses but also provides a platform for the future development of contact lenses that have lab-on-a-chip capabilities. This opens the door for using them as functional real-time biomarker probing applications. Overall, the research has provided an interesting research direction for the future of contact lens-based biomedical devices.
More from AZoM: A Current View of Scanning Electron Microscopy in Forensics
Further Reading
Aravind, M. Chidangil, S & George, S.D. (2022) Self-Moisturizing Contact Lens Employing Capillary Flow Additive Manufacturing 102842 [online, pre-proof] sciencedirect.com. Available at: https://www.sciencedirect.com/science/article/abs/pii/S221486042200241X
Disclaimer: The views expressed here are those of the author expressed in their private capacity and do not necessarily represent the views of AZoM.com Limited T/A AZoNetwork the owner and operator of this website. This disclaimer forms part of the Terms and conditions of use of this website.