Feb 28 2008
The cover that Bosch uses for the alternators of renowned car manufacturers is now being made of BASF’s Ultramid® A3UG5 LS, a polyamide 66 (PA 66). This is the first time that this novel material is being applied in automotive construction. The product - dyed black in this case - is rendered flame-retardant without halogen or red phosphorus and it is rated V0 according to the UL 94 fire safety standard. This is the only way to properly protect the alternator while meeting the high requirements made by Bosch standard N 2580-1 governing the contents of components.
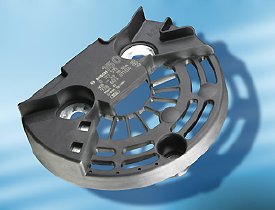
Moreover, this plastic can also be laser-written, a property that is becoming increasingly important: The logistics of large companies as well as the administration of detailed parts information often call for barcodes and data-matrix codes that can be flexibly and cost-effectively applied by means of laser technology.
The alternator cover made of Ultramid has now gone into serial production and is assembled at Bosch’s generator plant in Cardiff, Wales, U.K. Bosch intends to soon manufacture this product in other regions as well, which is why it needs suppliers like BASF since this company can ensure deliveries worldwide.