Jan 19 2010
In support of the 9.7% growth rate in the Chinese plastics processing industry, and in response to growing supply from the Middle East and other lower-cost feedstock regions, China's SINOPEC Beijing Research Institute of Chemical Industry has sponsored major programs in polyolefin catalyst, process, additive, and product developments. These programs and their resultant technology advances will be addressed by Dr. Jinliang Qiao at the SPE International Polyolefins Conference in Houston, TX, Feb. 22-24, 2010.
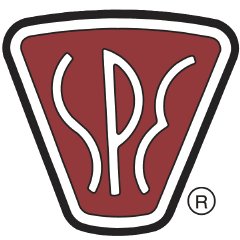
Research on BOPP film and PP pipe has resulted in new catalysts and additives. SINOPEC claims their N-series catalyst (also produced by BASF and known as Lynx 1000 in the U.S.) delivers PP with higher isotacticity and better stability. The N-catalyst technology was also extended to PE as BCE and BCS catalysts for slurry and gas-phase processes. A critical success factor was lower cost. Work continues on chrome-based and single-site catalysts for PE and broad-MWD catalysts for PP.
In the area of nucleating agents, SINOPEC has developed new agents with more efficient increases in PP stiffness (as measured by flexural modulus) and crystallization temperature. They have also identified nucleating agents for toughening and clarifying PP and nucleating LLDPE. Additives have also been identified to aid in the dispersion of bactericides, etc.
Responding to cost pressure, SINOPEC developed higher-crystallinity TPO formulations for automotive bumpers, eliminating the need for rubber compounding. Similarly, they developed new BOPP resins designed to allow faster extrusion on wider lines producing down-gauged uniform film. Additional requirements for this BOPP program were lower extractables with fewer "fisheyes," while accommodating reduced thickness with higher stiffness. This new BOPP resin was designed to utilize refinery propylene where ethylene is not available as a comonomer. It is produced with a patented non-symmetric donor technology.
Overall Chinese growth in GDP has supported increased demand for building and construction, leading SINOPEC to develop new PP pipe resins for hot water. Again, the developments have included catalyst programs to broaden molecular weight distribution. SINOPEC extended their new knowledge to PE to address challenging requirements in long-term hydrostatic strength, rapid crack propagation, and slow crack growth. Their structure/property research focused on the conflicting demands for stiffness and toughness, for which they have developed new PE100+ products.
The research has been conducted in cooperation with the National Nature Science Foundation of China under the auspices of the National Basic Research Program and the Ministry of Science and Technology.
Dr. Qiao's talk will be included in the plenary session of the SPE International Polyolefins Conference. Other sessions will include recent advances in catalyst technology, new process developments, new additives and polymer modification technologies, and emerging characterization methodologies. Applications sessions target packaging, infrastructure, and automotive markets.