Powder characterisation company Freeman Technology has joined and is actively supporting a collaborative program in the USA which aims to bring together a cross-disciplinary team of engineers, scientists and industry leaders to improve the way pharmaceuticals, foods and agriculture products are manufactured.
The Engineering Research Center for Structured Organic Particulate System (C-SOPS) involves the academic institutions of: Rutgers, the state university of New Jersey; Purdue University; New Jersey's Science and Technology Institute; and Universidad de Puerto Rico. Industry affiliates range from major pharmaceutical manufacturers to instrumentation suppliers.
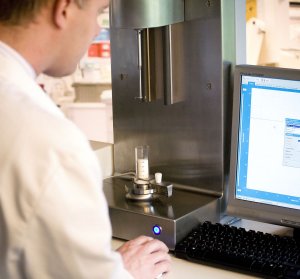
SOPS refers to multicomponent organic systems where performance depends on microstructure. They are used to deliver active substances at a pre-determined rate in a specific environment, are manufactured using similar processes across industries and share common technical limitations. The program provides a focal point for the science-based development of structured organic composite products and their manufacturing processes in the pharmaceutical, nutraceutical, and agrochemical industries. Full details are available at http://ercforsops.org/
Tim Freeman, Director of Operations at Freeman Technology is enthusiastic about his company's participation. "The FT4 powder rheometer is becoming an established tool within powder processing, and especially in the pharmaceutical industry," he said. "Freeman Technology is pleased to be supporting and adding expertise to this exciting and valuable research program. We are able to contribute to the direction of projects and I also have the privilege of being a mentor on a number of the project groups."
Freeman Technology specialises in systems that measure powder flow properties and has over a decade of experience in powder characterisation. The FT4 Powder Rheometer is a universal powder tester that uses patented dynamic methodology, fully automated shear cells and several bulk property tests, including density, compressibility and permeability to quantify powder properties in terms of flow and processability. Correlating this data with processing performance enables users to optimise powder processes.