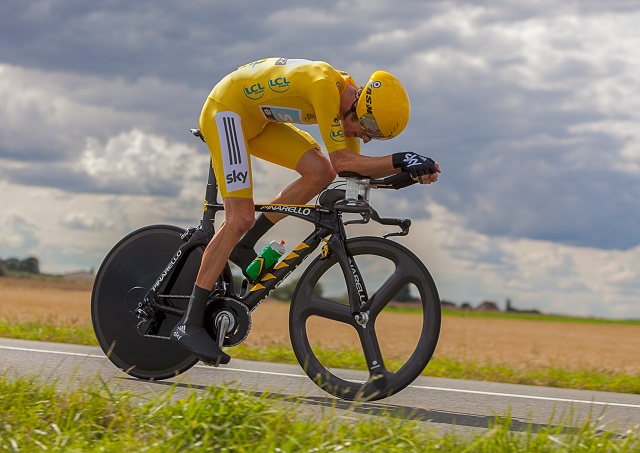
Image Credit: Radu Razvan | Shutterstock.com
On Sunday 7th June 2015, Sir Bradley Wiggins broke the World Hour Record with the help of 3D printed super lightweight and aerodynamic handlebars developed at the University of Sheffield’s Mercury Centre, in conjunction with Pinarello.
Sir Bradley broke the world record for the longest distance that a cyclist has ridden within an hour on the track, after spanning 218 laps or 54.526 km of the Lee Valley VeloPark in London. He achieved this record on the Pinarello Bolide HR, which is a track version of the Bolide, the time trial bike which Sir Bradley used to win the UCI World Championship Time Trial Championship in September 2014.
This record breaking bicycle was produced by Pinarello Lab, which is a part of the technical department of Pinarello, and designed by Dimitris Katsanis, a well-known aerodynamics and composites expert who works for British Cycling.
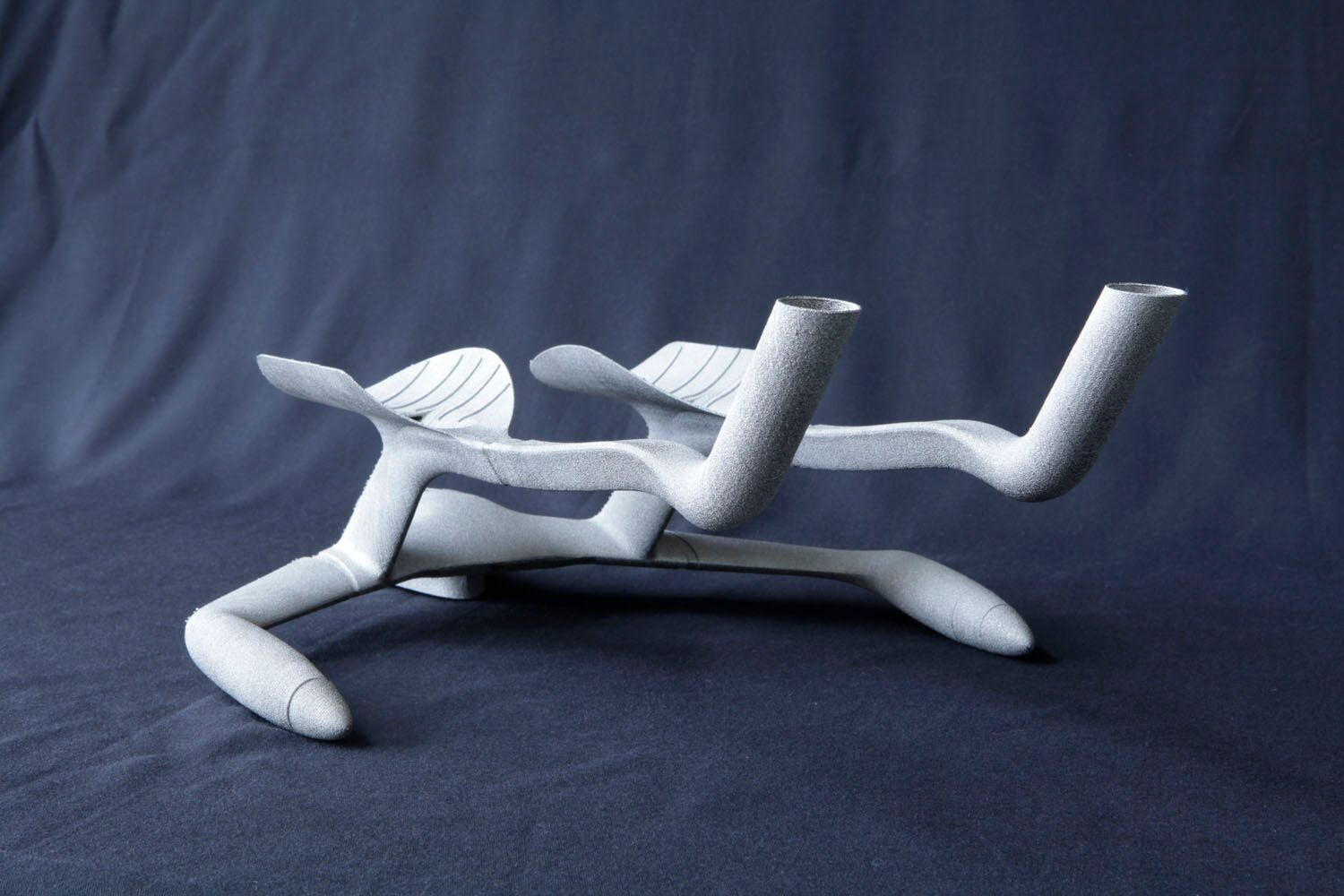
Image Credit: The University of Sheffield
3D printing, which is also known as additive layer manufacturing, was the technology used to develop the titanium handlebars on Sir Bradley’s Pinarello Bolide HR. The use of 3D printing technology allowed the developers to create complex designs and to quickly produce a number of versions in order to test which handlebars best matched the body size and cycling style of Sir Bradley.
The handlebars were the only component of the record breaking bike which was not composed of carbon fibre. This is because in the limited time frame the developers had available, several prototypes were developed and trials were conducted, which would have not been possible if the handlebars would have been produced using carbon fibre.
The University of Sheffield's leadership in advanced manufacturing illustrates the importance of Universities to the Northern Powerhouse. The Mercury Centre exemplifies Sheffield's capability in accelerating the translation of highly innovative powder materials and processes to UK industry; a key component of the Sir Henry Royce Institute.
Iain Todd, Professor of Metallurgy at the University of Sheffield
The Mercury Centre, a research institute under the Faculty of Engineering at the University of Sheffield, has also worked on projects with Formula 1 teams and aerospace companies in the past. The facility has been operational since 2007, with the aim of developing breakthrough scientific research and to implement new technologies such as 3D printing in various industries.
The key is to manage the airflow around the bike so the different components of the bike disrupt that flow as little as possible. Because the handlebars hit the airflow first it’s absolutely critical to perfect that part of the design – 3D printing allows us to make shapes that optimise this aspect that would be very hard to achieve using other manufacturing techniques.
James Hunt, Research Associate at the Mercury Centre
The designers used an Arcam Electron Beam Additive Manufacturing machine in order to make slight modifications quickly, without having to build new moulds to fabricate individual pieces. This saved time and allowed the designers to thoroughly test the parts and make the necessary adjustments to the handlebars prior to the world record attempt.
Bolide HR is the most aerodynamic bike in the world. When it came to the handlebars, we needed them to be as good in terms of aerodynamics, but we also needed them to be a perfect fit for the rider.
Dimitris Katsanis, Chief Designer at Pinarello Lab
Sir Bradley's Hour Record Around the Web