Jun 16 2015
A research team at the Cockrell School of Engineering, The University of Texas at Austin, has developed an innovative technology that could help future military gear and vehicles to offer excellent protection from impact. Known as negative stiffness (NS) honeycombs, the technology can be built into protective hardware such as athletic and military helme and car bumpers.
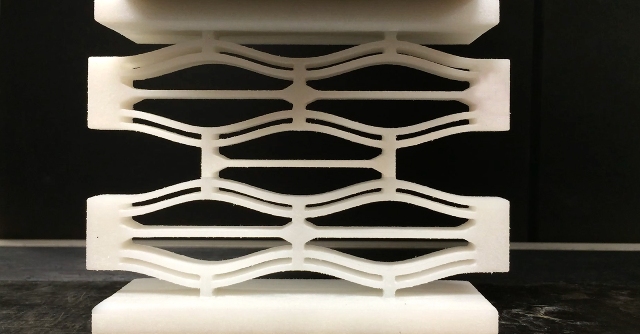
The NS honeycombs are energy-absorbing structures that are resistant to blunt and ballistic impact. They provide more durability than the present-day honeycomb technology that has been integrated into a wide range of products, spanning from aircraft through to automobiles. Study results on the novel structure have appeared online in May in Integrated Materials and Manufacturing Innovation.
"Whether you’re serving our country in uniform, playing in a big game, or just driving or biking to work, the potential for multiple collisions or impacts over time — however big or small — is a reality. We believe that this technology, when constructed in future helmets and bumpers, could reduce or even prevent many of the blunt-force injuries we see today," said mechanical engineering professor Carolyn Conner Seepersad. Seepersad headed the research along with Michael Haberman, a research scientist at UT Austin.
NS Honeycombs Demonstration
Traditional honeycomb structures contain repetitive insular panels, which are hexagonal-shaped cells occurring in different configurations and sizes. However, a major drawback of this type of honeycomb structure is that after a single impact they lose their overall protective properties on account of plastic buckling of the material. In other words, once these honeycomb structures absorb the force of a single compression, they do not bounce back to their original shape. In contrast, NS honeycombs can easily return to their original shape.
The cell geometry developed by the research team is capable of elastic buckling. It gives the required flexibility to the new NS honeycomb structures so that they can regain their energy-absorbing properties and shape subsequent to impact. It is possible to customize the cell dimensions so that the cell can tolerate varied amounts of force, and thus translate to a range of flexible applications. For instance, the present 3.5” lab model exhibits a force threshold level of 200 N, which is sufficient to absorb the energy of a 100 mph fastball in just 0.03 seconds.
The UT Austin team developed 3.5” NS honeycomb structures from nylon using selective laser sintering for experimentation. NS honeycombs can also be developed from a range of materials to suit specific application needs. The team also developed miniature NS honeycomb cells. Next, custom compression and drop tests that were designed and developed at UT Austin confirmed the predicted resilience and energy-absorbing behavior of the NS honeycomb structures.
Back in 2014, the U.S. Department of Defense awarded a Small Business Innovation Research Grant to the UT Austin team. This grant, and a partnership with the Maritime Applied Physics, made it possible to develop the NS honeycomb technology. Maritime Applied Physics is an engineering firm that often collaborates with the U.S. military. Another assessment will be carried out involving ballistic testing. Additionally, the research team is constructing a model of an improved combat helmet, which will contain NS honeycomb cells. This prototype will be ready this fall.