By Susha Cheriyedath, M.Sc.Reviewed by Skyla BailyNov 22 2021
A group of researchers from the USA has found a cost-effective and energy-efficient method to selectively recover cobalt and nickel from scraped Li-ion batteries using electrodeposition. This research has been published in the journal of Nature Communications.
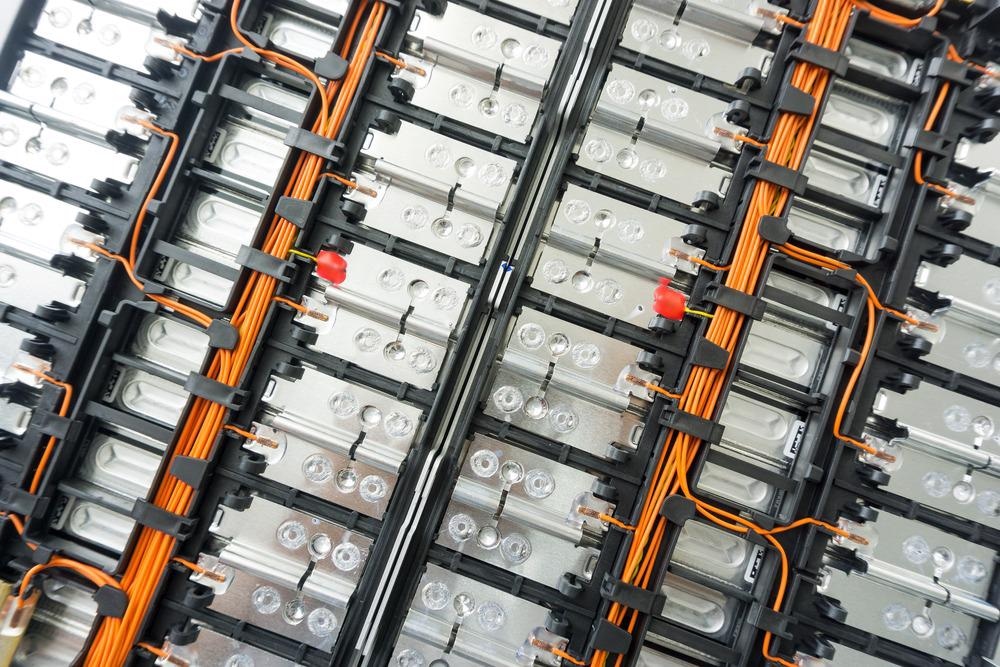
Study: Selective cobalt and nickel electrodeposition for lithium-ion battery recycling through integrated electrolyte and interface control. Image Credit: Smile Fight/Shutterstock.com
Why is it Necessary to Recycle Spent Li-ion Batteries?
As the global demand and consumption of lithium-ion (Li-ion) batteries (LiB) are increasing day by day, end-of-life spent LiBs are contributing to environmental pollution and governmental and political pressure.
On top of that, most of the metals used in these batteries are still scarce in terms of mining. These spent multi-metallic cathodes of LiBs, such as lithium nickel manganese cobalt oxide (NMC) cathodes, contain lithium (5–8%), nickel (5–10%), cobalt (5–20%), and manganese (10–15%), whereas nickel-metal-hydride batteries possess a high content of nickel (36–42%) and cobalt (3–5%).
What are the Pre-Existing Processes and Challenges in the Recycling of LIBs?
The chemical separation of cobalt and nickel from NMC can be achieved through solvent extraction, precipitation, adsorption, intercalation, and dialysis. The solvent extraction and precipitation usually exhibit high selectivity performance, but require large thermal energy consumption, large chemical costs, or waste generation and may face challenges concerning complex solution/speciation chemistry.
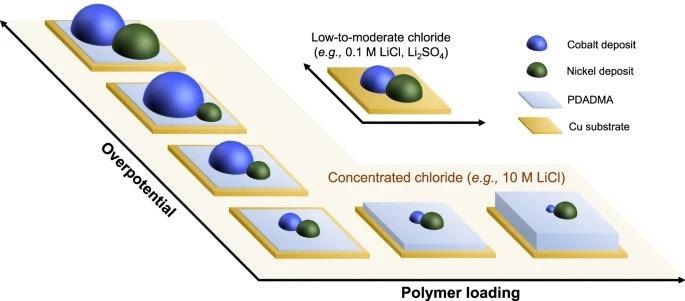
A schematic representation of potential-dependent selectivity tuning enabled by synergistic electrolyte and interfacial control. Image Credit: Kim, K et al., Nature Communications
Among various electrochemically driven techniques, electrodeposition is a simple and versatile method with command over nucleation and growth, morphology, and deposit composition. The reduction potentials of component metals are the most critical parameter in electrodeposition for the selective separation and recovery of metals from multicomponent mixtures.
The low-temperature, aqueous-based alternatives are a more desirable, environmentally compatible, and energy-efficient route in electrodeposition. However, aqueous electrolytes present intrinsic selectivity limitations for electrodeposition processes, due to the near-equal standard reduction potentials between nickel and cobalt (E° Ni = −0.250 V and E° Co = −0.277 V vs standard hydrogen electrode (SHE)), leading to untargeted co-deposition with low selectivity, thus necessitating additional chemical steps for nickel-cobalt separation such as solvent extraction before recovery via electrowinning.

Selectivity tuning in the electrodeposition of cobalt and nickel enabled by interfacial charge control with a positive polyelectrolyte, PDADMA. Image Credit: Kim, K et al., Nature Communications
What are the Steps in this Electrodeposition Process?
Cathode recycling involves a series of pre-treatment steps, including discharging, dismantling, separating, and harvesting active materials from a current collector. The batteries were immersed in 10% (w/v) NaCl solution for 24 hours to completely discharge.
Then they were manually disassembled using a saw and a sharp-nosed plier and were cut into small pieces. After that, the cathode active materials were separated from the aluminum current collector by using N-methyl pyrrolidine (NMP) as a solvent to dissolve the PVDF binder present in the collector. The small pieces of cathode scraps were treated in NMP at 100 °C for 24 h.
The obtained active material mixture was leached in 10 M HCl solution; this resulted in the formation of a dark green mixture of nickel-rich concentrated chloride, composed of cobalt, nickel, and manganese of the molar ratio 1.00:6.52:0.50, respectively.
The rest of the processes involve two cycles of electrodeposition/stripping, one each for cobalt and nickel recovery, respectively.
The first electrodeposition was carried out at −0.725 V vs Ag/AgCl on a poly (diallyl dimethylammonium chloride)/ copper (PDADMA/Cu) electrode for selective up-concentration of cobalt on an electrodeposit, followed by anodic stripping that released recovered solid-phase cobalt/ nickel into a liquid phase for secondary up-concentration and processing.
The stripping electrolyte, after the addition of 10 M LiCl, appeared distinctively bluish in color, due to the formation of predominant CoCl42− complex, as compared to the strong greenish and nickel-rich electrolyte obtained right after the leaching. The secondary PDADMA-driven electrodeposition at −0.725 V vs Ag/AgCl from the up-concentrated electrolyte gave significantly improved cobalt purity of about 96.4 ± 3.1%.
After the first selective cobalt deposition, the Ni/Co ratio increased in the remaining liquid phase. The second cycle of electrodeposition was carried out at −0.6 V vs Ag/AgCl that gave nickel of purity 94.1 ± 2.3% on the deposit after 30 min electrodeposition.
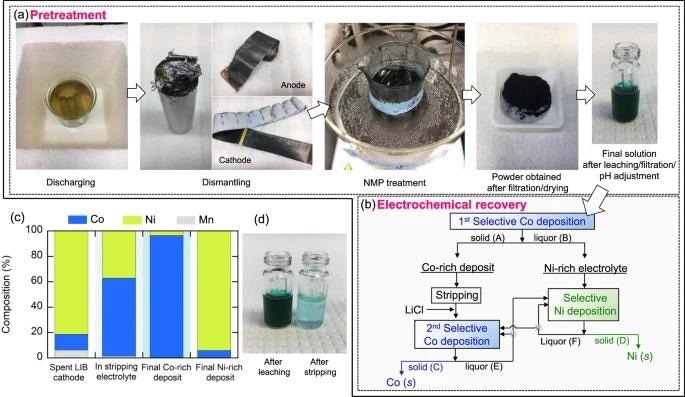
Application of selective electrodeposition for potential use in battery recycling processes. Image Credit: Kim, K et al., Nature Communications
What Was the Result?
The researchers combined electrochemical approaches i.e. electrolyte control and interfacial design for tuning molecular selectivity for cobalt and nickel recovery. The control of speciation effectively discriminated against metals with similar electrochemical properties in aqueous solutions.
The interfacial tailoring of the electrode with a positively charged polyelectrolyte, PDADMA, for additional selectivity control is enabled by modulating the mobility of CoCl4 2− in the positive polyelectrolyte layer.
The finding suggests that metal selectivity depends on electrode potential and polymer loading. The mass loss of PDADMA upon anodic stripping accounted for only less than 0.3% of the entire PDADMA loading, indicating the stability of the polyelectrolyte upon electrodeposition/stripping under the given electrolyte conditions. The report gives a final product purity of 96.4 ± 3.1% and 94.1 ± 2.3% for cobalt and nickel, respectively.
Thus, the results point to an innovative way of recovering electrodeposited cobalt and nickel without the intensive input of thermal energy or the use of harmful chemicals in an environmentally friendly aqueous medium.
Reference
Kim, K., Raymond, D., Candeago, R. et al. Selective cobalt and nickel electrodeposition for lithium-ion battery recycling through integrated electrolyte and interface control. Nat Commun 12, 6554 (2021). https://www.nature.com/articles/s41467-021-26814-7
Disclaimer: The views expressed here are those of the author expressed in their private capacity and do not necessarily represent the views of AZoM.com Limited T/A AZoNetwork the owner and operator of this website. This disclaimer forms part of the Terms and conditions of use of this website.