Nanotechnology has the potential to revolutionize many of today’s advanced systems and machinery via the manipulation of matter on a near-atomic scale to produce new structures, materials, and devices. A team of researchers, writing in the journal Polymers, have synthesized a hybrid fiber-reinforced polymer specifically for aeronautical structural purposes with the addition of ceramic nanoparticles.
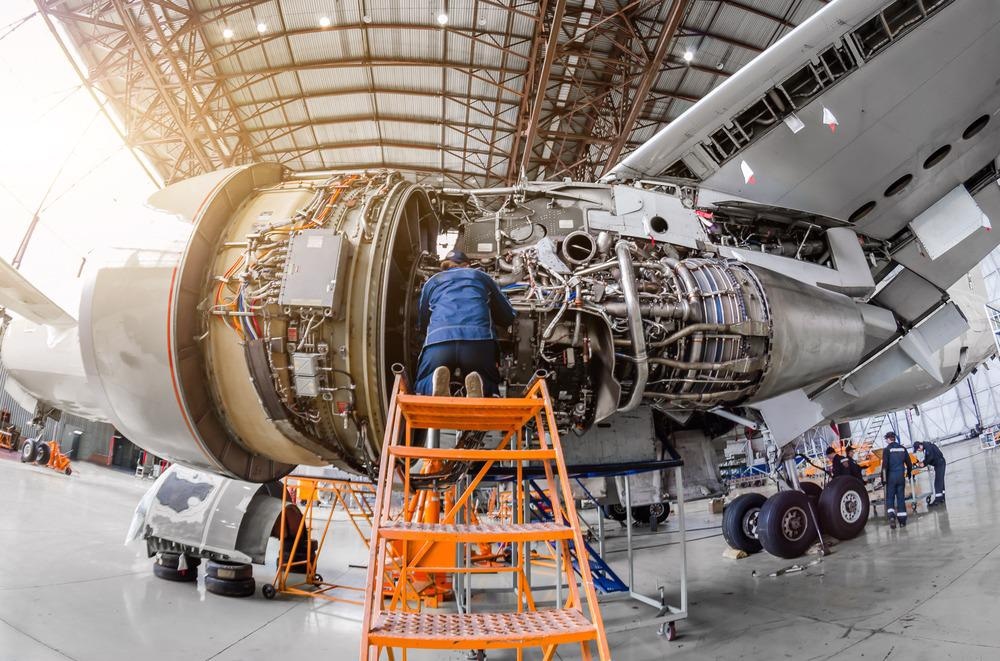
Study: Synthesis and Characterization of Hybrid Fiber-Reinforced Polymer by Adding Ceramic Nanoparticles for Aeronautical Structural Applications. Image Credit: aapsky/Shutterstock.com
This work could lead to the development of advanced nanomaterials which could lead to the innovation of future construction methods for aeronautical structures.
The aeronautical and aerospace industries are among the most important industries in the world. Many companies rely on their ability to transport both products and people around the world at speed. Today, nanotechnology finds application across the aerospace industry at various levels. The main industry objectives align well with the advantages nanomaterials offer, which have begun to replace traditional bulk metals such as steel.
Multiscale Hybridization of Ceramic Nanoparticles
Aeronautical structures attract significant attention due to the importance placed on durability and reliability of component structural parts as well as the complexity of varying loading rates on the overall structure, i.e. the airplane. Thus, thin-walled structures (TWS) using fiber-reinforced polymers (FWPs) are typically used in construction owing to high strength, high corrosion resistance, low weight, low cost, and ease of fabrication.
![Airplane components and functions [24,26].](https://d12oja0ew7x0i8.cloudfront.net/images/news/ImageForNews_57509_16382755176924093.jpg)
Airplane components and functions. Image Credit: Bafakeeh OT et al., Polymers
Multiscale hybridization of ceramic nanoparticles in polymer matrices reinforced with hybrid fibers to produce new polymer composites based on graphene nanoplatelets (GNPs) or carbon nanotubes (CNTs) can provide a wide range of benefits. These benefits will be particularly well-suited in aerospace applications and for fabricating aeronautical structures.
Various aeronautical structural components, which include fuselages, flight controls, landing gear, stabilizers, and wings experience a broad spectrum of varying loads during each flight: to put it simply, during each flight an airplane makes several complex maneuvers, which can cause different modes of loading on the aircraft. Thus, as mentioned, the TWS must be durable and reliable as basic and essential requirements when constructing modern aeronautical structures.
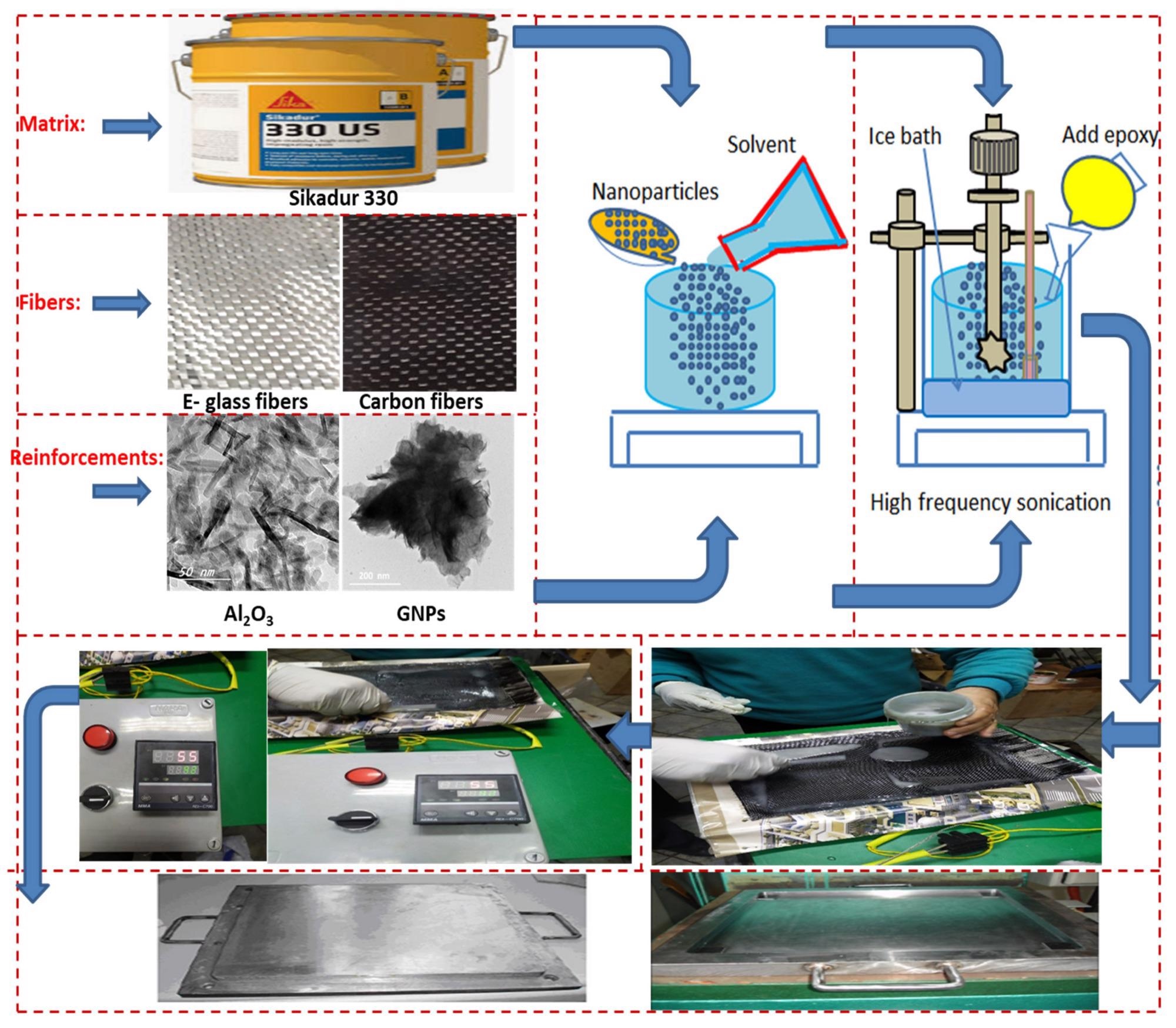
The procedures of dispersion, hand lay-up technique, and compression mold technology.
Note: the images of Al2O3 and GNP nanoparticles were taken from reference. Image Credit: Bafakeeh OT et al., Polymers
However, to meet these fundamental requirements there are a number of limitations and restrictions that present a number of challenges during the design process of airplanes: “These restrictions make aeronautical structural applications some of the most complex products of modern technology,” says co-author Mohamed Abu-Okail, Assistant Professor at the Modern Academy for Engineering and Technology, Cairo, Egypt.
Therefore, the purpose of the aircraft’s usage or intended purpose (passenger or fighter aircraft) must be taken into careful consideration when selecting materials for structural components. Additionally, aircraft regulations, which represent the conditions for acquiring certification for a new aircraft design; and financial factors such as market, environmental, and safety, impact both the design process and choice of materials used.
“Achieving higher performance, efficiency, and reliability with lower costs for aeronautical structures is a difficult request. Therefore, a newly developed composite material characterized by lightweight design, fatigue resistance, high toughness, high durability, and damage tolerance, as well as being environmentally friendly and recyclable, is crucially needed,” explains Abu-Okail.
Synthesized Hybrid Fiber-reinforced Polymer with Ceramic Nanoparticles
The team fabricated a reinforced structural material by combining hybrid fibers comprised of woven carbon and glass fibers with two different ceramic nanoparticles – alumina (Al2O3) and graphene nanoplatelets (GNPs). These materials were selected for their strength and lightweight properties which when combined produce a more advanced engineering material.
Once the team had successfully synthesized hybrid fiber-reinforced polymer with ceramic nanoparticles for specific use in aeronautical and aerospace applications they carefully evaluated the characteristics of the nanomaterial.
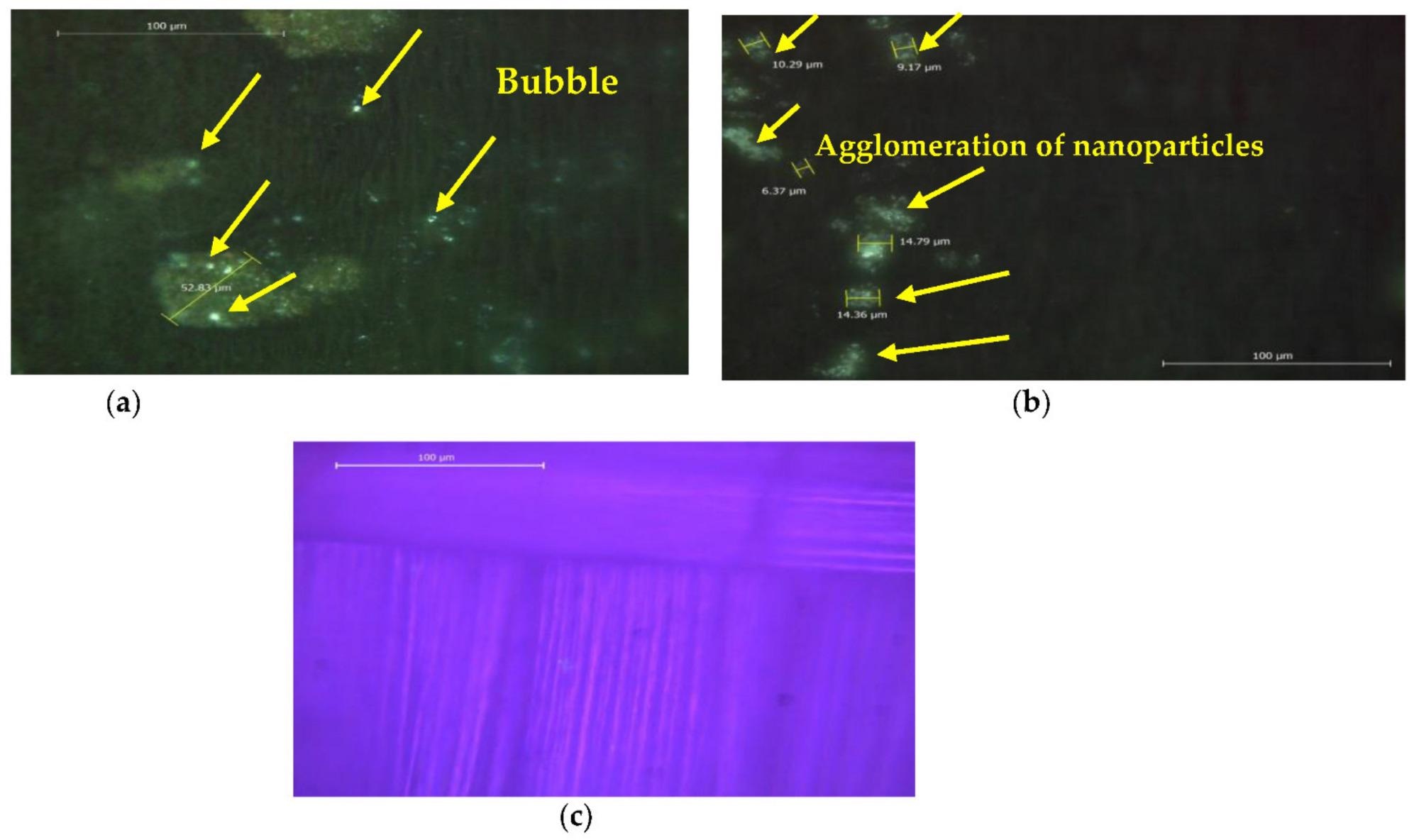
Optical microscope of prepared samples at: (a) S1, (b) S2, and (c) S3. Image Credit: Bafakeeh OT et al., Polymers
The team conducted an analysis of the microstructural observations using optical microscopy (OM), scanning electron microscope (SEM), and X-ray diffraction (XRD), as well as energy-dispersive X-ray spectroscopy (EDS). Mechanical testing was performed using tensile and hardness tests.
Overall, the team discovered that uniform distribution of the GNPs and Al2O3 was achieved in the hybrid matrix which would in effect facilitate the production of successful thin-walled structures with exceptional properties for application in the aeronautical, aerospace, and airplane industries.
In addition to the uniform distribution of the ceramic nanoparticles, the hybrid FRPs demonstrated improved mechanical and microstructural properties that could help improve engineering design capabilities, the durability and reliability of aeronautical structural parts, and overall craft performance.
The researchers concluded they had successfully created and characterized an advanced material for use in aeronautics and aerospace: “These conclusions and findings can be of assistance to produce successful thin-walled structures with extraordinary properties, such as high strength-to-weight ratio, resistance to fracture toughness, fatigue, and damage,” says Abu-Okail.
To date, nanomaterials have been used with relative success in aircraft construction as filler materials to enhance the properties of structural and non-structural polymers. With the development of new advanced hybrid materials, then the industry as a whole can take another step towards meeting its future objectives while ensuring regulations are met as well as allaying other concerns such as the market, safety, and to some extent environmental impact – lighter aircraft use less fuel, therefore, generate less pollution.
References and Further Reading
Bafakeeh OT, Shewakh WM, Abu-Oqail A, Abd-Elaziem W, Abdel Ghafaar M, Abu-Okail M. Synthesis and Characterization of Hybrid Fiber-Reinforced Polymer by Adding Ceramic Nanoparticles for Aeronautical Structural Applications. Polymers. 2021; 13(23):4116. https://www.mdpi.com/2073-4360/13/23/4116
Will Soutter, ‘Nanotechnology in Aerospace Materials’ AzoNano, April 2019 [https://www.azonano.com/article.aspx?ArticleID=3103]
Disclaimer: The views expressed here are those of the author expressed in their private capacity and do not necessarily represent the views of AZoM.com Limited T/A AZoNetwork the owner and operator of this website. This disclaimer forms part of the Terms and conditions of use of this website.