A new breakthrough was considered in the Journal of Materials Science: Materials in Medicine, where tribological characteristics of biodegradable natural Zn and Zn-X (Cu, Li, Ge) alloys were investigated.
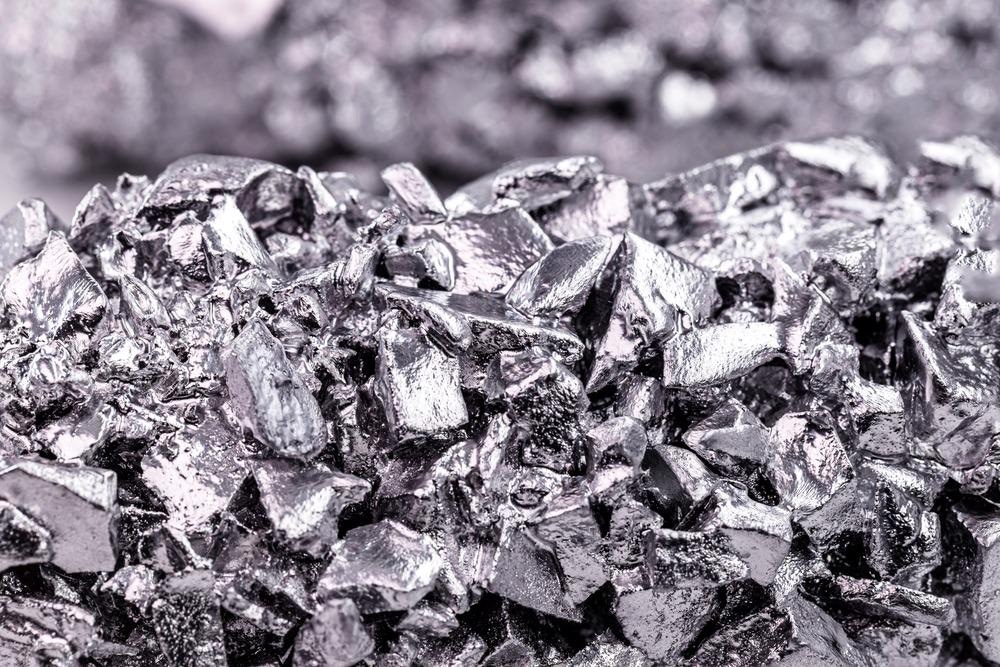
Study: Investigation on tribological behaviors of biodegradable pure Zn and Zn-X Materials in Medicine. Image Credit: RHJPhtotoandilustration/Shutterstock.com
The research discovered that the alloying elements Li and Cu can enhance the friction characteristics of Zn under simulation model body fluid and dry friction situations.
Biodegradable Implant Material
Zinc (Zn) alloys have received increased attention as an effective biodegradable implant material due to their excellent biocompatibility and reasonable degradability. Zn and its composites are predicted to be candidates for medical device components. Metals transplanted in the human body will undoubtedly undergo friction before being completely deteriorated.
XRD patterns of Pure Zn, Zn-0.5Li, Zn-1Cu, Zn-1Ge. Image Credit: Li, H., et al., Materials in Medicine
Friction and wear are important factors that can lead to the failure of medical devices. Even so, there have been few studies on the wear and friction properties of biodegradable Zn-based alloys, with most studies focusing solely on the alloys' mechanical characteristics, degradation characteristics, and biocompatibility. As a result, it is critical to investigate the friction and wear properties of Zn and its alloys.
Biomedical Metallic Materials
Traditional bioinert different metals for load-bearing and bioresorbable metals are examples of biomedical metallic materials. Because of their biodegradability and biocompatibility, biodegradable metals (BMs) are perfect temporary implant components. Many conventional bioinert metals (like Ni-Ti, Ti-Nb, Ti-6Al-4V, and others) are often used in biological applications for bone replacement and heart valves due to their good strength and corrosion resistance.
Conventional bioinert metals that are irrevocably implanted in the muscle, on the other hand, necessitate a second surgery to be removed from patients after transplantation. After implantation, BMs progressively degrade and promote the complete recovery of local tissues. It eliminates the need for a second removal surgery, lowering the patient's medical costs and physical discomfort.
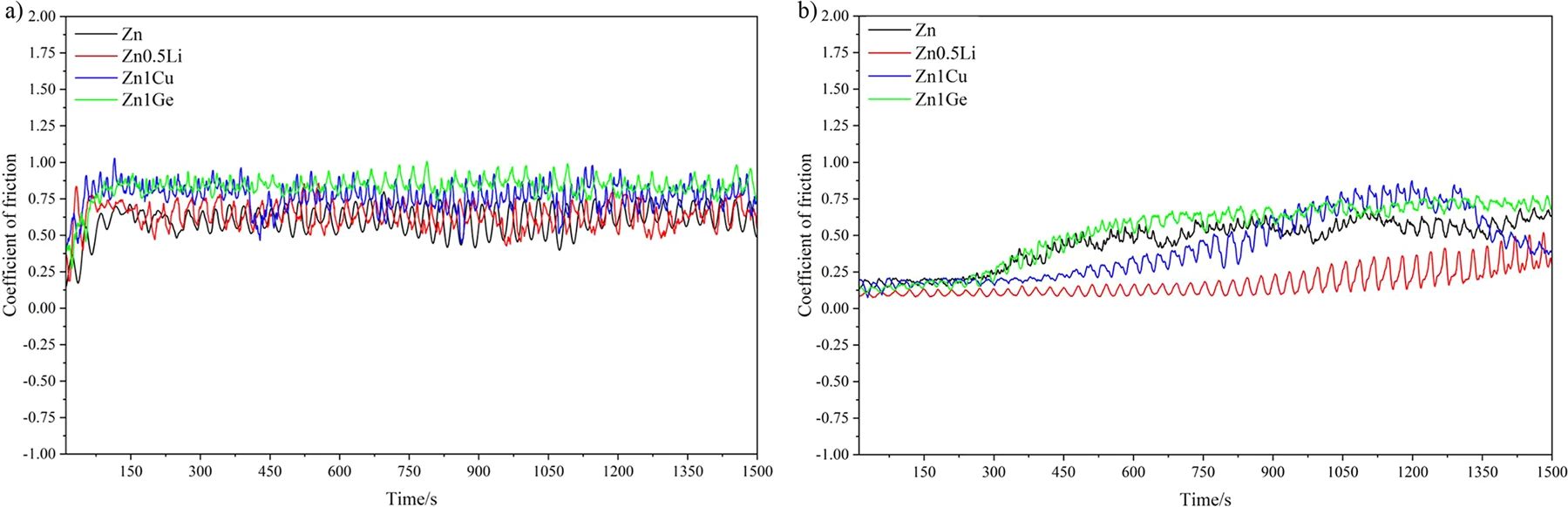
Coefficient of friction vs sliding time of four metals: (a) under dry sliding condition; (b) in simulated body fluids (Hank’s solution). Image Credit: Li, H., et al., Materials in Medicine
Why Tribological Properties are Needed
Micromotion of the bone-implant connection is inescapable in the human body. Wearing materials in the body has a number of negative consequences. Wearing down materials creates abrasive particles that can harm cells and induce cancerous reactions. It can also cause osteolysis, redness, and other unpleasant side effects.
The major reasons for implantation surgery failure are inflammation and bone resorption surrounding the implant material induced by friction with human joints following implantation in the internal organs. As a result, the implant materials must have appropriate tribological qualities to limit wear debris production and avoid inflammation and bone resorption.
Research Process
A multipurpose X-ray diffractometer was used to analyze the sample's phases. After that test, scanned electron microscopy was used to evaluate the structure and chemical components of the phases of the alloy specimens. After the wear and friction test, the three-dimensional morphology of the prepared sample was seen using a white light interfering microscope, and the breadth and depth of the wear tracks were determined.
The electrochemical measurements were performed at 37 °C in Hank's solution using an electrochemical workstation. As the auxiliary electrodes, a platinum electrode was used, a saturated silver chloride electrode was used as the electrode material, and the specimens were used as the working electrode.
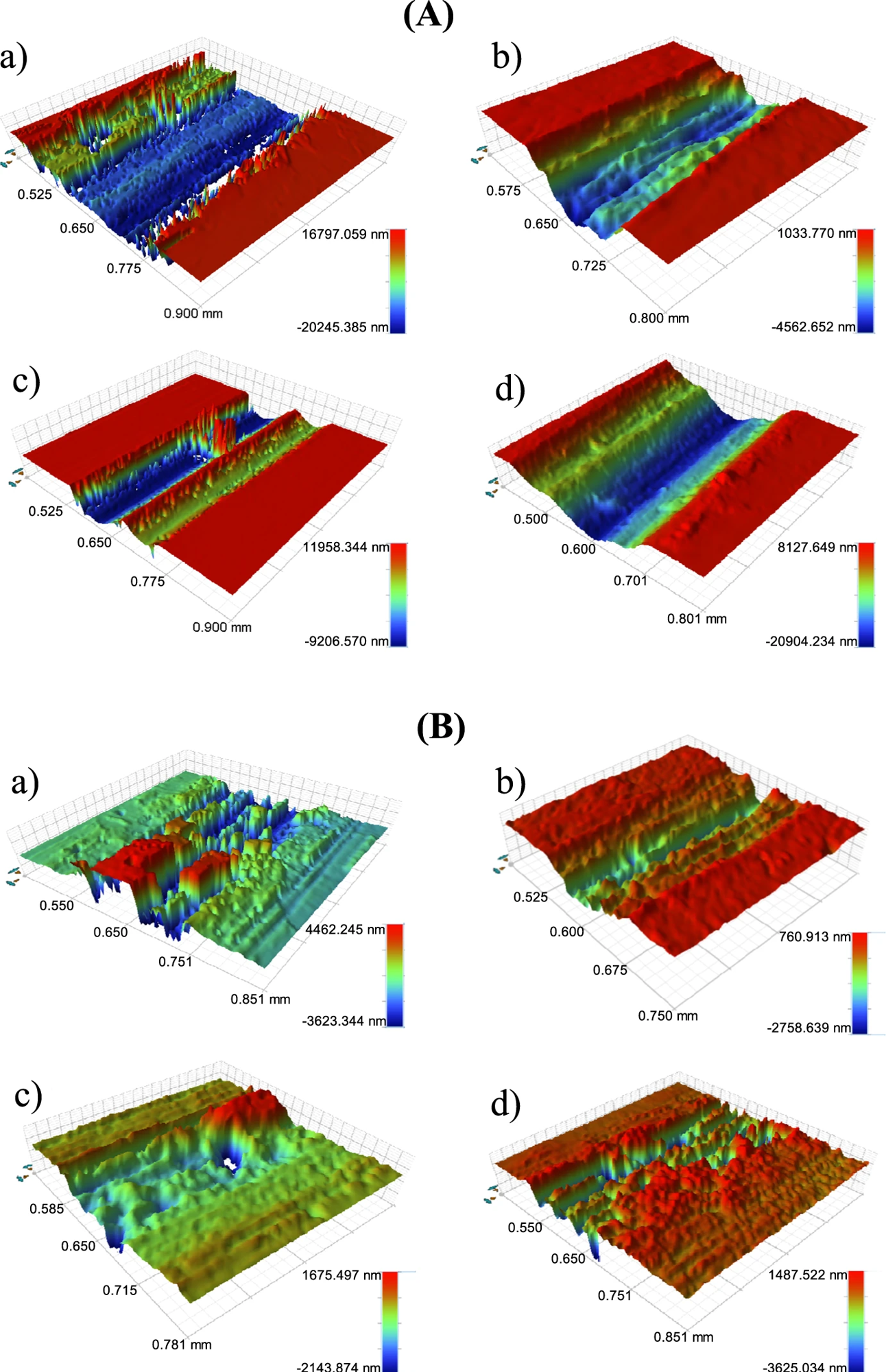
(A) Surface topographies of wear tracks tested under dry sliding condition: (a) pure Zn; (b) Zn-0.5Li; (c) Zn-1Cu; and (d) Zn-1Ge; (B) Surface topographies of wear tracks tested under Hanks’ solution condition: (a) Pure Zn; (b) Zn-0.5Li; (c) Zn-1Cu; and (d) Zn-1Ge. Image Credit: Li, H., et al., Materials in Medicine
Result of Tribological Research
The coefficients of friction of the four materials fluctuated while sliding, as can be shown. The Zn-Li alloy had the lowest friction factor curve of the samples tested. In Hank's method, the amount of the friction coefficient grew with the rise of the test period, and the friction coefficients fluctuation range steadily expanded.
The friction factor of Hank's solution underneath the lubrication condition is lower than that of the friction factor in the dry sliding situation in the long-term friction and wear test. The friction coefficient in Hank's solution, meanwhile, is less stable than in dry sliding friction circumstances. The abrasion lines of all other three Zn-based alloys are thinner and the corrosion is lighter than pure Zn.
In both modeled bodily fluid and dry frictional situations, the inclusion of intermetallic compounds Li and Cu can increase Zn's friction qualities.
The lowest friction factor and best wear resistance are found in the Zn-Li alloy. The wear capacity of Zn and its alloys is smaller under Hank's lubrication conditions than under dry friction circumstances, demonstrating that Hank's solution has a lubricating effect that outweighs its corrosive impact. Friction and corrosion have a synergistic relationship. The alloys in Hank's solution exhibit a tribocorrosion behavior, rather than just single friction or corrosive activity. Corrosion will be accelerated by friction.
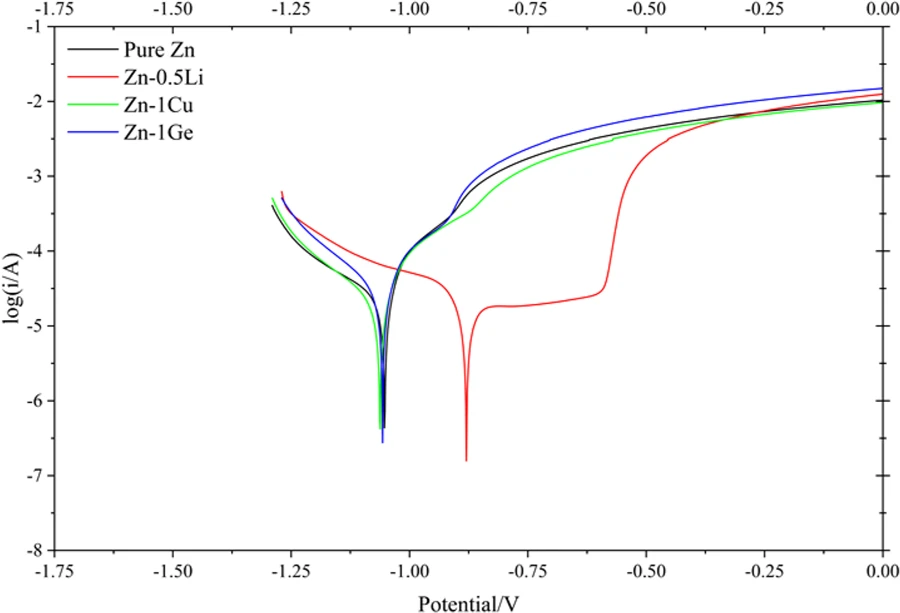
Polarization curves of pure Zn, Zn-0.5Li, Zn-1Cu and Zn-1Ge immersed in Hank’s solution. Image Credit: Li, H., et al., Materials in Medicine
Important Process of Tribological Formed
At first, a corrosion byproduct coating forms on the material's surface, creating a physical barrier that prevents ions from the solution from diffusing into the metal matrix. The surfaces corrosion product coating is lost as the friction proceeds, exposing the surface metal and causing it to corrode. Furthermore, when the metal slides, the wear track in the metal grows wider, the exposed surface grows greater, and the corrosion of the metal grows stronger.
References
Li, H., et al. (2021). Investigation on tribological behaviors of biodegradable pure Zn and Zn-X (Li, Cu, Ge) binary alloys. Journal of Materials Science: Materials in Medicine volume 32, Article number: 149 (2021). Published Online: 04 December 2021. https://link.springer.com/article/10.1007/s10856-021-06625-4
Disclaimer: The views expressed here are those of the author expressed in their private capacity and do not necessarily represent the views of AZoM.com Limited T/A AZoNetwork the owner and operator of this website. This disclaimer forms part of the Terms and conditions of use of this website.