A frequently used method of powder granulation in metal or ceramic powder manufacturing is spray drying. Slurries composed of solid particulates, polymer additives e.g. lubricants and surfactants, and other additives are typically milled and homogenised in a liquid medium, for example ethanol or water, and are then spray dried into powder agglomerates.
The purpose of and intent behind spray drying is to create free flowing, highly consistent powders to enable easy and highly reproducible die-filling to enable tablet compaction and rapid automation. It is therefore clear that powder flowability and performance are of critical importance in a powder metallurgy based production plant.
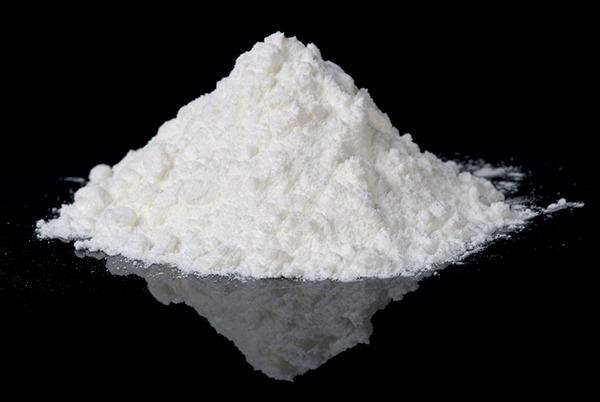
Image Credit: Freeman Technology
The recycling of materials is finding ever increasing importance in the world today, and the powder metallurgy industry is no exception. It was observed, however, that recycled spray-dried powders (produced from recycled cemented carbide cutting tools) behaved differently during manufacturing, compared to spray dried powders manufactured from new, ‘as-synthesised’ raw materials. Hence, a detailed investigation of new or 'as synthesized' powders compared to recycled powders was conducted.
In this presentation, Dr. Chris Freemantle (Sr. Materials Engineer at Pilot Tools (Pty) Ltd) explores the causes of the behaviour differences when using recycled powders, the interconnectedness of slurry and powder rheology and the potential impact that the use of recycled powders can have on a manufacturing process. Ultimately, this case study demonstrates the power and utility of powder rheology, a technique yet to be fully embraced by the powder metallurgy industry.
The investigation made use of microscopy and microstructural analysis, slurry rheology, zeta potential measurements and powder rheology using the FT4 Powder Rheometer®.