In a recent study published in the journal Additive Manufacturing, researchers from Taiwan developed a new method to fabricate 3D printed conductive structures using metal fillers containing photocurable resin and digital light processing (DLP) technique.
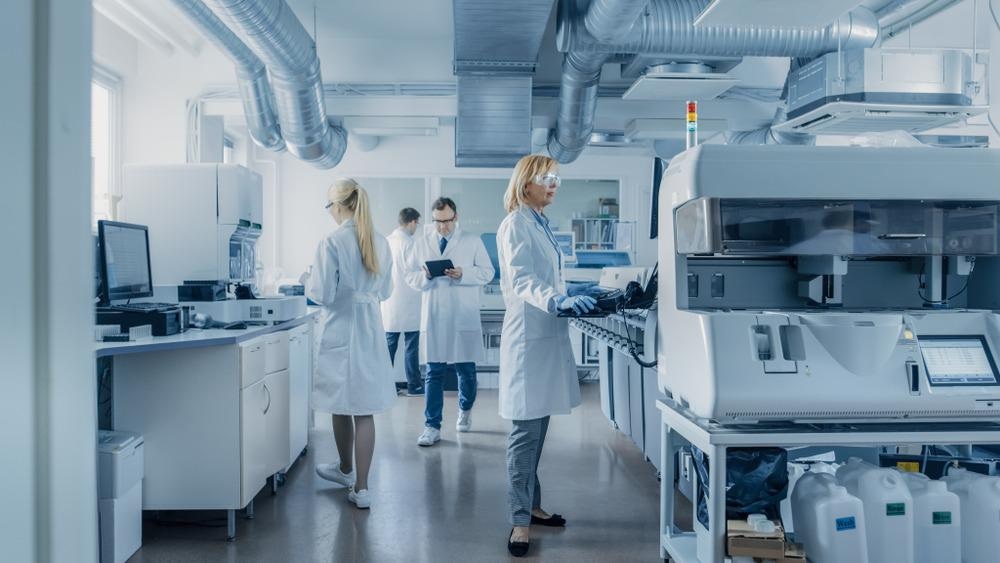
Study: Photocurable resin for 3D printed conductive structures. Image Credit: Gorodenkoff/Shutterstock.com
Researchers used silver-coated copper flakes (AgCu) and silver nanoparticles (Ag NP), which are suitable for DLP due to their low UV shielding effect and minimal printing derivation, with photocurable acrylic resin. Also, carbon nanotubes (CNT) were added to increase the dispersivity and prevent the sedimentation problem of metal fillers in the resin. The prepared structure exhibited a conductivity up to 1000 S/cm without sintering.
Metal Fillers in Photocurable Resin
In 3D printing of photocurable resins, the UV light projected from DLP is exposed to a pool of photocurable resin to fabricate 3D structures with a layer-by-layer approach. Also, fibers, fillers, and polymers have been incorporated in photocurable resin to enhance the mechanical, electrical, magnetic, and optical characteristics of the 3D printed structures.
Conductive structures usually incorporate fillers such as metal nanoparticles, CNT, and conductive polymers. The low electronic conductivity of metal filler-based printed structures owing to a low filling ratio (8-12%) is resolved by heating the printed objects at a high temperature (above 950°C for copper) to remove the plastic resin and to sinter the metal powder to form a solid metal path, which adversely deforms the shape.
Consequently, the filler ratio can be improved by using more metal fillers, but with an increase in metal filler content, the scattering and absorption of light, and the viscosity of the resin paste also increases, which lowers UV light penetration/curing depth and increases the possibility of reflow during the DLP printing technique that distorts the printed structure.
Further Reading: What Does 3D Printed Skincare Have to Offer?
The low dispersivity and sedimentation of high metal filler-containing resin can be alleviated by adding CNT to the mixture paste. Also, the high aspect ratio of CNT improves the mechanical properties and enhances the conducting network without requiring sintering.
About the Study
In this study, researchers used acrylic as the photocurable resin, AgCu flakes, and Ag NP for the metal fillers. They prepared the mixed resin solution/paste by adding 15 wt% of ethylene glycol, 7.428 g of AgCu flakes, 5 wt% single-walled CNTs, and 8 mg of photo-initiator Irgacure-819 into 80 wt% of commercial acrylic resin followed by ultrasonication and magnetic stirring for an hour.
Subsequently, a DLP 3D printer with UV light of 405 nm wavelength and 2.5 mW/cm2 intensity was used for the curing up to the thickness of 25 µm. Finally, the prepared samples were characterized using a rheometer, UV-vis spectrophotometer, Fourier-transform infrared (FTIR) spectroscopy, scanning electron microscopy (SEM), X-ray diffraction (XRD), digital micrometer, and a multimeter.
Observations
The XRD pattern showed that AgCu flakes contained only copper and silver elements without any metal oxide because the silver shell prevented the oxidation of copper. The UV-visible light spectra obtained from the spectrophotometer indicated that both metal fillers demonstrated strong light scattering or shielding and absorbance, which was much higher than the pristine resin. The highest absorption peak of value ~400 nm was recorded for Ag NP, which was close to the light source (i.e., 405 nm) during DLP.
Moreover, the Ag NP-resin printed samples showed large surface roughness, much smaller cured thickness, and high thickness variation than pristine resin samples, whereas AgCu flake-resin samples showed good area control, lesser thickness deviation, and better electrical conductivity than Ag NP-resin samples due to the formation of a percolating network of metal fillers in the printed structure.
Further Reading: Energy Absorption Properties of Two 3D-Printed Lattice Structures
The addition of CNT in a concentration below 0.0875 wt.% in AgCu-resin samples, slowly increased the yield stress, whereas beyond that the yield stress increased rapidly. Additionally, the conductivity of the samples with CNT was 10 to 100 times better than those made from pristine AgCu-resin, indicating a much better uniformity and suspension stability of metal fillers in the resin.
Samples with 70 wt% AgCu concentration in resin reached a high conductivity of 1000 S/cm, whereas for resin with more than 70 wt% AgCu, the resin mixture became gel-like and was not suitable for 3D printing.
Conclusions
In this study, researchers prepared 3D conductive tracks for printed circuit boards using photocurable acrylic resin and AgCu flakes as metallic fillers. Resins with a low filling ratio (8-12%) of metallic fillers required sintering, whereas resins with a filling ratio above 50% required a thickening agent such as CNTs for improved dispersivity.
For this specific materials and arrangement setup, metal fillers up to 70 wt% were easily well-dispersed in the resin and remained fluidic for the entire 3D printing process. The high filling ratio resulted in a high solid fraction and demonstrated a high conductivity of 1000 S/cm without requiring an energy-intensive sintering process. Hence, this method is suitable for the simple and cost-effective fabrication of metallic filler-based conductive 3D printed structures.
Reference
Tsai, S., Chen, L., Chu, C., Chao, W., Liao, Y., Photocurable resin for 3D printed conductive structures, Additive Manufacturing, Volume 51, 2022, 102590, ISSN 2214-8604, https://www.sciencedirect.com/science/article/pii/S2214860421007375
Disclaimer: The views expressed here are those of the author expressed in their private capacity and do not necessarily represent the views of AZoM.com Limited T/A AZoNetwork the owner and operator of this website. This disclaimer forms part of the Terms and conditions of use of this website.