This article is based on a review paper on the use of magnesium (Mg)-based alloys in orthopedic surgery, which is openly accessible in the journal Materials. The key outlines of this paper are the importance of Mg in orthopedic implants, major alloying elements in Mg-based alloys and their physicochemical properties, effects on osteogenesis and angiogenesis, fabrication methods, animal testing results, and some of the currently used commercial Mg-alloys.
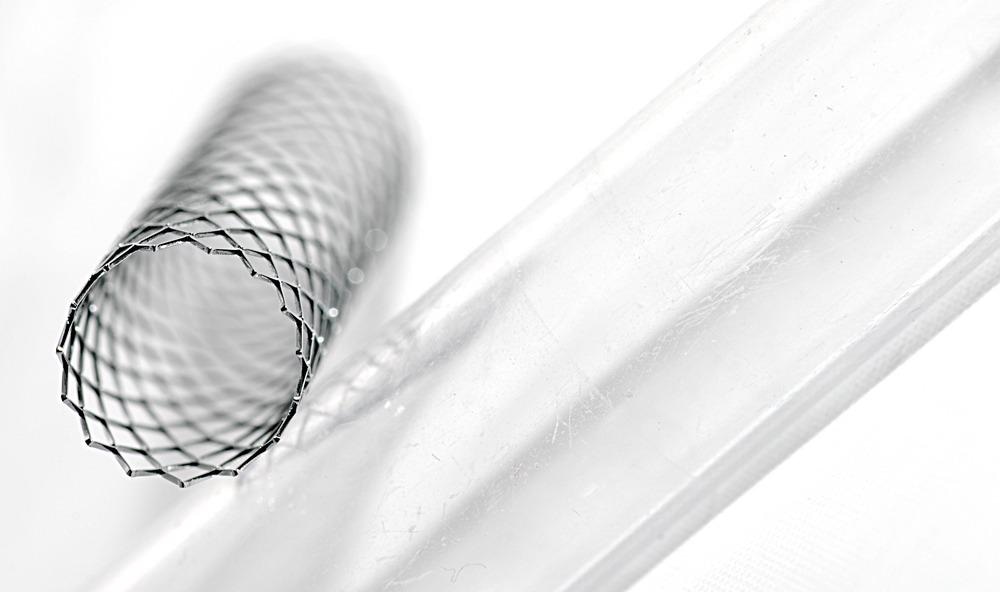
Study: Magnesium-Based Alloys Used in Orthopedic Surgery. Image Credit: Floris Slooff/Shutterstock.com
Mg-based Biomaterials in Orthopedic Treatment
Magnesium (Mg) is an essential mineral for humans and animals. Humans need about 250-350 mg of Mg on a daily basis, out of which a major portion is excreted through the gastrointestinal (GI) tract and renal system. Meanwhile, about 70-180 mg of it is absorbed by the human body for cellular fluids, kidneys, and bones. Mg is both biocompatible and biodegradable in the human body that promotes bio-responses at cellular and molecular levels.
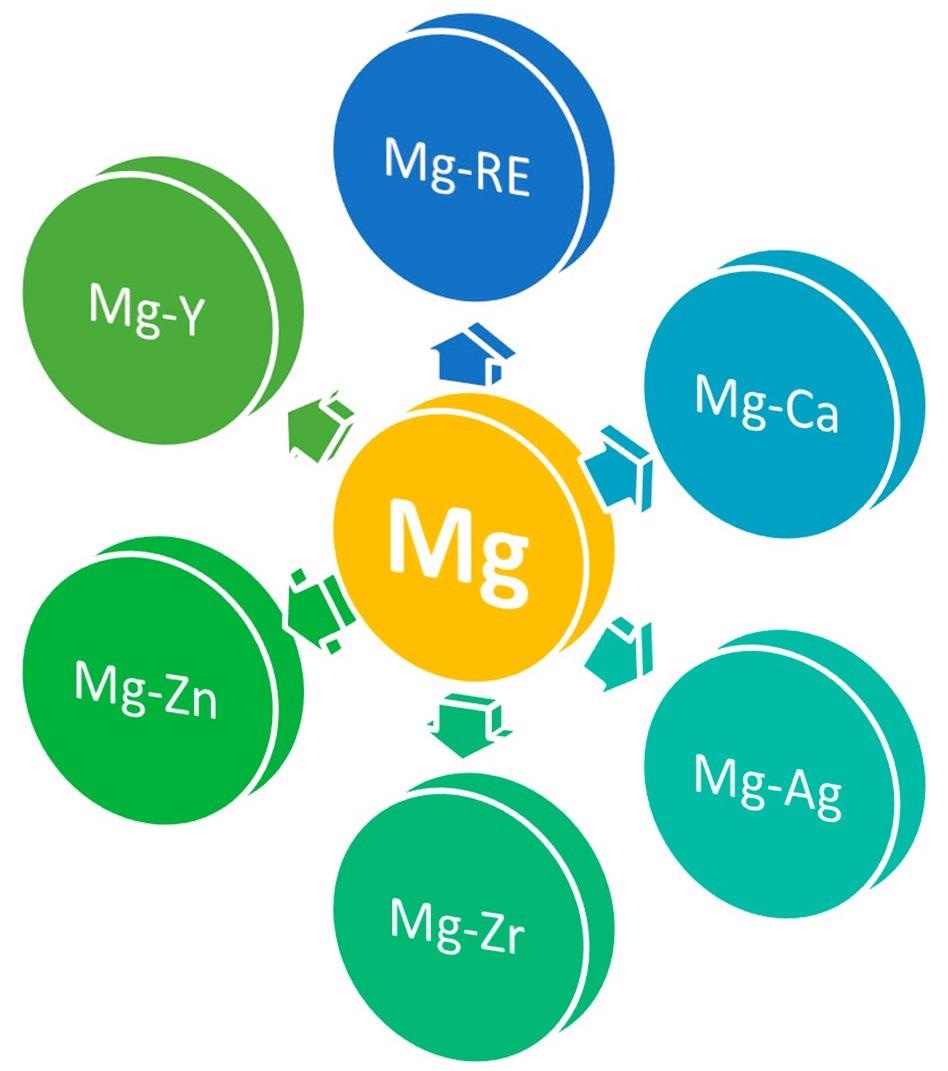
The main six Mg-based binary alloys for orthopedical applications. Image Credit: Antoniac, I. et al., Materials
Orthopedic implants are used to compensate for bone or soft tissue losses due to traumas, cancers, infections, amputations, and inflammations, either permanently or temporarily, until they recover. Each prosthetic is either osteogenic (bone generating) or osteoclastic (bone removing).
Temporary implants are needed to be removed from the body after a certain period. Hence, in such situations, biodegradable implants are handy as they eliminate the requirement of a second surgery to remove the planted implants.
Mg exhibits an elastic modulus of ~45 GPa, which is close to that of the human bone (15-25 GPa). Similarly, Mg alloys have a density between 1.74 and 1.84 g/cm3, which is close to that of bone (1.8–2.1 g/cm3), opposing the stress shielding effect. Additionally, its degradation products are non-toxic and osteogenic.
However, it has a low standard electrode potential (SHE) of -2.372 V that makes it prone to corrosion in an aqueous medium and its very low compressive yield strength of 65-100 MPa makes it inappropriate for load-bearing implants. Human bones have a compressive yield strength of 130-180 MPa.
Mg-Alloy Compositions and Characteristics
Binary Mg-alloys are usually Mg-yttrium (Y), Mg-zinc (Zn), Mg-calcium (Ca), Mg-silver (Ag), Mg-zirconium (Zr), and Mg-rare earth (RE). Mg-Zn alloys with a Zn concentration of up to 3% are used to decrease the corrosive effect of iron and nickel impurities. Similarly, Mg-Mn alloys with a concentration up to 2 wt.% improve the ductility, mechanical strength, and alloy viscosity.
In Mg-Ca alloys, Ca forms Laves-type intermetallic phases such as Mg2Ca. These precipitation hardened solid solutions increase creep resistance, refine the grains, and strengthen the grain boundaries. Zr is also a grain refiner and reduces the corrosive effect of Fe impurities. The most commonly used RE element in Mg alloys is Y, which is highly soluble in Mg, followed by strontium (St), gadolinium (Gd), neodymium (Nd), and cerium (Ce).
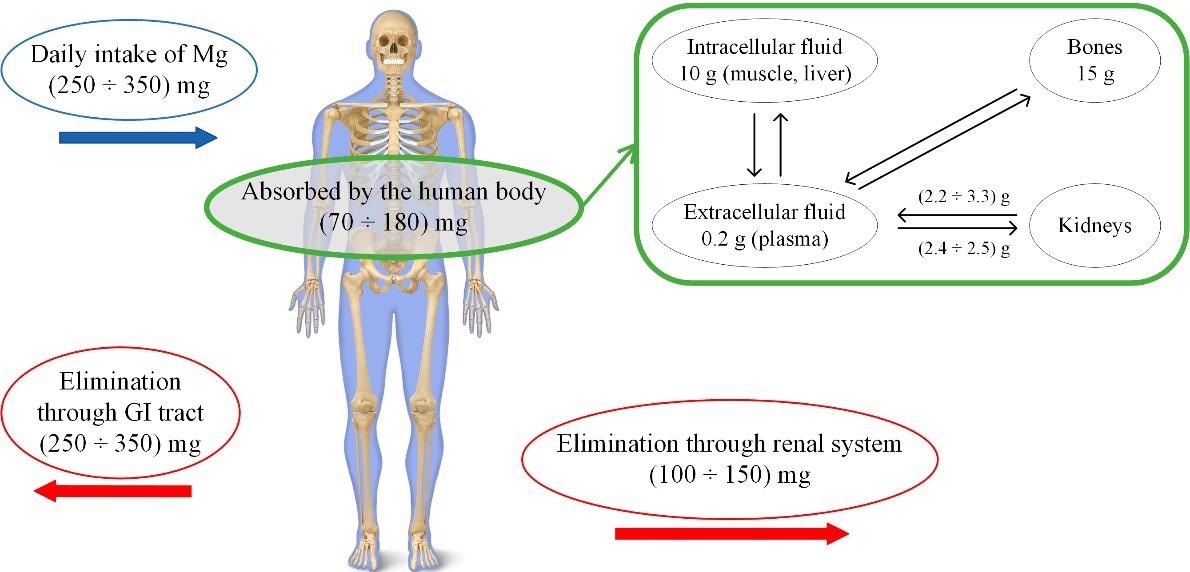
Absorption phenomenon and excretion equilibrium of Mg in the human body system. Image Credit: Antoniac, I. et al., Materials
Mg-Alloy Fabrication Process
Casting methods such as high-pressure gravity casting, squeeze casting, stir casting, and sand casting are the easiest and cheapest methods to fabricate Mg-based alloys; however, they may lead to phase segregation and unwanted preferential orientation. Meanwhile, powder metallurgy has high precision and exhibits no preferential orientation due to homogenous mixing and a high mass transport rate.
The Mg powders are obtained through mechanical crushing, atomization of molten metal, electrolysis, and evaporation-condensation. The last of the Mg alloy manufacturing method is laser-based additive manufacturing, which is beneficial for rapid prototyping, and one of the most sought techniques used by surgeons nowadays.
In vivo animal testing of Mg Alloys in mice, rabbits, rats, miniature pigs, beagle dogs, and goats were performed. The WZ42 alloy demonstrated adequate biocompatibility, no accumulation of Mg, and normal fracture healing.
The WZ43 alloy exhibited a four times slower degradation rate when immersed in SBF solution. The coated implants exhibited higher strength retention compared to the uncoated ones after 12 weeks. The brushite-coated Mg-Nd alloy demonstrated a slow degradation rate and superior osteoinductivity. Similarly, MAGNEZIX® (Mg-Y-RE-Zr), Syntellix AG, and RESOMET™ (Mg-Ca alloy) are some of the most commonly used Mg-based alloys in orthopedic surgery.
![Schematic illustration of the corrosion behavior of Mg in the commonly used media [75].](https://d12oja0ew7x0i8.cloudfront.net/images/news/ImageForNews_58124_16439712894947495.jpg)
Schematic illustration of the corrosion behavior of Mg in the commonly used media. Image Credit: Antoniac, I. et al., Materials
Conclusions and Future Scope
Mg-based alloys are suitable temporary orthopedic implants owing to their biocompatibility and biodegradability. Additionally, due to similar mechanical properties to that of human bone, they exhibit a low-stress shielding effect. Moreover, their osteogenic properties make them a suitable candidate for small-scale orthopedic implants.
Disclaimer: The views expressed here are those of the author expressed in their private capacity and do not necessarily represent the views of AZoM.com Limited T/A AZoNetwork the owner and operator of this website. This disclaimer forms part of the Terms and conditions of use of this website.
Source:
Antoniac, I., Miculescu, M., Mănescu, V., Stere, A., Quan, P.H., Păltânea, G., Robu, A., Earar, K. Magnesium-Based Alloys Used in Orthopedic Surgery. Materials, 2022, 15, 1148. https://www.mdpi.com/1996-1944/15/3/1148