In a recent study posted to the preprint* server Research Square as a submission to Functional Composite Materials, researchers analyzed the mechanical properties of a stretchable conductor consisting of braided carbon nanotube yarns (CNTYs) wrapped around an elastomeric core.
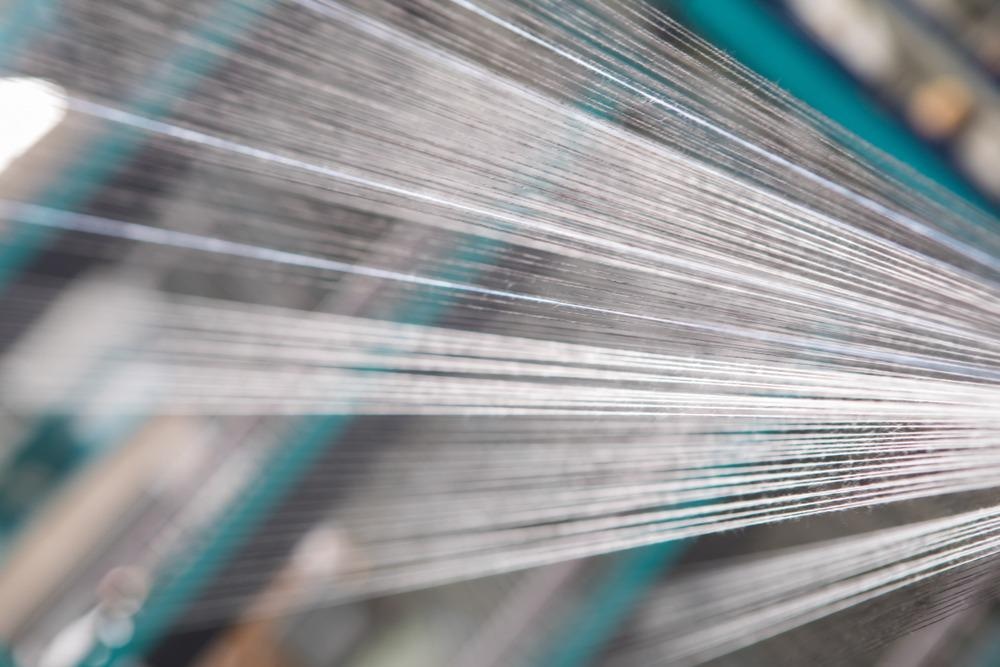
Study: Stretchable Conductive Materials Based On Braided Cnt Yarns On Elastomeric Core. Image Credit: Hakan Tanak/Shutterstock.com
The researchers investigated the ideal stress-strain behavior and minimum resistivity conditions for the prepared composite wire that included parameters such as initial braiding angle, number of pitches, critical strain, and friction between the CNTY braid and the elastomeric core. The fabricated stretchable conductive composite wire exhibited a resistivity of 9.05x10-4 ohm.cm, which remained constant until the tensile loading failure under cyclic loading.
Background
Braided cables are not new in the market. Metal yarn braided cables have been used for two primary reasons viz. to protect the cable from electromagnetic interference (EMI) and to increase the mechanical strength and flexible life of a cable. The latter requirement is also true for improving the flexibility and mechanical strength of carbon nanotube (CNT) yarn-based wires. Meanwhile, in today’s fast-paced human lives, stretchable cables are becoming essential and highly in demand owing to their increased shelf-life and high reliability.

Geometric relations for a helical braid. Image Credit: Bar, A. et al., Functional Composite Materials
Stretchability can be incorporated into conductors by two methods, either by using conducting elastomeric polymers or by using a composite of elastomers and rigid conducting materials. The conducting polymers have yet to undergo more developments to reach a conductivity value similar to that of metals and CNTs.
Meanwhile, CNTs are not only excellent electric conductors but also exhibit excellent mechanical and thermal properties such as high stiffness, high thermal stability, high aspect ratio, high elasticity, corrosion-resistance, and being lightweight. Hence, braided CNTY wrapped elastomeric composites can withstand large linear and transverse deformations without requiring any change in the geometry of the conductor.
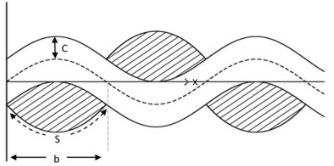
Yarn crossover model for a diamond tubular braid. Image Credit: Bar, A. et al., Functional Composite Materials
About the Study
In this study, researchers fabricated a CNTY braided silicone rubber-based elastomeric core and evaluated its mechanical, electrical, and thermal properties. The model assumed the following conditions: the braiding had open gaps, each yarn followed a helical path, the circular cross-section of the core and diameter of the yarn was unaffected under the tensile load, the core was an anisotropic material, and the radial stress was uniform.
Three modes of compression of CNTY to the elastomeric core were considered. In mode I, the braid and core had no contact. In mode II, the friction and normal stresses developed due to the radial compression of the braid onto the core was considered. Finally, in mode III, the core was squeezed to its maximum limit before failure.
Observations
In mode I, from the strain (εr) vs variation of core diameter and braid diameter (D/D0) curves, it is evident that for initial braiding angles lower than 55◦ the intersection occurred at small axial strains, whereas for braiding angles above 55◦, the intersection occurred at larger axial strains. After the intersection point, the core was compressed by the yarns and the rubber squeezed out of the braid open gaps. Hence, under equal tensile load, the core was squeezed out at different deformation values based on the braiding angles.
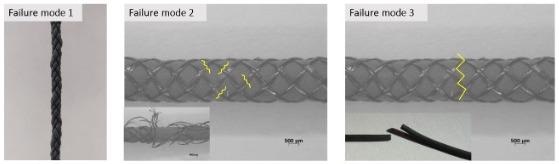
Three failure modes. Image Credit: Bar, A. et al., Functional Composite Materials
In mode II, the increase of the initial braiding angle from 45° to 55° increased the strain of the hybrid structure from 0.4 to 0.7, indicating that the braiding angle was the limiting factor for the total strain of the composite. Also, the friction force increased significantly with the increase in the number of yarns. For the initial braiding angle of 47°, the core started to squeeze out at a strain of 16%.
In mode III, the braid was interlocked with the core and the braid angle remained constant. The modulus of elasticity was the deciding factor in determining which one will fail first, the core, or the yarn.
Furthermore, the stress-strain curve revealed that, for the initial braiding angle of 47°, a difference of 40% elongation before strain lock was observed for coefficients of friction value of 0.001 and 0.5. Hence, friction had a significant role in determining the strain lock point.
Conclusions
To conclude, the researchers of this study fabricated an elastomeric rubber core braided with CNTY to obtain a stretchable conducting composite and studied its mechanical, electrical, and thermal behavior under axial and transverse loading.
During mode II compression, the initial braiding angle of the yarn and the friction between yarn and core had a significant role in determining critical strain value at the interlocking state. After the interlocking, the elongation stopped and the failure mechanism started. The failure point was dependent upon the tensile load, elastic moduli of yarn and core, number of yarns, and diameters of yarn and core.
*Important Notice
Research Square publishes preliminary scientific reports that are not peer-reviewed and, therefore, should not be regarded as conclusive, guide clinical practice/health-related behavior, or treated as established information.
Disclaimer: The views expressed here are those of the author expressed in their private capacity and do not necessarily represent the views of AZoM.com Limited T/A AZoNetwork the owner and operator of this website. This disclaimer forms part of the Terms and conditions of use of this website.
Source:
Bar, A., Mead, J., Dodiuk, H., et al. Stretchable Conductive Materials Based On Braided Cnt Yarns On Elastomeric Core, Functional Composite Materials, 28 January 2022, PREPRINT (Version 1) available at Research Square. https://www.researchsquare.com/article/rs-1292460/v1