Fused deposition modeling is a 3D printing technology that has been explored for several industrial applications over the past few years. Writing in SN Applied Sciences, a team of researchers has presented a trial to convert a polymer fused deposition modeling 3D printer to print clay materials for ceramic devices.
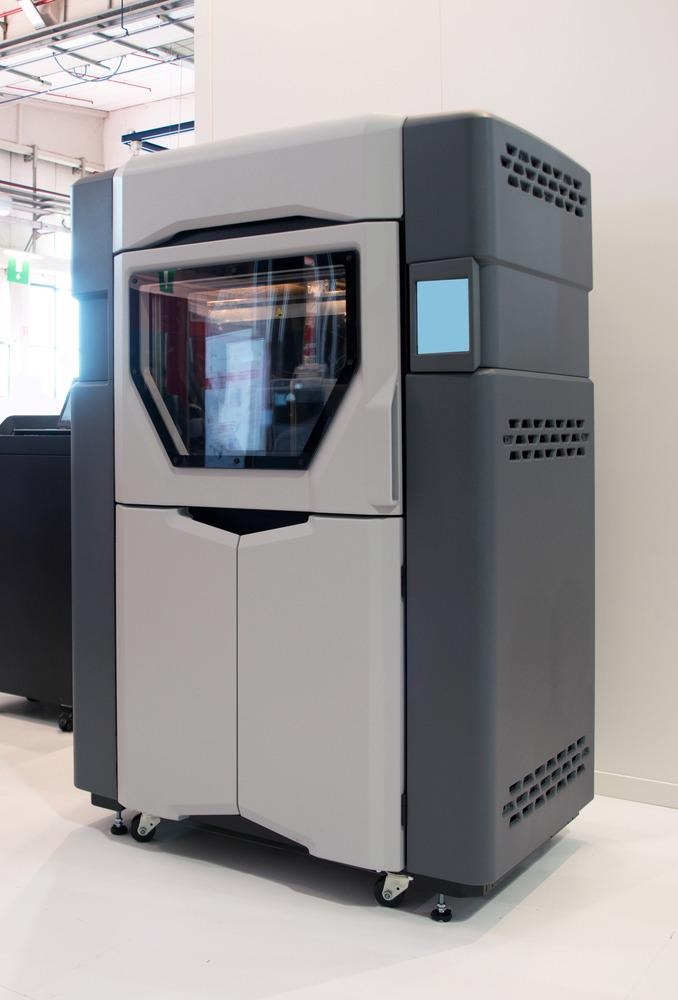
Study: A trial to convert a polymer FDM 3D printer to handle clay materials. Image Credit: Moreno Soppelsa/Shutterstock.com
Ceramic Devices
Ceramic devices are used in several industries. Ceramic clay is used in many dielectric products such as vehicle sensors, medical sensors, and engineering devices. Specialized technologies are used to produce these devices, and there are several considerations that govern the design of ceramic devices.
Forming is a crucial step in the manufacturing process as it is the foundation of designing ceramic products. Traditionally, the main forming methods for ceramic product design are molding, handcrafted forming and, more recently, 3D printing (additive manufacturing.)
In handcrafted forming, the ceramic device is hand thrown and formed in a plaster mold, relying on the expertise and aesthetic perception of workers. Alternatively, the model can be completely formed using a mold. Slip casting techniques can be utilized to form a ceramic product with thin walls, or small parts of the product can be pressed into the mold by hand.
3D printing, which builds a product based on a CAD model, is more precise than handmade products. Materials are extruded from a nozzle, which has a precisely controlled position at all times. The amount of product and extrusion time are also tightly controlled. Furthermore, the high-density ceramic slip is highly suited for indirect three-dimensional printing of functional products.
Flowchart of the 3D process of ceramic manufacture by slip. Image Credit: Chaari, M.Z, et al., SN Applied Sciences
3D Printing Ceramic Devices from Clay Materials
Several additive manufacturing technologies have been developed in recent years for printing clay materials for ceramic products. Products with complex geometrical shapes can be printed from a three-dimensional digital model. Clay can be extruded and then heated and hardened, like a handcrafted product.
Layer-by-layer printing is the main method for 3D printing. Clay paste is compressed by the printer and deposited in layers according to software instructions. The principal difference between 3D clay printing and polymer printing is that this process does not require a heated tip on the extrusion nozzle. 3D clay printing techniques have been used widely in the design of products such as sensors and dielectric ceramic antennas.
Several studies have been published in the last 10 years on clay additive manufacturing. WASP, an Italian 3D printer manufacturer, developed a Delta-3D printer that possesses a nozzle with a greater degree of freedom in 2014. In 2019, the feasibility of using a modified fused deposition modeling 3D printer for the printing of carbon-fiber-reinforced polymer composites was investigated by Rarani et al.
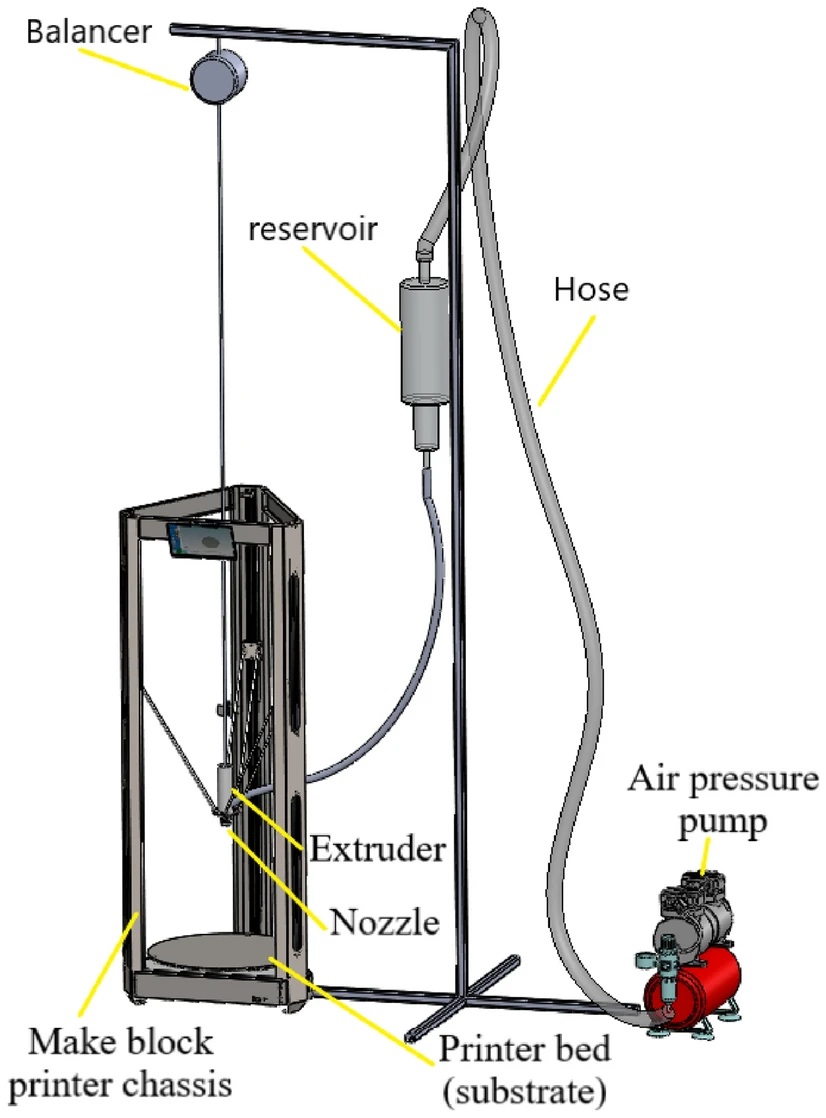
Primitive concept design for 3D printer ceramic after conversion. Image Credit: Chaari, M.Z, et al., SN Applied Sciences
The Study
Based on previous studies in the field of clay additive manufacturing, the authors behind the new study in SN Applied Sciences have demonstrated a method for 3D printing clay materials using a modified polymer fuse deposition modeling 3D printer. The authors have designed a dedicated extruder to control the flow of the material slip.
The proposed fuse deposition modeling 3D printer design is cheap, simple, and easy to construct in a laboratory. The prototype can be used to construct a multitude of dielectric ceramic devices for antennas, sensors, and several different components with high precision and efficiency without the need for a complicated and costly 3D printer clay. The thermal and electrical conductivity of the printed ceramic devices depends on the clay material’s physical properties.
The study has focused on the development of a 3D clay printer with two main research targets. These are the printed product’s material properties and the design of the 3D printer’s dispensing mechanism. The work demonstrated the effect of nozzle size in printing tests and provided the optimum slicing configuration and air pressure for efficient printing of parts.
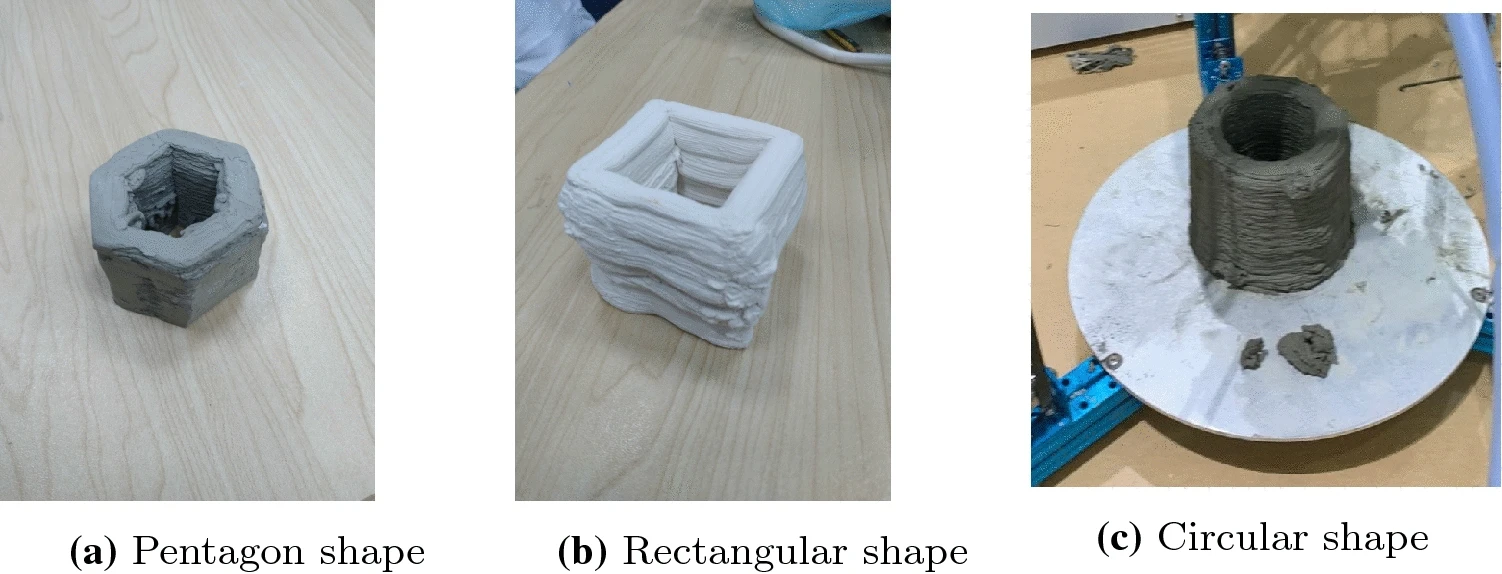
Samples fabricated by additive manufacturing of clay. Image Credit: Chaari, M.Z, et al., SN Applied Sciences
WASP ceramic slurry was selected as the raw material for printing with liquid deposition modeling in a two-step dispensing technique that utilized an Archimedes screw and air pressure. Different shapes constructed out of clay were produced using the proposed process with water-to-clay ratios ranging from 0.57 to 0.69. The print head mechanism, material properties that made them suitable for putty, and how the slurry is extruded were evaluated. Finally, samples were dried for 24 h at average temperatures and then exposed to 1000 oC for 1 hour to stress-test them.
The authors have identified that in practice, printing times and cost of clay material additive manufacturing may vary, and they have stated that future research will involve integrating a drying system into the printer to improve the equipment’s yield. Additionally, converting the fuse deposition 3D printer into a liquid deposition modeling 3D printer could confer benefits in terms of cost and ease of manufacturing.
Further Reading
Chaari, M.Z, Abdelfatah, M & Loreno, C (2022) A trial to convert a polymer FDM 3D printer to handle clay materials [online] SN Applied Sciences 4 68 | link.springer.com. Available at: https://link.springer.com/article/10.1007/s42452-022-
Disclaimer: The views expressed here are those of the author expressed in their private capacity and do not necessarily represent the views of AZoM.com Limited T/A AZoNetwork the owner and operator of this website. This disclaimer forms part of the Terms and conditions of use of this website.