Manufacturing Chemist Live is a conference designed to highlight the current standards and regulations affecting the pharmaceutical industry. It also reviews the latest production protocols. The event taking place on the 25-26 May 2022, in Birmingham, UK.
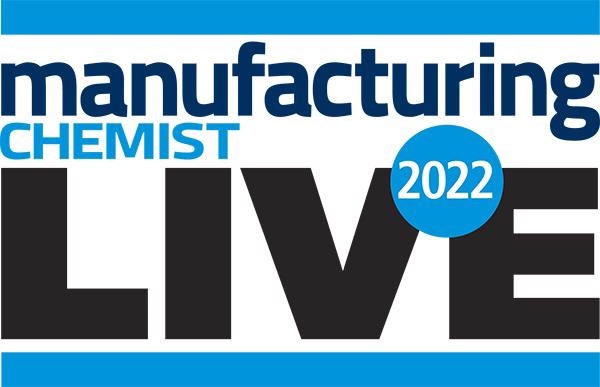
Image Credit: Freeman Technology
Please join Jamie Clayton, Operations Director from Freeman Technology, for “Investigating the Influence of Powder Flow Properties on DPI Dosator Performance” on May 25 at 16:15 BST.
Due to the small particle size of most Active Pharmaceutical Ingredients (APIs) for Dry Powder Inhalers (DPIs), the bulk powder tends to be highly cohesive. An excipient, for example lactose monohydrate, is required as a transport medium for the API. As the drug formulation is ejected from the inhaler the carrier is stripped away as the API continues to the deep lung. The selection of the carrier excipient will not only influence the ejection of the powder from the inhaler, and subsequent detachment of the API, but also the filling of capsule and blister packs during the manufacturing process.
Dosator technology is routinely used to dispense controlled but miniscule quantities of API. Dosators operate by being inserted into the powder bed, which forces powder into their cavity. Dosators are suited to a limited range of powders, demanding the need to match powder properties to dosator design.
In this presentation, Freeman Technology investigates the relationship between excipient and dosing performance. Five grades of lactose with varying particle sizes were processed through a lab-scale dosator (3P Innovation, Warwickshire) using outlets of progressively smaller size. For each combination of dosator outlet size and excipient, the standard deviation was measured for target doses of 50 mg. This was repeated across 30 runs with a target relative standard deviation (RSD) of 2%. The excipients were also evaluated using an FT4 Powder Rheometer® to quantify dynamic flow, bulk and shear properties.
The results in this study demonstrate that even minor variations in powder properties can result in substandard dosing performance, as such it is important that powders are matched to the dosator being utilised. Dynamic flow testing was shown to support the development of more easily processed DPI formulations and the selection of process equipment that will more consistently deliver the required dose.