By Surbhi JainReviewed by Susha Cheriyedath, M.Sc.Apr 5 2022
In an article recently published in the open-access journal Materials, researchers reported the optimization of corrosion resistance of alumina ceramics in nitric acid.
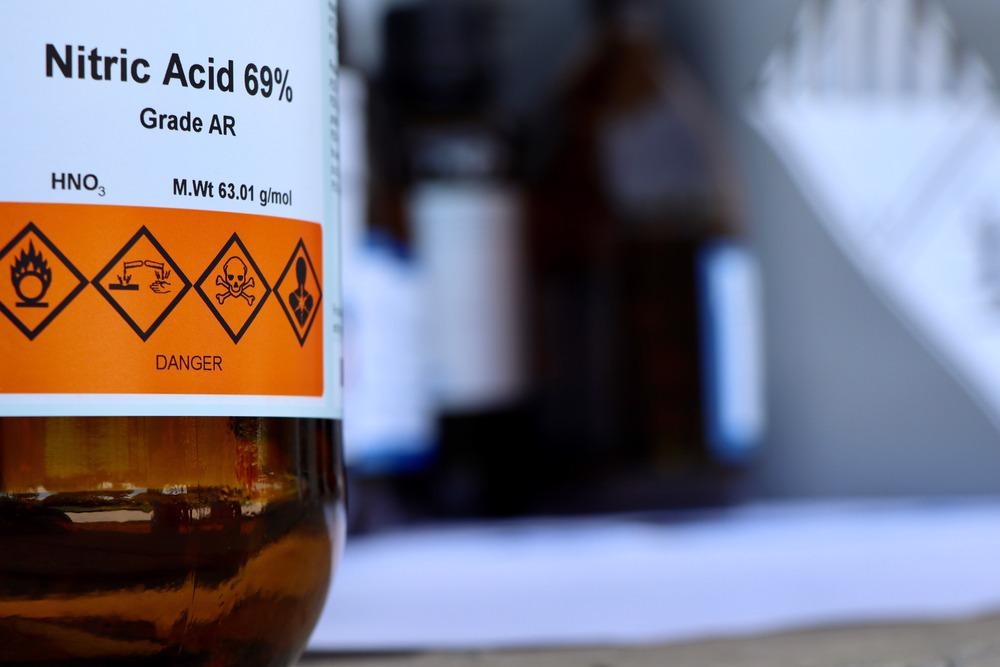
Study: Optimization of Alumina Ceramics Corrosion Resistance in Nitric Acid. Image Credit: chemical industry/Shutterstock.com
Background
Alumina (Al2O3) is a type of ceramic with great hardness, wear resistance, and strength, as well as chemical stability. Ceramic corrosion is, nevertheless, examined and investigated in a variety of domains. Impurities and additives in small proportions have a significant impact on the manufacture and final qualities of alumina-based ceramics.
The desire for further knowledge of advanced ceramic chemical resistance in strong acid environments has expanded dramatically as a result of their rapid development, and hence, new application possibilities have emerged.
The "one-factor-at-a-time" technique (OFAT) can be used to investigate the characteristics that influence ceramic corrosion; however, it is a time-consuming method. Response surface methodology (RSM), on the other hand, is a useful technique for assessing the interactions between the process variables and, as a result, optimizing them.
The development of a model that can predict the development of corrosion procedures within experimental areas, determine interactions between factors, and define the conditions for minimal corrosion is the need of the hour. Within the given conditions, this type of model could also greatly reduce maintenance costs and improve the life expectancy of ceramic materials, such as alumina.
XRD pattern of the Al2O3 granules. Image Credit: Ropuš, I et al., Materials
About the Study
In this study, the authors investigated the corrosion resistance of alumina ceramics in aqueous nitric acid (HNO3) solutions with concentrations of 0.50 mol dm-3, 1.25 mol dm-3, and 2.00 mol dm-3 and exposure durations ranging from 1 to 10 days. Temperature effects at 25, 40, and 55 °C were also studied.
Powder X-ray diffraction (PXRD) was used to assess the phase composition of Al2O3 granules. The produced sintered samples' morphology was determined using a standard ceramographic technique. The sintered samples' hardness was determined using a hardness tester. After unloading, the diagonals were measured using an optical microscope. The Vickers hardness of each sample was determined ten times.
The researchers assessed the corrosion resistance of Al2O3 ceramics by using inductively coupled plasma atomic emission spectrometry (ICP-AES) concentration measurements of eluted Fe3+, Mg2+, Na+, Al3+, Ca2+, and Si4+ ions, as well as the density measurements of the examined alumina ceramics.
Within the experimental "sample-corrosive media" domain, the response surface technique (RSM) was employed to optimize the corresponding parameters. According to the Box–Behnken design, alumina ceramics were exposed to aqueous HNO3 solutions. Following the definition of the regression functions, the conditions for achieving the highest corrosion resistance of sintered ceramics were found through optimization within the experimental region.
During the static corrosion test, the team used the Box–Behnken design to investigate the effect of immersion time, temperature, and HNO3 concentration on the chemical stability of sintered alumina samples by monitoring their density and the number of eluted ions from the samples. Lower alumina ceramics density values were measured under the aforementioned conditions.
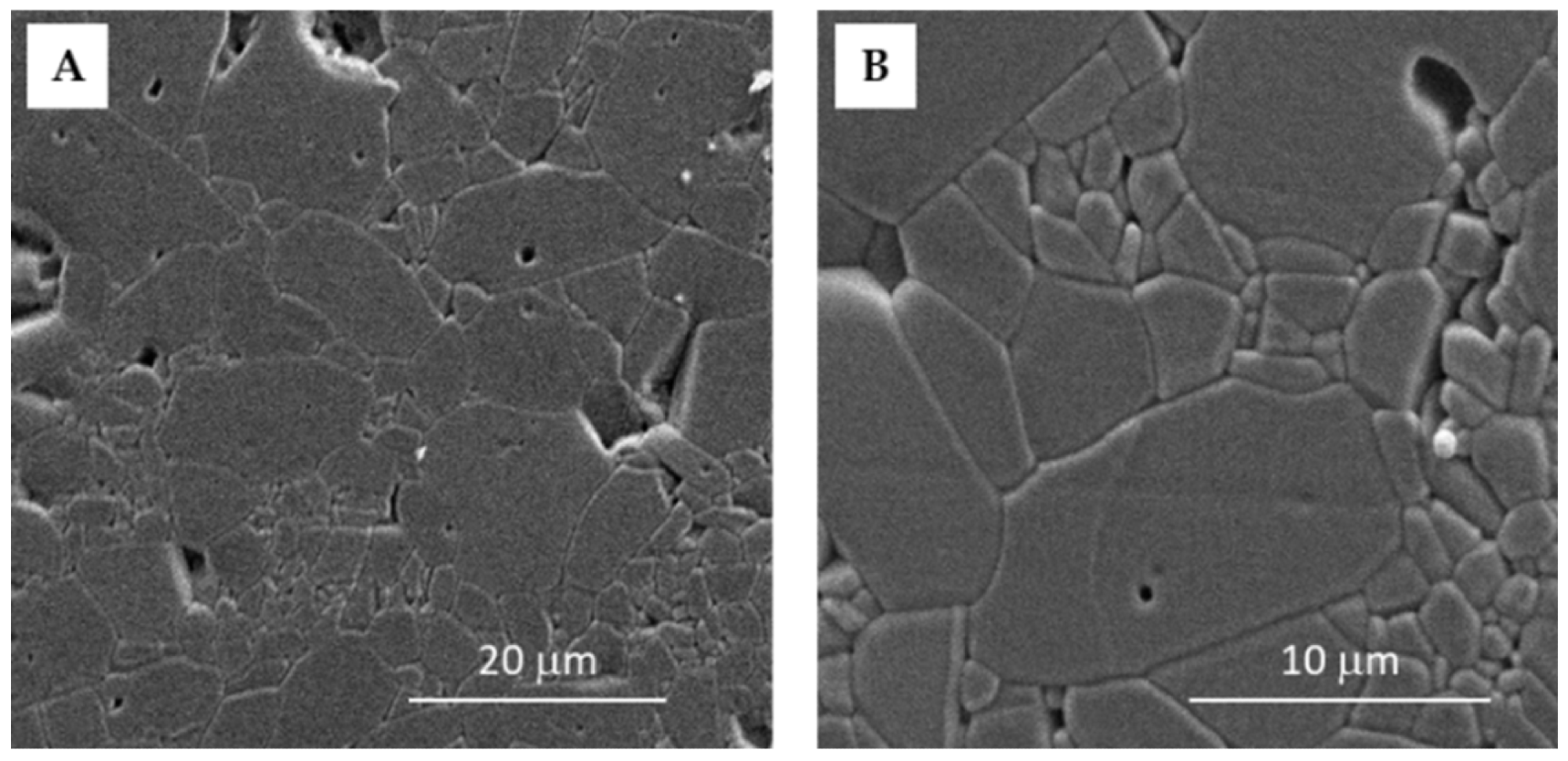
SEM images of the sintered Al2O3 ceramics with the magnification of (A) 2500× and (B) 6000×. Image Credit: Ropuš, I et al., Materials
Observations
The best circumstances for achieving the least amount of ion elution and the highest density of alumina ceramics were achieved at the start of the experiment, i.e., 0.50 mol dm-3 concentration of HNO3 at 25 °C, and 24 h exposure with the desirability of 93%. More than 98% of the total variation in the amount of all eluted ions was described by the regression models, as it was more than 83% of the density variation. The bulk density was found to be 3.864 ± 0.018 g cm-3, with a relative porosity of 3.1 ± 0.5%.
With time, regression models revealed a higher elution of ions from alumina ceramics at lower HNO3 concentrations and higher temperatures. After a minimum exposure duration of 24 h to 0.50 mol dm-3 HNO3 at 25 °C, optimum conditions for achieving the maximum corrosion resistance, i.e., the lowest number of eluted ions and the highest alumina ceramics density, were achieved inside the experimental "sample-corrosive media" area.
A second optimum was also found at 2.00 mol dm-3 HNO3 at 40 °C and 24 h exposure. Lower HNO3 concentrations at higher temperatures were found to have a greater impact on the dissolving of segregated impurities such as Fe2O3, Na2O, CaO, and SiO2, as well as sintering aid, i.e., MgO, at the grain borders of alumina ceramics.
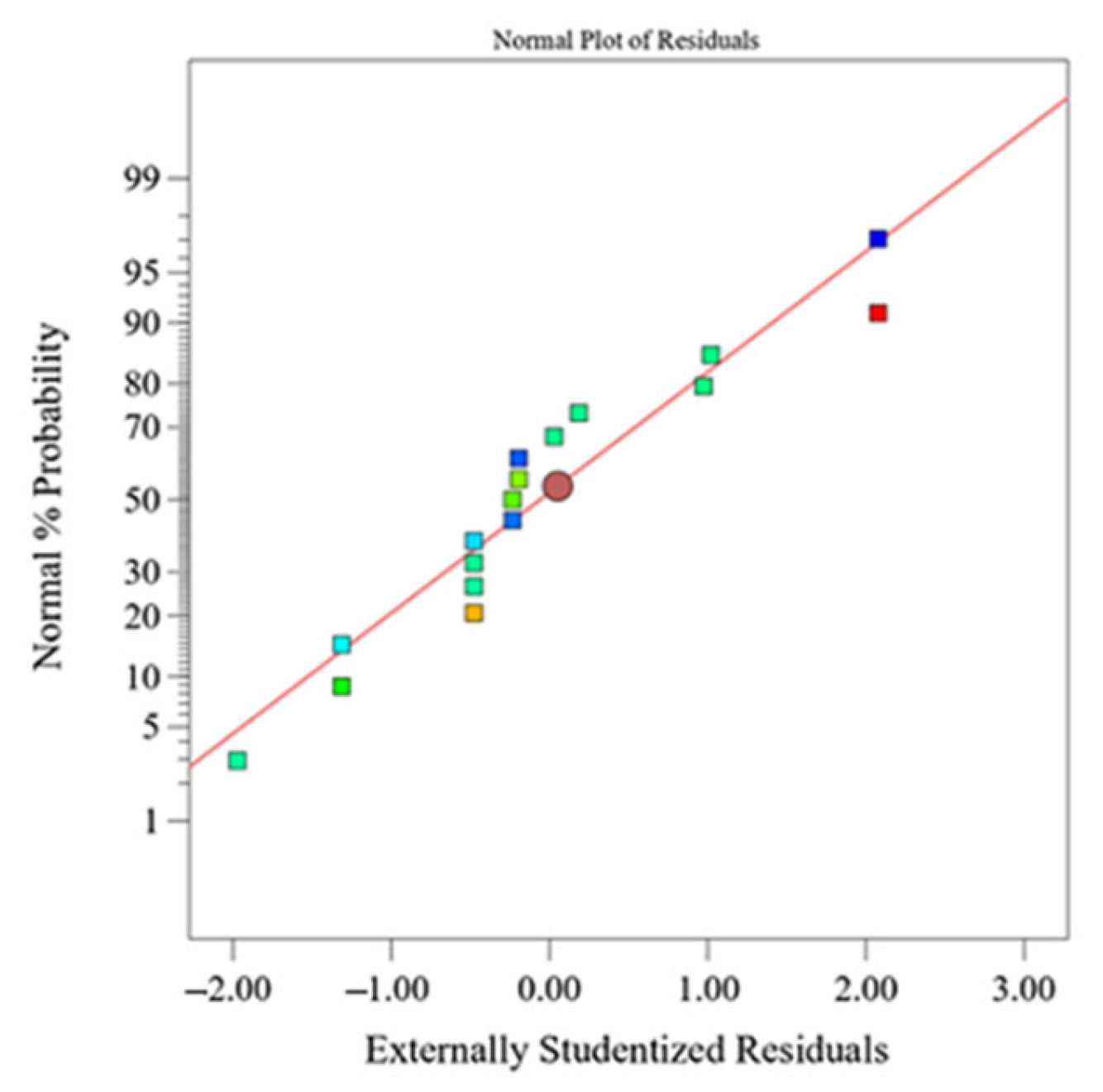
Normal plot of response residuals—amount of eluted Al3+ ions from Al2O3 ceramics after exposure to HNO3. Image Credit: Ropuš, I et al., Materials
Conclusions
In conclusion, this study elucidated the chemical stability of alumina at temperatures of 25, 40, and 55 °C with HNO3 concentrations of 0.50, 1.25, and 2.00 mol dm-3 for up to 240 hours.
The authors emphasized that the experiment was designed using the Box–Behnken method such that the conditions in which the corrosion resistance was maximum could be achieved.
Disclaimer: The views expressed here are those of the author expressed in their private capacity and do not necessarily represent the views of AZoM.com Limited T/A AZoNetwork the owner and operator of this website. This disclaimer forms part of the Terms and conditions of use of this website.
Source:
Ropuš, I., Curkovi´c, L., Cajner, H., et al. Optimization of Alumina Ceramics Corrosion Resistance in Nitric Acid. Materials 15(7) 2579 (2022). https://www.mdpi.com/1996-1944/15/7/2579.