By Surbhi JainReviewed by Susha Cheriyedath, M.Sc.May 18 2022
In an article recently published in the journal Additive Manufacturing, researchers presented the ferromagnetic polylactic acid (PLA) untethered and selectively actuated microwave 4D printing.
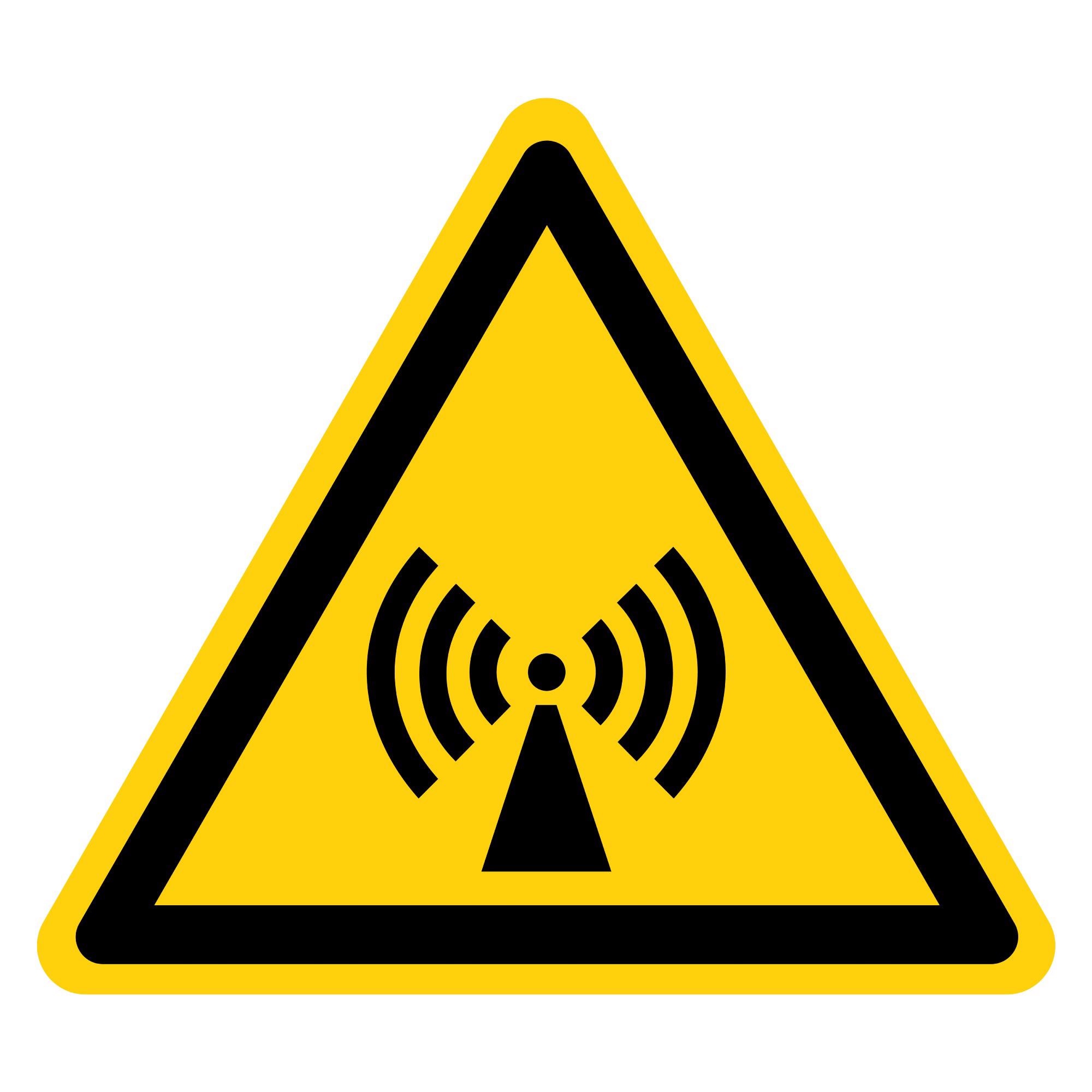
Study: Untethered selectively actuated microwave 4D printing through ferromagnetic PLA. Image Credit: Technicsorn Stocker/Shutterstock.com
Background
4D printing is a unique extension of additive manufacturing (AM) that has gotten a lot of interest in recent years. For prospective 4D printing applications, several forms of smart materials and alternate stimuli have been demonstrated. Despite the fact that different processes have distinct advantages and uses, 4D printing is yet to garner widespread acceptance. Thermally actuated 4D printing based on fused deposition modeling (FDM) is a promising approach.
It has been demonstrated by many studies that by manipulating the printing parameters with heat as the actuation source, numerous shape transformations of the 3D printed parts can be easily achieved using commonly utilized thermoplastic filaments such as PLA or acrylonitrile butadiene styrene (ABS) in an FDM printer.
Traditional thermal activated FDM 4D print technologies apply heat externally and uniformly to the entire printed structure through a water bath or oven. Researchers faced difficulties while attempting to actuate devices that required precisely localized deformation.
About the Study
In this study, the authors demonstrated a novel four-dimensional (4D) printing technology that employed microwave radiation to produce non-contact actuation on thermally activated shape-shifting objects. Microwave radiation was utilized to actuate a 4D printed item by including dielectric elements into a shape memory polymer (SMP) structure at specific points. An FDM printer and thermoplastic filaments were used to show the proposed process.
The proposed approach added novel features such as selective region heating, remote actuation, accurate multi-step actuation, and reduced heating time to existing shape-shifting deformations. A coupled mathematical model for heat transfer, electromagnetic waves, and solid mechanics was simulated using finite element methods and confirmed by comparing experimental results to the behavior of the proposed method.
The team offered a new design and development process for the 4D printing of ferromagnetic PLA incorporated SMP operated by microwave radiation. When the printed structure was subjected to microwave radiation, the heater elements were heated, which then heated the surrounding SMP.
The researchers discussed the manufacturing procedure of the new 4D printing approach, the additional control over existing 4D printing designs, and exemplified a new generation of shape-shifting structures that were not conceivable with conventional methods through computational studies and experimental validations. The advantages of the actuation technology, such as quick response, non-contact, and localized heating, were thoroughly investigated using simulation and practical test scenarios.
Observations
Even though the leaves were actuated as anticipated when the identical structure was placed in a water bath at 90 °C to be uniformly heated, the structural integrity was impaired. In the length of the longitudinally printed samples, the greatest reported percent strain was 43.2%. 1 mm of heater element at 90 second microwave time achieved the highest average experimental temperature of 134.5 °C, while 4 mm of heater element at 30 second microwave time achieved the lowest average experimental temperature of 42.1 °C.
Because the heater elements were printed, they could take on a variety of shapes, including wires and geometrically formed masses. This activation caused anisotropic shrinkage, while the remainder of the SMP remained rigid and under the glass transition temperature. Localized deformation could be performed without the use of microcontrollers or any further post-processing procedures by the strategical placement of heater components. More characteristics, such as actuation timings and deformation magnitude, could be modified by the modification of the dimensions and location of heater components.
Conclusions
In conclusion, this study elucidated the development of novel 4D printing composite structures activated by microwave radiation by utilizing ferromagnetic PLA and PLA. The proposed technology combined AM and microwave-heated shape memory processes, which could open up new possibilities and provide verifiable benefits. The amplitude, time, and position of the programmed deformation could all be controlled using these structures.
The test cases described in this work show how selective heating adds control to existing 4D printing designs while also showcasing a new generation of multi-layered shape-shifting structures that can be driven by many stimuli. Microwave-activated 4D printing could function in tandem with and complement other heating technologies such as induction heating, allowing for more material and stimulus combinations.
The authors believe that the proposed approach might be used for a wide range of SMPs and dielectric materials, opening up new possibilities for a wide range of innovative 4D printing composites. They also mentioned that robotics, product packaging, deployable structures, medicine, and other fields could benefit from this research.
More from AZoM: What are Profile Roughness Parameters?
Disclaimer: The views expressed here are those of the author expressed in their private capacity and do not necessarily represent the views of AZoM.com Limited T/A AZoNetwork the owner and operator of this website. This disclaimer forms part of the Terms and conditions of use of this website.
Source:
Koh, T. Y., Sutradhar, A., Untethered selectively actuated microwave 4D printing through ferromagnetic PLA. Additive Manufacturing 102866 (2022). https://www.sciencedirect.com/science/article/abs/pii/S2214860422002652