Superior toughness and unusual electrical activity are just a few of the characteristics of the unique class of materials known as ceramics. In recent industrial applications, variable thickness ceramic thin films have been extensively utilized. The latest research published in the journal Materials has utilized in-situ time-resolved optical methods to thoroughly assess pulsed laser deposition (PLD) of ceramic layers.
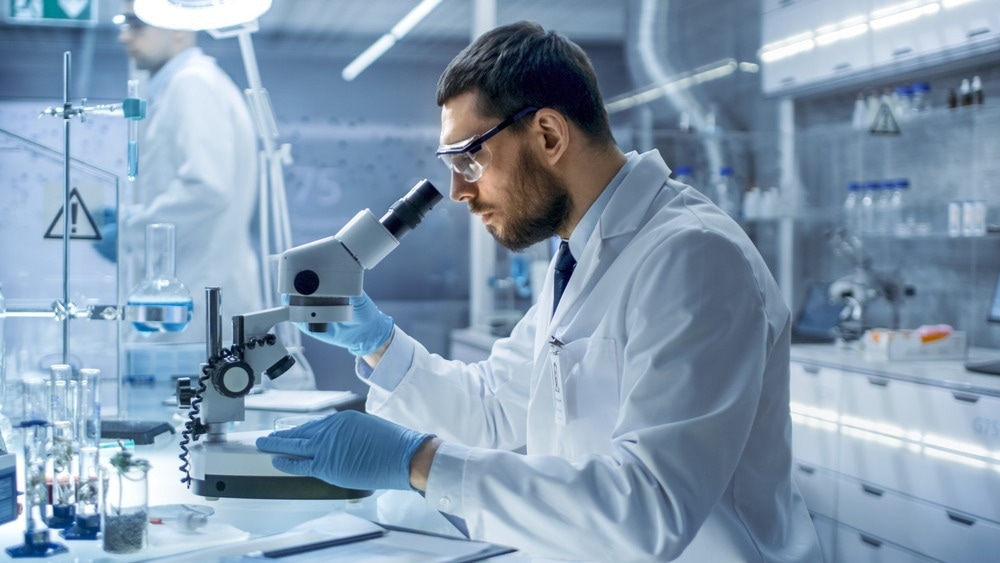
Study: On the Deposition Process of Ceramic Layer Thin Films for Low-Carbon Steel Pipe Protection. Image Credit: Gorodenkoff/Shutterstock.com
Uses of Carbon and Low-Alloy Steel
As they have superior mechanical qualities and are inexpensive, carbon steel and low-alloy steel are the most commonly used materials used to make apparatus for the petroleum sectors, notably containers, exchangers, heat pumps, filtration equipment, spherical injectors, tubes, and couplings. Steel is frequently exposed to various environments and employed for a variety of purposes in the energy and petroleum industries.
Hydrogen sulfide concentrations (H2S) or the soluble percentage in the aqueous phase (pH), the oxygen content, sulfur, or other oxidation products, high pressure, extreme heat, time of exposure, as well as complex operational circumstances are the variables that impact a material's protection against corrosion.
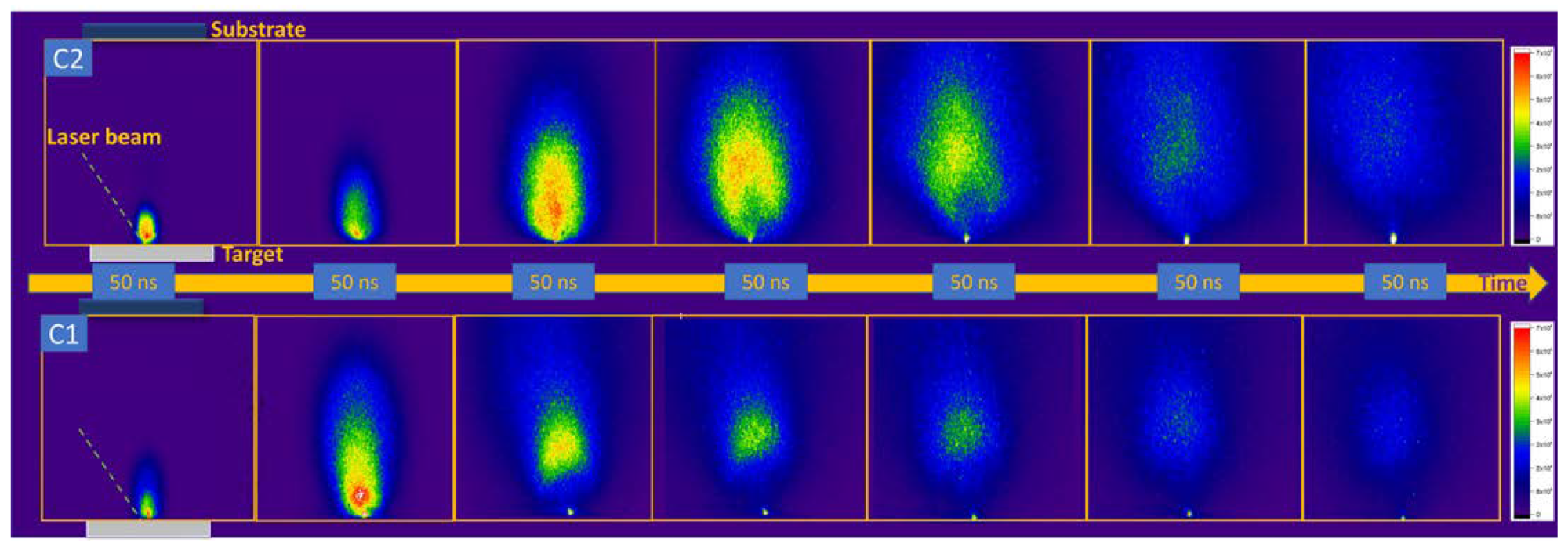
ICCD images of the laser-produced plasmas on C1 (Al2O3 + SiO2) and C2 (Al2O3 + TiO2 + WC) on a 1.5 μs time span. Image Credit: Irimiciuc S. et al., Materials
Coating Technology as a Tool Against Corrosion Resistance
In the past few years, coating techniques have emerged as a particularly efficient approach for enhancing the characteristics of carbon steel. A fine ceramic coating applied to the material surface can withstand contact pressures and guard against material wear. High-performance oxidation layers can be applied by ceramic coatings to metallic materials to address issues with oxidation, abrasion, thermal degradation, insulation, and friction.
To create thin, compact, and well-stoichiometric layers that can shield metallic materials from the damaging effects of H2S, the pulsed laser deposition (PLD) technology is appropriate.
A Brief Introduction of Pulsed Layer Deposition (PLD)
On big platforms, the PLD technique can be utilized to deposit thin films with remarkable compositional and morphological homogeneity.
This is a thin-film deposition process that vaporizes a solid target's interface inside of a sealed container using high-energy pulsating lasers. The deposition region of the PLD method has recently expanded by up to 4 inches, making it ideal for commercial processes.
For both research and manufacturing, new goods and infrastructure are now being commercialized at a consistent rate. Some instances need extended spans of coated components and standardized wafers with high efficiencies, for which PLD plays an essential role.
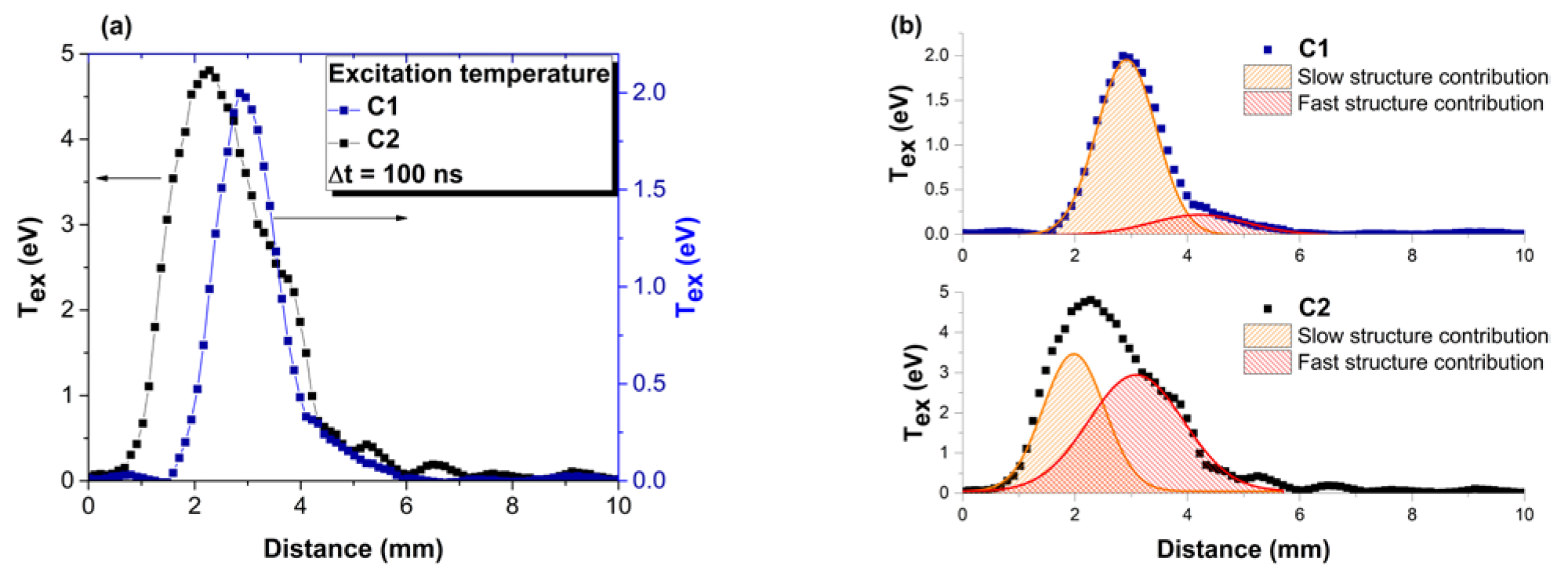
Spatial evolution of electron excitation temperature after 100 ns (a) and the deconvolution for both investigated plasmas (b). Image Credit: Irimiciuc S. et al., Materials
Limitations of PLD
Even though PLD has become a more popular deposition process in recent years, complicated stoichiometric thin films can be challenging to manage and tune to attain the best formability.
The production of particles during film deposition and the uneven covering density when large-area surfaces are coated are the two most obvious PLD constraints.
It appears that PLD is only useful in the design of highly-technological fields such as nanoelectronics, sensing technologies, photonic technology, and advanced functional films. This is due to the expense and accumulation capacity of the optical film processing apparatus.
To manage and comprehend the deposition technique, however, concentrated progress has been achieved in recent years to use several diagnostic tools, such as the Langmuir Probing, ICCD imaging, and spectroscopic analysis techniques.
In this latest study, researchers have discussed the application of ceramics coating materials on metal specimens. Global and spectral-resolved techniques for optical emission spectroscopic analysis were utilized.
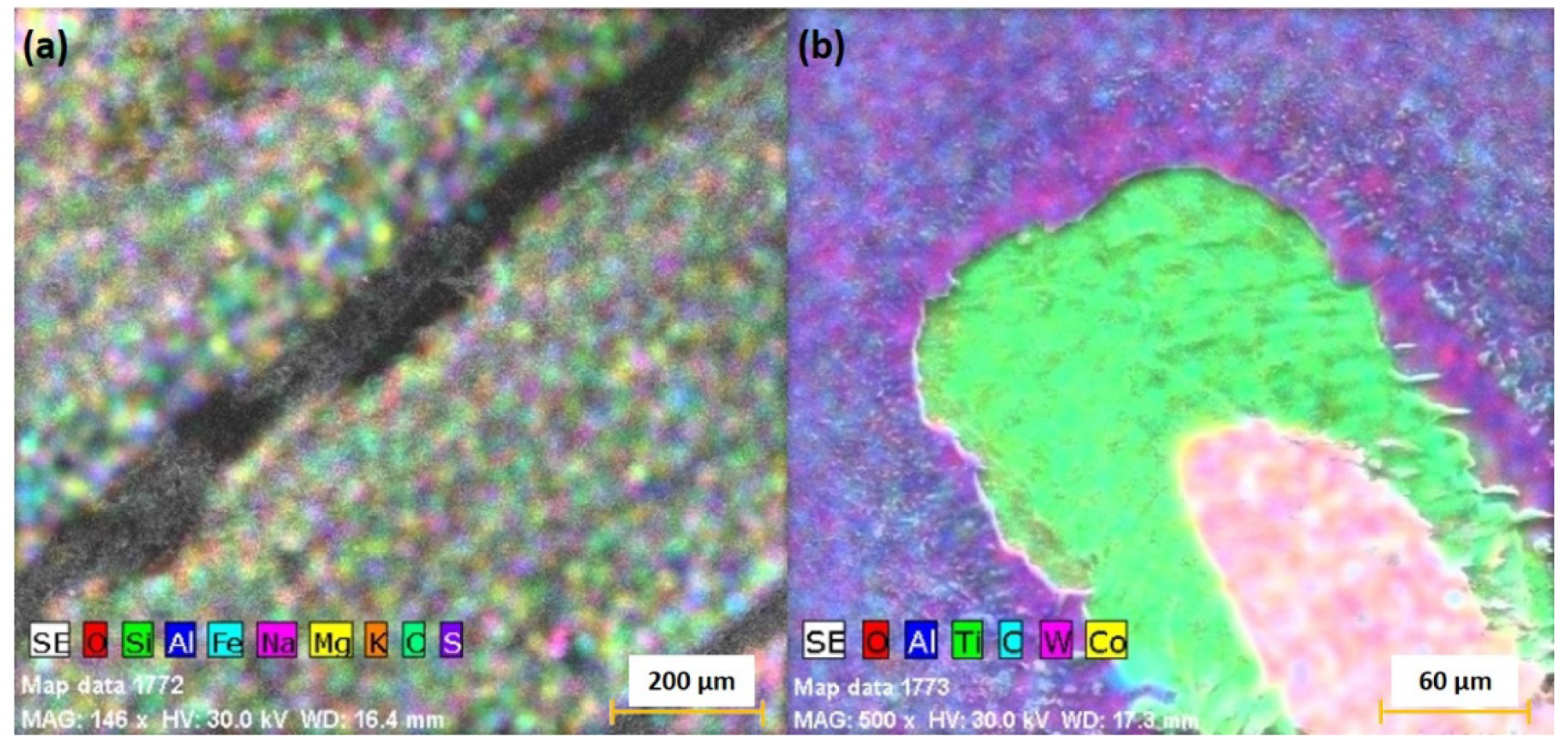
EDX mapping of the post-ablation crater of the C1 (a) and C2 (b) targets. Image Credit: Irimiciuc S. et al., Materials
Research Findings
ICCD rapid video imagery was used to capture a videotape of the film deposition as the initial stage in regulating it. While C2 plasma exhibited a bigger electroluminescence area, C1 plasma was more extended in shape.
Greater ionized phases of silicon and oxygen were seen in C1 plasma, which implied that lighter elements with energies greater than 18.8 eV were detected. In contrast, the majority of excitations in C2 plasma were the first rank, which implied that the frontal region's maximum energy was around 7-8 eV. These discrepancies are consistent with the ICCD rapid camera imaging, which shows a sizable variation between the two plasmids' particle emitter volumes.
When contrasted to the C2 plasma, which contained larger and heavier substances, carbon and oxygen were shown to have higher energy levels in the C1 plasma. This difference was attributed to the enhanced transition stage in the latter scenario. The constituent components were distributed equally across the C1 target. In contrast, the re-deposited substance was distributed spatially for the C2 target.
In short, the findings showed a clear relationship between the species' molecular weight and kinetic energy, and electron temperature did a good job of capturing losses due to impact and dispersion activities.
Further Reading
Irimiciuc S. et al. (2022). On the Deposition Process of Ceramic Layer Thin Films for Low-Carbon Steel Pipe Protection. Materials. 15(13). 4673. Available at: https://www.mdpi.com/1996-1944/15/13/4673
Disclaimer: The views expressed here are those of the author expressed in their private capacity and do not necessarily represent the views of AZoM.com Limited T/A AZoNetwork the owner and operator of this website. This disclaimer forms part of the Terms and conditions of use of this website.