Cracks in the positive electrode of lithium-ion batteries do not just cause problems; according to a University of Michigan study, they also shorten battery charging times.
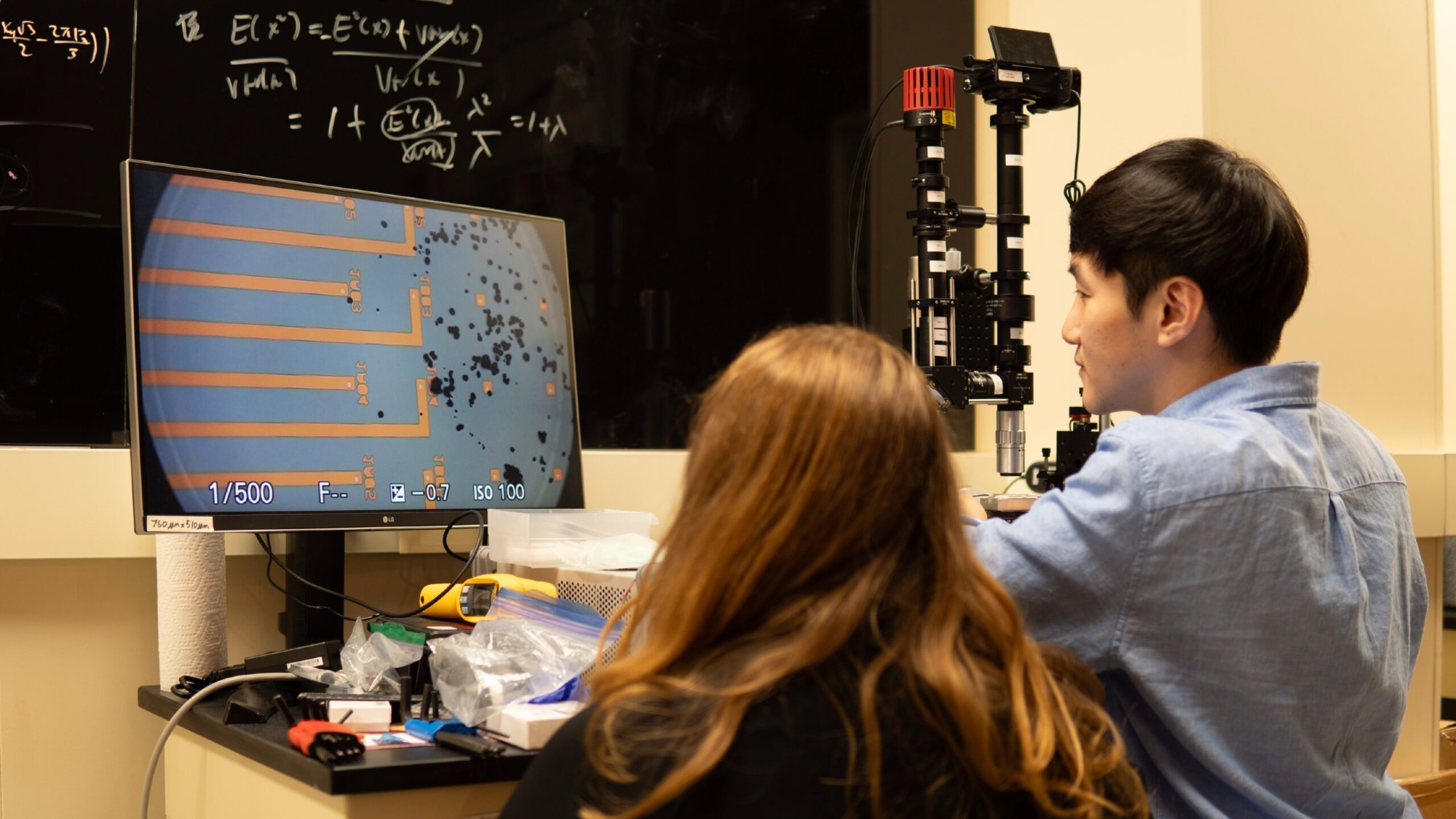
Jinhong Min, a doctoral student in materials science and engineering, and Lindsay Gubow, a former Master’s student in materials science and engineering who graduated in Fall 2021, arrange charge-holding battery particles on an array of microelectrodes. When they are finished, each particle will occupy its own electrode, which allows the team to measure how quickly each individual particle charges. Image Credit: Jinhong Min, Li+ Research Group, University of Michigan
This goes against the philosophy of many electric vehicle producers, who want to reduce cracking since it shortens battery life.
Many companies are interested in making ‘million-mile’ batteries using particles that do not crack. Unfortunately, if the cracks are removed, the battery particles won’t be able to charge quickly without the extra surface area from those cracks.
Yiyang Li, Study Corresponding Author and Assistant Professor of Materials Science and Engineering, University of Michigan
Li added, “On a road trip, we don’t want to wait five hours for a car to charge. We want to charge within 15 or 30 minutes.”
More than half of all electric vehicle batteries, whose positive electrode, or cathode, is made up of billions of tiny particles comprised of either lithium nickel manganese cobalt oxide or lithium nickel cobalt aluminum oxide, are thought to be affected by the research, according to the study.
The surface-to-volume ratio of the particles should determine how quickly the cathode charges. Due to their greater surface area to volume ratio and shorter diffusion lengths for the lithium ions, smaller particles should charge more quickly than larger ones.
Conventional techniques, on the other hand, could only assess the average of the charging characteristics of all the cathode particles that make up the battery. Because of this restriction, the commonly held belief that charging speed and cathode particle size are related was only a supposition.
We find that the cathode particles are cracked and have more active surfaces to take in lithium ions—not just on their outer surface, but inside the particle cracks. Battery scientists know that the cracking occurs but have not measured how such cracking affects the charging speed.
Jinhong Min, Doctoral Student, Materials Science and Engineering, University of Michigan
The key to understanding the benefit of cracking cathodes was to measure the charging speed of individual cathode particles, which Li and Min did by putting the particles inside a device that is commonly used by neuroscientists to examine how individual brain cells receive electrical signals.
Li added, “Back when I was in graduate school, a colleague studying neuroscience showed me these arrays that they used to study individual neurons. I wondered if we can also use them to study battery particles, which are similar in size to neurons.”
Each array is made of a 2-by-2-centimeter chip with up to 100 microelectrodes. Min used a needle that was around 70 times finer than a human hair to transfer individual particles onto their respective electrodes on the array after dispersing several cathode particles in the chip’s core.
Once the particles were in position, Min was able to concurrently charge and discharge up to four distinct particles at a time on the array, and in this investigation, he observed 21 particles.
The experiment demonstrated that the charging rates of the cathode particles were independent of their sizes. According to Li and Min, the most plausible explanation for this surprising behavior is that when larger particles crack, they really operate like a group of smaller particles.
Another theory is that the grain boundaries—the minuscule areas between the nanoscale crystals that make up the cathode particle—are where the lithium ions are moving extremely swiftly. Unless the electrolyte—the liquid medium in which the lithium ions move—pierces these limits and creates fissures, Li believes that this is unlikely to occur.
Designing long-lasting batteries with intact single-crystal particles requires careful consideration of the advantages of cracked materials. These particles may have to be smaller than current cracking cathode particles to charge more quickly.
The option is to create single-crystal cathodes out of various substances that can transfer lithium more quickly, but Li warned that these substances might have lower energy densities or be constrained by the availability of critical metals.
The Lurie Nanofabrication Facility created the device, while the Michigan Center for Materials Characterization conducted research on it. The University of Michigan College of Engineering, LG Energy Solution, and Battery Innovation Contest provided funding for the study.
The University of Michigan College of Engineering, LG Energy Solution, and Battery Innovation Contest provided funding for the study.
Journal Reference
Min, J., et al. (2023) Direct measurements of size-independent lithium diffusion and reaction times in individual polycrystalline battery particles. Nature Nanotechnology. doi:10.1039/D3EE00953J