A recent article published in Materials demonstrated the chemical plating of nickel-boron-polytetrafluoroethylene (Ni-B-PTFE) nanocomposite on the surface of 2A12 aluminum alloy, the primary component of the spinning cup widely employed in the textile industry.
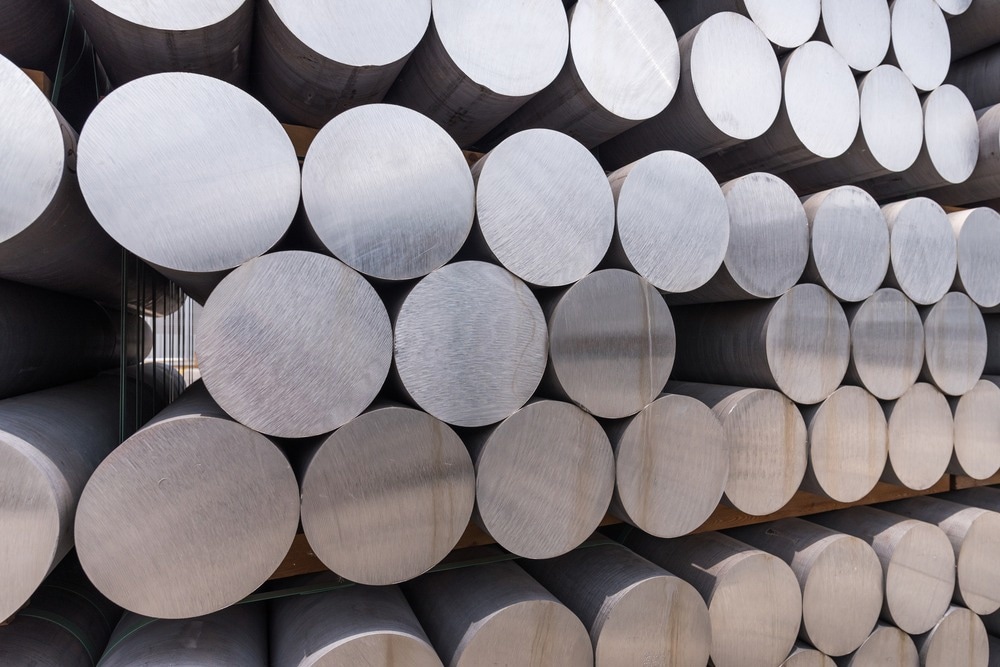
Image Credit: Nattakit Jeerapatmaitree/Shutterstock.com
Background
Air-jet spinning machines are widely used in the textile industry globally. The main component of these machines is the spinning cup, which is primarily made of 2A12 aluminum alloy. Under atmospheric conditions, a protective passivation layer (approximately 250 nm thick) develops on the alloy’s surface. However, it cannot protect the surface in highly corrosive and erosive conditions.
Thus, electroplating and chemical nickel-phosphorus (Ni-P) plating are generally employed to improve the alloy’s surface characteristics. Nevertheless, the hardness and wear resistance of Ni-P coatings are insufficient to fulfill the rising industry standards.
Electroless plating technology has led to the emergence of composite particle coatings and multi-element alloy coatings. These are formed by introducing inert micro/nanometer particles into the base solutions of Ni-P and Ni-B and result in high-quality coatings with exceptional characteristics of hardness, wear resistance, self-lubrication, and hydrophobicity. However, the impact of plating solution components on the rate of deposition and hardness of the coating is scarcely investigated.
This study examined the Ni-B-PTFE electroless plating process for 2A12 aluminum alloy.
Methods
Cylindrical-shaped (30 mm diameter, 10 mm thickness) test specimens were fabricated by cutting 2A12 aluminum alloy using a wire-cutting machine. A minuscule circular orifice (1 mm diameter) was bored in the uppermost part.
An orthogonal experiment was performed to determine the optimal chemical plating parameters for Ni-B, forming the basis of composite electroless plating with nanoscale PTFE.
The Ni-B electroless plating on the alloy specimens was performed on a constant-temperature magnetic stirrer. The plating solution contained varying concentrations of nickel chloride (20 g/L, 25 g/L, 30 g/L, and 35 g/L), ethylenediamine (50 mL/L, 60 mL/L, 70 mL/L, and 80 mL/L), and sodium borohydride (0.6 g/L, 0.8 g/L, 1.0 g/L, and 1.2 g/L).
The plated specimens were observed using a metallographic microscope, with the thickness and deposition rate measured by metallography. The microhardness of the plated layer was determined using a microhardness tester at 100 grams loading and 10 seconds holding time.
The morphology of the plated section was observed using scanning electron microscopy (SEM), and its tissue structure was analyzed using an X-ray diffractometer (XRD). A friction test determined the coatings' coefficient of friction and wear resistance, while indentation tests revealed their adherence to 2A12 aluminum alloy.
The coatings' adhesive strength was evaluated against predefined standard values, and their corrosion resistance was analyzed using an electrochemical workstation with a three-electrode system and a 3.5 % NaCl solution as the corrosive medium.
Results and Discussion
Experiments revealed that 30 g/L nickel chloride, 70 mL/L ethylenediamine, 0.6 g/L sodium borohydride, 90 g/L sodium hydroxide, 30 mg/L lead nitrate, pH 12, 90 °C temperature, 30 mg/L surfactant content, and 10 mL/L PTFE emulsion were ideal for Ni-B-PTFE coating with maximum wear and corrosion resistance.
The nano-Ni-B-PTFE composite coating exhibited greater hardness (1109 HV0.1) and a lower coefficient of friction (approximately 0.1) than the Ni-B plating (232.38 HV0.1). Consequently, a robust protective layer was formed on the alloy surface, enhancing its wear resistance by almost twice.
SEM images revealed a consistent, dense, and smooth surface of the nanocomposite coating without noticeable pores or fissures. Additionally, Ni-B-PTFE composite coatings demonstrated favorable lubrication properties under frictional stress, reduced mechanical wear, and exceptional corrosion resistance, extending the service life of 2A12 aluminum alloy under various chemical environments.
The self-corrosion potential of the specimen coated with Ni-B-PTFE composite coating was -6.195 V, with a corrosion current density of 7.81×10−7 A/cm², the lowest value recorded so far.
Conclusion
The researchers successfully demonstrated electroless chemical plating of nano-Ni-B-PTFE composite co-deposition on the 2A12 aluminum alloy, a key material for the spinning cup. The study examined the influence of different process parameters on the coating's performance, with initial orthogonal tests on basic Ni-B plating revealing optimal parameters for Ni-B-PTFE composite coating.
The nanoscale PTFE particles introduced in the Ni-B coating with a low friction coefficient enhanced the wear and corrosion resistance of the 2A12 aluminum alloy matrix, making Ni-B-PTFE composite coatings suitable for extensive use in the surface treatment of spinning cups to enhance durability and performance.
Journal Reference
Mei, S., et al. (2024). Ni-B-PTFE Nanocomposite Co-Deposition on the Surface of 2A12 Aluminum Alloy. Materials. DOI: 10.3390/ma1713329
Disclaimer: The views expressed here are those of the author expressed in their private capacity and do not necessarily represent the views of AZoM.com Limited T/A AZoNetwork the owner and operator of this website. This disclaimer forms part of the Terms and conditions of use of this website.