Whenever an aircraft engine experiences a vibration problem, it is important to identify the problem quickly so as to save both time and cost of removing the engine.
When trim balancing is needed to reduce the levels of vibrations, the engine has to send a consistent, one-per-revolution signal to provide critical information on the vibration phase. This article briefly explains the differences between the two most common methods of acquiring this signal.
Challenges Involved in Jet Engine Testing
In order to test jet engines on-wing, it is necessary to have access to speed and vibration signals from the engine. Accessing these signals is often difficult because of the mechanical constraints under engine cowls and also due to the design of aircraft wiring harnesses.
Wiring and auxiliary equipment must be positioned and routed in such a way that any possibility of them becoming foreign object debris (FOD) is eliminated. Standard AVM/EVM connections typically provide once-per-revolution signals; however, a number of commercially available systems use an externally mounted laser tachometer to deliver this signal.
These laser tachometers must be mounted with reflective tape onto the spinner, which in turn creates a high contrast reflectance whenever the tape passes under the laser. However, this technique needs an elaborate setup and alignment. It is also unreliable, complex, sensitive to unfavorable weather conditions, and proves unsafe for aircraft operators.
Moreover, vibration during engine testing usually causes misalignments between the tape and laser, thus making the test ineffective.
Reliable Vibration Testing/Trim Balancing
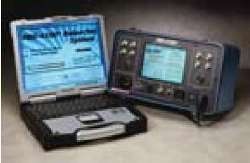
Figure 1. PBS-4100 Plus
MTI Instruments’ PBS-4100 Plus system (Figure 1) coupled with aircraft-specific accessory kits offers safe and reliable trim balancing and vibration testing on almost any jet engine.
Engineers at MTI have studied wiring configurations of a variety of engines and airframe combinations and have designed cable sets that join directly to the equipment connections of the aircraft.
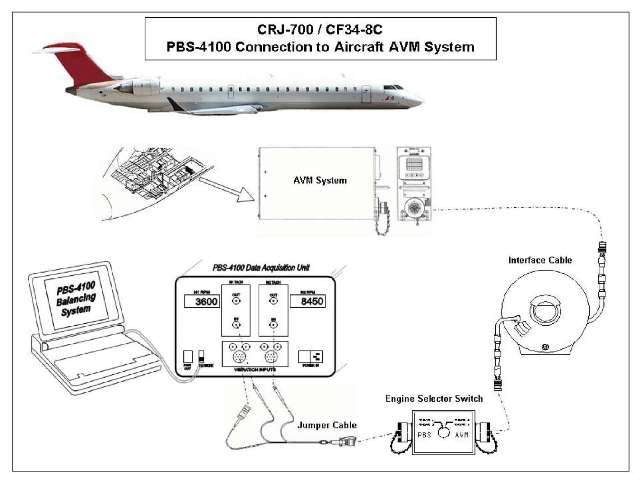
Figure 2. PBS-4100 connection diagram
The PBS-4100 Plus system features a powerful software program that includes circuitry, which automatically senses and "locks on" to the unique odd-tooth signal sent by the speed sensor in the engine.
This prevents the necessity for externally mounted laser tachometer systems that pose alignment issues and operational problems. Figure 2 shows how the system can be easily set up for vibration analysis and trim balance.
Conclusion
MTI Instruments’ PBS-4100 Plus system, along with aircraft-specific accessory kits, provides safe and effective vibration testing and trim balancing on jet engines.
About MTI Instruments
MTI Instruments is a worldwide leader in the design, manufacture and engineering of non-contact measurement systems and sensors.
MTI’s main products consist of computerized general gauging instruments for position, displacement, thickness and vibration applications based on laser triangulation, fiber-optic and capacitance measurement technologies.
Microtrak Pro 2D Laser Sensor, MTI’s newest product innovation, offers an economical, industrial, high precision solution to your position, displacement and profile applications.
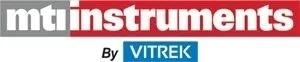
This information has been sourced, reviewed and adapted from materials provided by MTI Instruments Inc.
For more information on this source, please visit MTI Instruments Inc.