In many industries, laser diffraction is used to perform routine particle size analysis. The power of laser diffraction is such that it has started to replace conventional techniques, such as sieving. However, the transition from sieving to laser diffraction requires some form of assessment of the benefits of laser diffraction and how it weighs up against sieving. This article describes 10 differences between laser diffraction and sieving for particle size analysis.
Smaller Sample
In contrast to sieving methods, laser diffraction needs just a small representative sample, but it can also be used with a larger sample. The only limitation on the size of the sample for laser diffraction is the duration of the experiment, as the instrument can be continuously fed or even placed online. However with sieves, the practical limit is dependent on the quantity of material each sieve can handle. Hence, the sample size needed for laser diffraction provides better flexibility to manage the most polydisperse materials.
Faster Experiments
In current material testing, speed is a major factor when choosing an analytical technique. A standard laser diffraction experiment takes only 15 seconds for 10g of material. This means the measurements can be performed virtually in real time, without the need for process instrumentation, and results are also available as soon as the run is complete. Sieve methods, on the other hand, need a few minutes each and often create a bottleneck in the analysis lab. This results in wasted material and restricts the number of samples that can be run in a single shift. Thus, laser diffraction improves lab efficiency and throughput.
Repeatability and Reproducibility of Results
In laser diffraction, the repeatability and reproducibility of results is significantly better than with sieving. Standard laser diffraction measurements provide better than 1% reproducibility and better than 0.5% repeatability, with slight variations caused by the operator. However, in sieving methods, reproducibility can differ considerably depending on the operator and the age of the sieve stack.
Size Range
The Mastersizer 3000 laser diffraction instrument covers a large dynamic range in a single measurement. In contrast, sieves are restricted to ranges that encompass tens to hundreds of microns, with poor performance under 45µm. Sieves also tend to sample the middle dimension of particles, and such a condition can result in misrepresentation of the actual size of particles in a sample.
Customization of Reports
The Mastersizer 3000 software suite enables easy customization of reports to offer the most relevant data to users. When correlating to a sieve stack, users can simply choose the related size ranges and include them directly to the report to acquire percent-in-range. In addition, particle size distribution as well as common statistical parameters can easily be displayed on a single report to help with specification transfer for demanding customers.
Cost of Operation
In laser diffraction systems only simple window cleaning, and sometimes window replacement are required to maintain them. In a dry dispersion system, it is important to regularly change the vacuum bag for optimum performance. This is in contrast to a sieve stack, where wire breakage and tearing will require the sieves to be replaced so as to ensure continuity with previous measurements.
Cleaning and Maintenance
Dry dispersion laser diffraction techniques require just a quick brushing of the system prior to loading the next sample for measurement. The Mastersizer 3000 comes with the Aero S disperser that includes a pre-coded cleaning routine for users. In comparison, sieves need extensive cleaning and weighing of the screens between experiments and this can add more minutes to the total turn-around time.
Automation Techniques
Malvern Panalytical's range of laser diffraction technologies is built around the Standard Operating Procedure (SOP), reducing inter-user variance while improving efficiency. Once an SOP has been ascertained for determining a sample, users simply need to load and name the sample, and the system will do the rest. Although automated sieve techniques are available, they suffer from longer cleaning times, longer experiment times and operator variance.
Sample Containment
The Mastersizer range of dry dispersion accessories is fully sealed from the sample loading area via the vacuum bag. A vacuum collection system ensures quick and easy disposal. Moreover, the system is compact enough to be fitted into an enclosure or hood for maximum safety when running dry samples. Since sieve methods have an open architecture, they are more prone to exposure risk.
More Space, Reduced Noise
The Masterizer 3000 laser diffraction system needs only minimal space and can run on virtually any internal air supply; the vacuum can be placed outside the lab to reduce noise. In contrast, a sieve assembly is noisy, vibrates and requires a larger amount of bench space.
Conclusion
The above points clearly show the advantages of the laser diffraction method over traditional sieving methods. The former technique is suitable for all routine particle size measurements, making the labs a safe and better place to work.
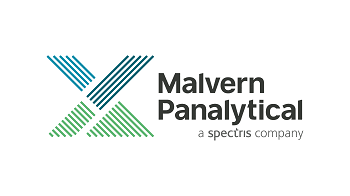
This information has been sourced, reviewed and adapted from materials provided by Malvern Panalytical.
For more information on this source, please visit Malvern Panalytical.